Сварка силумина аргоном в домашних условиях: технология
Сварка силумина сопряжена с некоторыми трудностями. В первую очередь, сварке поддается только силумин литейных марок, в состав которого входит цинк. Во-вторых, сварка этого материала в отличие от алюминия более ресурсозатратна.
Сварка силуминаСилумин – это двухкомпонентный сплав, в составе которого кроме алюминия и кремния присутствуют медь, железо, марганец и прочие элементы. Из него изготавливаются различные изделия методом литья. Хорошие литейные свойства позволяют получать тонкостенные или сложной конфигурации детали, к которым предъявляются повышенные прочностные требования.
Широко применяется силумин при производстве элементов и деталей в авиационной, корабле-, судостроительной отраслях.
Сломанное изделие из силумина легко узнать. На его сколе четко выделяются крупицы. На практике обычно ремонтом не занимаются. Но если возникает острая необходимость, то соединить детали можно несколькими способами: сваркой, пайкой и склеиванием.
Особенности сплава
Силумин – это сплав алюминия и кремния, а кремний влияет на плохую свариваемость. Но примеси железа и титана дают возможность качественного сварного соединения. Марки материала силумин различны. Дешевые составы из Китая буквально плавятся при воздействии высокой температуры. Но изделия известных торговых марок выполняются из более качественного материала.
Среди особенностей силумина следует отметить следующее:
- высокая прочность;
- высокая износостойкость;
- коррозионная стойкость.
У каждого изделия имеется ресурс работы, после которого происходит его разрушение. Соединить элементы можно методами, описанными выше. Склеиваются декоративные изделия. Если к изделию не будут прилагаться значительные внешние усилия, то соединение можно произвести пайкой. Пайка силумина осуществляется при помощи специальных припоев. В основном применяются припои для алюминия: ЕR4043, Harris52, HTS2000.
Изделие из силумина, требующее сварки
Пайку тонкостенных изделий производят мощным электрическим паяльником. Толстостенные же детали разогреть под силу только с использованием газобаллонного оборудования. Процесс протекает при температуре свыше 200°С. Но для предотвращения перегрева деталей используются металлические (стальные) подкладки.
Технология сварки силумина
Сварка силумина в домашних условиях проводится электродуговым методом, но двумя способами. Первый способ – это сварка плавящимися электродами. Широко применяются электроды марки ОК96.50. Стержень изготавливается из силумина, а в качестве обмазки используются составы на основе солей и щелочей из хлора или фтора.
Для соединения деталей плавящимися электродами требуются подготовительные работы. Кроме разделки кромок и удаления окислов с соединяемых поверхностей детали подвергаются предварительному нагреву. Сваривание производится в диапазоне температур от 250°С до 300°С. Для нагрева используется газовая горелка.
Результат сварки силумина
К тому же процесс проводится электродами, которые подвергаются нагреву. Печь настраивается на температуру 150°С. При сваривании силумина должны соблюдаться элементарные правила охраны труда. Для защиты должны использоваться:
- костюм;
- маска;
- рукавицы;
- защитная обувь.
Кроме того, в помещении должны присутствовать средства первичного пожаротушения и отсутствовать горящие и легковозгараемые предметы. Сварочное место должно иметь надежное заземление.
Второй способ – это сварка неплавящимся электродом в облаке инертного газа. Но не стоит забывать, что данный метод не подходит для работ в труднодоступных местах, на открытых пространствах, а также внутри резервуаров.
Аргонодуговая сварка силумина
В отличие от первого способа соединения деталей аргонодуговой метод оставляет после себя аккуратный шов и отсутствие шлака.
Технология сварки аргоном предполагает наличие следующего оборудования:
- сварочный инвертор;
- регулирующий осциллятор;
- баллон с аргоном;
- горелку для работы с защитными газами;
- присадку.
Конструкция горелки позволяет одновременно подавать в зону сварки ток для розжига дуги и защитный газ.
Аргонодуговая сварка силумина
Перед тем как подвергнуть силумин сварке его подготавливают. Для этого:
- кромки зачищаются от окислов механическим способом;
- обезжириваются химическим составом.
Процесс аргонодуговой сварки протекает следующим образом:
- Подсоединение инвертора производится в обратной полярности для лучшего плавления металла. При прямой полярности происходит ионизация газа и в сварочной зоне образуется плазма, которая силумин режет, а не плавит.
- Электрод горелки из вольфрама подводится к свариваемой поверхности на расстояние не более 2,5 мм. Соприкасаться им категорически запрещено.
- Аргон в зону сварки начинает подаваться по истечении четверти минуты (15 секунд) после образования дуги. Это обеспечивает лучший прогрев свариваемых элементов.
- Для заполнения сварочной ванны к дуге вводится силуминовый присадочный пруток или проволока. Ее подают под некоторым углом к сварочной ванне и электроду. Скорость подачи проволоки не должна быть быстрой, иначе большой объем расплава провоцирует разбрызгивание.
- Присадка вводится перед горелкой по пути ее движения. Все перемещения только вдоль шва.
- После окончания горения дуги аргон, подается еще в течение 10 секунд. За это время металл шва немного остывает, что предотвращает образование тугоплавких окислов и трещин.
Достоинства и недостатки сварки аргоном силумина
Среди достоинств выделяются:
- узконаправленное воздействие дуги предотвращает деформацию свариваемых элементов;
- аргон значительно тяжелее воздуха, поэтому он вытесняет кислород из сварочной зоны, увеличивая качество;
- высокая скорость процесса;
- наличие разнообразных разработанных методик для сварки различных составов.
Минусы метода:
- работы можно производить только в закрытых помещениях иначе порывы ветра будут сдувать аргон из-под горелки;
- высокие сварочные токи требуют дополнительного теплоотведения;
- дорогостоящее оборудование;
- долгий подбор режимов.
Процесс сварки силумина – занятие достаточно сложное. Для качественного выполнения необходим большой практический опыт.
Силумин (припой для алюминия) — Энциклопедия по машиностроению XXL
Другим путем снижения эрозионной активности силумина, содержащего более 1,5% Mg, является легирование его германием и медью, образующими с алюминием более легкоплавкие и менее богатые алюминием эвтектики. По данным А. А. Суслова и др., состав такого припоя 5—10% Ge, 5—12% Si, 10—15% Си, 1—6% Mg, А —остальное.
Пайка алюминия со сталью (в том числе с нержавеющей) значительно облегчается при предварительном лужении стали оловом, цинковыми, алюминиевыми припоями, эвтектикой Л1 — 51 — Си, эвтектическим силумином, алюминием (136, 247] и особенно при предварительном гальваническом покрытии стали серебром [134], активирующим растекание этих припоев по стали. При лужении сталь подогревают до 100—-150°С, а алюминий или припой перегревают выше температуры их полного расплавления на 150—170° С. Применяются флюсы из хлористых и фтористых солей (типа 34А, ФВЗ и др.). Алюминий и его сплавы паяют со сталью, предварительно покрытой гальваническим серебром, алюминиевыми припоями с соответствующими флюсами [134]. Учитывая возможность образования и рост хрупких интерметаллидов между железом и алюминием, время пайки алю-
297]
Для твердой пайки алюминия применяют силумины или припой марки 34А (6% 31, 28% Си, остальное А1) с температурой плавления 525° С. [c.320]
Температура плавления силумина довольно высока, поэтому технологически удобнее применять припои 34А и 35А. Припой 35А несколько пластичнее, чем припой 34А, а припой СЛМ-2 еще более пластичен. Пайка алюминия и его сплавов твердыми припоями производится с применением флюса 34А (см. табл. 97). [c.472]
В качестве припоя чаще всего используют эвтектические сплавы на основе алюминия, например, силумин или припой 34А. Процесс пайки силумином более труден из-за его высокой температуры плавления, близкой к температуре плавления алюминия и его сплавов. Преимущество соединений, паянных силумином, — высокая стойкость против коррозии даже в морской воде. [c.210]
При пайке алюминия горелкой наибольшее распространение имеет припой 34А, который более легкоплавок, чем силумин, поэтому пайка им проще, отсутствует опасность оплавления паяемых деталей.
[c.210]
При пайке алюминия и его сплавов в печах обычно применяют те же флюсы и припои, что и при пайке горелкой, но наносят их на паяемые детали заранее. Припой наносят при сборке деталей, а флюс в виде пасты (на безводном спирте) непосредственно перед загрузкой деталей в печь. Температура пайки 600° С для силумина и 560° С для припоя 34А. Выдержка в печи при температурах пайки минимальная. После расплавления припоя и образования галтелей детали выгружают из печи и охлаждают на воздухе.
Силумин (припой для алюминия) 115 Синтамид 42, 44 Синтанол 42, 44 [c.325]
Например, для бесфлюсовой пайки алюминия в вакууме К. Дж. Миллер предложил силумин с содержанием 3—15% Si, легированный 0,4—10% Mg. Силумин, содержащий магний, оказался пригодным для пайки стеклянных отражателей с алюминиевой подложкой в дорожных знаках и сигналах. Для этой цели использован припой состава А1 — (4-т-13%) Si — (4- -б) % Mg в виде плакированного слоя (б—10% его толщины) на алюминии (паяемом металле). Пайку выполняют после нагрева алюминие-
[c.104]
Во флюсовых ваннах паяют изделия из технического алюминия или АМц, плакированных силумином. Для пайки крупногабаритных изделий при температуре 600—620° С удобен сплав АМцПС, так как АПС в этих условиях почти полностью теряет прочность. При необходимости высокой ударной вязкости паяных швов при температуре —196° С применяют припой А1 — (6-ь8%) Si. Этот припой имеет более низкую эрозионную активность, чем припой с А1—10% Si, При этом толщина плакирующего слоя (во избежание сильной химической эрозии) не должна превышать 100 мкм. Толщина плакирующего слоя припоя, содержащего менее 9% Si, не должна превышать 30 мкм. [c.253]
Жидкий цинковый припой хорошо смачивает посеребренную поверхность алюминия. В некоторых случаях при пайке алюминия и его сплавов применяются промежуточные покрытия с температурой плавления ниже температуры пайки.

Наиболее широкое применение нашли припой 34А и эвтектический силумин. Некоторое повышение прочности паяных соединений из алюминия и его сплавов достигается при применении модифицированных эвтектических припоев системы Л1 — 51 (силумины) и Л1 — Си — 51 (34А) вместо немодифицированных. Снизить температуру плавления припоя 34А можно легированием сплавов А1 — Си — 81 цинком (В62 П480). В отличие от других припоев припои П575А и П590А образуют швы, поверхность которых- может быть подвергнута анодированию (бесцветному и цветному) и фосфатированию.
Пайка алюминия и его сплавов с титаном возможна только после предварительного покрытия титана алюминием, путем погружения в расплавленный алюминий или алюминиевый припой, перегретые до температуры 750—800° С и раскисленные сверху флюсом (например, Ф34А или АФ4А, карналлитом). Пайка алюминиевых сплавов с облуженной поверхностью титана производится с применением флюса Ф34 припоями на основе алюминия (например, эвтектического силумина). [c.298]
Технология пайки алюминия и его сплавов (часть 3)
Известны бесфлюсовые способы низкотемпературной пайки. Бесфлюсовую пайку алюминия можно осуществить в газовых средах без применения защитных покрытий контактно-реактивным методом.
В качестве припоя применяют кремний, медь или серебро, которые наносят на алюминий гальваническим путем, термовакуумным напылением или плакировкой. Высокое качество паяного соединения получают при пайке в вакууме 10-5 мм рт. ст. и толщине покрытия 10-12 мкм.
Пайку алюминия припоями типа силумина осуществляют в специальных газовых средах. В качестве последних используют смеси аргона с парами магния. Такая атмосфера способна при температуре 550-580°С восстанавливать окись алюминия и обеспечивать смачивание паяемой поверхности припоями типа силумин.
При пайке алюминиевых сплавов в атмосфере паров магния последний переходит из газовой фазы в расплав. Предел прочности соединений сплава АМг6, выполненных этим способом, составляет 35,2-35,8 кгс/мм 2, а для сплава АМц 11,5-12,5 кгс/мм2. Коррозионная стойкость получаемых соединений намного выше соединений, чем при флюсовой пайке.
Пайку в защитной атмосфере можно осуществить при использовании самофлюсующих припоев (например, 3-15% Si, 0,4-10% Mg, Al — остальное).
Другой припой состава 7,5-13,0% Si, 0,3% Си, 0,1 % Mg, 4,5% Р, 0,1-30,0% металлов из группы Ni и Со, 0,2% Zn, 0,5% Mn, А1 — остальное. Пайку этими припоями следует производить в среде аргона, гелия или в вакууме.
Бесфлюсовую пайку алюминия припоями типа 34А, силумин ПСр 5АКЦ можно производить по предварительно луженной поверхности припоем П200А. Лужение производят абразивным способом, толщина слоя должна составлять 0,03-0,05 мм на сторону.
Нагрев под пайку рекомендуется производить в печи, в потоке аргона или на воздухе индукционным способом.
Известны способы низкотемпературной пайки без применения флюсов, такие как абразивная пайка или пайка трением. При этом способе пайки окисную пленку с поверхности алюминия можно удалить шабером, металлическими щетками, частицами абразива (асбест, металлические порошки, первичные кристаллы сплавов-припоев, в твердо-жидком состоянии и т. п.), находящимися в расплаве припоя.
Применяют также абразивные паяльники для лужения алюминия, у которых рабочая часть паяльника представляет собой стержень из частиц припоя и абразива.
Собственно операция пайки осуществляется уже после абразивного лужения путем обеспечения плотного контакта по луженым поверхностям при температуре полного расплавления припоя. Возможна подпитка шва припоем.
Ультразвуковое лужение можно производить с помощью ультразвуковых паяльников и в ультразвуковых ваннах.
В связи с тем, что при ультразвуковом лужении отмечается сильная эрозия основного металла, лужению этим способом нельзя подвергать детали с толщиной стенок менее 0,5 мм.
Имеется также способ абразивно-кавитационного лужения. При этом способе лужения твердые частицы, находящиеся в жидком припое, в ультразвуковом поле оказывают дополнительное абразивное воздействие на металл.
При пайке алюминия припоями-пастами на основе галлия в качестве наполнителя паст служат алюминий и сплав алюминия с магнием. Температура пайки 200-225°С, время выдержки 4-6 ч. Предел прочности соединений составляет 3-5 кгс/мм2.
При пайке по полуде чистым галлием с последующей термообработкой предел прочности соединения составляет 2,8-3,8 кгс/мм2. Паяные швы выдерживают ударные, вибрационные и термоциклические нагрузки, обеспечивают вакуумную плотность не ниже 10-2
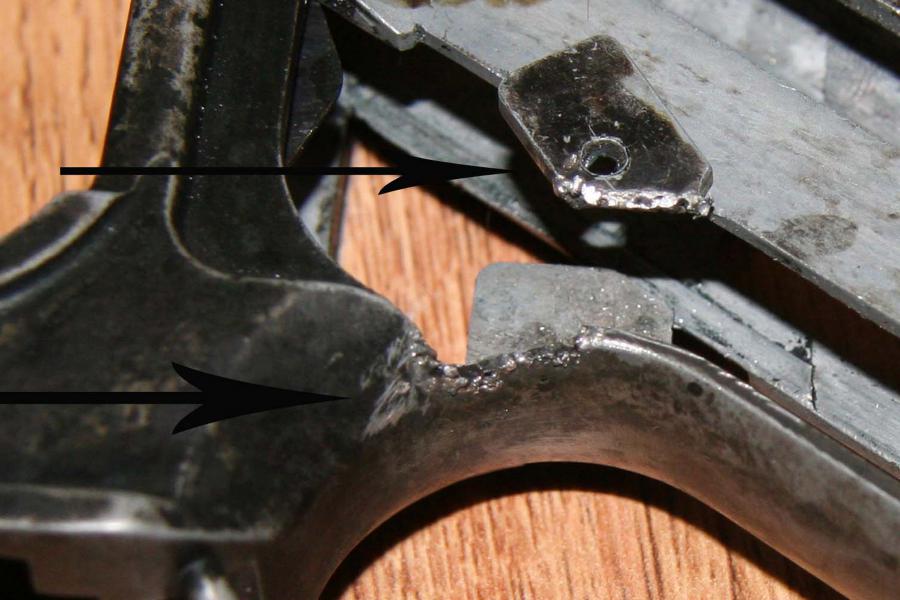
Применяют также пайку цинковыми припоями по серебряному покрытию, нанесенному на поверхность алюминия предпочтительно термовакуумным напылением с последующей термообработкой.
Разработан ряд технологических процессов, обеспечивающих надежное соединение алюминия с медью и ее сплавами, со сталью, никелевыми и другими сплавами.
Основные трудности при осуществлении процесса пайки алюминия с указанными материалами заключаются в трудности выбора флюса или газовой среды, обеспечивающих удаление окислов с поверхностей столь разнородных материалов; в образовании хрупких соединений из-за возникновения интерметаллидов в зоне шва; в наличии большой разницы температурных коэффициентов линейного расширения алюминия и перечисленных выше материалов.
Первые два осложнения успешно преодолевают при предварительном нанесении на поверхности соединяемых материалов защитных металлических покрытий.
Пайку алюминия с медью можно успешно осуществить по никелевому покрытию, нанесенному на алюминий химическим способом. Пайку производят в водороде припоем состава 49% Ag, 20% Си, 31% In; температура пайки близка к температуре плавления алюминия.
Пайка алюминия с медью и ее сплавами может также быть осуществлена путем нанесения защитных покрытий типа цинк, серебро и их сплавы на поверхность меди. При этом используют припои на основе олова, кадмия, цинка.
Через серебряное покрытие на меди может быть осуществлена контактно-реактивная пайка с образованием в паяном шве хрупкой эвтектики Al — Ag — Си. Такие паяные соединения могут быть использованы только в несиловых конструкциях.
Соединение алюминия со сталью, в том числе и с нержавеющей, облегчается при предварительном лужении поверхности стальной детали легкоплавкими свинцово-оловянистыми припоями, алюминием и алюминиевыми припоями с применением активных флюсов на основе хлористых и фтористых солей.
При пайке алюминия со сталью очень важно строго ограничивать режим из-за опасности образования хрупких интерметаллидов в паяных швах. Время выдержки не должно превышать 1-4 мин, температура пайки также не должна превышать заданного предела.
Пайка алюминия с титаном возможна только по слою алюминия или олова, нанесенных на поверхность титана путем горячего лужения.
Сварка силумина в домашних условиях электродом и аргоном
В предметах бытового использования, деталях автомобилей широко используется сплав на алюминиевой основе — силумин. Получается он при легировании основы кремнием в количестве 4-22%. Помимо главного критерия, благодаря которому он пользуется популярностью — красивым внешним видом, можно добавить и технические параметры:
- высокие литейные свойства;
- способность к выдерживанию статистических и динамических нагрузок;
- химическая стойкость ко многим агрессивным веществам.
Высокий процент кремния придает прочность, одновременно повышая хрупкость материала, поэтому нередко требуется сварка силумина.
Стоит сразу отметить, что свариванию поддается только литейный алюминий, с содержанием кремния 4-22% и практически нулевым легированием цинком. Процедура достаточно сложная и требует профессионального подхода (соответственно, обходится дорого), поэтому сваривают такие детали только в случае, если они испытывают нагрузки. Что касается декоративных изделий, здесь достаточно применить склеивание одно- или двухкомпонентным клеем. Практикуется также пайка: она несколько прочнее. Но для нагруженных и ответственных деталей необходима все-таки полноценная сварка.
Отличительные особенности сплава силумин
Особенности сплава
Несмотря на высокое легирование прочным кремнием, силумин имеет все характеристики, присущие алюминию: этот элемент является первым металлом по сродству с кислородом, поэтому среди всех прочих собратьев он будет первым входить в реакцию с ним.
В холодном состоянии алюминий образует на поверхности плотную оксидную пленку, которая исключает проникновение кислорода и дальнейшее окисление металла. Любая царапина запускает повторную реакцию: «чистый» алюминий образует новый оксид Al2O3, который, в свою очередь, восстанавливает потерянную защиту.
В расплавленном виде, из-за близкого сродства к кислороду, алюминий активно окисляется, образуя шлак — плотную жаропрочную пленку, исключающую взаимосвязь между его молекулами. Из-за этого сварка силумина в домашних условиях очень сложная. Стоит также отметить, что в химический состав входят более тугоплавкие вещества, одним из самых влиятельных оказывается цинк — при его большом содержании сплав свариванию не поддается. Соединить такие элементы можно только механическим способом.
На сегодня рассматриваются 2 метода сваривания алюминия и его сплавов. Каждый из них имеет свои недостатки и используется для ограниченного количества сплавов:
- Электродный. Применяется силуминовая фаза с щелочно-солевой обмазкой.
- Электродуговой. Наиболее рационален за счет использования защитной инертной среды.
Сварка силумина электродом
Технология сварочного процесса
Важно! Проводить сваривание алюминия можно только на обратной полярности при «невысокой» температуре нагрева газа, поскольку ионизация аргона при сильном разогреве может привести к резке металла
В домашних условиях проводится сварка силумина электродом марки ОК96. 50. Его принцип работы аналогичен использованию припоев. Основой фазы служит силуминовый сплав, поверх которого наносится солевая, щелочная обмазка производных фтора или хлора. При расплавлении электрода обмазка образует защитную оболочку (шлак) для получаемого расплава. Однородный (или близкий к нему) химический состав стержня восполняет окислившиеся элементы и объем расплава.
Чтобы провести сварку электродами, нужно подготовить поверхности: зачистить от окислов, разделать кромки, после чего нагреть. Сварку электродами проводят при температуре металла 250-300 °С. Для этого используется обычная газовая горелка. Способ очень пожароопасен, поэтому в помещении должны находиться средства тушения (песок, огнетушитель).
Наряду с клеем и пайкой используется еще один метод — холодная сварка для силумина. Представляет собой пластичную смесь, которая при взаимодействии с кислородом упрочняет структуру. Ее синтетическая основа не предназначена для перепадов температур, также она «не любит» отрицательной t, ею можно заделать только небольшие трещины.
Самый результативный способ, применяемый для нагруженных деталей, — сварка силумина аргоном и вольфрамовым (неплавящимся) электродом. Используется для толстостенных деталей (толщиной более 3 мм). Для этих целей нужен сварочный инвертор, который подключается по обратной полярности на короткой дуге.
Инвертор должен оснащаться осциллятором (поскольку электрод находится на расстоянии не менее 2,5 мм от металла и не должен соприкасаться с ним). В качестве присадки используется наплавляемая силуминовая проволока. Подготовка состоит из таких этапов:
- Кромки обрабатываются по одинаковой схеме: можно использовать пескоструйную машину, болгарку с металлической насадкой.
- После механической очистки проводят химическую, которая позволяет проникнуть на молекулярный уровень. Обрабатывают кромки бензином, раствором каустической соды, растворителем, после этого промывают напором воды.
- Газ подают после 15-секундного прогрева электрода, а отключают его подачу через 10 секунд после аргона.
Процесс сварки силумина аргоном
Достоинства и недостатки сварки аргоном
Правильный выбор метода основывается на знаниях принципа их работы. Преимущества аргонодугового переплава:
- Получение однородного шва с отличными физико-химическими показателями.
- Высокая скорость сварки.
- Полная защита от окисления.
- Легкая регулировка мощности благодаря использованию современного оборудования.
- Наличие разработанных методик для различных сплавов.
К минусам можно отнести:
- Дорогостоящее оборудование.
- Необходимость проведения пробных работ.
- Качественный сплав, соответствующий заявленному химическому составу.
- Необходимость постоянного повышения квалификации работника.
Заключение
Каждая технология сварки силумина подбирается в зависимости от назначения детали, ее ценности и производителя. Дешевые китайские изделия сварке не подлежат, поскольку не соответствуют химическому составу, для них лучше использовать клей. Что касается фирменных производителей, лучшим способом соединения является сварка аргоном, поскольку она устраняет самую главную проблему — окисление, а сварной шов обладает высокой прочностью и эстетичным видом.
Видео: Сварка силумина, сварка дюраль электродом
Сварка силумина, профессиональная и в домашних условиях
В настоящее время все чаще встречаются изделия не только из чистого алюминия, но и из его сплавов. Такие сплавы по характеристикам намного прочнее, что позволяет изготавливать детали сложных форм для различных механизмов и машин. Одним из таких популярных сплавов является силумин — изделия из него распространены в кораблестроении и авиационном моделировании. Однако, сварка силумина имеет некоторые особенности, о которых необходимо знать и помнить.
Свойства сплава
Алюминиевые сплавы отличаются от чистого алюминия по многим характеристикам. Они также легки, но в разы прочнее и чаще пластичнее. В свою очередь, имея в своем составе от 4% до 22% кремния, силумин славится прочностью, устойчивостью к износу и коррозии. Но в это же время данный сплав не сильно пластичен и, при неправильной обработке, изделие из него может рассыпаться.
Процесс сварки силумина со стороны кажется незатейливым, но это не так. Работа с данным сплавом имеет свои отличительные моменты, которые стоит рассмотреть подробнее.
Подготовка к работе
Первый нюанс встречается уже на подготовительном этапе. Дело в том, что силумин снаружи покрыт оксидной пленкой, которая мешает правильной и качественной обработке. Поэтому, перед началом работы необходимо сначала удалить оксидную пленку:
- Зачистить заготовки. Для этого стоит воспользоваться наждачной бумагой, металлической щеткой, шлифовальным диском или пескоструйной установкой.
- Обезжирить. Тщательно протереть зачищенные места стыка бензином или растворителем (типа РС-1, РС-2). Можно окунуть детали в раствор каустической соды, только после этого тщательно промыть их под проточной водой.
Мнение эксперта
Багров Виктор Сергеевич
Сварщик высшего 6-го разряда. Считается мастером своего дела, знает тонкости и нюансы профессии.
Не затягивайте с дальнейшими действиями, рекомендуется приступить к сварочным работам не позднее, чем через три часа после обработки.
На промышленной основе для удаления оксидной пленки популярен метод катодного распыления. За счет бомбардировки положительными ионами происходит полное очищение металлической поверхности и предотвращение образования окислов в процессе сварки.
Способы соединения
Перед осуществлением каких-либо ремонтных работ стоит вспомнить, что для этого используется силумин только литейных марок, содержащий в своем составе цинк. Определить, что сломанное изделие из силумина, довольно просто — на поверхности сколов (разломов) имеются характерные крупицы. Устранить поломку можно тремя способами:
- Пайка — бытовой метод сварки без аргона. Соединить посредством пайки возможно только металлические детали с тонкими стенками. Помогут в этом специальные припои, предпочтительны для сварки алюминия, например ER4043, Harris 52, HTS 2000. Для эффективного скрепления стоит пользоваться мощным электрическим паяльником или иметь при себе компактную газовую горелку, баллон с газом (не аргон) и припой.
- Склеивание. Ремонт выполняется весьма и весьма редко. Причина в том, что склеить возможно только те изделия, которые выполняют в большей степени декоративную функцию. Для серьезных нагрузок этот тип ремонта не подходит.
- Сварочные работы. Самый надежный метод починки, но в то же время самый затратный по используемым ресурсам.
Для ремонта конструкций из алюминиевых сплавов применяется электродуговой метод, который в свою очередь, включает в себя два способа сварки:
- Аргонодуговая.
- Работа плавкими электродами.
Сваривание аргоном
Технология аргонодуговой сварки представляет собой процесс работы неплавким электродом в защитном газовом облаке. Аргон сам по себе инертный газ, он не вступает в реакцию с воздухом и прочими веществами. Его основная функция в сварочном процессе — защита металла от окисления. Аргон тяжелее воздуха и легко вытесняет его из рабочей сварной зоны. Благодаря аргоновому облаку оксидная пленка не успевает образоваться на сплавах и шов получается прочным и аккуратным.
Работа с аргонодуговой сваркой требует наличия необходимого оборудования:
- Баллон с газом, в данном случае с аргоном.
- Инвертор.
- Специальная горелка для работы с защитными газами.
- Осциллятор.
- Проволока из силумина в качестве присадки.
При подготовке к сварочным работам стоит помнить, что горелка должна быть специфичной, совмещающей в себе возможность одновременной подачи электротока и газа.
Многие неопытные сварщики считают аргонодуговую сварку простым делом, но это совсем не так. Для сварки с аргоном необходима сосредоточенность и внимательность в течение всего процесса. Не следует пренебрегать средствами индивидуальной защиты, чтобы уберечься от брызг раскаленного металла.
Для создания качественного сварного соединения подготовленные детали сваривают следующим образом:
- Для того чтобы металл легче плавился сварные работы производятся при обратной полярности тока с применением короткой дуги.
- Присадку помещают в сварочную ванну. Там она расплавляется и соединяется с основным металлом, образуя однородную массу, которая при застывании образуется прочное соединение.
- Для качественного прогрева деталей подача аргона начинается через 15 секунд после образования дуги. Важно не допустить перегрев газа, иначе металл будет не свариваться, а разрушаться.
- Присадочная проволока подается в зону сварки под углом и непременно перед горелкой. Подача должна быть точно, равномерной и двигаться строго вдоль шва. Поперечная или слишком быстрая подача присадки может спровоцировать разбрызгивание металла и ухудшить итоговое качество шва.
- После окончания сварных работ аргон подается еще в течение 10 секунд, что позволяет сплаву остыть и избежать трещин и уплотнений в шве.
Все движения сварщика, подача присадки, а также продвижения горелки должны быть плавными и размеренными.
Регулировка сварных соединений алюминия и его сплавов осуществляется ГОСТом 14806-80 от 01.07.1981 года издания. Все типы швов, их стыки, длина и прочее можно узнать в данном ГОСТе.
Кто знаком с данным методом, выделяют такие его достоинства, как:
- малые затраты времени;
- высокое качество полученных соединений;
- возможность выполнить ремонт в домашних условиях;
- разнообразие методик сварки металлов.
Помимо преимуществ имеются и недостатки:
- высокие затраты ресурсов;
- невозможность работы на открытом воздухе;
- возможные проблемы с настройкой сварочного режима;
Применение плавких электродов
В домашних условиях также произвести сварку изделий из силумина можно и без аппарата для аргоновой сварки. Для этого подходят плавкие электроды, представляющие собой сердечник из необходимого металла (в данном случае силумин) и щелочно-солевую оболочку.
При работе с плавящимися электродами требуется соблюдать некоторые условия:
- прогревать детали до 200°С-300°С;
- электроды нагреть перед применением до 150°С;
- рабочее место обязательно должно иметь заземление;
- должны отсутствовать легковоспламеняющиеся предметы;
- использовать средства индивидуальной защиты: обувь, костюм, маску, рукавицы.
При работе с плавкими электродами необходимо неотрывно контролировать процесс, чтобы своевременно убрать со шва шлак от электрода. Качество соединения получается немного ниже, чем у аргоновой сварки, но этот метод более доступен и не требует больших затрат на оборудование.
Обобщая сказанное, стоит признать, что для новичка сваривание деталей из силумина довольно трудоемкий и требует соответствующих теоретических и практических знаний. При наличии опыта работы, сварка силумина не доставит особых хлопот и соединение получится качественным и прочным.
Рекомендуем приобрести: Установки для автоматической сварки продольных швов обечаек — в наличии на складе! Сварочные экраны и защитные шторки — в наличии на складе! Алюминий и его сплавы находят широкое применение для изготовления паяных конструкций в авиационной, электротехнической, радиотехнической и ряде других отраслей промышленности. Особенности пайки алюминиевых сплавов определяются такими факторами, как высокая стойкость оксидной пленки, низкая температура солидуса большинства промышленных алюминиевых сплавов, высокая теплоемкость алюминия. Алюминий, обладая большим сродством к кислороду, образует стойкий оксид Аl2O3, находящийся на его поверхности в виде плотной и прочной пленки. Состав и структура оксидных пленок на поверхности алюминиевых сплавов зависят от состава последних. Так, на поверхности алюминиево-магниевых сплавов присутствует смесь оксидов Аl2O3 и MgO. При пайке алюминиевых сплавов оксиды удаляют с помощью флюсов, в вакууме с добавлением паров магния, трением и ультразвуком. Кроме того, разработаны способы пайки контактным плавлением, а также по защитным и барьерным покрытиям и др. Для высокотемпературной пайки алюминиевых сплавов в качестве флюсов применяют смеси солей хлоридов щелочных и тяжелых металлов с добавками фторидов металлов. Пайку алюминия с указанными флюсами производят припоями на основе алюминия типа силумин, 34А, П425А, В62 и др. Зазор при флюсовой пайке должен быть не менее 0,1…0,25 мм. Высокотемпературная флюсовая пайка алюминия и его сплавов может производиться с применением газопламенного, печного, индукционного и контактного нагрева, а также путем погружения в расплавы флюсов. Для пайки алюминиевых деталей применяют бензовоздушные и газовоздушные горелки. Ацетилено-кислородное пламя непригодно, так как снижает активность флюсов. Для пайки ажурных тонкостенных конструкций из алюминиевых сплавов хорошие результаты обеспечивает печной нагрев. Скорость нагрева для пайки зависит от толщины стенок соединяемых деталей. Температуру печной пайки с применением припоя 34А и флюса 34А поддерживают 550…560 °С; при пайке эвтектическим силумином — 580…600 °С. Применение флюса 34А при печном нагреве опасно ввиду возможности значительного растворения паяемого металла цинком, выделяющимся из флюса; в случае пайки тонкостенных деталей это может привести к сквозному проплавлению. Лучшие результаты дает применение флюсов, в которых хлористый цинк заменен на хлористое олово, хлористый кадмий или хлористый свинец. Это приводит к резкому снижению растворения паяемой поверхности металлом, выделяющимся из флюса. Пайка в солевых ваннах отличается высокой производительностью В связи со значительной температурой пайки (580…620 °С) этим способом паяют сплавы с высокой температурой ликвидуса — АД1, АМц и др. Припои должны быть заранее нанесены на паяемые поверхности в виде покрытия или плакирующего слоя (пайка пластинчатых теплообменников). В случае пайки в солевых расплавах состав флюсовой ванны не должен содержать активных хлоридов типа ZnCl2 из-за сильного растворения в них паяемого металла. Для нормальной работы ванны необходимо тщательное удаление из расплава влаги и солей тяжелых металлов. Для этого солевую ванну обезвоживают алюминием при температуре около 600 °С. Еще более высокой степени очистки удается достигнуть применением порошка сплава, состоящего из 30 % Аl и 70 % Mg. При подготовке поверхности изделий из алюминиевых сплавов к пайке рекомендуется после обезжиривания поверхностей производить их травление в 7…10 %-ном растворе едкого натра при 60 °С с последующей промывкой в холодной воде и обработкой в 20 %-ном растворе азотной кислоты, после чего следует тщательная промывка в проточной горячей и холодной воде и сушка горячим воздухом. Пайку рекомендуется производить не позже чем через 2-3 суток после травления. При пайке погружением в расплав флюса необходим предварительный подогрев изделий до 400…500 °С. Сборку изделий под пайку производят с помощью специальных приспособлений, не взаимодействующих с солевыми расплавами. Приспособления изготовляют из коррозионно-стойких сталей, инконеля, керамики. Своеобразной разновидностью флюсовой высокотемпературной пайки алюминия и его сплавов является реактивно-флюсовая. Флюсы-пасты для этой цели, как правило, содержат до 90 % активных хлоридов. При использовании таких паст наблюдается заметная эрозия основного металла. Для избежания указанного недостатка пайку производят погружением в солевую ванну, в состав которой вводят небольшое количество (в сумме до 1 %) активныххлоридов типа хлористого цинка, хлористого олова, хлористого кадмия и др. В связи с тем что остатки флюсов чрезвычайно коррозионно-активны, особенно при эксплуатации паяных соединений в электропроводящих средах, необходимо сразу же после пайки изделия подвергать тщательной обработке с целью удаления остатков флюсов; с этой целью их промывают в горячей и холодной проточной воде с последующей обработкой в 5 %-ном растворе азотной кислоты или в 10 %-ном растворе хромового ангидрида Однако флюсы могут оказаться и внутри паяного шва, и такая обработка не устранит опасности возникновения очагов коррозии. В этом заключается основной недостаток флюсовой пайки алюминиевых сплавов. Прочностные характеристики паяных соединений при применении наиболее распространенных припоев приведены в табл. 10. 10. Прочность паяных соединений из алюминиевых сплавовНизкотемпературную пайку алюминия и его сплавов припоями на основе олова можно осуществить с применением флюсов на основе высококипящих органических соединений типа триэтаноламина с добавками в качестве активных компонентов борфторидов кадмия и цинка. Применение этих флюсов хотя и обеспечивает удаление оксида алюминия при пайке, но в промышленности они не нашли широкого распространения, так как не обеспечивают получения надежных и герметичных соединений. Кроме того, компоненты легкоплавких припоев в паре с алюминием образуют коррозионно-нестойкие соединения вследствие большой разности нормальных электродных потенциалов. Такие соединения не способны работать в коррозионно-активных средах. Указанные недостатки и затруднения исчезают при использовании технологических покрытий под пайку. В качестве таких покрытий при низкотемпературной пайке алюминия принято использовать медь, никель, серебро, цинк и т.п. Покрытие может быть нанесено электролитически, химически, термовакуумным напылением и другими способами. Наиболее высокое качество сцепления покрытия с основным металлом и коррозионную стойкость паяных соединений обеспечивает применение никельфосфорных покрытий, наносимых на поверхность алюминия химическим способом из специальных гипофосфитных растворов. Оптимальная толщина покрытия 17…25 мкм. После нанесения покрытия деталь подвергают термической обработке в защитной среде (аргон или вакуум) при 200 °С в течение 1 ч, что приводит к повышению прочности сцепления покрытия с поверхностью паяемого металла. Пайка по покрытию легкоосуществима оловянно-свинцовыми припоями с применением канифольно-спиртовых флюсов или флюсов на основе водных растворов хлористого цинка. Коррозионная стойкость таких соединений намного выше стойкости соединений из алюминия, выполненных без защитных покрытий. Соединения из сплавов АМц и Д16. выполненные по никельфосфорному покрытию припоем ПОС61, обеспечивают σср = 30…50 МПа. После годичных испытаний в 3 %-ном растворе поваренной соли прочность соединений снижается лишь на 15…18 %. Коррозионная стойкость соединений, выполненных по медному покрытию, особенно в коррозионно-активных средах, гораздо ниже, чем, по никельфосфорному покрытию; коррозионная стойкость повышается при пайке по цинковым покрытиям и, в частности, по слою цинкового сплава, содержащего 5 % Аl. Слой нанесен на поверхность алюминия методом горячего плакирования. Пайку по цинковому покрытию рекомендуется вести припоем типа ПОСК51 с удалением оксидных пленок механическим способом или с помощью флюса на основе эвтектики NaOH-KOH, вводимой в количестве до 20 % в глицерин. Бесфлюсовую высокотемпературную пайку алюминия можно осуществить в вакууме, в газовых средах без применения защитных покрытий (контактно-реактивным методом). В качестве припоя применяют кремний, медь или серебро, которые наносят на алюминий гальванически, термовакуумным напылением или методом горячего плакирования. Высокое качество паяного соединения получают при пайке в вакууме 10-3 Па и толщине покрытия 10…12 мкм. Пайку алюминия припоями типа силумин осуществляют в специальных газовыхсредах: смесях аргона с парами магния. Такая атмосфера способна при 550…580 °С восстанавливать оксид алюминия и обеспечивать смачивание паяемой поверхности припоями типа силумин. При пайке алюминиевых сплавов в атмосфере паров магния последний переходит из газообразной фазы в расплав. Предел прочности на срез соединений сплава АМг6, выполненных этим способом, 352…358 МПа, а для сплава АМц — 115…125 МПа. Коррозионная стойкость получаемых соединений намного выше, чем при флюсовой пайке. Пайку в защитной атмосфере можно осуществить при использовании самофлюсующих припоев [например, составов (в %): 3 — 15 Si; 0,4 — 1,0 Mg; Аl — остальное, или 7,5-13 Si; 0,3 Сu; 0,1 Mg; 4,5 Р; 0,1 — 3,0 металлов из группы Ni и Со; 0,2 Zn; 0,5 Mn; Аl -остальное]. Пайку этими припоями следует производить в среде аргона, гелия или в вакууме. Бесфлюсовую пайку алюминия припоями типа 34А, силумин (ПСр 5АКЦ) можно производить по предварительно луженой поверхности припоем П200А. Лужение производят механическим способом; толщина слоя 0,03…0,05 мм на сторону. Нагрев под пайку рекомендуется производить в печи в потоке аргона или на воздухе индукционным способом. Прогрессивные способы пайки в вакууме и инертных средах значительно вытеснили пайку с применением флюсов. Пайку в вакууме осуществляют в специальных печах при разрежении 1 * 10-3 Па (в этом случае в камере пайки содержится 3 * 10-7 г/м3 кислорода и 2 * 10-8 г/м3 паров воды). В процессе нагрева с изделия и с внутренней поверхности печи происходит десорбция паров воды и кислорода, что значительно ухудшает состав среды. Для улучшения состава атмосферы применяют распыляемый геттер — магний. При пайке в вакууме с распыляемым геттером получают высококачественные паяные соединения. Недостатком этих печей и способа является сложность удаления после пайки магния, конденсирующегося на стенках печного пространства, нагревателях и теплоотражающих экранах, а также длительность цикла нагрева изделия. Альтернативой способу пайки в вакуумных печах, имеющих внутри камеры экраны и нагреватели, является пайка в аргоне в печах с аэродинамическим подогревом. Внутри рабочей камеры этих печей нет традиционных экранов и нагревателей, а нагрев в них осуществляют вращающиеся колеса с лопатками, и он происходит за счет диссипации энергии газа при его вихреобразовании на лопатках специального профиля. Примером использования такого способа нагрева является агрегат, созданный в ОАО «Криогенмаш» для бесфлюсовой пайки алюминиевых изделий в аргоне. Агрегат состоит из термобарокамеры со встроенными аэродинамическими нагревателями (АДН), систем очистки аргона и подачи его в камеру, вакуумирования, контроля и управления процессом пайки и средств загрузки и выгрузки изделия. Рабочая камера агрегата объемом 40 м3 представляет собой гладкий стальной толстостенный цилиндр, внутри которой нет экранов, поэтому она легка и доступна для очистки от конденсирующихся компонентов. Перед напуском каталитически очищенного аргона камера вакуумируется до разрежения 10-3 Па; нагрев камеры до температуры 635 °С с градиентом по газу 3…5 °С осуществляется тремя встроенными АДН общей мощностью 450 кВт. Аэродинамические колеса, вращающиеся с переменной частотой (500, 1000, 1500 об/мин), позволяют регулировать интенсивность нагрева. Теплоотдача от газа к изделию осуществляется путем интенсивной конвекции сильно турбулизированного потока газа, а также теплопроводности по элементам конструкции. По сравнению с вакуумной пайкой, при сопоставимых габаритах и показателях качества изделий, пайка в среде аргона за счет сокращения термического цикла (интенсивный нагрев в газе и выгрузка изделия при 400 °С) является более производительной (на 20 %), менее энергоемкой (на 30 %), а конструкция камеры пайки, не содержащей экранов, облегчает очистку камеры от сконденсированного магния. Качество паяных соединений из алюминиевых сплавов зависит как от выбора эффективного способа предварительной подготовки поверхностей деталей к пайке, включающего удаление жировых загрязнений и «старых» оксидных пленок, так и от состава газовой среды, в которой производится пайка. Для подготовки поверхностей деталей к пайке распространение получили в основном два способа: травление в щелочных растворах и в растворах кислот. Однако эти способы подготовки поверхности нельзя отнести к экологически чистым. Между тем в настоящее время созданы универсальные кислотные и щелочные очищающие средства, представляющие собой водорастворимые, нетоксичные, взрывопожаробезопасные, полностью биоразлагаемые жидкости широкого спектра применения, в составе которых присутствуют поверхностно-активные вещества и компоненты, способные удалять с поверхностей алюминиевых сплавов жировые загрязнения и оксидные пленки. Такие средства в виде концентратов производит, например, российская компания «ЕСТОС». Продукция компании сертифицирована, по гигиеническим показателям допущена к производству на территории России в качестве очищающих средств, в промышленности и в быту. Активность растворов очистителей на основе ортофосфорной кислоты, например ЕС-очиститель фасадов ФФ (ЕС — ФФ), начинается с 10 %-ной концентрации. В отличие от широко распространенных кислотных и щелочных способов подготовки поверхностей деталей обработка в растворе ЕС — ФФ производится при значительно меньшей потере металла (7,0 мкм/мин в NaOH и 0,09 мкм/мин в очистителе ЕС — ФФ). Раствор ЕС — ФФ сохраняет высокую активность после обработки не менее 1,0 м2 на 1 л раствора без корректировки состава. При пайке в вакуумных печах с разрежением в камере пайки 1 * 10-3 Па газовая среда содержит 3 * 10-7 г/м3 кислорода и 2 * 10-8 г/м3 паров воды. При пайке в аргоне содержание паров воды и кислорода на 2-3 порядка выше, что неблагоприятно для пайки Аl-сплавов. Так, в аргоне высшего сорта по ГОСТ 10157-79 содержится 7 * 10-4 г/м3 кислорода. При пайке алюминиевых сплавов припоями типа силумин в таком непроточном аргоне качественных соединений не образуется. Это еще связано и с непрерывным ухудшением атмосферы в процессе пайки за счет термической дегазации паров воды и кислорода с поверхностей изделия, камеры и приспособления. Улучшить состав газовой среды в данном случае можно за счет предварительного и промежуточного вакуумирования камеры до 1 * 10-3 Па, подогрева изделия с приспособлением, дополнительной осушки аргона от паров воды и кислорода и применения нераспыляемого геттера — пористого титана. Например, в процессе пайки в аргоне высокой чистоты (ТУ 6-21-1279) при использовании названных приемов среда для пайки улучшается на порядок и содержит 6 * 10-4 г/м3 кислорода и 1 * 10-4 г/м3 паров воды. Однако в аргоне при пайке сплава АМц эвтектическим силумином даже в такой среде не удается получить стабильное качество соединения. Условия пайки существенно улучшаются, если в паяемом металле или припое содержится магний в количестве не более 1 %. При нагреве в атмосфере аргона алюминиевых сплавов, легированных магнием, магний практически не испаряется, а диффундирует к поверхности детали и способствует разрушению оксидной пленки и улучшению растекания припоя. В результате технологический процесс, включающий каталитическую очистку аргона, двукратное вакуумирование камеры, использование нераспыляемого геттера, ампулирование изделия и подготовку паяемых поверхностей экологически чистыми растворами, реализован при пайке крупногабаритных пластинчато-ребристых теплообменников (ПРТ) длиной 3000 мм и сечением 850 х 1100 мм. Пайка производится при температуре 605 ± 5 °С. Общее время цикла составляет 22 ч. Конструктивно ПРТ представляет собой паяный пакет из проставочных листов толщиной 1…1,5 мм и гофрированной насадки, выполненной из ленты толщиной 0,2…0,7 мм. Припоем служит эвтектический (11,7 % Si) или близкий к эвтектическому силумин, которым с обеих сторон на толщину 80…120 мкм плакирован проставочный лист. Количество припоя, наносимого на паяемые поверхности, должно быть расчетным, поскольку при недостаточной толщине плакированного слоя снижаются качество и прочность соединений, а при избыточной возможно растворение тонкостенных элементов. При пайке крупногабаритных конструкций ПРТ применение сплавов, содержащих магний, для тонкостенной насадки (0,15…0,3 мм) недопустимо, так как проникновение припоя по границам зерен приводит к полной потере ее устойчивости. Поэтому насадку изготавливают из сплава АМц, в качестве материала для брусков используют сплав АД31, содержащий магний, а для проставочных листов применяют сплав АМц, плакированный эвтектическим силумином. Известны способы низкотемпературной пайки без применения флюсов, такие, как абразивная пайка или пайка трением. При этом способе пайки оксидную пленку с поверхности алюминия можно удалить шабером, металлическими щетками, частицами абразива; помогают удалению оксида и первичные твердо-жидкие кристаллы, находящиеся в расплаве припоя. Для лужения алюминия применяют также абразивные паяльники, у которых рабочая часть представляет собой стержень из частиц припоя и абразива. Операция пайки осуществляется уже после абразивного лужения обеспечением плотного контакта по луженым поверхностям при температуре полного расплавления припоя; возможна подпитка шва припоем. Ультразвуковое лужение можно производить с помощью ультразвуковых паяльников и в ультразвуковых ваннах. В связи с тем что при ультразвуковом лужении отмечается сильная эрозия основного металла, лужению этим способом нельзя подвергать изделия с толщиной стенок менее 0,5 мм. Применим также способ абразивно-кавитационного лужения. При этом способе твердые частицы, находящиеся в жидком припое, в ультразвуковом поле оказывают дополнительное абразивное воздействие на металл. При пайке алюминия припоями-пастами на основе галлия в качестве наполнителя паст служат алюминий и сплав алюминия с магнием. Температура пайки 200 … 225 °С, время выдержки 4…6 ч; σв = 30…50 МПа. При пайке луженой поверхности чистым галлием с последующей термической обработкой σв = 28…38 МПа. Паяные швы выдерживают ударные, вибрационные и термоциклические нагрузки, обеспечивают вакуумную плотность не ниже 1 Па и имеют удовлетворительную коррозионную стойкость. Применяют пайку алюминия цинковыми припоями по серебряному покрытию, нанесенному на поверхности пайки предпочтительно термовакуумным напылением с последующей термической обработкой. Разработан ряд технологических процессов, обеспечивающих надежное соединение алюминия с медью и ее сплавами, со сталью, никелевыми и другими сплавами. Основные трудности при осуществлении процесса пайки алюминия с указанными материалами заключаются в следующем: в выборе флюса или газовой среды, обеспечивающей удаление оксидов с поверхностей столь разнородных материалов; в образовании хрупких соединений из-за возникновения интерметаллидов в зоне шва; в наличии большой разности ТКЛР алюминия и перечисленных материалов. Первые две задачи успешно решаются предварительным нанесением на поверхности соединяемых материалов защитных металлических покрытий. Пайку алюминия с медью можно осуществить по никелевому покрытию, нанесенному на алюминий химическим способом. Пайку производят в водороде припоем состава (в %): 49 Ag, 20 Сu, 31 In; температура пайки близка к температуре плавления алюминия. Пайка алюминия с медью и ее сплавами может быть также осуществлена нанесением защитных покрытий типа цинка, серебра и их сплавов на поверхность меди. При этом используют припои на основе олова, кадмия, цинка. Через серебряное покрытие на меди может быть осуществлена контактно-реактивная пайка с образованием в паяном шве хрупкой эвтектики Al-Ag-Cu. Такие паяные соединения могут быть использованы только в ненагруженных конструкциях. Соединение алюминия со сталью, в том числе и с коррозионно-стойкой, облегчается при предварительном лужении поверхности стальной детали легкоплавкими оловянисто-свинцовыми припоями, алюминием и алюминиевыми припоями с применением активных флюсов на основе хлористых и фтористых солей. При пайке алюминия со сталью очень важно строго ограничивать режим из-за опасности образования хрупких интерметаллидов в паяных швах (время выдержки не должно превышать 1…4 мин, температура пайки — заданного предела). Пайка алюминия с титаном возможна только по слою алюминия или олова, нанесенному на поверхность титана путем горячего лужения. См. также: |
Сварка изделий из силумина | PrimeSteel
Заказать сварку изделий из силумина в Киеве вы всегда можете в Компании Праймстил, где все работы выполняются качественно, оперативно и по приемлемым ценам.
Сварка силумина имеет определенные технологические особенности. Процесс сварки изделий из силумина выполняется неплавящим электродом в защитном аргоновом облаке. В результате окись алюминия создает надежное наплавление на поверхности. В открытом воздухе произвести такую сварку невозможно. Аргон в данном случае выполняет только защитную функцию, он является инертным газом, и не вступает во взаимодействие ни с воздухом, ни с другими газами, ни тем более с металлами.
Силумин это алюминиевый сплав с добавлением кремния. Кремний добавляется для укрепления сплава. Обычно добавляют 10% кремния, что значительно увеличивает прочность, но не слишком увеличивает вес металла. По виду силумин не отличается от обычного алюминия. Из него изготавливают сложные литые детали, к которым предъявляются повышенные требования по прочности. Кроме того он устойчив к коррозии. Диапазон применения силумина необычайно широк. Вот только неполный список сфер его применения: посуда, сантехнические изделия, детали для автомобилей, и даже авиастроение.
Для сварки изделий из силумина используется аргонодуговая технология. В качестве наплавки используется силуминовая проволока. Поверхности для сварки предварительно зачищаются наждачной бумагой и обезжириваются химическим средством.
Очень часто в процессе эксплуатации выходят из строя детали автомобильной, строительной или сельскохозяйственной техники. У них могут появляться трещины в корпусе, разломы отдельных частей и элементов. Для ремонта и восстановления этих деталей нужно выполнить сварочные работы . Это могут быть поддоны картера, головки блока цилиндров, коробки передач, диски или другие автодетали. Используя восстановление поврежденных деталей с помощью сварки вам не понадобится тратиться на приобретение новых.
Стоимость сварки силумина зависит от вида и размера самой детали, а также от характера и размера повреждений. В любом случае для уточнения цены сварки силумина и для получения подробной консультации звоните нашему специалисту по телефонам, указанным на сайте.
Растекание припоев по поверхности металла в расплавленном флюсе
Никитин В.М., Муравьев Р.С. Взаимодействие медных припоев с нержавеющей сталью СН-4 в процессе растекания // Новые паяльные материалы и технологии. Машиностроение, Москва (1971), с. 99–103.
Г. Манько, Пайка и припои, Машиностроение, Москва (1968), 265 с.
Google Scholar
Н. Кагеяма, Распространение припоев на металлической поверхности, № 58213/6, ВИНИТИ, Москва (1966).
Google Scholar
Дж. Амато, Ф. Баудрокко и М. Равицца, «Распространение и агрессивное воздействие припоев на основе никеля на нержавеющую сталь», Сварка. I., 50 , № 4, 183 (1971).
Google Scholar
H. H. v. D.Слуис, Д. против. Торре, «Высокотемпературная пайка аустенитной стали AISI», Lastechniek, 38 , № 12, 290 (1972).
Google Scholar
Левина Л.Г., Сторчай Э.И., Баранов Н.С. Коррозионные характеристики некоторых строительных материалов в хлоридно-фторидных расплавах // Защита металлов. 1972. № 6. С. 726.
Google Scholar
Н.С. Баранов, С.Лоцманов Н., Степанов Г. А. Авторское свидетельство № 270462, Открытия, Изобретения, Промышленные образцы, Товарные знаки, № 16 (1970).
Баранов Н.С., Лоцманов С.Н., Сторчай Е.И., Ежов Н.В. Удаление воды из солевых расплавов при пайке алюминиевых сплавов // Новые паяльные материалы и технологии в машиностроении. 1971), стр. 171–178.
Сторчай Э.И., Савельева В.М., Куколев Е.Н. Кинетика флюсования алюминиевых сплавов в хлоридно-фторидных расплавах // Хим. Физика.я Нефти. Машиностр., № 9, 33 (1973).
Google Scholar
Туманов А.Т., Квасов Ф.И., Фридляндер И.Н. (редакторы), Алюминий: металлургия, обработка и применение алюминиевых сплавов, Металлургия, Москва (1972), 664 с.
Google Scholar
Алюминиево-кремниевый сплав | AMERICAN ELEMENTS ®
РАЗДЕЛ 1. ИДЕНТИФИКАЦИЯ
Название продукта: Алюминиево-кремниевый сплав
Номер продукта: Все применимые коды продуктов American Elements, например.грамм. AL-SI-01-P.50SI , АЛ-СИ-01-П.36СИ , АЛ-СИ-01-П.35СИ , АЛ-СИ-01-П.25СИ , АЛ-СИ-01-П.12СИ , АЛ-СИ-01-П.10СИ , АЛ-СИ-01-П.02СИ , AL-SI-01
Номер CAS: 11145-27-0
Соответствующие установленные области применения вещества: Научные исследования и разработки
Информация о поставщике:
American Elements
10884 Weyburn Ave.
Los Анхелес, Калифорния
Тел .: +1 310-208-0551
Факс: +1 310-208-0351
Телефон экстренной связи:
Внутренний, Северная Америка: +1 800-424-9300
Международный: +1 703-527-3887
РАЗДЕЛ 2.ИДЕНТИФИКАЦИЯ ОПАСНОСТИ
Классификация вещества или смеси в соответствии с 29 CFR 1910 (OSHA HCS)
Вещество не классифицируется в соответствии с Согласованной на глобальном уровне системой (GHS).
Опасности, не классифицированные иным образом
Информация отсутствует.
Элементы маркировки
Элементы маркировки GHS
Неприменимо
Пиктограммы опасности
Неприменимо
Сигнальное слово
Неприменимо
Краткие сведения об опасности
Неприменимо
Классификация WHMIS
Не контролируется
Система классификации
Рейтинги HMIS (шкала 0-4)
(Опасные материалы Система идентификации)
Здоровье (острые эффекты) = 0
Воспламеняемость = 0
Физическая опасность = 0
Другие опасности
Результаты оценки PBT и vPvB
PBT:
Не применимо.
vPvB:
Не применимо.
РАЗДЕЛ 3. СОСТАВ / ИНФОРМАЦИЯ ОБ ИНГРЕДИЕНТАХ
Химические характеристики: Вещества
Номер CAS Описание:
7429-90-5 Алюминий
7440-21-3 Кремний
РАЗДЕЛ 4. ПЕРВАЯ ПОМОЩЬ
Описание первого меры помощи
Общие сведения
Никаких специальных мер не требуется.
При вдыхании
В случае жалоб обратитесь за медицинской помощью.
При контакте с кожей
Обычно продукт не раздражает кожу.
После контакта с глазами
Промыть открытый глаз под проточной водой в течение нескольких минут. Если симптомы не исчезнут, обратитесь к врачу.
После проглатывания
Если симптомы не исчезнут, обратиться к врачу.
Информация для врача
Наиболее важные симптомы и воздействия, как острые, так и замедленные
Отсутствует какая-либо соответствующая информация.
Указание на необходимость немедленной медицинской помощи и специального лечения
Отсутствует какая-либо соответствующая информация.
РАЗДЕЛ 5. МЕРЫ ПОЖАРОТУШЕНИЯ
Средства пожаротушения
Подходящие средства тушения
Специальный порошок для металлических возгораний.Не используйте воду.
Средства пожаротушения непригодны из соображений безопасности
Вода
Особые опасности, исходящие от вещества или смеси
При пожаре могут образоваться следующие вещества:
Дым оксида металла
Рекомендации для пожарных
Защитное снаряжение:
Никаких специальных мер обязательный.
РАЗДЕЛ 6. МЕРЫ ПРИ СЛУЧАЙНОМ ВЫБРОСЕ
Меры личной безопасности, защитное снаряжение и порядок действий в чрезвычайной ситуации
Не требуется.
Меры по защите окружающей среды:
Не допускайте попадания материала в окружающую среду без соответствующих правительственных разрешений.
Методы и материалы для локализации и очистки:
Собирать механически.
Предотвращение вторичных опасностей:
Никаких специальных мер не требуется.
Ссылка на другие разделы.
См. Раздел 7 для информации о безопасном обращении.
См. Раздел 8 для получения информации о средствах индивидуальной защиты.
См. Раздел 13 для получения информации об утилизации.
РАЗДЕЛ 7. ОБРАЩЕНИЕ И ХРАНЕНИЕ
Обращение
Меры предосторожности для безопасного обращения
Хранить контейнер плотно закрытым.
Хранить в сухом прохладном месте в плотно закрытой таре.
Информация о защите от взрывов и пожаров:
Никаких специальных мер не требуется.
Условия безопасного хранения с учетом несовместимости
Хранение
Требования, предъявляемые к складским помещениям и таре:
Особых требований нет.
Информация о хранении в одном общем хранилище:
Не хранить вместе с кислотами.
Хранить вдали от окислителей.
Дополнительная информация об условиях хранения:
Держать емкость плотно закрытой.
Хранить в прохладном, сухом месте в хорошо закрытой таре.
Особое конечное использование
Отсутствует какая-либо соответствующая информация.
РАЗДЕЛ 8. МЕРЫ КОНТРОЛЯ ВОЗДЕЙСТВИЯ / ЛИЧНАЯ ЗАЩИТА
Контроль воздействия
Средства индивидуальной защиты
Общие защитные и гигиенические меры
Следует соблюдать обычные меры предосторожности при обращении с химическими веществами.
Поддерживайте эргономически соответствующую рабочую среду.
Дыхательное оборудование:
Не требуется.
Защита рук:
Не требуется.
Время проницаемости материала перчаток (в минутах)
Не определено
Защита глаз:
Защитные очки
Защита тела:
Защитная рабочая одежда.
РАЗДЕЛ 9. ФИЗИЧЕСКИЕ И ХИМИЧЕСКИЕ СВОЙСТВА
Информация об основных физических и химических свойствах
Общая информация
Внешний вид:
Форма: Твердое вещество в различных формах
Запах: Без запаха
Порог запаха: Не определено.
Значение pH: Не применимо.
Изменение состояния
Точка плавления / интервал плавления: Не определено
Точка кипения / интервал кипения: Не определено
Температура сублимации / начало: Не определено
Воспламеняемость (твердое, газообразное)
Не определено.
Температура возгорания: Не определено.
Температура разложения: Не определено.
Самовоспламенение: Не определено.
Взрывоопасность: Не определено.
Пределы взрываемости:
Нижняя: Не определено
Верхняя: Не определено
Давление пара: Не применимо.
Плотность при 20 ° C (68 ° F): Не определено.
Относительная плотность
Не определено.
Плотность пара
Не применимо.
Скорость испарения
Не применимо.
Растворимость в / Смешиваемость с водой: Не определено.
Коэффициент распределения (н-октанол / вода): Не определено.
Вязкость:
динамическая: Не применимо.
кинематика: Не применимо.
Другая информация
Отсутствует какая-либо соответствующая информация.
РАЗДЕЛ 10. СТАБИЛЬНОСТЬ И РЕАКЦИОННАЯ СПОСОБНОСТЬ
Реакционная способность
Информация отсутствует.
Химическая стабильность
Стабилен при соблюдении рекомендуемых условий хранения.
Термическое разложение / условия, которых следует избегать:
Разложение не происходит при использовании и хранении в соответствии со спецификациями.
Возможность опасных реакций
Реагирует с сильными окислителями
Условия, которых следует избегать
Отсутствует какая-либо соответствующая информация.
Несовместимые материалы:
Кислоты
Окислители
Опасные продукты разложения:
Пары оксидов металлов
РАЗДЕЛ 11.ТОКСИКОЛОГИЧЕСКАЯ ИНФОРМАЦИЯ
Информация о токсикологическом воздействии
Острая токсичность:
Эффекты неизвестны.
Значения LD / LC50, которые имеют отношение к классификации:
Нет данных
Раздражение или разъедание кожи:
Может вызывать раздражение
Раздражение или разъедание глаз:
Может вызывать раздражение
Сенсибилизация:
Сенсибилизирующие эффекты неизвестны.
Мутагенность зародышевых клеток:
Эффекты неизвестны.
Канцерогенность:
ACGIH A4: Не классифицируется как канцероген для человека: Недостаточно данных для классификации агента с точки зрения его канцерогенности для людей и / или животных.
Репродуктивная токсичность:
Реестр токсических эффектов химических веществ (RTECS) содержит репродуктивные данные для этого вещества.
Специфическая системная токсичность, поражающая отдельные органы-мишени — многократное воздействие:
Эффекты неизвестны.
Специфическая системная токсичность, поражающая отдельные органы-мишени — однократное воздействие:
Эффекты неизвестны.
Опасность при вдыхании:
Эффекты неизвестны.
От подострой до хронической токсичности:
Реестр токсических эффектов химических веществ (RTECS) содержит данные о токсичности при множественных дозах этого вещества.
Дополнительная токсикологическая информация:
Насколько нам известно, острая и хроническая токсичность этого вещества полностью не изучена.
РАЗДЕЛ 12. ЭКОЛОГИЧЕСКАЯ ИНФОРМАЦИЯ
Токсичность
Водная токсичность:
Отсутствует какая-либо соответствующая информация.
Стойкость и разлагаемость
Отсутствует какая-либо соответствующая информация.
Потенциал биоаккумуляции
Отсутствует какая-либо соответствующая информация.
Подвижность в почве
Отсутствует какая-либо соответствующая информация.
Дополнительная экологическая информация:
Общие примечания:
Не допускайте попадания материала в окружающую среду без соответствующих правительственных разрешений.
Избегать попадания в окружающую среду.
Результаты оценки PBT и vPvB
PBT:
Не применимо.
vPvB:
Не применимо.
Другие побочные эффекты
Отсутствует какая-либо соответствующая информация.
РАЗДЕЛ 13. УТИЛИЗАЦИЯ
Методы обработки отходов
Рекомендация
Проконсультируйтесь с государственными, местными или национальными правилами, чтобы обеспечить надлежащую утилизацию.
Неочищенная тара:
Рекомендация:
Утилизация должна производиться в соответствии с официальными предписаниями.
РАЗДЕЛ 14. ТРАНСПОРТНАЯ ИНФОРМАЦИЯ
Номер ООН
DOT, ADN, IMDG, IATA
Неприменимо
Собственное транспортное наименование ООН
DOT, ADN, IMDG, IATA
Неприменимо
Класс (ы) опасности при транспортировке
DOT, ADR, ADN, IMDG, IATA
Класс
Неприменимо
Группа упаковки
DOT, IMDG, IATA
Неприменимо
Опасности для окружающей среды:
Неприменимо.
Особые меры предосторожности для пользователя
Не применимо.
Транспортировка наливом в соответствии с Приложением II MARPOL73 / 78 и Кодексом IBC
Не применимо.
Транспортировка / Дополнительная информация:
DOT
Морской загрязнитель (DOT):
№
РАЗДЕЛ 15. НОРМАТИВНАЯ ИНФОРМАЦИЯ
Нормы безопасности, здоровья и окружающей среды / законодательные акты, относящиеся к веществу или смеси
Элементы маркировки GHS
Не применимо
Опасность пиктограммы
Неприменимо
Сигнальное слово
Неприменимо
Краткая характеристика опасности
Неприменимо
Национальные правила
Все компоненты этого продукта перечислены в U.S. Закон о контроле за токсичными веществами Агентства по охране окружающей среды Реестр химических веществ.
Все компоненты этого продукта занесены в Канадский список веществ, предназначенных для домашнего использования (DSL).
SARA Раздел 313 (списки конкретных токсичных химикатов)
7429-90-5 Алюминий
Предложение штата Калифорния 65
Предложение 65 — Химические вещества, вызывающие рак
Вещество не указано.
Правило 65 — Токсичность для развития
Вещество не указано.
Правило 65 — Токсичность для развития, женщины.
Вещество не указано.
Prop 65 — Токсичность для развития, мужчины
Вещество не перечислено.
Информация об ограничении использования:
Для использования только технически квалифицированными специалистами.
Этот продукт подпадает под требования к отчетности раздела 313 Закона о чрезвычайном планировании и праве общества на информацию от 1986 года и 40CFR372.
Другие правила, ограничения и запрещающие нормы
Вещество, вызывающее очень большую озабоченность (SVHC) в соответствии с Регламентом REACH (EC) № 1907/2006.
Вещества нет в списке.
Должны соблюдаться условия ограничений согласно Статье 67 и Приложению XVII Регламента (ЕС) № 1907/2006 (REACH) для производства, размещения на рынке и использования.
Вещества нет в списке.
Приложение XIV Правил REACH (требуется разрешение на использование)
Вещество не указано.
Оценка химической безопасности:
Оценка химической безопасности не проводилась.
РАЗДЕЛ 16. ПРОЧАЯ ИНФОРМАЦИЯ
Паспорт безопасности в соответствии с Регламентом (ЕС) №1907/2006 (REACH). Вышеприведенная информация считается правильной, но не претендует на исчерпывающий характер и должна использоваться только в качестве руководства. Информация в этом документе основана на текущем уровне наших знаний и применима к продукту с учетом соответствующих мер безопасности. Это не является гарантией свойств продукта. American Elements не несет ответственности за любой ущерб, возникший в результате обращения или контакта с вышеуказанным продуктом. Дополнительные условия продажи см. На обратной стороне счета-фактуры или упаковочного листа.АВТОРСКИЕ ПРАВА 1997-2021 AMERICAN ELEMENTS. ЛИЦЕНЗИОННЫМ ДАННЫМ РАЗРЕШЕНО ИЗГОТОВЛЕНИЕ НЕОГРАНИЧЕННЫХ КОПИЙ БУМАГИ ТОЛЬКО ДЛЯ ВНУТРЕННЕГО ИСПОЛЬЗОВАНИЯ.
силумин — английское определение, грамматика, произношение, синонимы и примеры
Субэвтектический безникелевый силумин , полученный из вторичных шихтовых материалов
Польские Патенты
Безникелевый почти эвтектический силумин , полученный из вторичных шихтовых материалов
Польские Патенты
Настоящее изобретение также касается производства кремния, возможно, силумина , и / или алюминия с использованием технологического оборудования, включающего два или более печей, объединенных в один блок с промежуточной перегородкой, которая предназначена / предназначены для передачи электролит из одной печи в другую.
патенты-wipo
Литейный приэвтектический силумин
Польские Патенты
Используемый реагент состоит из шлаков, образующихся при производстве синтетического силумина , водяного пара и углеродсодержащего материала.
патенты-wipo
Около 55% мирового потребления кремния металлургической чистоты идет на производство алюминиево-кремниевых сплавов ( силумин, сплавов) для литья алюминиевых деталей, в основном для использования в автомобильной промышленности.
WikiMatrix
Безникелевый субэвтектический сплав , силумин , полученный из чистых исходных шихтовых материалов.
Польские Патенты
Литейный безникелевый почтиэвтектический сплав , силумин , изготовленный из вторичных шихтовых материалов
Польские Патенты
Способ получения карбида кремния и, необязательно, алюминия и силумина , (алюминиево-кремниевый сплав) в одной ячейке, причем: силикатные и / или кварцевые породы подвергаются электролизу в солевом расплаве, состоящем из фторидсодержащей электролизной ванны, в результате чего кремний и алюминий образуются в одной ванне, а образованный алюминий, который может быть низколегированным, течет ко дну и необязательно отводится, углеродный порошок из катодного материала и / или из внешних источников добавляется непосредственно в ванну расплава или ванну замораживания в дополнение к катодному осадку, замороженная ванна и катодный осадок измельчаются до или после добавления углерода частицы; полученная смесь плавится при температуре выше 1420 ° C, и SiC кристаллизуется при охлаждении.
патенты-wipo
Способ производства металлического кремния, силумина и металлического алюминия
патенты-wipo
Безникелевый почти эвтектический силумин , полученный из чистых исходных материалов
Польские Патенты
В качестве реагента может использоваться шлак, полученный при производстве синтетического силумина , продукта, полученного обработкой графита водяным паром, известью, смесью графита и вторичного алюминиевого шлака или отработанной смесью, полученной в литейной промышленности.
патенты-wipo
Для производства силумина остаточный электролит с низким содержанием кремния со стадии I переносится во вторую печь и добавляется металлический алюминий (стадия II).
патенты-wipo
Настоящее изобретение относится к процедуре непрерывного или периодического производства в одну или, возможно, несколько стадий в одной или нескольких печах металлического кремния (Si), возможно, силумина, (сплавы AlSi) и / или металлического алюминия (Al) в требуемых условиях в ванна для плавления, предпочтительно с использованием полевого шпата или полевого шпата, содержащего породы, растворенные во фториде, и технологическое оборудование для проведения процедуры.
патенты-wipo
Процесс получения карбида кремния и, возможно, алюминия и силумина (алюминиево-кремниевый сплав)
патенты-wipo
Силумин высокой чистоты (сплавы AlSi) получают путем легирования высокочистого алюминия и высокочистого Si из остаточного Si и Si (IV) в криолит (Na¿3?
патенты-wipo
Другие применения элементарного бария незначительны и включают добавку к силумину (алюминиево-кремниевые сплавы), которая улучшает их структуру, а также подшипниковые сплавы; припой свинец-олово — для повышения сопротивления ползучести; сплав с никелем для свечей зажигания; добавка к стали и чугуну в качестве модификатора; сплавы с кальцием, марганцем, кремнием и алюминием в качестве раскислителей высококачественной стали.
WikiMatrix
Силумин для автомобильных отливок и способ придания им микроструктуры и текстуры поверхности для повышения износостойкости
Польские Патенты
Ремонт— Как закрепить стальной стержень в глухом отверстии силуминовой детали?
(Помогло бы изображение сломанного куска.)
Вариант 1. (Однозначно лучший ответ) Купите новую ножовку. Вы не сможете исправить это, не удалив резьбовую деталь, которая все еще остается в отверстии, а затем изготовив новую деталь для удержания лезвия.Это потребует добавления резьбы к новой детали. Если у вас нет инструментов для этой работы, вам нужно будет их приобрести, что будет стоить вам больше, чем новая рама для ножовки.
Вариант 2. Удалите резьбовую часть, которая остается внутри отверстия. Обычно это предполагает просверливание в нем небольшого отверстия, затем необходимо купить инструмент для вывинчивания шурупов, которые были отбиты в отверстии. (Обычно это называется ez-out или что-то в этом роде. Они есть в строительном магазине.) Вы вставите этот инструмент в просверленное отверстие.Он застрянет на месте с грубой обратной резьбой с острыми краями и позволит вам вытащить резьбовую деталь. Может помочь капнуть туда немного WD-40, когда вы пытаетесь открутить резьбовую часть.
Просверливание этого отверстия само по себе может быть проблематичным, поскольку существует большая вероятность, что часть ножовки была сделана из твердой стали — по конструкции, чтобы выдерживать нагрузки, которые она должна принимать для удержания полотна. Хуже того, вы должны просверлить отверстие в неровной поверхности.
Вы также можете вытащить резьбовую деталь другими способами, но вы должны делать все это, не повреждая там внутреннюю резьбу, иначе вы НИКОГДА не сможете закрепить там новую деталь.
Как я уже сказал, если у вас нет нескольких важных инструментов, все это может быть легче отремонтировано, просто купив новую раму для ножовки. Деньги решают все, хотя рама для ножовки стоит не так уж и дорого. И если вы не знаете, как извлечь этот фрагмент винта, то, вероятно, у вас нет этих инструментов, и вы не будете использовать их достаточно часто в будущем, чтобы заслужить их покупку. В то же время хорошо иметь возможность отремонтировать такие вещи, поэтому, если у вас есть интерес и желание выполнять такую работу в будущем, тогда дерзайте.Но не удивляйтесь, если вы обнаружите, что на покупку новой рамы для ножовки у вас уйдет гораздо больше времени и средств, чем того стоит на самом деле.
Теплопроводность металлов, металлических элементов и сплавов
Теплопроводность — к — это количество тепла, передаваемого за счет единичного температурного градиента в единицу времени в установившихся условиях в направлении, нормальном к поверхности единицы площади. Теплопроводность — к — используется в уравнении Фурье.
Металл, металлический элемент или сплав | Температура — t — ( o C) | Теплопроводность — k — | |||||||||||||||||
---|---|---|---|---|---|---|---|---|---|---|---|---|---|---|---|---|---|---|---|
Алюминий | -73 | 237 | |||||||||||||||||
« | 0 | 236 | |||||||||||||||||
127 | 240 | 127 | 240 | 9058||||||||||||||||
« | 527 | 220 | |||||||||||||||||
Алюминий — дюралюминий (94-96% Al, 3-5% Cu, следы Mg) | 20 | 164 | |||||||||||||||||
Алюминий — силумин (87% Al, 13% Si) | 20 | 164 | |||||||||||||||||
Алюминиевая бронза | 0-25 | 70 | |||||||||||||||||
Алюминиевый сплав 3003, прокат | 0-25 | 9 0583 190||||||||||||||||||
Алюминиевый сплав 2014.отожженный | 0-25 | 190 | |||||||||||||||||
Алюминиевый сплав 360 | 0-25 | 150 | |||||||||||||||||
Сурьма | -73 | 30,2 | |||||||||||||||||
« | 127 | 21,2 | |||||||||||||||||
» | 327 | 18,2 | |||||||||||||||||
« | 527 | 16,8 | |||||||||||||||||
Beryllium | 218 | ||||||||||||||||||
« | 127 | 161 | |||||||||||||||||
» | 327 | 126 | |||||||||||||||||
9055 | 527 | 107 7 | 107 7 | 9058« | 927 | 73 | |||||||||||||
Бериллий медь 25 | 9058 3 0-2580 | ||||||||||||||||||
Висмут | -73 | 9.7 | |||||||||||||||||
« | 0 | 8,2 | |||||||||||||||||
Бор | -73 | 52,5 | |||||||||||||||||
» | 0 | 31,7 | 9058 « | 327 | 11,3 | ||||||||||||||
» | 527 | 8,1 | |||||||||||||||||
« | 727 | 6.3 | |||||||||||||||||
» | 927 9058.2 | ||||||||||||||||||
Кадмий | -73 | 99,3 | |||||||||||||||||
« | 0 | 97,5 | |||||||||||||||||
» | 127 | 94,7 | 9058 CZ | 9058 9055 9058 C 9058« | 0 | 36,1 | |||||||||||||
Хром | -73 | 111 | |||||||||||||||||
» | 0 | 94,8 | |||||||||||||||||
127 | 3 | ||||||||||||||||||
« | 327 | 80,5 | |||||||||||||||||
» | 527 | 71,3 | |||||||||||||||||
« | 727 | 65,3 | 9055 9559 | -73 | 122 | ||||||||||||||
« | 0 | 104 | |||||||||||||||||
» | 127 | 84,8 | |||||||||||||||||
Медь | -73 4 | Медь | -73 | 401 | |||||||||||||||
« | 127 | 392 | |||||||||||||||||
» | 327 | 383 | |||||||||||||||||
« | 527 | 371 | 527 | 371 | « | 927 | 342 | ||||||||||||
Медь электролитическая (ETP) | 0-25 | 390 | |||||||||||||||||
Медь — Адмиралтейская латунь | 20 | 111 | |||||||||||||||||
Медь — алюминиевая бронза (95% Cu, 5% Al) | 20 | 83 9055 — 9057 9057 Бронза (75% Cu, 25% Sn) | 20 | 26 | |||||||||||||||
Медь — латунь (желтая латунь) (70% Cu, 30% Zn) | 20 | 111 | |||||||||||||||||
Медь — патронная латунь (UNS C26000) | 20 | 120 | |||||||||||||||||
Медь — константан (60% Cu, 40% Ni) | 20 | 22.7 | |||||||||||||||||
Медь — немецкое серебро (62% Cu, 15% Ni, 22% Zn) | 20 | 24,9 | |||||||||||||||||
Медь — фосфористая бронза (10% Sn, UNS C52400) | 20 | 50 | |||||||||||||||||
Медь — красная латунь (85% Cu, 9% Sn, 6% Zn) | 20 | 61 | |||||||||||||||||
Купроникель | 20 | 29 | |||||||||||||||||
— | |||||||||||||||||||
« | 0 | 66.7 | |||||||||||||||||
« | 127 | 43,2 | |||||||||||||||||
» | 327 | 27,3 | |||||||||||||||||
« | 527 | 19,8 | 9055 9055 | 927 | 17,4 | ||||||||||||||
Золото | -73 | 327 | |||||||||||||||||
« | 0 | 318 | |||||||||||||||||
» | 127 | 9058 304 | |||||||||||||||||
« | 527 | 292 | |||||||||||||||||
» | 727 | 278 | |||||||||||||||||
« | 927 | 262 | 4 | ||||||||||||||||
« | 0 | 23,3 | |||||||||||||||||
» | 127 | 22,3 | |||||||||||||||||
« | 327 | 21,3 | 9058 | 727 | 20,7 | ||||||||||||||
« | 927 | 20,9 | |||||||||||||||||
Hastelloy C | 0-25 | 12 | |||||||||||||||||
Inconel | 9058 | 0-100 | 12 | ||||||||||||||||
Индий | -73 | 89.7 | |||||||||||||||||
« | 0 | 83,7 | |||||||||||||||||
» | 127 | 75,5 | |||||||||||||||||
Иридий | -73 | 153 | 9055 | 9055 | 9055 « | 127 | 144 | ||||||||||||
» | 327 | 138 | |||||||||||||||||
« | 527 | 132 | |||||||||||||||||
» | 727 126 | 727 126 | 727 126 | 9058 120||||||||||||||||
Железо | -73 | 94 | |||||||||||||||||
« | 0 | 83.5 | |||||||||||||||||
« | 127 | 69,4 | |||||||||||||||||
» | 327 | 54,7 | |||||||||||||||||
« | 527 | 43,3 | 9055 79055 | 927 | 28,2 | ||||||||||||||
Чугун — Литой | 20 | 52 | |||||||||||||||||
Железо — Перлитное железо с шаровидным графитом | 100 | 100 | Кованое железо 59 | ||||||||||||||||
Свинец | -73 | 36.6 | |||||||||||||||||
« | 0 | 35,5 | |||||||||||||||||
» | 127 | 33,8 | |||||||||||||||||
« | 327 | 31,2 | 9058 | 9058 — 9055 | |||||||||||||||
Сурьма свинец (жесткий свинец) | 0-25 | 30 | |||||||||||||||||
Литий | -73 | 88,1 | |||||||||||||||||
« | 0 | 79.2 | |||||||||||||||||
« | 127 | 72,1 | |||||||||||||||||
Магний | -73 | 159 | |||||||||||||||||
» | 0 | 157 | 9058 « | 327 | 149 | ||||||||||||||
» | 527 | 146 | |||||||||||||||||
Магниевый сплав AZ31B | 0-25 | 100 | |||||||||||||||||
Марганец | .17 | ||||||||||||||||||
« | 0 | 7,68 | |||||||||||||||||
Ртуть | -73 | 28,9 | |||||||||||||||||
Молибден | -73 | 143 | 143 | 143 | 143 | « | 127 | 134 | |||||||||||
» | 327 | 126 | |||||||||||||||||
« | 527 | 118 | |||||||||||||||||
» | 7279 | 7279 112 | 105 | ||||||||||||||||
Монель | 0-100 | 26 | |||||||||||||||||
Никель | -73 | 106 | |||||||||||||||||
« | 0 | 94 | |||||||||||||||||
« | 327 | 65,5 | |||||||||||||||||
» | 527 | 67,4 | |||||||||||||||||
« | 727 | 71,8 | 9058 9 9058 9 — Кованый | 0-100 | 61-90 | ||||||||||||||
Мельхиор 50-45 (константан) | 0-25 | 20 | |||||||||||||||||
Ниобий (колумбий) | -73 | 6 | |||||||||||||||||
« | 0 | 53,3 | |||||||||||||||||
» | 127 | 55,2 | |||||||||||||||||
« | 327 | 58.2 | 9058 | 727 | 64,4 | ||||||||||||||
« | 927 | 67,5 | |||||||||||||||||
Осмий | 20 | 61 | |||||||||||||||||
Палладий | 75.5|||||||||||||||||||
Платина | -73 | 72,4 | |||||||||||||||||
« | 0 | 71,5 | |||||||||||||||||
» | 127 | 7371,6 | 9055 « | 527 | 75,5 | ||||||||||||||
» | 727 | 78,6 | |||||||||||||||||
« | 927 | 82,6 | |||||||||||||||||
Плутоний | .0|||||||||||||||||||
Калий | -73 | 104 | |||||||||||||||||
« | 0 | 104 | |||||||||||||||||
» | 127 | 52 | |||||||||||||||||
красный | |||||||||||||||||||
Рений | -73 | 51 | |||||||||||||||||
« | 0 | 48,6 | |||||||||||||||||
» | 127 | 46,1 | |||||||||||||||||
.2 | |||||||||||||||||||
« | 527 | 44,1 | |||||||||||||||||
» | 727 | 44,6 | |||||||||||||||||
« | 927 | 45,7 | 9055 « | 0 | 151 | ||||||||||||||
» | 127 | 146 | |||||||||||||||||
« | 327 | 136 | |||||||||||||||||
» | 527 | 9057 | 527 | 121||||||||||||||||
« | 927 | 115 | |||||||||||||||||
Рубидий | -73 | 58.9 | |||||||||||||||||
« | 0 | 58,3 | |||||||||||||||||
Селен | 20 | 0,52 | |||||||||||||||||
Кремний | -73 | 264 | 9058 9058 | 9058 | 9058 « | 127 | 98,9 | ||||||||||||
» | 327 | 61,9 | |||||||||||||||||
« | 527 | 42,2 | |||||||||||||||||
» | 7272 | ||||||||||||||||||
« | 927 | 25,7 | |||||||||||||||||
Серебро | -73 | 403 | |||||||||||||||||
» | 0 | 428 | 9058 | ||||||||||||||||
327 | 405 | ||||||||||||||||||
» | 527 | 389 | |||||||||||||||||
« | 727 | 374 | |||||||||||||||||
» | 9279 | 138 | |||||||||||||||||
« | 0 | 135 | |||||||||||||||||
Припой 50-50 | 0-25 | 50 | |||||||||||||||||
Сталь — углерод, 0.5% C | 20 | 54 | |||||||||||||||||
Сталь — углерод, 1% C | 20 | 43 | |||||||||||||||||
Сталь — углерод, 1,5% C | 20 | 36 | |||||||||||||||||
» 400 | 36 | ||||||||||||||||||
« | 122 | 33 | |||||||||||||||||
Сталь — хром, 1% Cr | 20 | 61 | |||||||||||||||||
Сталь — хром, 5% Cr | 20 | ||||||||||||||||||
Сталь — хром, 10% Cr | 20 | 31 | |||||||||||||||||
Сталь — хром никель, 15% Cr, 10% Ni | 20 | 19 | |||||||||||||||||
Сталь — хромоникель, 20% Cr , 15% Ni | 20 | 15.1 | |||||||||||||||||
Сталь — Hastelloy B | 20 | 10 | |||||||||||||||||
Сталь — Hastelloy C | 21 | 8,7 | |||||||||||||||||
Сталь — никель, 10% Ni | 20 26 | Сталь — никель, 20% Ni20 | 19 | ||||||||||||||||
Сталь — никель, 40% Ni | 20 | 10 | |||||||||||||||||
Сталь — никель, 60% Ni | 20 | 19 | Сталь — хром никель, 80% никель, 15% никель | 20 | 17 | ||||||||||||||
Сталь — хром никель, 40% никель, 15% никель | 20 | 11.6 | |||||||||||||||||
Сталь — марганец, 1% Mn | 20 | 50 | |||||||||||||||||
Сталь — нержавеющая, тип 304 | 20 | 14,4 | |||||||||||||||||
Сталь — нержавеющая, тип 347 | 203 | ||||||||||||||||||
Сталь — вольфрам, 1% W | 20 | 66 | |||||||||||||||||
Сталь — деформируемый углерод | 0 | 59 | |||||||||||||||||
Тантал | -73 57584 | 5||||||||||||||||||
« | 0 | 57,4 | |||||||||||||||||
» | 127 | 57,8 | |||||||||||||||||
« | 327 | 58.9 | 9058,4 | 727 | 60,2 | ||||||||||||||
« | 927 | 61 | |||||||||||||||||
Торий | 20 | 42 | |||||||||||||||||
Тин | -73 | -73 | -733 | ||||||||||||||||
« | 0 | 68,2 | |||||||||||||||||
» | 127 | 62,2 | |||||||||||||||||
Титан | -73 | 24,5 | « | 127 | 20,4 | ||||||||||||||
» | 327 | 19,4 | |||||||||||||||||
« | 527 | 19,7 | |||||||||||||||||
» | 727 | 727 | 7 | ||||||||||||||||
« | 927 | 22 | |||||||||||||||||
Вольфрам | -73 | 197 | |||||||||||||||||
» | 0 | 182 | 9055 9055 | 9055 9055 9055 9055 9055 9058 « | 327 | 139 | |||||||||||||
» | 527 | 128 | |||||||||||||||||
« | 727 | 121 | |||||||||||||||||
» | 927 | 927 | 115ран25.1 | ||||||||||||||||
« | 0 | 27 | |||||||||||||||||
» | 127 | 29,6 | |||||||||||||||||
« | 327 | 34 | 9058 | 727 | 43,9 | ||||||||||||||
« | 927 | 49 | |||||||||||||||||
Ванадий | -73 | 31,5 | |||||||||||||||||
» | 0 | 3 | |||||||||||||||||
« | 427 | 32,1 | |||||||||||||||||
» | 327 | 34,2 | |||||||||||||||||
« | 527 | 36,3 | 9055 7907 | 927 | 41,2 | ||||||||||||||
Цинк | -73 | 123 | |||||||||||||||||
« | 0 | 122 | |||||||||||||||||
» | 127 | 127 | 127 | 127 | 127 | 9058 105||||||||||||||
Цирконий | -73 | 25.2 | |||||||||||||||||
« | 0 | 23,2 | |||||||||||||||||
» | 127 | 21,6 | |||||||||||||||||
« | 327 | 20,7 | 9058 | 727 | 23,7 | ||||||||||||||
« | 927 | 25,7 |
Сплавы — температура и теплопроводность
Температура и теплопроводность для
- 0002 Hastelloy A
- Advance
- Монель
сплавы:
Изменения структуры и свойств сплава Al-Si, обработанного импульсным электронным пучком, Материалы письма
С использованием современных методов исследования материалов выявлено, что структура литого сплава Al-Si (силумин) многофазна и морфологически неоднородна.Он состоит из зерен твердого раствора и эвтектики Al-Si с разнообразной морфологией. С помощью селективного травления на границах зерен α-твердого раствора обнаруживаются интерметаллиды (AlNiCu и AlMg). Обработка образцов силумина интенсивным импульсным электронным пучком различной плотности приводит к выделению субмикро- и наноразмерных частиц второй фазы. Согласно экспериментам оптимальные плотности энергии электронного пучка составляют 25, 30 и 35 Дж / см 2 . Облучение силумина приводит к многократному улучшению механических и трибологических свойств поверхностных слоев.Как выяснилось, эти характеристики поверхностных слоев существенно меняются из-за субмикро- и наноразмерной структуры ячеистой кристаллизации, образованной электронным пучком, которая свободна от первичных включений, состоящих из кремния и интерметаллических соединений.
中文 翻译 :
脉冲 电子 束 处理 Al-Si 合金 的 组织 和 性能 变化
的 材料 方法 , 发现 铸 的 的 体 和 Al-Si借助 选择性 蚀刻 , α- 固溶 的 的 到 金属 间 (AlNiCu 和 AlMg)) 具有 的 子 束 子 蛋白。 根据 , 电子 束 的 最佳 能量 为 25、30 和 35 J / sm 2 silumin 辐照 导致 表面 层 的 机械 和 倍。 由于 由 子束 形成 的 蜂窝状 结晶 的 亚 微米 和 纳米 级 结构 表面 层 的 这些 特征 发生 了 , 电子 束 不含 由 硅 组成。
Кислота для пайки алюминия своими руками.Способы пайки алюминиевых проводов. Метод химической очистки
Печать
Флюс для пайки алюминия
Когда-то я думал, что пайка алюминия паяется на заводах, а не дома. Однако со временем это заблуждение развеялось. Эта статья о том, как припаять алюминий в домашних условиях и как припаять алюминий.
В школе тема алюминия ранее обсуждалась на уроках химии и физики о его свойствах, он имеет отличные электропроводящие свойства, теплопроводность, но его очень сложно паять.Сложность пайки связана с тем, что на очищенной поверхности моментально образуется оксидная пленка, очень устойчивая к различным агрессивным средам.
Как-то раньше встречал такую информацию, что пайка ведется припоем, состоящим из олова и цинка или олова и висмута. Однако практика показывает, что его вполне нормально паять обычными припоями ПОС 40 и ПОС 60. Как паять, не важно, главное как.
Механическая прочность такой пайки невелика, но в целом требуется не прочность, а электрическая проводимость соединения.Чем еще можно паять алюминий кроме этих припоев, не скажу, не пробовал. Также можно паять свинцом, главное, чтобы мощности паяльника хватило и он нагрелся до достаточной температуры.
Паяльник
Как уже было сказано выше, алюминий обладает повышенной теплопроводностью, недаром из него делают радиаторы охлаждения. Поэтому для пайки крупных элементов мощность паяльника должна быть большой 100-200 Вт.Если, конечно, это два небольших провода, то возможно хватит мощности 60 — 100 Вт.
Флюсы
Сейчас проблем с выбором средства нет, а до этого приходилось использовать аспирин, технический вазелин, солидол с оловянным алюминием. Для пайки алюминия в домашних условиях я выбрал два хороших флюса F-64 и FTBf-A, и флюс FIM также дает хорошие результаты. Это самое главное, пожалуй, чем лучше флюс, тем проще пайка.
Главное не нарваться на подделку, но этого хватит, покупаешь такой «Флюс для пайки алюминия», а он ни на что не годится.Кстати, на вопрос, чем еще можно лужить алюминий, есть такой флюс Ф-34, это можно сказать как раз по его составу — это аспирин. Также возможно лужение алюминия «паяльным жиром»
.Способы лужения
При хорошем флюсе процесс лужения и пайки не проблема … Другое дело, если его нет под рукой, здесь процесс становится более трудоемким.
Самое главное в процессе лужения — исключить контакт очищаемой поверхности с кислородом.Поэтому очищаемую поверхность густо смазывают или заливают флюсом, а при необходимости можно немного прогреть. Если продукт небольшой, например проволока, можно просто зачистить его прямо в растворе, налив его во что-нибудь.
К способу, как паять алюминий паяльником с канифольным раствором, делал примерно так. Поверхность предварительно очистили, смазали раствором и присыпали медной или железной опилкой. Затем, прижав кончиком паяльника (чем жестче, тем лучше) и сняв оксид, залудил обычным припоем.
Иногда при необходимости для пайки двух проводов, например алюминия и меди, я использовал этот метод. Я скрутил два конца проволоки и сварил их токовым разрядом с помощью графитового сердечника от аккумулятора. Для такой «сварки» я использовал трансформатор на 6-12 вольт с током 3 ампера. Подключаем один конец провода от трансформатора к скрутке, а ко второму прикручиваем шток аккумулятора (можно щеткой от двигателя). При прикосновении возникает дуга и концы спаяны в шарик.
Так что паять алюминий в домашних условиях вполне возможно и это не такая уж сложная задача. Немного практики и все.
В настоящее время алюминий и его сплавы широко используются в бытовых электроприборах, таких как алюминиевые электрические провода и т. Д. Поскольку алюминий и его сплавы при контакте с воздухом быстро окисляются, обычные методы пайки не дают удовлетворительных результатов. Ниже описаны различные способы пайки алюминия в домашних условиях оловянно-свинцовыми припоями ПОС-61, ПОС-50, ПОС-90.
1. Для пайки двух алюминиевых проводов они предварительно луженые. Для этого конец провода покрывают канифолью, кладут на наждачную бумагу (со средней зернистостью) и прижимают к ней горячим луженым паяльником, при этом паяльник не снимается с провода и канифоли. все время добавляется к заслуженному концу. Проволока хорошо залужена, но все операции приходится повторять много раз. Далее пайка продолжается в обычном режиме. Наилучшие результаты дает использование минерального масла для швейных машин или щелочного масла (для очистки оружия после стрельбы) вместо канифоли.
2. Пайка листового алюминия или его сплавов осуществляется следующим образом: горячим паяльником на шов наносится канифоль с мелкими железными опилками. Паяльник лужен, и им начинают протирать шов, все время добавляя припой. Опилки своими острыми краями удаляют оксид с поверхности, и олово прочно прилегает к алюминию. Паять хорошо нагретым паяльником. Для пайки тонкого алюминия достаточно мощности паяльника 50 Вт, для алюминия толщиной 1 мм и более желательна мощность 90 Вт, при толщине более 2 мм точку пайки нужно прогреть паяльником и только после этого нанести флюс и припой.Минеральное масло здесь также с успехом можно использовать в качестве флюса.
3. Оригинальный способ пайки алюминиевых проводов и алюминиевой поверхности. Перед пайкой алюминиевая поверхность алюминиевой детали предварительно покрывается медью с помощью простейшего гальванического станка, описанного ранее. Но вы можете сделать это проще.
— +
Рис. Один
Для этого берется толстая кисть для акварели, металлический ободок которой, касаясь волосков, обматывается голой медной проволокой (рис.1). Другой конец провода подключается к положительному полюсу источника постоянного тока (выпрямитель, аккумулятор фонарика или аккумулятор). Алюминиевая деталь подключается к отрицательному полюсу. Место пайки зачищается наждачной бумагой. Приступая к покрытию детали, кисть необходимо тщательно смочить в насыщенном растворе медного купороса, и водить по детали, как при покраске. Спустя какое-то время на поверхности алюминиевой детали оседает слой красной меди, которую после промывки и сушки залуживают обычным способом (паяльником).
Примечание. В промышленности и ремонтной практике для пайки монтажных элементов из алюминия и его сплавов, а также соединения их с медью и другими металлами используются припои марок П150А, П250А и П300А. Пайка осуществляется обычным паяльником, жало которого нагревается до температуры 350 ° С, с использованием флюса, представляющего собой смесь олеиновой кислоты и иодида лития.
- Этапы лужения
- Проволока алюминиевая лужение
Для получения надежного соединения при пайке оловянно-свинцовым припоем необходимо зачистить и облучить провода.
Если этими действиями пренебречь, то шип вряд ли получится качественным и прочным.
В первую очередь следует подготовить паяльник, при необходимости провести его обслуживание: снять шкалу ножом, очистить жало паяльника на мелкозернистом наждачном круге или напильником.
Перед началом пайки паяльник необходимо прогреть до рабочей температуры. Затем окуните жало в канифоль, дотроньтесь до твердого олова или оловянно-свинцового
.Если на кончике паяльника образовался тонкий блестящий слой припоя (а не свисающая капля), можно переходить к дальнейшим работам.
Все металлы в воздухе окисляются. Их поверхность покрыта оксидной пленкой, предотвращающей смачивание металла расплавленным припоем. Поэтому все паяемые поверхности необходимо зачистить до металлического блеска ножом или мелкой наждачной бумагой; дополнительно его можно обезжиривать растворителями.
Паяльником нужно прогреть провод, нанести на него канифоль, втирать в него припой неторопливыми движениями.
Если все сечение проводника равномерно
копаем припоем, лужение можно прекратить.
Лужение медных проводов особых проблем не вызывает. С этой работой справится даже начинающий припой. Но далеко не все мастера умеют залудить алюминиевую проволоку.
Паять алюминиевую проволоку в домашних условиях сложно, многие мастера за такую работу не берутся.
Как паять алюминий
Проблема в том, что при удалении оксидной пленки алюминий в воздухе почти мгновенно окисляется, и пленка восстанавливается. Но, проявив терпение, можно получить достаточно качественный припой.
- готовят флюс растворением канифоли в диэтиловом эфире;
- подготовка стальной опилки;
- зачистите провод обычным способом;
- немедленно нанести флюс на проволоку;
- посыпать место пайки металлической стружкой;
- осторожно проведите лужение, втирая припой в алюминий.
Металлическая стружка играет роль абразивных частиц и постоянно разрушает образующуюся оксидную пленку.
При необходимости их нужно залить в место склеивания.
Этот метод не всегда гарантирует достижение желаемого результата. Контакт между припаянными проводами может быть плохим и непродолжительным.
Профессионалы предпочитают использовать специальные припои и флюсы. При этом паяемую проволоку следует прогревать не паяльником, а газовой горелкой или паяльной лампой. Температура нагрева припоя и луженой проволоки должна быть не менее 600 ° С.
Еще один простой способ лужения алюминиевых проводов с помощью медных проводов.
Он основан на явлении электролиза.Для этого нужно запастись концентрированным раствором медного купороса и источником постоянного тока мощностью не менее 10 Вт. Несколько капель медного купороса наносятся на очищенный алюминий в точке пайки и оборачиваются вокруг него несколькими витками медной проволоки.
Алюминиевый провод подключается к отрицательному полюсу источника тока, а медный — к положительному. В цепи возникает электрический ток, происходит электролиз, алюминиевый проводник покрывается тонким слоем меди.На алюминиевом проводе образуется слой луженой меди. Этот метод нельзя использовать для лужения массивных деталей, но он вполне подходит для пайки тонких проводников.
Если сульфата меди нет, его можно заменить соляной кислотой.
В месте предполагаемой пайки нужно сдвинуть медный проводник с давлением. В этом случае электролиз протекает более эффективно. Но необходимо помнить, что точка пайки с применением кислоты со временем окисляется, поэтому после окончания работ ее необходимо промыть чистой водой или слабым раствором щелочи.
Кожа — Алюминий
Алюминиевая форма не используется для облегчения пайки и производится после обработки цинком изделия и.
Для пайки и лужения алюминия используйте ультразвуковой паяльник.
Известно, что алюминий на воздухе быстро покрывается слоем оксидной пленки, которая препятствует прилипанию припоя к металлу. Под действием ультразвука оксидная пленка разрушается и удаляется с поверхности алюминия.
Алюминий особенно трудно закаливать.Ультразвуковая закалка, используемая для пайки узких швов, не подходит для утонения больших поверхностей, таких как алюминиевые шины.
На заводе «Динамо» разработали метод абразивной и абразивно-кристаллической обработки алюминиевых покрышек.
Алюминий особенно трудно чистить. Ультразвуковая закалка, используемая для пайки с узкими калибрами, не подходит для утонения больших поверхностей алюминиевых шин.
Алюминий особенно трудно чистить.
Ультразвуковое упрочнение, используемое для пайки узкими калибрами, не подходит для утонения больших поверхностей алюминиевых шин.На заводе «Динамо» разработали метод абразивной и абразивно-кристаллической обработки алюминиевых покрышек.
Помимо ультразвуковых паяльных машин, для шлифовки алюминия используются абразивные растворители. В отличие от обычных паяльников, абразивные шлифовальные детали 5 (рис.
68), спрессованный из порошка припоя и асбеста, который действует как абразив.
Проблемы при пайке, сварке и фрезеровании алюминия и его сплавов из-за наличия на их поверхности чрезвычайно стабильной оксидной пленки легко устраняются с помощью ультразвука.
Помимо ультразвуковых паяльных машин, для шлифовки алюминия используются абразивные растворители.
В отличие от обычных электрических паяльников, абразивные шлифовальные машины имеют рабочий стержень 5 (рис. 68), спрессованный из порошка припоя и асбеста, которые действуют как абразив.
Важным преимуществом перед вышеупомянутыми калиево-алюминиевыми методами является использование ультразвука.
Ультразвуковая пайка используется для пайки и лужения алюминия.
Рубрика: «Работа с металлом»
Алюминий на воздухе быстро покрывается оксидным слоем, препятствующим прилипанию припоя к металлу.Под действием ультразвука оксидная пленка разрушается и удаляется с поверхности, в результате чего припой становится доступным для доступа к поверхности алюминия.
Страниц: 1 2
Паять любые металлические детали в домашних условиях — дело несложное, многие мальчишки, особенно увлекающиеся радиотехникой, легко с этим справляются. Для пайки или лужения понадобится сам паяльник (самый примитивный, требующий нагрева у источника тепла или более продвинутый — с регулируемой температурой), припой, флюс и канифоль.
Детали, подготовленные к пайке, очищают и обезжиривают наждачной бумагой, бензином или растворителями.
Затем на поверхность наносится флюс, предотвращающий процессы окисления на паяемых деталях.
Паяльником, жало которого предварительно окунут в канифоль, на место пайки наносится припой.
Как самому припаять алюминий
Однако не все так просто — некоторые металлы и сплавы трудно паять.
Как паять алюминий? Сложность состоит в том, что алюминиевые сплавы окисляются на воздухе за доли секунды, образуя пленки, которые делают пайку обычными методами невозможной.
Однако есть метод, позволяющий паять алюминиевые поверхности с помощью самого обычного паяльника, припоя и канифоли.
Для пайки алюминия потребуется достаточно мощный паяльник (60-100 Вт), так как этот металл имеет очень хорошую теплопроводность.
Может потребоваться дополнительный прогрев паяемых деталей над пламенем газовой плиты.
Секрет в том, что место склеивания натирают кирпичом, песком, раствором и сразу заливают канифолью.
Протираем паяльные детали жало паяльника, удаляя оксидную пленку.
В результате получается очень прочная связь без особых затрат.
Припой для алюминия, состоящий из олова и цинка (олова и висмута) вместе с парафином и стеариновым флюсом, также дает хороший результат, если припой защищен от окисления канифолью.
Как паять алюминий, если речь идет о проводах? В этом случае, вероятно, можно вообще обойтись без пайки: например, использовать клеммник.
Если вам необходимо подключить провода в ограниченном пространстве, где нельзя установить клеммную колодку или аналогичный разъем?
Тогда лучше просто скрутить (намотать провода один на другой) и припаять, сдавить плоскогубцами.
Активный флюс на основе фосфорной кислоты для пайки алюминия сегодня легко доступен.
Вы можете купить его в любом магазине, где продаются всевозможные радиоприемники, а также электронные детали и аксессуары.
Это, наверное, самый простой и эффективный способ пайки алюминия.
Еще по теме:
Состав флюсов для высокотемпературной пайки приведен в соответствующем разделе.
В таблице показаны состав, температурные диапазоны активности и назначение некоторых флюсов, разработанных с 1973 по 1984 год. Среди органических кислот и других веществ, пригодных в качестве активатора флюсов для пайки алюминия и его сплавов при температуре
Среди алифатических кислот наиболее активными являются одноосновные кислоты: стеариновая, элаидиновая, олеиновая, лауриновая, коприновая, каприловая, нейлоновая, валериановая, масляная, пропионовая, уксусная, муравьиная.Активность этих кислот увеличивается с увеличением их относительной молекулярной массы и температуры плавления. При их взаимодействии с оксидом Al2O3 протекают следующие реакции:
Al2O3 + 6RCOOH → 2 (RCOO) 3Al + 3h3O (1)
2Al + 6RCOOH → (RCOO) 3Al + ЗН2 (2)
Наиболее интенсивно реакция протекает с муравьиной и уксусной кислотами, менее интенсивно — с капроновой кислотой.
Однако введение этих кислот во флюсы малоперспективно из-за их интенсивного выкипания при температуре пайки и уменьшения энергии разрыва связи СОО-НС — с увеличением молекулярной массы кислоты.Соли карбоновых кислот, полученные по реакциям (1) и (2), термически нестабильны. Например, ацетат алюминия разлагается при температуре 200 ° C.
Марка или номер флюса | Состав флюса,% | Температура Интервал активности, ° С | Примечание |
1 | 4-7 борфторид аммония; 4-7 борфторид кадмия; опора из эпоксидной смолы | Для пайки алюминия и алюминиевого сплава — 2% Mg (AMg2). Высокая коррозионная стойкость | |
Форма 59A | 10 ± 0,5 фторборат кадмия; 2,5 ± 0,5 фторборат цинка; 5 ± 0,5 фторборат аммония; 82 ± 1 триэтаноламин | 150-320 | Для пайки алюминия или сплава AMts с медью и стали с припоями на основе: Sn — Zn, |
Форма 61A | 10 фторборат цинка; 8 фторборат аммония; 82 триэтаноламин | 150-320 | Для пайки алюминия, бериллиевой бронзы, оцинкованного железа, меди с припоями на основе Sn — Zn, Zn — Cd |
Форма 54A | 10 фторборат кадмия; 8 фторборат аммония; 82 триэтаноламин | 150-320 | |
3 | 7 бромид висмута; 47.9 уксусная кислота; 55,1 олеиновая кислота | Для лужения в жидком олове более активен, чем флюс F54A | |
4 | Для лужения алюминиевых сплавов, слабокоррозионно-активный | ||
5 | 1,5 триэтаноламин; 4 салициловой кислоты; 94,5 спирт этиловый | 150-320 | Для пайки алюминия с медью, бериллиевой бронзой, оцинкованного железа с припоями на основе Sn-Zn и Zn-Cd |
6 | 30 г иодида лития; 200 мл олеиновой кислоты | Для пайки алюминия | |
7 | 4.2-10 йодид титана; Канифоль 16,8-22; капроновая кислота — остальное | ||
8 | |||
9 | 10-15 тетрафторборат цинка; баланс триэтаноламина | ≥350 | Для пайки алюминиевых изолированных проводов (повышает устойчивость) Для пайки алюминия |
10 | 7,5 фторгидрат анилина; 92,5 канифоль | ||
11 | 83 триэтаноламин; 9 фторборат кадмия; 7 кислый фторид аммония; 1 канифоль | > 150 |
Среди двухосновных насыщенных кислот, которые сильнее одноосновных, первые три члена гомологического ряда кислот (щавелевая, малоновая, янтарная) не проявляют активности при пайке алюминия, что связано с их декарбоксилированием при нагревании.
Высшие кислоты обладают такой же активностью в потоках, как одноосновные кислоты, с тем же числом атомов в радикале.
Ангидриды кислот не активны при пайке. Галогензамещенные кислоты обладают более высокой активностью в флюсах для пайки алюминия, что объясняется одновременным действием на оксид алюминия как карбоксильной группы, так и атома галогена.
Обнаружено, что в составе флюсов активны некоторые твердые аминокислоты: α-аминопропионовая кислота и фениланитронил, обеспечивающие хорошее растекание припоя.
Принимая во внимание физические свойства, степень токсичности и активности в потоках среди органических кислот, наиболее подходящими являются высшие жидкие незамещенные кислоты, их твердые аналоги и аминокислоты.
Флюсирующая способность смесей кислот в любом соотношении не превышает активности компонента с наибольшей молекулярной массой.
Салициламид и мочевина по активности эквивалентны действию нейлона или элаидиновой кислоты.
Добавление солей в кислые растворы
Активность аммониевых солей органических кислот близка к активности исходных одно- и двухосновных кислот.Эти соли имеют преимущества перед амидами — меньшая летучесть при пайке и лучшая растворимость в кислотах.
Характерно, что введение в триэтаноламин органических кислот и их производных не увеличивает его активности при флюсовании алюминиевых сплавов.
Дальнейшее повышение флюсующей активности кислых органических растворов достигается добавлением к ним галлоидных солей аминов или металлов.
Введение LiI и SnCb в дециловый спирт (точка кипения 231 ° C) или в капроновую кислоту (точка кипения 205 ° C) LiBr, LiI, NaI, SnCb в виде кристаллогидратов активирует раствор.
Введение солей этилового спирта 95% в кислые флюсирующие растворы дезактивирует их из-за вытеснения воды по реакции:
Al (OR) 3 + 3h3O → Al (OH) 3 + 3ROH.
Однако присутствие кристаллизационной воды в спиртовом растворе хлорида олова не влияет на его активность при пайке.
Реактивные органические флюсы
Реактивные органические флюсы предложены для пайки алюминия легкоплавкими сплавами.
Основу этих флюсов составляет органический аминоспирт триэтаноламин, а активаторами — фторбораты тяжелых металлов и аммония.В местах контакта фторборатов с алюминием металлы: кадмий и цинк выделяются через неоднородности в оксидной пленке Al2O3. Остатки триэтаноламина при нагревании переходят в инертное смолистое вещество, не вызывающее коррозии паяных соединений. Эти флюсы и их остатки после пайки имеют pH = 8, что также подтверждает их некоррозионную активность.
Все эти флюсы не отличаются по коррозионной активности при пайке алюминия, но при пайке со сплавом АМц, медью и ее сплавами наиболее эффективен флюс F59A.Температурный диапазон активности этих флюсов составляет 150-300 ° С. Флюсы данного типа непригодны для пайки внахлест с наложением припоя в зазоре деформируемых сплавов АМг, Д1, Д16, В95 и литых алюминиевых сплавов. Их можно использовать только при лужении паяемой поверхности алюминия с последующей пайкой, например, флюсом ЛТИ-120.
В этом случае температура между свариваемыми деталями при пайке не должна отличаться более чем на 10 ° С.
Как паять алюминий паяльником
Остатки флюсов легко смываются водой или протираются влажной тканью, смоченной водой или этиловым спиртом, и не вызывают заметной коррозии более 1000 часов.Исследования показали, что по сравнению с флюсами, содержащими уксусную, нейлоновую, олеиновую, лауриновую кислоту, и в качестве активатора хлорида висмута, флюс F54A обеспечивает большую площадь растекания припоя P250A по алюминию AD1; но он менее активен при пайке коррозионно-стойкой стали, латуни и меди, чем флюсы, содержащие хлорид висмута.
Флюсы F54A, F59A и F61A подходят для пайки в указанном диапазоне температур с припоями P200A, P250A, P300A, P170A и P150A.
Для этого используются терморегулирующие электрические паяльники, индукционный нагрев и пайка погружением в расплавленный припой.Пайка этими флюсами при нагреве открытым пламенем недопустима из-за возможности их возгорания. При температурах выше 350 ° C в паяных соединениях контактных соединений, выполненных с использованием этих флюсов, образуется непропан. При быстром нагреве (электроконтакт, индукция) в чистом аргоне пайка этими флюсами возможна при температуре 320 ° С.
Имеются данные об использовании легкоплавкого припоя Sn — (8-15)% Zn- (2 -5)% Pb с температурой плавления 190 ° C для пайки алюминиевых сплавов с флюсом в виде раствора фторида бора и фторида аммония в моноэтаноламине.
В флюсах для низкотемпературной пайки алюминия и его сплавов вместо канифоли предлагается использовать более жаростойкий, чем канифоль, пентаэритритбензоат, его остатки не вызывают коррозии и в виде эластичного пленка, предохраняющая паяные швы от окисления. Карбоновые кислоты используются в качестве активатора флюса. Паяные соединения (припой Р250) не разрушаются в физиологическом растворе в течение 200 суток. Проволочный припой (Sn-Pb-Ag) с сердечником из указанного флюса подходит для пайки всех алюминиевых материалов, содержащих менее 3% Mg и 3% Si.
У мастеров нет проблем с пайкой медных, латунных и стальных проводов и деталей, но если нам приходится иметь дело с алюминиевыми поверхностями, припой не удерживает изделие, и пайка превращается в пытку. Проблемы вызваны тем, что на поверхности этого металла образуется тонкая, но очень прочная оксидная пленка Al2O3. Эту пленку можно удалить механически — например, очистить изделие наклейкой для ногтей, но при контакте с воздухом или водой металл сразу же покроется пленкой.
Несмотря на проблемы, с которыми мы сталкиваемся, изделия из алюминия можно паять. Паять алюминий можно несколькими способами.
Пайка алюминиевых сплавов
Отличные результаты можно получить со следующими сплавами:
- два куска цинка и восемь кусков олова
- одна медь и 99 штук олова
- один кусок висмута и 30 штук олова
Перед пайкой сплав и деталь должны быть хорошо нагреты.
Также следует помнить, что в этом способе пайки следует использовать кислоту для пайки.
Пайка алюминия специальными токами
Стандартные токи не растворяют оксидную пленку на поверхности алюминия, поэтому необходимо использовать специальные активные токи.
Флюс для пайки алюминия применяется для работы плоскогубцами с температурой эксплуатации 250-360 градусов. Этот поток во время пайки и закалки очищает оксидную пленку, очищает поверхность металла и, следовательно, припой лучше распределяется по поверхности.
Все это приводит к созданию более плотного и прочного соединения расплавленных деталей. Избыток этого потока легко удаляется растворителями, спиртом или специальными жидкостями.
Другие способы пайки алюминия
Есть и нестандартные способы решения этой проблемы, например:
- Тщательно очистите алюминиевые детали от паяльника и добавьте несколько капель концентрированного сульфата меди.
Небольшой отрезок медного провода, зачищенный по кругу диаметром, равным точке пайки, и свободный конец провода подсоединяют к плюсовой клемме аккумулятора на 4.5 вольт. Часть проволоки с катящимся кругом попадает на небольшое количество медного купороса. Отрицательный аккумулятор следует подключить к той части, на которую через определенное время будет установлен определенный слой меди.
Как припаять алюминий консервной банкой
После высыхания в этой комнате обычно можно сварить необходимые детали или проволоку.
- В этом случае используйте абразивный порошок с небольшим количеством трансформаторного масла, чтобы получить жидкую пасту.
Паста предназначена для тонких паяльных изделий.Тогда паяльник хорошо сваривается и наносит эти пятна до тех пор, пока на поверхностях не отделится слой олова. Затем промойте детали и спаяйте обычным способом.
- Для этого метода требуется трансформатор.
Его минус связан с изделием, а большая часть медного провода, состоящего из небольших сосудов, подключена к соединению. Если вы подключите этот провод к будущей точке пайки в течение короткого времени, будет сделан микропайка из меди и алюминия, что в будущем позволит подключить провод обычным способом.
Для упрощения процесса можно использовать паяльную кислоту.
Паяльная посуда алюминиевая (без паяльника)
В некоторых бытовых нуждах используется алюминиевая фурнитура, иногда ломается и не покупают новую (что очень дорого), эти изделия можно починить пайкой без паяльника.
Следующий метод подходит для заделки небольших отверстий (до 7 мм в диаметре).
- Место пайки следует очистить до металлического блеска с помощью наждачной бумаги или напильника.Если емкости эмалированные, отверстия вокруг эмали необходимо удалить в радиусе 5 миллиметров.
Для этого из емкости попадает свет на молоток, который отбрасывается эмалью. Затем нужно очистить металл.
- Место пайки смазывают выдувной кислотой или покрывают канифолью. Изнутри над отверстием кладут кусок горшка и нагревают каменку на огне печи.
Если емкости покрыты эмалью, желательно нагревать их над лампочкой — это позволяет нагреть место сильнее, чтобы другие губки не нагревались.
- При нагревании слизь тает и закрывает отверстие в горшочке.
При этом паяльник не нужен.
Часто в радиолюбительской практике и даже в быту встает вопрос о пайке алюминия. Электрические провода, корпуса, негерметичные емкости — мало ли что. Но, к сожалению, алюминий и его сплавы не очень любят паять. Этот материал можно даже лужить (покрывать слоем припоя), и это проблема, а не только качественная пайка.Единственный выход, как принято считать, — это сварка, причем специальная сварка, например, аргонодуговая сварка. Тем не менее, алюминий по-прежнему можно паять, причем качественно, в домашних условиях и без использования специальных инструментов и технологий.
«Не спаян» — не совсем правильное утверждение. Скорее плохо припаян. Дело в том, что алюминий практически мгновенно окисляется на воздухе, покрываясь чрезвычайно прочной оксидной пленкой, не покрытой никаким металлом. Но если эта пленка разрушается, то паять алюминий не сложнее, чем ту же медь.Другое дело, что оксид алюминия — очень прочное соединение. Вы, наверное, слышали о фрезах из корунда, который представляет собой оксид алюминия.
С одной стороны, этот оксидный слой надежно защищает алюминий от дальнейшего окисления и разрушения, а с другой — значительно усложняет процесс пайки. Причем разрушить его обычными нейтральными флюсами — той же канифолью — невозможно. Но если вы все же найдете такой флюс, то паять алюминий в домашних условиях легко.
Флюсы для пайки алюминия
Как упоминалось выше, пленка оксида алюминия чрезвычайно прочная, и ее очень трудно разрушить химическими методами. Тем не менее существует множество составов, позволяющих этой самой пленке не только разрушиться, но и предотвратить появление нового оксидного слоя до завершения процесса пайки. Выбирая тот или иной флюс, в первую очередь следует руководствоваться типом пайки — паяльником или горелкой. Неправильно подобранный состав либо не даст желаемого результата, если его не нагревать, либо просто выгорит в пламени, например, газовой горелки.
Если вы собираетесь работать с легкоплавкими припоями и использовать паяльник, то есть смысл обратить внимание на флюс F-59A и ему подобные (F61A, F64 и др.). Он обладает высокой активностью и отлично разрушает даже толстый слой оксидной пленки при относительно низкой температуре нагрева обычным паяльником.
Но нельзя использовать для пайки горелкой и жаропрочных припоев. Если тому же F-59A удастся даже разрушить оксид, в процессе дальнейшего нагрева он просто выгорит, и по сути его задача не только удалить корунд, но и предотвратить окисление алюминия до конца срока службы. процесс пайки.
Для работы с высокотемпературными припоями придется использовать что-то еще, например, флюс F-34A (AF-4A, Castolin 190 Flux и др.), Который выдерживает температуру до 610 градусов.
Высокотемпературный флюс для алюминия
Почему не подходит для работы с паяльником? Поскольку нижний порог активности этого флюса составляет 520 градусов, его просто нельзя нагреть паяльником до нужной температуры, а значит и активировать.
Конечно, выбор мастера не ограничивается вышеперечисленными композициями.Их очень много — как отечественных, так и импортных. Таким образом, у вас есть из чего выбирать, исходя как из стоимости, так и по доступности.
Припои для алюминия
Паять алюминий можно как обычными свинцово-оловянными припоями, так и специальными, содержащими алюминий, цинк, серебро и другие металлы и даже неметаллы (например, кремний). POS-припои, как и специальные для алюминия, имеют разную температуру плавления, что необходимо учитывать как при работе с ними, так и при эксплуатации отремонтированного изделия.
Если вы решили паять посуду, соприкасающуюся с пищевыми продуктами (канистра, фляга, трубка для дистиллятора и т. Д.), То использовать припои, содержащие свинец, нельзя. Придется выполнить высокотемпературную пайку с использованием, например, припоя 34А, содержащего медь, кремний и, конечно же, алюминий. Подходит ЦОП-40, содержащий цинк.
Припой для пайки алюминия Алюминий-13
Другой вариант — пайка чистым оловом. Он отлично подходит для ремонта кухонной утвари и имеет низкую температуру плавления, а это значит, что работу можно выполнять с помощью паяльника.Но при использовании олова следите за тем, чтобы точка пайки не сильно нагревалась во время работы изделия. Например, можно припаять дно чайника оловом (он соприкасается с водой и не нагревается выше 100 градусов), но клюв того же чайника отвалится после первого закипания.
Особого внимания заслуживают так называемые флюсы, которые уже содержат специальный флюс (обычно в виде покрытия, но не обязательно).Бытует мнение, что для работы с ними флюс вообще не нужен и в принципе это так. Тем не менее, очень желательно защитить паяное соединение от окисления во время работы. Для этих целей подойдет любой пассивный флюс, выдерживающий температуру пайки. Идеальным решением здесь может стать обычное трансформаторное масло, которое используют электрики при пайке высоковольтных муфт.
Припой для алюминия с флюсовым покрытием
Среди недостатков порошковых сплавов можно отметить их более высокую стоимость, разовое использование (припой неиспользован, но после нагрева повторно его не использовать) и необходимость опыта работы с такими составами.
Выбор источника тепла
Тут выбор не очень большой:
- паяльник обыкновенный;
- открыть огонь.
Первый вариант подойдет, если не требуется особая механическая прочность стыка. Например, вам нужен надежный электрический контакт или какая-то деталь, не несущая большой механической нагрузки. Допустим, дырявая кружка, чтобы не текла. Второй вариант предполагает тот или иной тип горелки и использование тугоплавкого припоя.Он намного сложнее первого, но позволяет получить прочное механическое соединение, как говорится, веками.
Паять металл обычным паяльником
Как уже упоминалось выше, вы можете паять алюминий легкоплавкими припоями с помощью обычного и привычного паяльника. Единственное условие — мощность инструмента должна быть достаточной для нагрева деталей, подлежащих пайке, до необходимой температуры.
Если вы умеете работать с паяльником, то проблем с пайкой алюминия у вас не возникнет (ну или почти никогда).Вы очищаете детали, покрываете их соответствующим флюсом и припаиваете. Хорошей идеей будет добавить немного мелкого абразива в область пайки, смазанную флюсом, что поможет очистить паяные поверхности от оксидной пленки.
Если в вашем распоряжении нет паяльника достаточной мощности, то паяемые детали можно нагревать параллельно горелке (слегка) или даже пламенем газовой горелки.
Некоторым электрикам вообще удается паять алюминий «таким, какой он есть», и с точки зрения электрической прочности его паять хорошо.Вы также можете использовать этот метод при соединении, например, двух алюминиевых проводов. Для этого вам понадобится:
- любой абразивный порошок, например мелкий песок;
- обычное машинное масло (лучше оружейное).
Вылить абразив на ровную поверхность, капнуть масло, погрузить зачищенную алюминиевую проволоку в состав и, взяв припой на наконечник, «натереть» им эту проволоку. Абразив снимает оксид, масло предотвращает образование новой пленки, а припой на полдня надежно покрывает алюминий.
Единственный недостаток этого метода — малая механическая прочность соединения, поэтому перед окончательной пайкой проводников их необходимо скрутить после лужения. Электрическая прочность такой пачки отличная, поэтому, если она не сломается механически, то простоять десятилетиями.
Применение газовой горелки
Если вы решили использовать для пайки алюминия тугоплавкие припои, то без открытого пламени не обойтись. В этом случае следует обратить внимание на следующие нюансы:
- Пламя должно быть качественным — не курить, поддерживать постоянную температуру и размер горелки.
- Пайка открытым пламенем требует значительного опыта в поддержании оптимальной температуры нагрева, так как «температурный коридор» качественной пайки достаточно узок. Перегрев — потеря механической прочности или даже потек алюминия. Недогретый — тугоплавкий припой не плавится.
Для выполнения первого условия, например, огонь или пламя свечи не подходят — дымят. Горелка газовой плиты? Он не дымит, но выдержать температуру нагрева паяемых деталей очень сложно даже профессионалу — малейшее движение по вертикали или горизонтали и температура «ушла».
К тому же в руку газовую горелку взять нельзя, а значит, придется держать в руках детали, которые нужно паять. Если предмет массивный, вы просто не сможете держать его в пламени в постоянном движении, чтобы поддерживать нужную температуру, пытаясь паять другой рукой. Ну раз уж вы будете нагревать снизу, то для нормальной пайки придется перегреть деталь (припаять нужно сверху), а значит, она легко расплавится. Тем не менее, по крайней мере, можно паять алюминий поверх газа, но только по крайней мере.
Идеально подойдет газовая горелка. Он компактен (в смысле самой горелки, а не емкости для нее), не дымит, мало весит. Но, к сожалению, получить его не всегда удается.
Самым простым выходом из ситуации может стать небольшая паяльная лампа. Чтобы было легче, только не заправляйте прибор бензином «под шею». Перед тем, как приступить к пайке, лампу нужно хорошенько прогреть, чтобы она не дымила.
Будем считать, что горелка прогрета, а детали, подлежащие пайке, зачищены и плотно прижаты друг к другу в месте будущей пайки.Нанесите на детали соответствующий флюс (если вы используете флюсовый припой, используйте трансформаторное масло в качестве флюса) и начните нагрев. За температурой нагрева необходимо постоянно следить кусочком припоя, касаясь места будущей пайки.
Как только припой начнет плавиться, постарайтесь поддерживать постоянную температуру (это придет с практикой) и протрите припой куском припоя, полностью залуживая его. Как только лужение закончится, вы можете припаять той же деталью, используя ее в качестве электрода для сварки.Часто при пайке муфт электрики используют тугоплавкий припой только для лужения оболочки кабеля, а после этого муфту припаивают обычным легкоплавким припоем.
Дело в том, что гильза сделана из свинца и просто не выдерживает тепла, необходимого для плавления тугоплавкого алюминиевого припоя. Но если обе части, конечно, алюминиевые, то лучше паять и лужить тугоплавким припоем — стык деталей будет иметь высокую электрическую и механическую прочность.
Как паять силумин
Прежде всего, давайте определим, что силумин — это сплав алюминия с кремнием и ничего больше.Например, сплав ЗАМ (цинк, алюминий, магний) — это совершенно другой материал. Если вы уверены, что держите в руках деталь из силумина, то можете смело браться за пайку — силумин можно паять по той же технологии, что и алюминий. Другое дело, что силуминовые детали обычно работают при довольно высокой механической нагрузке. Материал и без того, мягко говоря, бедный в этом плане, а если еще и припаять …
Вы все еще хотите отпаять лопнувший силумин кран? В принципе, это реально, но соседей снизу все же стоит пожалеть.Что касается сплава ЦАМ, который по внешнему виду очень похож на силумин, то хорошо и прочно его припаять не получится. Только «слюнявчик».
Промышленное производство алюминия по историческим меркам началось сравнительно недавно. Но за это время этот материал прочно вошел в нашу жизнь. Его основные параметры — высокая электрическая и теплопроводность, малый вес, устойчивость к коррозии — привели к тому, что этот металл стал основным материалом, применяемым в авиационной и космической отраслях.Кроме того, невозможно представить улицы наших городов без алюминия, из него делают светопрозрачные конструкции (двери, окна, витражи), рекламные конструкции и многое другое.
При его обработке допустимо использовать практически все виды обработки — токарную, штамповочную, литье, сварку и пайку. Последние методы используются для получения неразъемных соединений алюминиевых заготовок.
Общие принципы пайки алюминия в домашних условиях
Многие искренне считают, что пайка алюминия в домашних условиях — довольно сложный процесс.Но на самом деле все не так уж и плохо. Если использовать соответствующие припои и флюсы, то особых сложностей возникнуть не должно. В том случае, если домашний мастер паяет алюминиевые детали из материалов, предназначенных для меди или стали, результат, скорее всего, будет отрицательным.
Технологические особенности
Трудности при пайке алюминия в первую очередь связаны с тем, что на его поверхности имеется оксидная пленка, которая, в отличие от основного металла, имеет более высокую температуру плавления и высокую стойкость к различным химическим веществам.Именно эта пленка создает серьезные препятствия при использовании традиционных припоев и флюсов, а если, например, паять алюминий с оловом, то качественный результат гарантировать сложно. Для удаления этой пленки используются либо механическое воздействие, либо флюсы, содержащие сильнодействующие химические вещества.
Сам основной металл, в данном случае алюминий, имеет низкую температуру плавления, около 660 ° C. Эта разница между температурой плавления оксидной пленки и основного металла также приводит к трудностям при пайке.
Это свойство алюминия в результате приводит к тому, что нагретый алюминий становится слабее. Таким образом, алюминиевые конструкции начинают терять устойчивость даже при температурах 250-300 ° С. Кроме того, в состав алюминиевых сплавов могут входить материалы, которые начинают плавиться при температуре 500-650 ° С.
Большое количество припои включают олово, кадмий и другие компоненты. Алюминий практически не контактирует с этими материалами, а это, в свою очередь, приводит к тому, что швы, полученные с помощью этих припоев, отличаются низкой надежностью и прочностью.Между тем цинк и алюминий хорошо растворимы друг в друге. Использование цинка в составе припоев позволяет придать шву высокие прочностные параметры.
Использование трансформаторного масла
Как отмечалось выше, основным препятствием для пайки является наличие оксидной пленки. Перед пайкой алюминия его необходимо удалить. Для его удаления используются разные методы, начиная от использования абразивного инструмента и заканчивая специальными флюсами. Кроме того, существуют еще и «народные» методы. Один из них связан с использованием трансформаторного масла.
Для удаления оксидной пленки используется следующий состав — в абразивный порошок добавляется трансформаторное масло. При постоянном помешивании в результате должна получиться пастообразная масса. Его необходимо наносить на предварительно очищенную зону пайки. После этого жало паяльника нужно хорошенько покрыть металлом и натереть подготовленные места до появления олова. После этого места пайки необходимо промыть и можно продолжать работу.
Какой припой используется для пайки алюминия
Большинство припоев содержат вещества, не растворяющиеся в алюминии.Поэтому для создания неразъемных соединений алюминиевых деталей используются так называемые тугоплавкие припои на основе алюминия, кадмия, цинка и некоторых других веществ.
Легкоплавкие припои также используются для пайки алюминия.
Их использование позволяет выполнять работы при низких температурах. Это позволяет создавать соединения, избегая изменения свойств алюминия. Но сразу стоит отметить, что использование таких материалов не может обеспечить должной степени коррозионной стойкости и прочности соединения.
Оптимальный результат пайки можно получить при использовании состава, содержащего алюминий, медь, цинк. Работу с такими припоями необходимо производить паяльником, жало которого нагревается до 350 ° С. При соединении деталей нужно использовать флюс, который состоит из смеси олеиновой кислоты и йодида лития.
Состав для соединения алюминиевых деталей можно приготовить дома, а можно просто приобрести в магазине.
Одним из имеющихся в продаже припоев для алюминия является HTS-2000.Пайка этим припоем возможна без использования флюса. Отличительной особенностью этого состава является то, что он может проникать через оксидную пленку и создавать прочные связи между молекулами. Срок службы соединений из этого сплава — 10 лет.
Как правильно паять горелкой
Потребность в пайке алюминия и его сплавов может возникнуть как в промышленных, так и в бытовых условиях. Этот процесс можно использовать при ремонте деталей, но иногда вам приходится иметь дело с более крупными работами.
Обработка алюминия сопряжена с рядом трудностей, поэтому традиционные материалы технологии пайки не всегда гарантируют должный результат.
Один из наиболее часто используемых методов получения неразъемных соединений напрямую связан с использованием газовой горелки.
Работа с алюминием означает, что оксидная пленка на поверхности детали препятствует соединению деталей.
Пайка горелкой существенно отличается от работы паяльником и по праву считается более практичной.Работая с конфоркой, мастер может регулировать температуру. А это дает дополнительные возможности для обработки поверхности заготовок. В этом случае толщина материала особой роли не играет. Иногда при работе с горелкой используются флюсы и дополнительная обработка поверхности.
Пайка алюминия газовой горелкой в домашних условиях позволяет предварительно нагревать заготовки и расходные материалы.
Несомненно, для получения качественного соединения необходим опыт.Дело в том, что алюминий имеет низкую температуру плавления; соответственно расходные материалы, используемые для пайки, обладают хорошей текучестью. Если мастер ошибается, то велика вероятность, что припой просто растечется по заготовке, не задев шва.
Какой флюс использовать
Преимущества
Пайка — один из способов получения прочных соединений металлов. Но в отличие от других методов до недавнего времени отличался невысокой производительностью, малой прочностью на стыке.По этой и ряду других причин он не получил широкого промышленного применения.
С развитием технологий стали доступны методы соединения деталей с помощью электронного луча и ультразвуковых волн. Появление специальных припоев и флюсов позволило значительно улучшить качество паяного соединения.
Современные технологии пайки позволяют использовать готовые изделия без дальнейшей обработки на механическом оборудовании. Пайка вошла в число основных технологических процессов в машиностроении, авиационной и космической отраслях и, конечно же, в электронике.
Пайка имеет ряд неоспоримых преимуществ перед сваркой. Таким образом, процесс соединения деталей происходит при значительно меньшем расходе тепла. Другими словами, во время этого процесса не происходит серьезных изменений в структуре металла. Его физико-химические параметры практически не меняются. После пайки могут возникнуть такие явления, как остаточная деформация, ее размеры несопоставимы с теми, которые остаются после выполнения, например, сварки в облаке защитных газов.
Поэтому использование пайки гарантирует более точное соблюдение размеров, указанных в технической документации на изделие. Использование этого метода позволяет соединять разнородные металлы. Кроме того, можно сказать, что эти процессы достаточно легко автоматизировать.
недостатки
Говоря о пайке алюминиевых деталей, всегда нужно помнить, что для работы с ней необходимо использовать специальные припои и флюсы, которые способны удовлетворить требования к качеству получаемых соединений.
Малейшее нарушение технологии или использование неподходящих материалов приведет к тому, что полученный шов не будет соответствовать требованиям качества.
Это невероятно простой способ пайки алюминия. С его помощью любой желающий, дома или в гараже, сможет без проблем отремонтировать и восстановить любые изделия из алюминия, без аргонной сварки. Вы легко изготовите различные конструкции из алюминиевого профиля и многое другое.
Теперь, чтобы припаять радиатор или раму велосипеда из алюминия, необязательно идти в мастерскую и отдавать много денег, все можно паять в домашних условиях.
При правильном подходе пайка оказывается не хуже сварного соединения, но, безусловно, надежнее любой холодной сварки, которая обычно используется как альтернатива.
Понадобится
А газовая горелка не обязательно должна быть профессиональной. Достаточно обычной форсунки на газовый баллон, или подойдет любая другая.Более подробно расскажу о специализированном припое, который необходимо будет приобрести. Это трубчатый порошковый припой, специально разработанный для пайки алюминия (почему порошок? — порошок внутри трубки).Он состоит из двух компонентов: оболочки и порошковой основы внутри. Не будем вдаваться в подробности химического состава, это бесполезно.
Его можно купить в специализированных магазинах и использовать в автомастерских. Самый доступный способ для всех — купить его в.
Недорого, советую сразу брать упаковку — в жизни обязательно пригодится.
Пайка алюминия газовой горелкой
Берем профиль или детали, которые нужно сварить.Очищаем поверхность металлической щеткой. Как вариант, можно использовать грубую наждачную бумагу. Чем больше шероховатость паяльной поверхности, тем лучше будет соединение с припоем.
Закрепляем соединение хомутом или другим приспособлением. Включаем газовую горелку и разогреваем стык.
Привозим трубчатый припой. Он плавится и растекается по шву.
Весь процесс происходит при температуре около 450 градусов Цельсия.
Припой обладает невероятной текучестью и сам течет в любые, даже самые маленькие трещины в металле.
После распределения припоя еще немного прогреваем стык, чтобы он распределился и максимально растекся в стыках узла.
Подведем итоги
Лично я, когда узнал о таком простом и доступном способе пайки, был невероятно удивлен. Думаю, мне удалось вас тоже удивить, если, конечно, о нем раньше не знали.Несколько слов о надежности. Конечно, выигрывает сварка, так как конструкции бывают комбинированные и смешанные, но этот способ ничем не уступает.Если соединение гнулось, гнется сама деталь. Паяное соединение чрезвычайно надежно и вполне способно выдерживать практически любые нагрузки, как если бы соединение было литым.
Единственное, если пайка не совсем качественная, скорее всего не хватает нагрева горелкой. В остальных случаях все держится плотно.
Теперь вам не составит труда пропаять отверстие в алюминиевом поддоне, сделать резервуар из листового металла, а из профиля сделать стеллаж.