Припои. Какой выбрать для пайки?
Какие бывают припои, и какие у них свойства?
В начале своей радиолюбительской деятельности многие начинающие радиолюбители редко задаются вопросом о том, какие бывают припои и каковы их свойства.
Для сборки простейших самодельных устройств достаточно самого распространённого ПОС-61 или ему подобного. Как говориться: «Было бы, чем паять…»
Припой можно даже не покупать. Достаточно взять старую печатную плату от какого-нибудь электронного прибора и собрать его разогретым жалом паяльника с паяных контактов.
Особенно такой метод «добычи» актуален для тех, кто живёт вдали от городов и крупных населённых пунктов, где нет возможности побывать в магазине радиотоваров.
Припой, собранный с печатных плат
Но всё же, припой припою рознь. В своей практике человек, имеющий дело с электроникой, должен разбираться в вопросе его выбора. Поэтому рассмотрим подробно, какие бывают припои, для чего они применяются, какой из них лучше использовать для монтажа электронных схем и ремонта бытовой радиоаппаратуры.
Какие бывают припои?
Припои делят на мягкие (легкоплавкие) и твёрдые. Для монтажа радиоаппаратуры применяются как раз легкоплавкие, т.е. такие, температура плавления которых лежит в пределах до 300 – 4500C. Мягкие припои по своей прочности уступают твёрдым, но для сборки электронных приборов применяются именно они.
Припой представляет собой сплав металлов. Для легкоплавких припоев это, как правило, сплав олова и свинца. Именно эти металлы составляют большую часть в сплаве. Также в нём могут присутствовать и легирующие металлы, но их количество в составе невелико. Примеси других металлов вводят в сплав для получения определённых характеристик (температуры плавления, пластичности, прочности, устойчивости к коррозии).
Наибольшее распространение получил припой марки ПОС (Припой Оловянно-Свинцовый). Далее за кратким обозначением его марки следует число, которое показывает процентное содержание в нём олова. Так в ПОС-40 содержится 40% олова, а в ПОС-60, соответственно, 60%.
Бывает, что в пользование попадает припой неизвестной марки. Приблизительно оценить его состав можно по косвенным признакам:
Припои оловянно-свинцовой группы имеют температуру плавления 183 – 2650C.
Если припой имеет яркий металлический блеск, то в нём достаточно большое содержание олова (ПОС-61, ПОС-90).
И, наоборот, если он тёмно-серого цвета, а поверхность матовая, то это указывает на большое содержание свинца. Именно свинец придаёт поверхности своеобразный сероватый оттенок.
Припои, в которых много свинца очень пластичны.
Так, например, пруток припоя диаметром 8 мм. с большим содержанием свинца (ПОС-30, ПОС-40) легко гнётся руками. Олово, в отличие от свинца, придаёт сплаву прочность и жёсткость. Если олова в сплаве много, то легко погнуть такой пруток уже не получится.
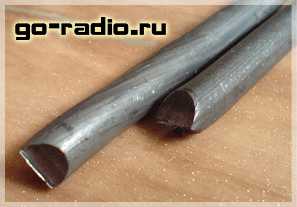
ПОС-40 (пруток)
Рассмотрим, в каких целях используются припои оловянно-свинцовой группы (ПОС).
ПОС-90 (Sn 90%, Pb 10%). Применяется при ремонте пищевой посуды и медицинского оборудования. Как видим, в нём небольшое содержание свинца (10%), который достаточно токсичен и его применение в вещах, соприкасающихся с пищей и водой недопустимо.
ПОС-40 (Sn 40%, Pb 60%). В основном служит для пайки электроаппаратуры и деталей из оцинкованного железа, применяется для ремонта радиаторов, латунных и медных трубопроводов.
ПОС-30 (Sn 30%, Pb 70%). Его применяют в кабельной промышленности, а также используют для лужения и пайки листового цинка.
И, наконец, ПОС-61 (Sn 61%, Pb 39%). Тоже, что и ПОС-60. Думаю, между ними особой разницы нет.
ПОС-61 используется для лужения и пайки печатных плат радиоаппаратуры. Именно он в основном служит материалом для сборки электроники. Температура его плавления начинается со 183 0C, а полное расплавление достигается при температуре в 1900C.
Производить пайку таким припоем можно с помощью обычного паяльного инструмента не боясь перегрева радиоэлементов, поскольку полное его расплавление достигается уже при 1900C.
ПОС-30,ПОС-40,ПОС-90 полностью расплавляются при температурах в 220 – 2650C. Для многих радиоэлектронных компонентов такая температура является предкритической. Поэтому для сборки самодельных электронных устройств лучше использовать ПОС-61.
Зарубежным аналогом ПОС-61 можно вполне считать припой Sn63Pb37 (олова 63%, свинца 37%). Он также применяется для пайки радиоаппаратуры и для изготовления самодельной электроники. Радиолюбители выбирают именно его, как альтернативу отечественному ПОС-61.
Как правило, любой припой продаётся в катушках или тюбиках по 10 ~ 100 грамм. На упаковке указывается состав сплава, например, так: Alloy 60/40 («Сплав 60/40» – он же ПОС-60). Имеет форму проволоки разного диаметра (от 0,25 до 3мм).
Также не редкость, что в его состав входит флюс (FLUX), которым заполнена сердцевина проволоки. Содержание флюса указывается в процентах (обычно от 1 до 3,5%). Такой форм-фактор очень удобен. При работе нет необходимости отдельно подавать флюс к месту пайки.
Одной из разновидностей припоев ПОС является припой марки ПОССу. Да, если произнести вслух, то звучит не очень то презентабельно . Но, несмотря на это, оловянно-свинцовый припой c сурьмой (именно так расшифровывается сокращённое обозначение) применяется в автомобилестроении, в холодильном оборудовании, для пайки обмоток электрических машин, элементов электроаппаратуры, моточных деталей и кабельных изделий. Хорошо подходит для пайки оцинкованных деталей. В таком сплаве кроме свинца и олова присутствует от 0,5% до 2% сурьмы.
Припой | Начальная t0 плавления (Солидус) | Полное расплавление (Ликвидус), t0 |
ПОССу-61-0,5 | 183 | 189 |
ПОССу-40-2 | 185 | 229 |
ПОССу-40-0,5 | 183 | 235 |
ПОССу-30-2 | 185 | 250 |
ПОССу-30-0,5 | 183 | 255 |
Как видим из таблицы, припой ПОССу-61-0,5 наиболее подходит для замены ПОС-61, так как имеет температуру полного расплавления – 1890C.
Стоит отметить, что существует и полностью бессвинцовый оловянно-сурьмянистый припой ПОСу 95-5 (Sn 95%, Sb 5%). Температура его плавления 234 – 2400С.
Низкотемпературные припои.
Далее по убыванию температуры плавления идёт сплав РОЗЕ (Sn 25%, Pb 25%, Bi 50%). Маркируется как ПОСВ-50. Температура его плавления ниже температуры кипения воды и составляет 90 – 940C. Он предназначен для пайки меди и латуни. В составе сплава РОЗЕ олово занимает 25%, свинец – 25%, висмут – 50%. Процентное соотношение металлов в сплаве может немного отличаться. Обычно указывается в графе «Состав» на упаковке.
Находит применение в плавких защитных предохранителях, которые можно обнаружить в любой радиоаппаратуре.
Ещё более низкотемпературным является сплав ВУДА (Sn 10%, Pb 40%, Bi 40%, Cd 10%). Его температура плавления 65 – 720C. Так как в сплаве ВУДА присутствует кадмий (10%), то он токсичен, в отличие от сплава РОЗЕ.
Стоит отметить, что сплавы РОЗЕ и ВУДА достаточно дороги.
Паяльная паста.
В конце и без того длинного повествования хотелось бы немного рассказать о паяльной пасте. Используется она в основном для пайки поверхностно монтируемых компонентов (SMD’шек) и безвыводных микросхем в корпусах BGA.
На вид представляет собой серого цвета кашицу и состоит из о-о-очень мелких шариков сплава
Паяльная паста Solder Plus
Применяется паяльная паста при сложном ремонте мобильных телефонов для пайки микросхем в корпусе BGA. Для её использования требуется дополнительное оборудование для ремонта сотовых телефонов, например, специальные трафареты. Стоимость такой пасты довольно высока. Да и не удивительно, ведь в её составе есть серебро.
В настоящее время в производстве электроники стали массово применяться бессвинцовые припои.
Главная » Радиоэлектроника для начинающих » Текущая страница
Также Вам будет интересно узнать:
go-radio.ru
Пайка нержавейки твердыми припоями — выбор флюса для пайки
На сегодняшний день, пайка нержавейки твердыми припоями используется в тех областях, где требуется достигнуть максимально прочного соединения, не прибегая к сварке. Данный метод соединения относится к промежуточному положению между сваркой и низкотемпературной пайкой. В отличие от использования мягких припоев, твердые потом могут использоваться в условиях высокотемпературной эксплуатации. Процесс спаивания не влияет на структуру металла, что не приводит к их деформации и разупрочнению. Активно все это используется при изготовлении металлорежущих инструментов, как резцы с твердосплавными пластинами и прочие. Благодаря такой спайке получается высокая прочность соединения и нет негативного воздействия на геометрию и прочность пластин, к которым припаиваются детали.
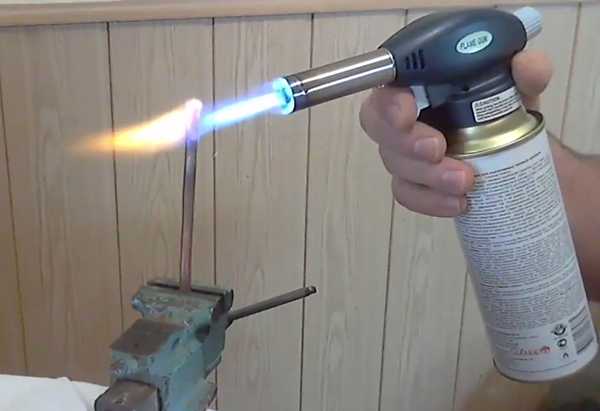
Пайка нержавейки твердыми припоями
Твердая пайка нержавейки применяется также при ремонте и изготовлении сосудов из нержавеющей стали, соединения труб, которые могут служить для проводки воды или охладительных систем. Особенно активно она используется там, где затруднительна сварка. Ее можно встретить при ремонте автомобильных двигателей, радиаторов и трансмиссии. Благодаря высокому качеству соединения выдерживают даже упругие деформации и значительны нагрузки. Для многих вариантов ремонта, этот процесс не имеет альтернативы. Технология контролируется по ГОСТ 1499-54.
Преимущества пайки нержавейки твердыми припоями
- Пайка нержавейки твердыми припоями является самой качественной из всех возможных вариантов;
- Такой метод используется в промышленности для ответственных соединений, работающих в сложных условиях;
- Соединение может применяться даже в местах с высокой температурой;
- Детали стойки к различного рода нагрузкам;
- Процесс пайки происходит относительно быстро и не требует большого количества подготовительных процедур;
- Ею намного легче ремонтировать детали в станкостроительной сфере;
- Во время обработки температура является не столь высокой, чтобы деформировать металл заготовок, как это случается при сварке.
Недостатки пайки нержавейки твердыми припоями
- Если сравнивать с использованием других припоев, то процесс получается более трудоемким;
- Твердые сплавы нередко оказываются более дорогостоящими, как и себестоимость пайки, за счет того, что используется больше ресурсов;
- Далеко не каждый инструмент может дать ту температуру, которая требуется для этого процесса, поэтому, в домашних условиях он оказывается трудноосуществимым.
Подготовка оборудования и материалов
Перед тем как паять нержавейку твердым припоем, следует заняться подготовкой. Для проведения пайки нужно подобрать правильную горелку, которая бы смогла выдать требуемую температуру и обладала достаточной шириной пламени, чтобы равномерно обрабатывать поверхность.
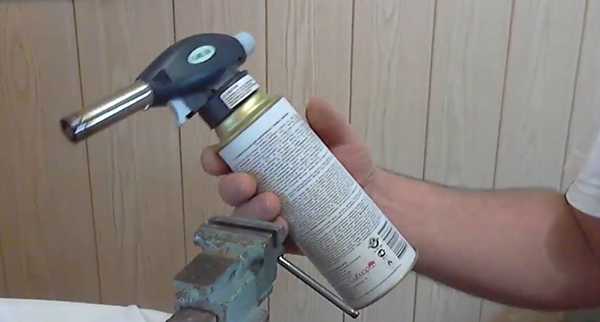
Выбор горелки для пайки припоями
Следует сделать так, чтобы под рукой всегда находился флюс и припой, чтобы вовремя сделать все нужные процедуры. Перед работой нужно подготовить все под заданный режим работы и проверить работоспособность инструментов.
Отличия высокотемпературной пайки от низкотемпературной
При высокотемпературном спаивании используется нагрев при помощи горелки, тогда как в ином случае применяется электрический нагрев.
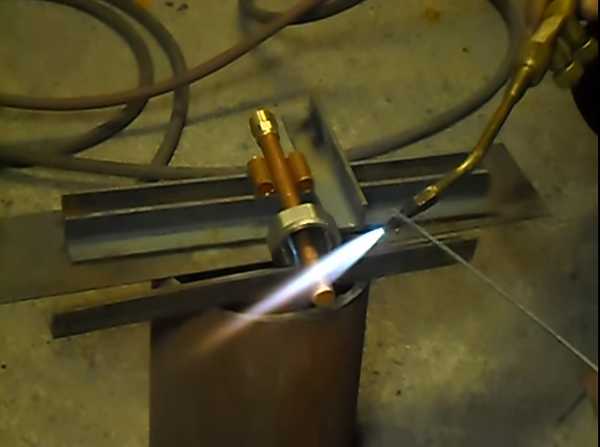
Высокотемпературная пайка нержавейки
Также различается температура плавления самого припоя. В первом случае она намного более высокая, что также влияет и на качество соединения, так как оно становится значительно выше. Низкотемпературная пайка, впоследствии, выдерживает меньшие температурные режимы воздействия. Высокотемпературная может вызывать структурные изменения в металле, если температура его плавления близка к той, которая используется при обработке. Для них также используется оборудование различной мощности.
Выбор твердого припоя
Медно-цинковый припой представлен в серии ПМЦ с различным содержанием меди. Его часто используют вместе с дополнительным легированием, чтобы снизить сильную отдачу при вибрации.
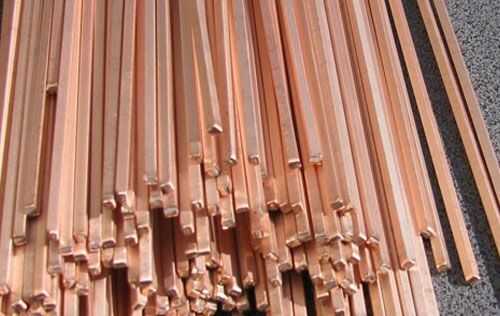
Медно-цинковый припой
Медно-фосфорный представлен в серии ПМФ с различным содержанием фосфора, в зависимости от цифры модели. У него хорошая устойчивость к коррозии и высокая текучесть. Иногда его могут использовать для замены серебряного припоя.
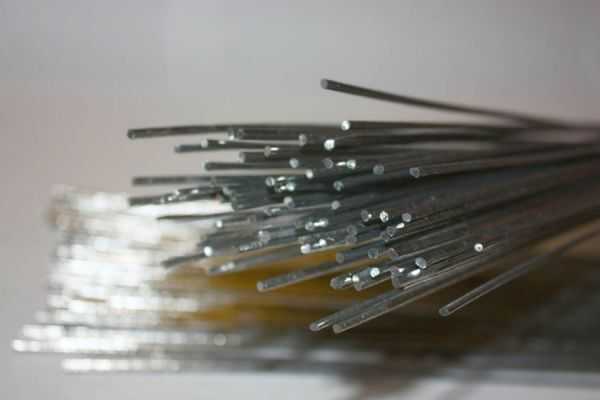
Медно-фосфорный припой
Медно-циноквые обладают высокими технологическими свойствам. При добавлении олова температура плавления снижается, так что он относится к универсальным припоям.
«Обратите внимание!
Для каждой процедуры выбор материала может отличаться, что зависит от свойств деталей.»
Выбор флюса
Пайка нержавеющей стали твердыми припоями требует тщательного подбора флюса. Одним из лучших вариантов для данного металла состоит на 70% из буры, на 20% из борной кислоты и на 10% из фтористого кальция.
Технология пайки нержавейки твердым припоем
- Зачистить механическим способом стыковые части деталей.
- Зафиксировать заготовки в неподвижном положении.
- Зону, где будет происходить спайка, нужно промазать флюсом.
- Горелка зажигается и устанавливается на нужный режим.
- Постепенно прогревается зона спайки, пока не изменится цвет металла.
- К детали подается припой, который может быть сразу покрыт флюсом.
- Осуществляется постепенное запаивание поверхности, передвигая расходный материал вдоль линии спайки.
«Важно!
Пламя горелки не должно содержать в себе слишком много кислорода, так как он окисляет поверхность заготовок и делает соединение менее надежным.»
Контроль качества шва
Существует несколько способов проверить, насколько хорошо все спаялось. Для этого используют такие методы как:
- Параметрический;
- Трансформаторный;
- Люминесцентный;
- Цветной;
- Оптический;
- Визуальный.
Меры безопасности
Даже когда происходит пайка пищевой нержавейки твердыми припоями в домашних условиях, то следует придерживаться правил безопасности. Во-первых, для пищевой нержавейки припой не должен содержать цинк или свинец. Также не стоит забывать о высоких температурах, с которыми идет работа и брать все незащищенными руками раньше времени остывания. Баллон с газом должен находиться на достаточном расстоянии от открытого огня горелки.
Почему пайка может не получиться?
Основными причинами неудач являются:
- Недостаточно хорошая зачистка перед самим процессом;
- Плохой разогрев заготовки, так что припой не смог нормально сцепиться с металлом;
- Был неправильно подобран припой для такого соединения;
- Было использовано недостаточное количество флюса, так что материал не начал плавиться, как того требовала технология;
- После спайки, когда все еще не остыло, было механическое воздействие со сдвигом детали.
svarkaipayka.ru
Припой для пайки медных труб: твердый припой, флюс, горелка
Присоединить разнообразные жесткие изделия можно с помощью процесса припаивания, который сопровождается сложными процессами с химической и физической точки зрения. В наши дни владельцы домов и квартир монтируют в своих жилищах трубы в основном из медного или алюминиевого материала (см. Алюминиевая труба). При этом часто появляется необходимость не только правильно установить медные элементы трубных систем, но и качественно их отремонтировать. Для этого обязательно придется приобрести специальный инструмент, оснащение и материалы. Неотъемлемой деталью при паянии труб из меди является припой, при подборе которого необходимо учесть ряд важных замечаний.
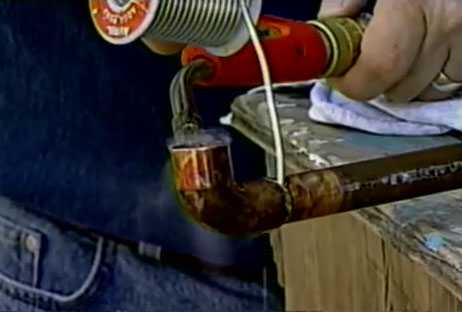
Как подбирать припой?
При паянии медных изделий применяются как мягкие, так и твердые виды припоев. В случае использования мягкого припоя для соединения труб из меди необходимо достичь температуры в пределах 4250С. При припаивании посредством твердых видов припоя следует добиться рабочей температуры для паяния до 460-5600С. В этих случаях используется газовая горелка.
Увеличить качество присоединения труб из меди можно при использовании припоев медно-фосфорного типа, но при этом у них возрастет температура плавки и снизится смачиваемость, по сравнению с серебряными тинолями.
В процессе припаивания медных деталей посредством припоя медно-фосфорного типа использовать флюс нет необходимости. При обычном присоединении медных изделий между собой, а также меди с бронзовыми элементами обязательно используется флюс. Микрозазор при употреблении серебряных тинолей должен находиться в пределах 0-0,15 мм, а в случае применения припоев медно-фосфорного типа – 0,025-0,15 мм.
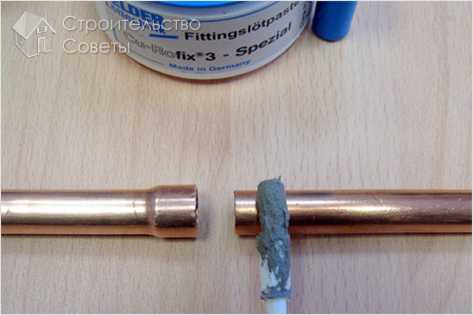
Медно-фосфорный тип припоя
Трехкомпонентные припои медно-фосфорного типа с процентным содержанием серебра до 15% применяются при воздействии высокой температуры в основном в холодильном производстве при использовании газа.
Специальные характеристики
Тиноли медно-фосфорного типа имеют невысокую температуру плавления. Такой тип материала значительно текуч в процессе работы с металлическими изделиями различного состава с содержанием меди. Положительным моментом данного случая является отсутствие необходимости в использовании флюса при работе с таким припоем, так как фосфор уже в нем находится.
Образовавшиеся швы при паянии таким способом получаются надежными и качественными. Такие прочные соединения требуются при использовании установок в холодильной промышленности. Холодильные установки работают с присоединениями, которые подвергаются небольшим вибрационным влияниям. При этом высокое содержание серебра в припое делает материал достаточно пластичным.
В процессе паяния арматурных деталей следует охлаждать нетермостойкие части для исключения перегревов. При присоединении металлических деталей необходимо обязательно применять продувку таким веществом, как сухой азот посредством специальной установки. Это необходимо выполнять с целью исключения образования окалины на оборудовании. Вещества медно-фосфорного состава не применяются при работе со стальными деталями, из-за появления рассыпчатой пленки из фосфитов на созданном шве.
Виды медно-фосфорных припоев существуют такие:
- Тип 102. Трехкомпонентный материал медно-фосфорного типа с процентным содержанием серебра в пределах 2%. Такой сплав является достаточно недорогим, имеет среднее растекание. Представляется возможным применять при установке холодильного оборудования при соединении деталей, на которые не действует вибрационная сила. При этом необходимо приобрести паяльник или газовую горелку;
- Тип 105. Трехкомпонентный материал медно-фосфорного типа с процентным содержанием серебра в пределах 5%. Такой материал имеет пластичность и медленное растекание, благодаря чему появляется возможность заполнять большие зазоры. Важно отметить, что присоединение медных деталей таким способом образовавшийся паяный шов сможет перенести небольшое вибрационное воздействие и мелкие удары. Рекомендуется применять для присоединения медных изделий, а также сплавов с ней в холодильных системах;
- Тип 115. Трехкомпонентный материал медно-фосфорного вида с процентным содержанием серебра в пределах 15%. В результате высокого процентного содержание серебра изделие имеет высокую степень пластичности. Такой способ рекомендуется использовать для присоединения медных деталей, сплавов с ней. Образованный шов после паяния способен переносить средние удары и вибрационные явления в период меняющихся тепловых режимов. Популярно используется такой метод при соединении холодильных систем, в которых применяется специальный газ.
Припои из серебра
Такие серебряные «инструменты» с высоким процентным содержанием серебра до 55 % при высокотемпературных процессах в сфере пищевой промышленности с применением холодильного оборудования.
Специфика тинолей из серебра
Невысокая температура плавления, относительно хорошее смачивание материала при паянии являются главными достоинствами припоев из серебра. Такой материал достаточно хорошо заполняет зазоры между стыкуемыми деталями, при этом создаются плотные и вакуумные швы.
Такие паяные швы требуются для монтажа и изготовления холодильных установок. Данный тиноль имеет более низкую температуру растекания по сравнению с остальными материалами припоя. Настоящий вариант позволяет применять данный припой в период обработки арматурных частей системы.
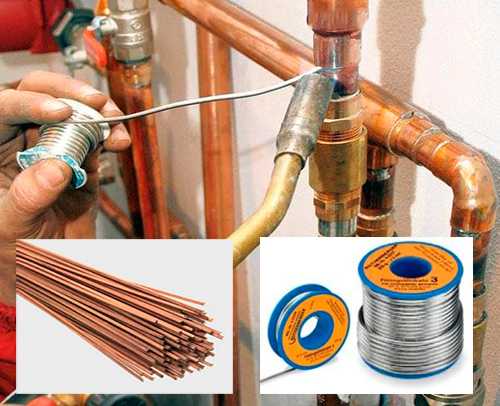
Виды серебряных тинолей существуют такие:
- Тип 1530. Четырехкомпонентное вещество с процентным содержанием серебра в пределах 30%. Достаточно недорогое, имеет среднее растекание по отделываемой поверхности, достаточно хорошо заполняет зазоры. Используется в различных устанавливаемых системах кроме пищевого оборудования из-за наличия вредного кадмия;
- Тип 530Sn. Четырехкомпонентный материал с процентным содержанием серебра до 30%. Имеет высокую температуру плавки, которая достигается посредством газовой горелки. При этом создается отличный паяный шов при любом расположении детали. Стоит отметить, что это еще не все положительные моменты;
- Тип 538Sn. Четырехкомпонентный материал с процентным содержанием серебра до 38%.
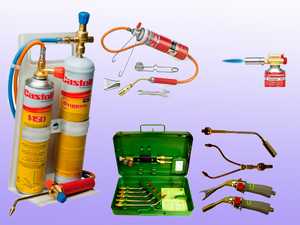
Припаивание изделий твердым тинолем
В настоящее время существует такой способ соединения металлов, как применение твердого припоя, который замечательно подходит для создания капиллярной и щелевой пайки, присоединения труб из меди для подачи воды, установки газопроводов и холодильного оборудования. Такой способ позволяет формировать надежное и качественное соединение в период работы с присоединяемыми материалами.
С целью присоединения труб из меди иногда применяется специальная паста, газ и другие вспомогательные инструменты и оснащение. Для надежного и безопасного припаивания необходимо изучить соответствующие инструкции по технологии пайки и технике безопасности.
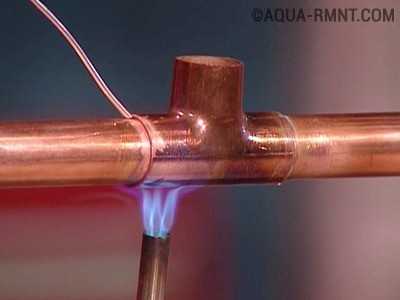
Как припаивать трубы?
С целью присоединения металлических заготовок собственными руками необходимо приобрести специальный инструмент, оснащение и материалы.
Для осуществления припаивания понадобится следующий инструмент:
1. Труборез.
2. Газовая горелка.
3. Шерсть металлическая.
4. Припой бессвинцовый.
5. Флюс.
Процесс паяния такой:
- Очистить участок присоединяемой детали и нанести порцию флюса;
- Надеть очищенный фитинг вручную, применяя специальный инструмент;
- Применяя газовую горелку, разогреть присоединяемый участок меди до заметного изменения ее цвета;
- Далее, использовать припой.
Припаивание медных заготовок – труб, разнообразных деталей, является сложным процессом, который под силу знающим и способным мастерам.
o-trubah.com
Пайка мягкими и твердыми припоями
Полуавтоматы для дуговой сварки и их основные узлы
Пайкой называется технологический процесс получения неразъемных соединений, выполняемый с применением припоя — проволоки из сплава, имеющего температуру плавления более низкую, чем температура плавления основного металла. В результате взаимодействия расплавленного при определенной температуре припоя с кромками основного металла и последующего остывания образуется спай. Кромки основного металла соединяются (спаиваются) вследствие эффекта смачивания их поверхностей, взаимного растворения и диффузии (проникновения) припоя и основного металла в зоне шва (спая). В связи с развитием современных ресурсосберегающих технологий процесс пайки находит широкое применение при изготовлении продукции машиностроения, приборостроения,
электротехнической и электронной промышленности. По сравнению с другими методами получения неразъемных соединений (в том числе и по сравнению со сваркой) пайка имеет ряд преимуществ: простота
выполнения операции, сохранение размеров и формы соединяемых деталей, сохранение неизменного химического состава и физикомеханических свойств паяемых материалов. Кроме того, при пайке отпадает необходимость в последующей механической и термической
обработке, легче получаются соединения в труднодоступных местах и есть возможности для механизации и автоматизации процесса пайки. Процесс получения паяного соединения газопламенной горелкой состоит из нескольких стадий. Подготовка деталей перед пайкой аналогична подготовке под сварку. Перед предварительным нагревом для защиты металла от окисления на детали наносят флюс. При пайке применяют горелку, как правило, малой мощности. Состав пламени, присадочную проволоку и флюсы подбирают в зависимости от паяемого металла. Восстановительным пламенем производят пайку меди, бронз, латуни и различных сталей. Нейтральным пламенем паяют, как правило, сплавы цветных металлов специального назначения. Пламенем горелки осуществляют общий или местный нагрев до температуры пайки. Обычно температура пайки превышает температуру плавления припоя на 30—50 °С. Затем расплавляют припой, который смачивает соединяемые поверхности и заполняет зазор соединения. Исходя из условий образования соединения, припои должны удовлетворять следующим основным требованиям: иметь температуру плавления ниже температуры плавления паяемых материалов; хорошо смачивать поверхность соединяемых материалов, хорошо растекаться по ним и заполнять капиллярные зазоры; не вызывать в последующем химическую эрозию, не подвергаться старению; не изменять свои физико-механические свойства в процессе эксплуатации изделия. Припои классифицируют по следующим основным признакам: температуре плавления —
особолегкоплавкие до 145 °С, легкоплавкие до 450 °С, среднеплавкие до 1100 °С, высокоплавкие до 1850 °С, тугоплавкие свыше 1850 °С; способу образования — готовые, образующиеся в процессе пайки; химическому составу (основному компоненту) — оловянные, медные, никелевые, марганцевые, железные, титановые, серебряные, золотые и т. д.; способности к флюсованию — флюсуемые и самофлюсующиеся; виду полуфабриката — листовые, ленточные, проволочные, порошковые и др. Выбор марки припоя и метода нанесения определяется конструкцией и требованиями, предъявляемыми к соединению. В настоящее время разработано большое количество всевозможных припоев и флюсов. Различают два основных вида пайки: мягкими и твердыми припоями. Мягкие припои имеют невысокую механическую прочность и их плавление осуществляется при температуре до 400 °С. Прочность твердых припоев значительно выше, а температура плавления — свыше 550 °С. Пайку мягкими припоями применяют главным образом для получения плотного соединения деталей, не подверженных значительным нагрузкам. Широко известны припои оловянно-свинцовые (ПОС). Химический состав, температура плавления и примерное назначение некоторых мягких припоев приведены в табл. 82.
Таблица 82
Химический состав, температура плавления и примерное назначение некоторых мягких припоев
Марка | Химический ссстаз. %. псмассе | Темпера тура гиаз- ления. ;С | Примерное назначение | ||||
Sii | Sb | РЪ | Bi | Cd | |||
ПОС90 | S9-90 | Не более 0.15 | Осталь ное | Не более 0.1 | — | 222 | Для пищевой промышленности и внутренних швов хозяйственной посулы |
ПОС40 | 39-40 | 1,5-2;0 | Осталь ное | Не более 0.1 | — | 235 | Для радиаторов, элек — тро — н радиоаппаратуры. физико-технических приборов |
nocis | 17—IS | 2.0-75 | Осталь ное | Не более 0.1 | — | 277 | Для изделий из цинка. оцинкованного железа. меди и ее сплавов, луження подтип Н ИЪ-ОБ |
Легко плав кий став | 13 | — | 27 | 50 | 10 | 70 | Для пайки изделий нз легкоплавких металлов сплавов |
При пайке железа мягким припоем применяют в качестве флюсов хлористый цинк ZnCI3 или хлористый аммоний Nh5C1 (нашатырь). Эти флюсы, как все хлориды, ускоряют последующее ржавление и поэтому после пайки поверхность необходимо тщательно промыть. Для пайки меди и латуни часто применяют канифоль, а для пайки легкоплавких сплавов и металлов — стеарин; они хорошо растворяют оксидные пленки. Пайка твердыми припоями дает возможность получить соединение, приближающееся по прочности к сварным, и поэтому широко применяется в производстве. Соединения могут быть внахлестку, встык или в «ус». Наиболее прочное соединение получается при пайке внахлестку. Подготовка кромок состоит в их точной подгонке, в обезжиривании горячей щелочью и в фиксации деталей, чтобы обеспечить заданный зазор. Чем меньше зазор, тем прочнее спай. Наиболее приемлемый и широко применяемый на практике зазор составляет 0,01—0,02 мм. Стальные детали обычно паяют электролитической медью. Кроме меди для пайки различных сталей и особенно сплавов цветных металлов применяют различные припои: медно-цинковые, медно-никелевые, серебряные, палладиевые, марганцевые, марганцово-никелевые, никелевые, германиевые, титановые, алюминиевые. Наиболее широко применяемые припои стандартизованы. Можно применять в качестве припоев латунь Л62 иЛ68, силумины и др. Наиболее известные в практике припои приведены в табл. 83.
Таблица 83
Химический состав, температура плавления и назначение некоторых твердых припоев
Маржа | Химический состав. иг массе | Температура плавления. :С | Примерное назначение | ||||
Си | Zu | As | Si | AI | |||
ПМЦЗб[11] | 34—3S | Опаль ное | — | — | — | S25 | Для панки изделий из латуни с содержанием ыедн не более 63% |
ПМЦ48 | 46-50 | Опаль ное | — | — | — | S65 | Дія панки медных сплавов, содержащих более 6S % мели |
ПСр45** | 30(0.5) | Опаль ное | 45(0.5) | — | — | 720 | То же. нто и ПМЦ4В, но прн более тонких работах, когда требуется высокая лнстоіа места спая |
ПСр72 | 23(0.5) | Опаль ное | 72(0.5) | — | — | 7S0 | Для панки проводников. когда место спая не должно резко уменьшать электропроводность |
AJI2 (силу мин) | — | — | — | 10-13 | S0-S7 | 577 | Для панки алюминиевых изделий |
В качестве флюса при пайке твердыми припоями используют традиционную обезвоженную буру (Na2B207). Широко известны флюсы ПВ200, ПВ201, ПВ209, ПВ284; для пайки алюминия применяется флюс типа 34А на основе щелочных и щелочноземельных металлов.
Методы контроля качества сварных соединений могут быть разделены на две основные группы: методы контроля без разрушения образцов или изделий — неразрушающий контроль; методы контроля с разрушением образцов или производственных стыков …
Надежность эксплуатации сварных соединений зависит от их соответствия нормативно-технической документации, которая регламентирует конструктивные размеры и форму готовых сварных швов, прочность, пластичность, коррозионную стойкость и свойства сварных соединений. Сварные соединения, выполненные …
Для предупреждения пожаров необходимо соблюдать следующие противопожарные мероприятия. Постоянно следить за наличием и исправным состоянием противопожарных средств (огнетушителей, ящиков с сухим песком, лопат, пожарных рукавов, асбестовых покрывал и т. д.). …
msd.com.ua
Припой и флюс для пайки, назначение, химсостав, приготовление
Для пайки паяльником применяется припой, а чтобы припой хорошо растекался по поверхности соединяемых пайкой деталей, используют вещество, которое называется флюс. В зависимости от металла деталей и их размеров, крепости и герметичности пайки необходимо выбирать определенную марку припоя и флюса. Информация в таблицах поможет Вам подобрать необходимый припой и флюс для пайки.
Марки мягких припоев для пайки паяльником
Основным компонентом при пайке электрическим паяльником является оловянно-свинцовый припой. Он выпускается в виде проволоки или трубки разных диаметров. Трубчатый припой внутри заполняется канифолью. Такой припой очень удобен при работе, так как не требует дополнительного брать на жало паяльника флюс.
Припой представляет собой сплав легкоплавких металлов. Как правило, в состав припоя входит олово. Можно паять и чистым оловом, но оно дорогое и поэтому в олово добавляют дешевый свинец. Олово является экологически чистым металлом и его можно применять в качестве припоя для пайки в чистом виде пищевой посуды и медицинских инструментов. Если согнуть или сжать трубочку из чистого олова, то она хрустит. Чем больше в составе припоя свинца, тем темнее поверхность припоя.
Припои маркируются буквами и цифрами. Например ПОС-61, что обозначает П – припой, О – оловянный, С – свинцовый, 61 – % содержания олова. ПОС-61 является самым распространенным, так как подходит для пайки в большинстве случаев. В народе ПОС-61 часто называют третник , так как в его составе третья часть свинца (Pb).
Припои бывают мягкие и твердые. Температура плавления мягких припоев ниже 450˚С. Твердые припои плавятся при нагреве свыше 450˚С и для пайки электрическим паяльником не используются.
Основные технические характеристики мягких припоев
для пайки электрическим паяльником
Удельное электрическое сопротивление оловянно-свинцового припоя (проводимость) составляет 0,1-0,2 Ом/метр, алюминия 0,0271, а меди 0,0175. Как видите, припой проводит ток в десять раз хуже, чем медь или алюминий.
Наиболее распространенным припоем является ПОС-61, его еще называют третник. Он отлично подходит для пайки и лужения токоведущих частей из меди, латуни и бронзы с герметичным швом и не дорогой. Подходит практически для всех случаев пайки в быту.
Флюс для пайки паяльником
Флюс это вспомогательное вещество, необходимое для освобождения поверхностей спаиваемых деталей от окислов и лучшему растеканию припоя по поверхности металла при пайке. Без применения флюса выполнить паяльником качественную пайку практически не возможно.
При приготовлении наиболее популярных флюсов для пайки электрическим паяльником, применяется канифоль. Ее получают из древесины деревьев хвойных пород, в основном сосны. При температуре около 50°С канифоль размягчается, а при 250°С начинает кипеть.
Канифоль не устойчива к воздействию атмосферной влаги – гидролизуется. Она состоит на 85-90% из абиетиновой кислоты. Если не удалить остатки канифоли после пайки то происходит окисление места пайки. Многие этого не знают и считают, что канифоль для металла безвредна. Кроме того, впитывая воду из атмосферы, канифоль увеличивает свою проводимость и может нарушать работу электронных устройств, особенно высоковольтных их цепей.
Популярные флюсы для пайки электрическим паяльником
Флюс на основе спирта и растворителей требуется хранить в герметичной таре, иначе жидкость быстро испарится. Очень удобна для этих целей бутылочка от маникюрного лака. Всегда и кисточка под рукой, которой удобно наносить флюс на место пайки. Такую бутылочку практически в любом доме можно найти. Еще ее достоинство, кисточка и закрутка не растворяются спиртом и растворителем. Перед наполнением флюсом обязательно нужно тщательно вымыть бутылочку и кисточку от лака. Если лак сильно застыл, то налить ацетона и оставить. Через время лак растворится.
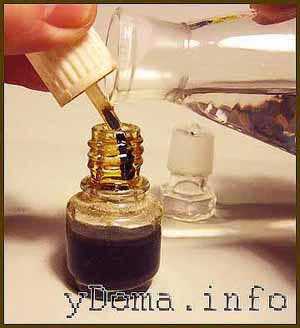
В бутылочке я и приготавливаю спирто-канифольный флюс. Сначала через воронку из бумаги насыпаю порошок канифоли и затем заливаю спиртом. Легко налить спирт в узкое горлышко бутылочки, если прикоснуться горлышком бутылки со спиртом к кисточке, предварительно смоченной в спирте. Лить нужно очень медленно и ни одной капли не прольете. Со временем спирт испаряется и флюс становится густым. Тогда нужно его разбавить спиртом до требуемой консистенции.
В качестве флюса я часто использую не документированный флюс аспирин (ацетил салициловая кислота), который применяют в качестве лекарства. С помощью его, можно без предварительной подготовки, залудить медные и стальные поверхности. На основе аспирина легко готовится и жидкий флюс для пайки паяльником, достаточно таблетку растворить в небольшом количестве спирта, ацетона или воды.
Паяльные пасты (тиноль) для пайки
Паяльная паста (тиноль) представляет собой композицию из припоя и флюса. Паста не заменима при пайке паяльником в труднодоступных местах, и при монтаже бескорпусных радиодеталей. Паста наносится лопаткой в нужном количестве на место пайки и затем прогревается электрическим паяльником. Получается красивая и качественная пайка. Особенно удобно ее применение при отсутствии опыта работы с паяльником.
Пасту можно изготовить самостоятельно. Для этого нужно выбрать марку припоя, подходящего для пайки требуемого металла. Далее напильником с крупной насечкой напилить из прутка опилок. Затем в подобранный из таблицы жидкий флюс для пайки добавлять, перемешивая опилки до получения состава пастообразного состояния. Хранить пасту нужно в герметичной упаковке. Срок хранения пасты не более полгода, так как опилки припоя со временем окисляются.
ydoma.info
Пайка твердыми электродами — Справочник сварщика
Среди методов сварки металлов, существует пайка твердым припоем. Этот вид соединения предполагает, что материалы будут соединяться с помощью присадочного металла, температура расплавления которого намного ниже, чем температура плавления свариваемого материала. Граничной температурой пайки твердым припоем, считается значение в 450°С.
Обратите внимание, что пайка бывает высокотемпературной и низкотемпературной. Что же их отличает между собой? – В первую очередь, это разность прочности спайных соединений, что обусловлено в разности температуры плавления между мягким и твердым припоем.
Также, одним из отличий пайки твердым припоем является термоустойчивость соединения. Так как температура плавления твердого припоя намного выше температуры мягкого припоя, соединение в таком случае способно выдерживать более высокие температуры и механические воздействия, и сохранять свои свойства.
Среди недостатков пайки твердым припоем перед мягкими припоями, следует отметить более высокую рабочую температуру при пайке, что в свою очередь, может вызвать серьезные структурные изменения в металлах. К примеру, такие случаи могут наблюдаться при пайке чугуна. При сильном нагревании возрастает вероятность хрупкости металла в области шва.
Так как для пайки твердым припоем нужна высокая температура, в процессе стоит использовать особые источники нагрева, которые готовы обеспечить расплавление при температуре 1000°С и выше. Поэтому, исключено использование паяльников, с помощью которых производят пайку мягким припоем.
Таким образом, достоинством высокотемпературной пайки является высокая прочность и последующая высокая термоустойчивость соединения. А к недостаткам этого способа является технологичная сложность процесса пайки и доведение металлов до высоких температур.
Где применяется пайка твердым припоем?
Пайка твердыми припоями применяется в «усредненных» случаях между пайкой мягкими припоями и сваркой. То есть, во всех случаях, где низкотемпературной пайки будет недостаточно, а сварка будет нецелесообразной, актуальнее всего использовать именно пайку твердым припоем.
Этот способ соединения применяют при изготовлении металлорежущих инструментов с твердосплавными пластинами. В процессе припаивания этих пластин, высокотемпературная пайка обеспечивает достаточно прочное соединение, не оказывая негативного воздействия на твердость и прочность режущих пластин.
С помощью такой пайки изготавливают изделия из цветных металлов и нержавеющих сталей, выполняют соединение стальных и медных трубопроводов, которые находятся в условиях высокого давления или при высокой температуре, в холодильных системах, теплообменниках и так далее.
Используют высокотемпературную пайку для ремонта автомобилей – пайки радиаторов и трубопроводных систем, для ремонта двигателя, трансмиссии, кузова и других деталей, в тех случаях, где не целесообразна любая другая сварка. Актуально применение пайки твердым припоем в случае тонкостенных деталей, которые выдерживают значительные нагрузки и упругие деформации.
Еще, высокотемпературную пайку применяют для ремонта бытовых изделий из меди и латуни, которые в процессе использования подвергаются высоким температурам.
Чем пользуются для нагрева при пайке твердыми припоями и что используют?
В целом, для пайки твердым припоем подойдет любой источник, который способен разогреть участок до температуры свыше 1000°С. Как правило, такими источниками являются газовые горелки, индукторы и печи, а также нагревание деталей электросопротивлением. В бытовых условиях, наиболее часто используется именно горелки.
В качестве припоев используются:
- медно-цинковые припои;
- медно-фосфорные припои;
- латунь;
- серебряные припои.
В качестве флюсов, как правило, применяют соединения на основе бора, такие как – бура (Na2B4O7), борная кислота (h4BO3) и борный ангидрид (B2O3). Используются и другие флюсы, регламентированные ГОСТ 23178-78, такие как – ПВ200, ПВ201, ПВ209, ПВ209Х, ПВ284Х.
Процесс пайки твердыми припоями
Технология высокотемпературной пайки не отличается сложными нюансами или деталями. Достаточно придерживаться техники безопасности и основных правил, для того чтобы процесс прошел успешно. Рассмотрим весь процесс на примере соединения гаечного ключа.
В таком случае, для нагрева достаточно воспользоваться газовой горелкой. В первую очередь, стоит зачистить стыковые части обеих половинок ключа с целью удаления окисной пленки, которая достаточно часто поражает нержавеющие детали.
Далее, детали зажимаются в тисках или других устройствах, которые будут надежно удерживать детали. Область соединения необходимо промазать флюсом и приступить к нагреву. Пламя на горелке необходимо установить таким, чтобы был легкий недостаток кислорода. В случае если будет кислородное перенасыщение, поверхность детали будет окисляться.
Итак, область паяемой зоны разогревается до необходимого цвета и температуры, после чего осуществляется офлюсование стыка с флюсом. В случае, когда используется неофлюсованный пруток, его необходимо окунать во флюс. Далее, область пайки разогревается до вишневого цвета, после чего расплавляется припой, растекается в зоне соединения и затягивается в стык. Далее остается лишь зачистить стык и процесс соединения деталей твердым припоем можно считать завершенным.
www.vse-o-svarke.org
Твердый припой на железохромовой основе
Изобретение относится к области металлургии, в частности к твердому припою для высокотемпературной пайки нержавеющей стали. Порошок твердого припоя на железохромовой основе для высокотемпературной пайки основного материала из нержавеющей стали содержит, мас. %: от 11 до 35 хрома, до 30 никеля, от 5 до 20 меди, от 2 до 10 кремния, от 4 до 10 фосфора, до 10 марганца, железо — остальное, в количестве по меньшей мере 20. При содержании Si, меньшем или равном 6 мас. %, содержание P составляет более 8 мас. %, а при содержании Р, меньшем или равном 8 мас. %, содержание Si составляет более 6 мас. %. Твердый припой образует паяное соединение с высокой прочностью и хорошей коррозионной стойкостью. 4 н. и 11 з.п. ф-лы, 2 табл., 5 пр.
ОБЛАСТЬ ИЗОБРЕТЕНИЯ
Это изобретение относится к твердому припою на железохромовой основе, подходящему для высокотемпературной пайки нержавеющей стали и других материалов, где требуется коррозионная стойкость и высокая прочность. Типичные примеры применений представляют собой теплообменники и каталитические конвертеры.
ПРЕДПОСЫЛКИ ИЗОБРЕТЕНИЯ
Высокотемпературная пайка представляет собой способ соединения металлических деталей с помощью твердого припоя и нагревания. Температура плавления твердого припоя должна быть ниже температуры плавления основного материала, но выше 450°C. Если твердый припой имеет температуру плавления ниже 450°C, то способ соединения называется термином «низкотемпературная пайка». Наиболее часто используемые твердые припои для высокотемпературной пайки нержавеющих сталей имеют медную или никелевую основу. Твердые припои на медной основе являются предпочтительными с точки зрения сокращения расходов, в то время как твердые припои на никелевой основе используют при необходимости высокой коррозионной стойкости и высокой прочности. Твердые припои на медной основе, например, часто используют при высокотемпературной пайке теплообменников для установок централизованного отопления и водоснабжения.
Твердые припои на никелевой основе с высоким содержанием хрома используют вследствие их высокой коррозионной стойкости в тех устройствах, на которые воздействуют коррозионные среды. Твердые припои на никелевой основе можно также использовать в устройствах, работающих при высокой температуре, и/или в устройствах, для которых необходима высокая прочность. Типичное устройство, на которое одновременно действует коррозионная среда и высокая рабочая температура, представляет собой радиатор рециркуляции отработавших газов (РОГ) в автомобильных дизельных двигателях. Твердые припои для данных устройств должны обладать определенными свойствами, чтобы быть подходящими для использования, такими как коррозионная стойкость, стойкость к окислению при высокой температуре, хорошее смачивание основного материала, не вызывающее охрупчивания основного материала во время высокотемпературной пайки (далее для краткости — просто пайка).
ОПИСАНИЕ УРОВНЯ ТЕХНИКИ
Стандарт ANSI/AWS 5.8 Американского национального института стандартов/Американского общества специалистов по сварке описывает несколько типов твердых припоев на никелевой основе. Многие из этих твердых припоев на никелевой основе используют для пайки теплообменников. Припой BNi-2 состава Ni-7Cr-3B-4,5Si-3Fe используют для получения высокопрочных соединений для применения при высокой температуре. Присутствие бора, однако, является недостатком, потому что он может вызывать охрупчивание основного материала при диффузии бора в основной материал. Другой твердый припой на никелевой основе, содержащий бор, имеет такой же недостаток. Чтобы преодолеть связанный с бором недостаток, были разработаны другие твердые припои на никелевой основе. Припой BNi-5 (Ni-19Cr-10Si) имеет высокую коррозионную стойкость вследствие высокого содержание хрома. Температура пайки для этого сплава является достаточно высокой (1150-1200°C). Другие, не содержащие бора твердые припои на никелевой основе представляют собой BNi-6 (Ni-10P) и BNi7 (Ni-14Cr-10P). Температура пайки для этих твердых припоев ниже вследствие высокого содержания фосфора (10 масс.%). При высоком содержании фосфора (10 масс.%) может получиться паяное соединение без требуемой прочности вследствие риска образования содержащих фосфор хрупких фаз.
Другой твердый припой на никелевой основе описан в патентах US6696017 и US6203754. Этот твердый припой имеет состав Ni-29Cr-6P-4Si и сочетает высокую прочность и высокую коррозионную стойкость с достаточно низкой температурой пайки (1050-1100°C). Этот твердый припой был специально разработан для нового поколения радиаторов РОГ, используемых в сильно коррозионной среде.
Недостаток всех твердых припоев на никелевой основе заключается в высоком содержании дорогостоящего никеля. Содержание никеля составляет по меньшей мере 60%, но обычно выше. Высокое содержание никеля в данных твердых припоях делает дорогостоящими сами твердые припои и производство теплообменников и каталитических конвертеров.
Чтобы преодолеть недостаток высокой стоимости твердых припоев на никелевой основе, была исследована возможность использования твердых припоев на основе железа. На рынке существуют два твердых припоя на основе железа. Припой AlfaNova, описанный в PCT-заявке WO02098600, имеет состав, близкий к нержавеющей стали, с добавками кремния, фосфора и бора для уменьшения температуры плавления твердого припоя. Температура пайки данного сплава составляет 1190°C.
Другой твердый припой на основе железа, AMDRY805, описанный в US20080006676 A1, имеет состав Fe-29Cr-18Ni-7Si-6P. Этот сплав не содержит бора, чтобы преодолеть связанный с бором недостаток. Температура пайки для данного сплава составляет 1176°C.
Третий твердый припой на основе железа, Fe24Cr20Ni10Cu7P5Si5Mn, поставляется на продажу под наименованием BrazeLet™ F300 фирмой Höganäs AB (Швеция). Этот сплав содержит медь, чтобы предотвратить выделение фосфора и повысить коррозионную стойкость. Температура пайки для данного сплава составляет 1100°C.
Максимально высокая используемая на практике температура, соответствующая ограниченной скорости роста, составляет 1095°C, согласно профессиональному справочнику Американского общества металлургов (ASM) «Нержавеющая сталь», 1994 г., страница 291. Таким образом, низкая температура пайки является предпочтительной для исключения связанных с ростом зерен проблем, таких как меньшая пластичность и повышенная твердость в основном материале.
СУЩНОСТЬ ИЗОБРЕТЕНИЯ
Это изобретение относится к железному твердому припою, который дает паяное соединение с высокой прочностью и хорошей коррозионной стойкостью.
Твердый припой может быть предусмотрен в виде порошка, и преобразование в порошок твердого припоя можно осуществлять, используя известные в технике способы. Например, порошки, имеющие состав, определенный в формуле изобретения, можно изготавливать, выплавляя гомогенный сплав и превращая его порошок в процессе распыления. Средний размер частиц порошка может составлять от 10 до 150 мкм, обычно от 10 до 100 мкм.
Порошок твердого припоя согласно изобретению представляет собой сплав, содержащий от 11 масс.% до 35 масс.% хрома, от 2 масс.% до 20 масс.% меди, от 0 масс.% до 30 масс.% никеля, от 2 масс.% до 10 масс.% кремния, от 4 масс.% до 10 масс.% фосфора и по меньшей мере 20 масс.% железа. Если содержание Si равно или меньше 6 масс.%, то содержание P должно быть выше 8 масс.%. Если содержание P меньше или равно 8 масс.%, то содержание Si должно быть выше 6 масс.%.
Согласно одному варианту осуществления содержание Si должно быть выше 6 масс.% и до 10 масс.%, а содержание P должно составлять от 6 масс.% до 10 масс.%. Согласно другому варианту осуществления содержание Si должно быть выше 6 и до 10 масс.%, а содержание P должно составлять от 8 масс.% до 10 масс.%. Твердый припой может также содержать вплоть до 10 масс.% марганца. Твердый припой является подходящим для изготовления каталитических конвертеров и теплообменников.
ПОДРОБНОЕ ОПИСАНИЕ ИЗОБРЕТЕНИЯ
Настоящее изобретение относится к твердому припою на железохромовой основе с превосходной смачиваемостью на нержавеющей стали. Данный твердый припой дает высокопрочные паяные соединения с хорошей коррозионной стойкостью и имеет значительно меньшую стоимость по сравнению с твердыми припоями на никелевой основе. Данный твердый припой является подходящим для пайки различных типов теплообменников и каталитических конвертеров при значительно меньшей стоимости, чем традиционные твердые припои на никелевой основе.
Типичным применением данного твердого припоя являются устройства, работающие при высокой температуре в коррозионных средах. Эти устройства могут представлять собой различные типы теплообменников (пластинчатые или трубчатые), которые используются в автомобильных системах, например, рециркуляции отработавших газов. Другие примеры представляют собой каталитические конвертеры (каталитические дожигатели отработавших газов) различных типов.
Состав твердого припоя согласно изобретению является следующим:
железо с содержанием по меньшей мере 20 масс.%;
медь примерно 2-20 масс.%, предпочтительно 5-15 масс.%;
хром примерно 11-35 масс.%, предпочтительно 20-30 масс.%;
никель примерно 0-30 масс.%, предпочтительно 10-20 масс.%;
кремний примерно 2-10 масс.%;
фосфор примерно 4-10 масс.%;
и если содержание Si равно или меньше 6 масс.%, то содержание P должно быть выше 8 масс.%;
и если содержание P меньше или равно 8 масс.%, то содержание Si должно быть выше 6 масс.%.
Это означает, что либо содержание Si выше 6 масс.%, либо содержание P выше 8 масс.%, или выполняются оба условия, т. е. и содержание Si выше 6 масс.%, и содержание P выше 8 масс.%.
Согласно одному варианту осуществления содержание Si должно быть выше 6 масс.% и до 10 масс.%, а содержание P должно составлять от 6 масс.% до 10 масс.%. Согласно второму варианту осуществления содержание Si должно быть выше 6 масс.% и до 10 масс.%, а содержание P должно составлять от 8 масс.% до 10 масс.%.
Могут присутствовать и другие компоненты, которые не перечислены выше.
Твердый припой может необязательно содержать марганец вплоть до 10 масс.%, обычно менее чем 7 масс.%.
Признано, что для состава по основным компонентам твердого припоя может быть выгодной схожесть с составом основного материала из нержавеющей стали. Примерами сортов нержавеющей стали являются сталь 316L, имеющая типичный состав Fe-17Cr-13,5Ni-2,2Mo, и сталь 304L, имеющая типичный состав Fe-18,8Cr-11,2Ni. Все сорта нержавеющей стали по определению содержат минимум 11% хрома, и немногие сорта нержавеющей стали содержат более чем 30% хрома. Содержание хрома выше 11% требуется для образования защитного слоя оксида хрома, который придает стали ее характеристики коррозионной стойкости. Чем выше содержание хрома, тем выше коррозионная стойкость, но его содержание выше 35% может вызывать уменьшение прочности соединения. Таким образом, содержание хрома должно составлять от 11 до 35 масс.%, предпочтительно 20-30 масс.%.
Чтобы снизить температуру плавления сплава, добавляют снижающие температуру плавления вещества. Хорошо известно, что кремний, бор и фосфор каждый являются эффективно снижающими температуру плавления веществами. При исследовании фазовой диаграммы системы Fe-P обнаружено, что данная система обладает минимальной температурой плавления 1100°C при приблизительно 10 масс.% фосфора. Система Fe-Si имеет температуру плавления 1380°C при 10 масс.% Si и минимальную температуру плавления в приблизительно 1210°C при приблизительно 19 масс.% Si. Содержание каждого элемента из фосфора и кремния выше 10 масс.% является нежелательным, поскольку чрезмерно повышается риск образования хрупких фаз. В патентах US6696017 и US6203754 отмечено, что содержание Si+P необходимо поддерживать в интервале от 9 до 11,5 масс.%. В случае сплава, в котором суммарное содержание Si и P составляет более чем 11,5 масс.%, сплав становится хрупким, и его прочность уменьшается.
Неожиданно было обнаружено, что медь уменьшает диффузию кремния и фосфора в основной материал при операции пайки. Кроме того, предотвращается выделение фосфора на межзеренных границах в основном материале, и это означает, что также предотвращается охрупчивание основного материала. Далее, это означает, что можно использовать повышенное суммарное содержание Si и P в сочетании с Cu для того, чтобы увеличить прочность паяного соединения. Таким образом, если требуется высокая прочность, предпочтительно поддерживать высоким содержание фосфора и кремния. Следовательно, суммарное содержание Si и P в содержащем Cu твердом припое может составлять вплоть до 20 масс.%.
Таким образом, когда содержание Si равно или меньше 6 масс.%, содержание P должно быть выше 8 масс.%, а если содержание P меньше или равно 8 масс.%, содержание Si должно быть выше 6 масс.%. Кроме того, содержание Si+P должно быть выше 10 масс.%, а обычно содержание Si+P будет выше 14 масс.%.
Неожиданно было обнаружено также, что присутствие меди оказывает положительное влияние на коррозионную стойкость паяных соединений в 10% H2SO4. Считается, что требуется 2 масс.% меди, чтобы создать положительное влияние меди. Содержание меди в предложенном изобретением твердом припое следует поддерживать ниже 20 масс.% для того, чтобы он не сильно отличался по химическому составу от подлежащего пайке основного материала. Таким образом, содержание меди должно составлять от 2 до 20 масс.%, предпочтительно 5-15 масс.%.
Система Fe-B имеет минимальную температуру плавления 1174°C при приблизительно 4 масс.% бора. Однако недостаток бора заключается в том, что он вызывает охрупчивание паяной детали. Бор представляет собой междоузельный атом, и, вследствие своего малого диаметра, он может быстро диффундировать в решетку основного материала и образовывать хрупкую фазу CrB. Вследствие диффузии бора увеличивается температура переплавки сплава, что в некоторых случаях представляет собой желательный эффект.
US4444587 описывает, как марганец может служить хорошим заместителем бора, поскольку марганец также снижает температуру плавления. Содержание 10-30 масс.% марганца наряду с кремнием и углеродом будет в системе на основе железа снижать температуру плавления более чем на 200°C. С другой стороны, марганец будет почти полностью испаряться во время цикла пайки, что позволит повышать температуру переплавки, но без риска образования каких-либо хрупких фаз типа CrB.
Никель стабилизирует аустенит, который повышает стойкость сплава к окислению. Никель также повышает ударную вязкость паяного соединения. При рассмотрении фазовой диаграммы тройной системы Cr-Fe-Ni можно видеть, что никель также обладает эффектом снижения температуры плавления. При 30 масс.% Cr и 20 масс.% Ni температура плавления в системе Cr-Fe-Ni составляет приблизительно 1470°C согласно профессиональному справочнику ASM «Нержавеющая сталь». Содержание никеля в относящемся к изобретению твердом припое должно поддерживаться ниже 30 масс.%, чтобы свести до минимума стоимость твердого припоя.
Твердый припой согласно изобретению находится в виде порошка и может быть получен распылением либо газом, либо водой. Твердый припой может быть использован в виде порошка или превращен в пасту, ленту, фольгу или другие формы традиционными способами. В зависимости от способа применения требуется различное распределение частиц по размерам, но средний размер частиц порошка твердого припоя составляет 10-100 мкм.
Твердый припой является подходящим для пайки в вакуумных печах при разрежении (<10-3 Торр). Твердый припой имеет температуру плавления ниже 1100°C и при температуре пайки 1120°C дает соединения, имеющие высокую прочность и хорошую коррозионную стойкость без какого-либо наблюдаемого роста зерен.
Твердый припой в виде пасты, ленты, фольги или в других формах помещают на зазор или в зазор между поверхностями основного материала, которые должны быть соединены. Во время нагревания твердый припой плавится, и под действием капиллярных сил расплавленный твердый припой смачивает поверхность основного материала и затекает в зазор. Во время охлаждения он образует твердое паяное соединение. Поскольку действие твердого припоя обусловлено капиллярными силами, смачивание твердым припоем подлежащего пайке основного материала является критически важным. Предложенный изобретением твердый припой обладает превосходным смачиванием на основном материале из нержавеющей стали. Твердый припой также обладает хорошим допуском на ширину зазора и способен запаивать зазоры свыше 500 мкм.
Соединения, паянные твердым припоем согласно изобретению, имеют микроструктуру, состоящую из гомогенной смеси богатых Cr-P фаз и богатых Ni-Fe-Si-Cu фаз. Неожиданно было обнаружено, что диффузия кремния и фосфора ограничена за счет присутствия меди в твердом припое. Присутствие Cu также препятствовало выделению фосфора на межзеренных границах в основном материале. Твердые припои без меди имели более широкую зону диффузии в основной материал, а также имело место выделение фосфора на межзеренных границах, что может вызывать охрупчивание основного материала.
ПРИМЕРЫ
В качестве материалов сравнения использовали два железных твердых припоя: Fe24Cr20Ni10Cu7P5Si5Mn (называется «сравнительный сплав 1») и Fe29Cr18Ni7Si6P (называется «сравнительный сплав 2»).
Сравнительный сплав 1 представляет собой твердый припой на основе железа BrazeLet™ F300, производимый фирмой Höganäs AB.
Сравнительный сплав 2 представляет собой твердый припой на основе железа, описанный в патентной заявке US2008006676.
Кроме того, приготовили три различных твердых припоя согласно изобретению путем распыления водой.
Таблица 1 показывает фактический состав полученных твердых припоев. Содержание каждого компонента приведено в массовых процентах. Выражение «Ост.» (остальное) означает, что остальной материал в расплаве состоит из Fe. Согласно изобретению порошок твердого припоя содержит по меньшей мере 20 масс.% Fe, а остальные компоненты регулируют в указанных пределах так, чтобы в сумме составлять 100 масс.%. Следовые элементы присутствуют в качестве неизбежных примесей, обусловленных способом изготовления, и следовые элементы присутствуют в настолько малом количестве, что они не влияют на свойства твердого припоя. Следовые элементы обычно присутствуют в суммарном количестве менее чем 1 масс.%.
Первый критерий, которому должен соответствовать твердый припой, заключается в том, что температура пайки должна предпочтительно составлять 1100°C или менее. В таблице 1 можно видеть, что медь влияет на ту температуру, при которой плавится и осуществляет пайку твердый припой. Сравнительный сплав 2 не плавится при 1100°C.
Для испытания свойств использовали следующие способы:
1) Испытание на смачиваемость
Твердый припой (0,2 грамма) помещали в форме круга с диаметром 9 мм на середину подложки из нержавеющей стали. Покрытая порошком площадь, т.е. исходная площадь порошка (Ai), составляла 63,6 мм2. Затем подложки с твердым припоем нагревали при 1100°C в течение 30 мин в вакууме 10-4 Торр. Смачиваемость определяли как коэффициент растекания, определяемый так: S=Am/Ai, где Am представляет собой площадь расплавленного припоя, и Ai представляет собой исходную площадь порошка.
Из таблицы 2 можно видеть, что твердые припои с высоким содержанием меди (сравнительный сплав 1) обладают очень хорошей смачиваемостью. Предложенные изобретением твердые припои (сплавы 1, 2 и 3) имеют умеренную смачиваемость.
2) Металлографическое исследование
Твердый припой превращали в пасту смешиванием металлического порошка со связующим. В качестве основного материала использовали нержавеющую сталь 304. Тавровые образцы, представленные на фиг. 1, паяли при 1100°C в течение 30 мин в вакууме 10-4 Торр. После пайки тавровые образцы разрезали поперек. Поверхность поперечного разреза исследовали в световом оптическом микроскопе. Хорошее паяное соединение определяли как не содержащее пор и трещин соединение с однородной микроструктурой.
Как видно в таблице 2, сплав твердого припоя согласно изобретению (сплавы 1, 2 и 3) образует однородную микроструктуру с ограниченной диффузией элементов в основной материал и без выделения фосфора на межзеренных границах. Более значительная диффузия в основной материал была обнаружена при использовании твердого припоя на основе железа без меди (сравнительный сплав 2).
3) Прочность соединения
Прочность соединения испытывали, используя процедуры, аналогичные тем, которые рекомендованы в стандарте ANSI/AWS C3.2M/C3.2.2001, для конфигурации соединения внахлестку с параллельным зазором 100 мкм (см. фиг. 2). Перед пайкой твердый припой превращали в пасту, смешивая твердый припой со связующим. Затем испытываемые на прочность соединения образцы с нанесенной пастой нагревали до 1100°C в течение 30 мин в вакууме 10-4 Торр.
Из таблицы 2 можно видеть, что наиболее высокая прочность получена для сплавов с самым высоким содержанием Si+P (сплавы 1, 3). Даже сплав 2 также имеет значительно более высокую прочность, чем сравнительный сплав 1 с меньшим содержанием Si+P. В полном противоречии с установившимся мнением, это доказывает, что высокие содержания кремния и фосфора в сочетании с Cu приводят к высокой прочности.
4) Испытания на коррозию
Коррозионную стойкость исследовали, выдерживая паяные тавровые образцы в лабораторных стаканах, содержащих коррозионные среды, в течение одной недели. После этого образцы проверяли на наличие признаков коррозии. Всего приготовили 5 паяных образцов, по одному из каждого сплава. В качестве коррозионных сред использовали водные растворы с 10% по массе H2SO4.
Результаты представлены в таблице 2. Сплавы 1-3 и сравнительный сплав 2 имели признаки коррозионного воздействия, но наиболее пострадавшим был сравнительный сплав 2. Сопоставление сравнительного сплава 2 с другими сплавами на железной основе доказывает положительное влияние Cu на коррозионную стойкость твердых припоев на железохромовой основе. Сопоставление предложенных изобретением сплавов (сплавы 1, 2 и 3) и сравнительного сплава 1 показывает преимущества более высокого содержания хрома в отношении коррозионной стойкости.
Таблица 1 Химический состав и температура плавления исследованных твердых припоев | ||||||||||
Сплав | Fe | Cu | Cr | P | Si | Ni | Mn | Si+P | Плавление при 1100°C | |
1 | Изобр. | Ост. | 5,3 | 15,3 | 7,4 | 9,4 | 11 | 0 | 16,8 | Да |
2 | Изобр. | Ост. | 5,1 | 15,2 | 9,2 | 4,9 | 10,1 | 0 | 14,1 | Да |
3 | Изобр. | Ост. | 5,1 | 15,1 | 8,5 | 7,1 | 9,9 | 0 | 15,6 | Да |
Сравн. 1 | Сравн. | Ост. | 10 | 24 | 7 | 5 | 10 | 5 | 12 | Да |
Сравн. 2 | Сравн. | Ост. | 0 | 28 | 7 | 6 | 18 | 0 | 13 | Нет |
Таблица 2 Результаты испытания на смачиваемость, металлографического исследования, испытания на прочность соединения и испытаний на коррозию | |||||
Сплав | Коэффициент растекания | Прочность соединения (Н/мм2) | Коррозия на паяных соединениях | Диффузия элементов и выделение P | |
1 | Изобр. | 15 | 105 | Некоторая | Ограниченная дифф., нет выдел. |
2 | Изобр. | 20 | 88 | Некоторая | Ограниченная дифф., некоторое выдел. |
3 | Изобр. | 23 | 110 | Некоторая | Ограниченная дифф., нет выдел. |
Сравн. 1 | Сравн. | 40 | 77 | Отсутствует | Нет дифф., нет выдел. |
Сравн. 2 | Сравн. | 15 | 93 | Сильная | Диффузия, нет выдел. |
1. Порошок твердого припоя на железохромовой основе для высокотемпературной пайки основного материала из нержавеющей стали, отличающийся тем, что он содержит, мас. %:
от 11 до 35 хрома,
до 30 никеля,
от 5 до 20 меди,
от 2 до 10 кремния,
от 4 до 10 фосфора,
до 10 марганца,
железо — остальное, в количестве по меньшей мере 20,
причем при содержании Si, меньшем или равном 6 мас. %, содержание P составляет более 8 мас. %,
а при содержании Р, меньшем или равном 8 мас. %, содержание Si составляет более 6 мас. %.
2. Порошок твердого припоя по п. 1, отличающийся тем, что он дополнительно содержит примесные элементы в количествах менее чем 1 мас. %.
3. Порошок твердого припоя по п. 1 или 2, отличающийся тем, что содержание Si составляет более 6 мас. % и меньше или равно 10 мас. %.
4. Порошок твердого припоя по п. 1 или 2, отличающийся тем, что содержание P составляет более 6 мас. % и меньше или равно 10 мас. %, предпочтительно содержание P составляет более 8 мас. % и меньше или равно 10 мас. %.
5. Порошок твердого припоя по п. 1 или 2, отличающийся тем, что суммарное содержание Si и P меньше или равно 20 мас. %.
6. Порошок твердого припоя по п. 1 или 2, отличающийся тем, что содержание никеля составляет от 10 до 20 мас. %.
7. Порошок твердого припоя по п. 1 или 2, отличающийся тем, что содержание меди составляет от 5 до 15 мас. %.
8. Порошок твердого припоя по п. 1 или 2, отличающийся тем, что содержание марганца составляет менее 7 мас. %.
9. Порошок твердого припоя по п. 1 или 2, отличающийся тем, что содержание хрома составляет от 20 до 30 мас. %.
10. Порошок твердого припоя по п. 1 или 2, отличающийся тем, что содержание хрома составляет от 11 до 20 мас. %.
11. Порошок твердого припоя по п. 1 или 2, отличающийся тем, что он имеет средний размер частиц 10-100 мкм.
12. Порошок твердого припоя по п. 1 или 2, отличающийся тем, что он предназначен для изготовления твердого припоя в виде пасты, ленты или фольги.
13. Применение порошка твердого припоя по любому из пп. 1-12 в качестве порошка для высокотемпературной пайки в печах.
14. Применение порошка твердого припоя по любому из пп. 1-12 в качестве порошка для высокотемпературной пайки теплообменников и каталитических конвертеров.
15. Паяное изделие, изготовленное высокотемпературной пайкой основных материалов из нержавеющей стали с использованием порошка твердого припоя на железохромовой основе, отличающееся тем, что использован порошок по любому из пп. 1-12.
findpatent.ru