Алюминотермитная сварка рельсов
На протяжении всего периода существования железных дорог велись поиски конструкций рельсовых стыков, которые обеспечили бы такую же надежность пути в местах соединения рельсов, как и вне стыков. Стыки остаются основными возбудителями динамических, а нередко и ударных воздействий подвижного состава на путь. Регулярные динамические нагрузки на рельсовый стык приводят к интенсивному износу как ходовых частей подвижного состава, так и к дефектам рельсов, а в долгосрочном периоде к просадкам в балласте и болезням земляного полотна. Затраты труда на содержание стыков достигают 20 % всех затрат на текущее содержание пути.
Стыковой путь.
Чтобы сократить число рельсовых стыков в пути, десятилетиями стремились увеличить стандартную длину рельсов. Коренное решение проблемы рельсового стыка воплотилось в так называемом бесстыковом пути, благодаря которому число стыков сокращается в десятки, а при сварке рельсов на перегонах, станциях и в пределах стрелочных переводов, в тысячи раз.
Бесстыковой путь.
Бесстыковой путь является наиболее прогрессивным и совершенным типом железнодорожного пути. Он позволяет:- исключаются удары колес о рельсы при перекатывании через зазоры в стыках и, следовательно, значительно снижается износ рельсов и колес;
- экономить металл за счет уменьшения количества стыковых скреплений;
- снизить динамическое воздействие на путь, возникающее в стыках;
- уменьшить износ рельсов и ходовых частей подвижного состава;
- сократить выход из строя рельсов по стыковым дефектам;
- уменьшить сопротивление движению поездов;
- снизить расходы на содержание и ремонт пути и подвижного состава.
С укладкой бесстыкового пути значительно уменьшается количество стыковых соединителей для участков с автоблокировкой и электрической тягой поездов. Отсутствие стыков уменьшает сопротивление движению поездов, что экономит топливо для тепловозов или электрическую энергию для электровозов.
С каждым проходящим по пути колесом подвижного состава усиливается как процесс старения пути и изменения положения рельсовых нитей, так и интенсивность этого процесса. Например, смятие концов рельсов не исчезает, а наоборот, постепенно накапливается. Увеличивается также износ и по длине рельсов. Таким образом, остаточные деформации элементов верхнего строения пути постепенно накапливаются под воздействием движущихся колес. Интенсивность нарастания остаточных деформаций определяется грузонапряженностью линии и скоростями движения поездов.
Все эти остаточные деформации рано или поздно приводят к выходу из строя части рельсовой нити, которая выявляется передвижными средствами дефектоскопирования.
В результате нить протяженностью более 600 метров приходит в негодность. Сменить целую плеть имея дефект на протяжении 0,5 м было бы бессмысленным, поэтому дефектный участок пути вырезается и на его место ставиться «рубок» рельса который образует в некогда целом рельсе 2 стыка.
Возникает вопрос: как в минимально короткие сроки и с минимальными затратами восстановить целостность рельсовой нити, и вот тут на помощь приходит алюминотермитная сварка рельсов в полевых условиях.
Сама мысль о алюминотермитной реакции происходит из второй половины ХVIII века. Французский ученый Антуан Лоран Лавуазье описал принцип экзотермической реакции, практическое внедрение которой в своей эпохе он не мог предполагать.
История термитной сварки насчитывает уже около ста сорока лет. Начало этому процессу было положено еще в 1859 году Русским ученым Н.Н. Бекетовым, который впервые открыл алюминотермию и дал описание алюминотермитной реакции. Ее сущность – получение металлов и сплавов восстановлением их окислов алюминием. Поскольку реакция проходит с выделением большого количества тепла, ее и назвали термитной (от греческого слова therme — теплота).
Алюминотермитная сварка рельсов (полное название: Сварка рельсов алюминотермитная методом промежуточного литья) — процесс, основанный на алюминотермии, при котором используются химические реакции восстановления железа из оксидов, эти реакции сопровождаются выделением тепла и получением расплавленного металла требуемого химического состава.
Алюминотермическая реакция:
2Al + Cr2О3 = Al2О3 + 2Cr
Fe2O3 + 2Al = 2Fe + Al2O3
Эти реакции сопровождаются выделением тепла и получением расплавленного металла требуемого химического состава. Для сварки применяется термит, расфасованный определенными порциями. Работу выполняет бригада из двух-трех человек. Общий вес используемого оборудования не превышает 350—400 кг.
При выполнении сварки и сопутствующих технологических операций используются автономные источники энергии.
Преимущества:
Свое развитие термитная сварка получила благодаря следующим позитивным факторам:
- Полная независимость от электроэнергии и газа;
- Простота и доступность технологии;
- Отсутствие сложного технологического оборудования;
- Возможность выполнения работ в линейных или полевых условиях монтажным персоналом, работниками ремонтных и эксплуатационных служб.
Принципы работы:
Термитной сваркой называют способ сварки, использующий тепло сжигаемой специальной смеси. Смесь порошкообразная, в ее состав входят:
- Оксиды железа в виде железной окалины;
- Порошкообразный алюминий.
Термит на основе алюминия используется для соединения стальных и чугунных изделий.
Термит с использованием оксида железа называется железоалюминиевый. Горение его протекает при температуре в пределах 2700 градусов Ц, что вполне достаточно для плавления железосодержащих сплавов.
Термитная сварка рельсов
Сущность этого технологического процесса практически не меняется уже свыше сотни лет:
Тигель перед началом сварки дополнительно просушивают кислород — пропановым пламенем с избытком кислорода кольцевыми движениями по спирали до верхних краев тигля в течение 55 — 60 с.
Затем на рельсы устанавливают и закрепляют комбинированную стойку, с помощью которой позиционируют горелку и тигель. Полуформы фиксируют относительно стыкового зазора так, чтобы его центр совпал с вертикальной осью литейной формы, а сами полуформы прилегали друг к другу без ступенек по периметру стыковки. Место контакта литейной формы с рельсом уплотняют формовочной смесью.
Перед подогревом проводят регулировку пламени до нормального горения: на газовых редукторах – давление пропана 0,1 МПа и кислорода – 0,50 МПа. После этого газовую горелку устанавливают на комбинированную стойку и начинают подогрев торцов рельсов в стыке.
До заливки формы расплавленным металлом торцы рельсов в стыке предварительно разогревают до температуры 1200–1250°C. Процесс плавления термитной смеси и выпуск расплавленного металла в литейную форму происходят автоматически через 20–28 секунд после начала термитной реакции. К этому моменту подогретые концы рельсов успевают остыть до 850–900 °C.
Жидкий металл является одновременно источником тепла и присадочным материалом, соединяющим концы рельсов 1.
Расплавленный металл поступает из тигля в форму и заполняет оставленный между торцами рельсов зазор. Иногда металл заливают через специальный литник. Постепенно заполняя зазор и свободное пространство между рельсами и стенками формы, металл расплавляет соприкасающиеся с ним стенки рельсов, а застывая, образует с рельсами одно целое — сварное соединение.
После выпуска термитного металла в литейную форму тигель переносят на вспомогательную стойку. Демонтаж комбинированной стойки и литейной формы проводят после кристаллизации металла сварного шва, которая в зависимости от массы порции термитной смеси, длится 3,0–3,5 мин. Затем головку рельса очищают от песка металлической щеткой и с помощью гидравлического обрезного станка в горячем пластическом состоянии удаляют прибыльную часть сварного шва на головке рельса, после чего рабочую часть головки подвергают шлифованию.
Ориентировочное время остывания составляет 90 — 20 мин в зависимости от температуры окружающего воздуха.
Термитная сварка рельсов трамвайного пути методом промежуточного литья
Основные методы сварки рельс
Прежде чем приступить к подробному описанию технологического процесса термитной сварки рельсов трамвайного пути, целесообразно рассмотреть специфику данного вида работ и применяемых для его выполнения способов.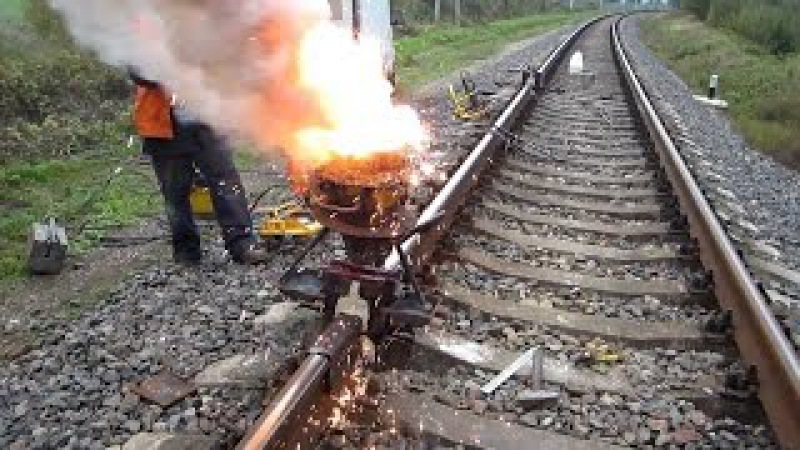
- изготовление из очень прочного материала – высокоуглеродистой стали, одним из свойств которой является плохая свариваемость;
- высокие требования к точности геометрических размеров конечного продукта, так как любые отклонения резко увеличивают вероятность аварии;
- большая протяженность путей, результатом которой становится необходимость быстрого перемещения в процессе работы.
Следствием перечисленных особенностей рельсовых трамвайных путей становятся следующие требования к исполнителю работ по их монтажу:
- специализированное профессиональное оборудование;
- качественные комплектующие и расходные материалы;
- жесткая система мер по контролю над качеством сварных швов и работы в целом.
Электроконтактная сварка
Технология широко применяется в различных сферах деятельности для соединения однотипных деталей. Применительно к монтажу рельсовых трамвайных путей принцип действия электроконтактной сварки выглядит следующим образом:
- сначала стыки рельсов сильно нагреваются под воздействием электрической дуги;
- результатом становится расплавление металла;
- затем происходит стыковка отдельных элементов с образованием в месте соединения однородной массы
Производство работ происходит с применением мобильных машинных комплексов, выполняющих сварку в автоматическом режиме и передвигающихся по смонтированному участку пути. На подготовительном этапе рельсы укладываются в непосредственной близости от предполагаемого места размещения.
Основные достоинства технологии электроконтактной сварки трамвайного пути – универсальность, отменная производительность, серьезный уровень автоматизации рабочего процесса. В числе недостатков – высокая стоимость профессионального оборудования и существенные эксплуатационные расходы. В первую очередь, они необходимы для комплектования рельсосварочной станции дорогостоящими контактными головками разного типа в зависимости от требуемого режима сварки.
Рис. 1. ПРСМ-6 – популярная модель автоматизированной установки для сварки электроконтактным методом |
Электродуговой метод
Электродуговая сварка бесконтактным способом, наряду с термитной, считается наиболее часто применяемой технологией монтажа трамвайных путей. Рабочий процесс ее практического использования выглядит следующим образом:
- рельсы укладываются в месте расположения трамвайного пути;
- между ними остается небольшой по размерам зазор;
- концы рельсов соединяются между собой при помощи металла электродов, который расплавляется под действием электрической дуги.
Главное достоинство описываемого метода – отсутствие необходимости прилагать серьезные усилия при стыковке рельсов и доступная стоимость выполнения работ. Дополнительные и весьма немаловажные плюсы – возможность использования как стационарных, так и мобильных источников электроснабжения разной мощности.
Рис. 2. Сварка рельсового пути электродуговым способом |
Наибольшее распространение получил так называемый ванный способ электродуговой сварки. В соответствии с его технологическим процессом, стык размещается в специальной герметичной емкости — ванне. Между рельсами остается зазор от 14 до 16 мм. Между торцами вертикально сверху помещается электрод. На него подается электрический ток, сила которого составляет около 350 А. В результате металл электрода расплавляется и равномерно распределяется внутри ванны, обеспечивая прочное надежное и долговечное соединение. Основным недостатком технологии выступает сравнительно невысокая производительность, которая объясняется серьезным уровнем трудозатрат.
Газопрессовая сварка
В данном случае применяется совершенно иной принцип соединения стыков рельсов трамвайного пути. Он предполагает сварку отдельных элементов в единую конструкцию при намного более низких температурах, исключающих плавление металла, под воздействием высокого давления. На подготовительном этапе происходит максимально плотное прижатие стыков рельсов друг к другу, которое достигается при помощи специального рельсорезного станка.
Затем место соединения обрабатывается четыреххлористым углеродом или дихлорэтаном, незначительно нагревается с применением комбинированной горелки и сильно сжимается с использованием гидравлического пресса. Воздействие давления с усилием около 10-13 тонн сопровождается разогревом стыка примерно до 1 200 градусов.
Такая технология позволяет получить еще более однородное и прочное соединение рельсов, чем описанные выше способы. Как следствие, чаще всего газопрессовая сварка применяется для монтажа путей, эксплуатация которых предполагаем самые высокие нагрузки, то есть железнодорожных. Основным недостатком метода является высокая стоимость, необходимость в узкоспециализированном дорогостоящем оборудовании и сравнительно низкая производительность.
Термитная (алюмотермитная) сварка
Каждый из перечисленных выше методом сварки рельсового трамвайного пути не лишен каких-либо существенных недостатков. Наиболее сбалансированным и отвечающим современным требованиям к качеству, стоимости и скорости выполнения монтажных работ справедливо считается термитный способ (другие его часто применяемые наименования – алюмотермитный или метод промежуточного литья).
В его основе лежит реакция, происходящая при контакте алюминия и окиси железа, которые входят в состав специального порошка – термита. Результатом реакции становится образование восстановленного железа. Она сопровождается выделением большого количества тепла, что ведет к дальнейшему нагреву металла до температуры примерно 2 000 градусов. После этого он заливается в специальную форму, которая размещается на стыке рельсов и совпадает с ними по форме. Использование в технологическом процессе термита на основе алюминия стало причиной появления названия сварки – термитная или алюмотермитная.
Рис. 3. Алюмотермитная сварка рельсового пути |
Технология была разработана достаточно давно – в середине XIX века. Ее постоянное совершенствование в сочетании с разработкой нового более эффективного и производительного оборудования, а также впечатляющим набором достоинств сделали термитную сварку самым востребованным на данный момент способом монтажа и ремонта рельсовых трамвайных путей.
Технологические особенности, сфера применения и преимущества термитной сварки методом промежуточного литья
В настоящее время применяются 4 базовых метода термитной сварки. Каждый из них имеет характерные особенности и собственную область практического использования. В указанную цифру входят следующие способы выполнения сварочных работ:
-
соединение встык.
Наиболее трудоемкая и сложная для практического применения технология;
- способ промежуточного литья. Обладает комплексом достоинств, подробно описанных ниже;
- комбинированная сварка. Предусматривает совмещение характерных особенностей двух указанных выше методов, комбинируя и их недостатки;
- метод дуплекс. Отличительная особенность данного способа – дополнительная стадия технологического процесса, представляющая собой спрессовку заготовок после заливки сплава восстановленного железа.
Рис. 4. Технологическая схема сварки методом промежуточного литья |
Самой популярной и часто применяемой разновидностью термитной сварки заслуженно считается способ промежуточного литья. В большинстве случаев именно он имеется в виду, если речь идет о рассматриваемой технологии. Основными причинами востребованности метода следует считать три фактора:
- сравнительно простой рабочий процесс;
- длинный перечень достоинств, с лихвой компенсирующий небольшое количество недостатков;
- универсальность в сочетании с широкой сферой практического применения;
- наличие четких и детализированных стандартов, регламентирующих выполнение работ.
Для получения объективного и более глубокого представления об особенностях технологии, требуется подробно рассмотреть каждый из перечисленных факторов.
Схема технологического процесса
Традиционный метод термитной сварки рельсового пути способом промежуточного литья включает в себя следующие технологические этапы:
- над стыком двух рельсов устанавливается специальная конструкция в виде емкости;
-
внутрь ее помещается специальный порошок — термит, на 23% состоящий на крошки алюминия и на 77% — из оксида железа.
Он имеет мелкодисперсную структуру с размерами гранул около 0,5 мм;
- непосредственно на стык монтируется герметичная заливочная форма, конфигурация которой совпадает с профилем рельс;
- металлическая емкость нагревается до 1 000 градусов при помощи разового воздействия специального воспламенителя, запускающего алюмотермитную реакцию;
- она протекает с выделением тепла, результатом чего становится дальнейший нагрев порошка до 2 000 градусов и перемещение получившегося расплава в заливочную форму;
- под воздействием расплава торцы рельсов также сильно нагреваются, оплавляются, в результате чего в месте стыка создается однородная масса по всему сечению рельса;
- постепенное охлаждение сварного шва сопровождается дополнительным уплотнением металла и выдавливанием шлака на поверхность;
-
завершающая стадия рабочего процесса – отбивка шлака и шлифовка сварного шва при помощи обычной болгарки или угловой шлифмашинки.
Преимущества и недостатки
Повсеместное применение алюмотермитной сварки в целом и конкретно метода промежуточного литья объясняется рядом серьезных преимуществ, которые достигаются при грамотном использовании технологии. Самыми впечатляющими из них являются такие:
- высокая скорость ведения сварочных работ. Продолжительность технологического процесса составляет не более 25-30 минут. Как следствие – бригада сварщиков, укомплектованная необходимым оборудованием, способна выполнить 10-12 сварных швов в течение часа;
- отсутствие привязки к стационарным источникам электроснабжения. Для выполнения работ используются мобильные установки, обладающие компактными размерами и работающие в автономном режиме. Общий вес необходимого оборудования редко превышает 350-400 кг;
- сравнительно невысокие требования к квалификации исполнителей. Для грамотного практического применения описываемого способа сварки достаточно четко следовать пошаговой инструкции по выполнению работ и технологической схеме рабочего процесса;
- высокий уровень безопасности, для обеспечения которого достаточно использовать исправное оборудование и выполнять общепринятые правила техники безопасности при проведении сварочных работ;
-
одинаковая эффективность как для монтажа нового рельсового пути, так и при ремонте существующего.
Важный дополнительный плюс – отсутствие необходимости делать длительные перерывы в движении транспорта при выполнении ремонтных работ;
- отменные эксплуатационные характеристики сварного шва. Они не уступают или даже превосходят аналогичные показатели, полученные при использовании альтернативных методов сварки, при заметно более высокой производительности и доступной стоимости производства монтажных работ.
Рис. 5. Термитная сварка рельсового пути |
К числу недостатков, характерных для термитной сварки рельсов трамвайного пути, следует отнести такие особенности технологии:
- необходимость аккуратного и осторожного обращения с используемым в ходе работ порошком, который является легко воспламеняемым веществом;
- для получения качественного шва требуется четкое выполнение схемы и последовательности производимых технологических операций;
-
обязательное условие для безопасного ведения сварочных работ – исключение возможности попадания в рабочие емкости воды, что приведет к разбрызгиванию металла.
Анализ приведенных выше списков достоинств и недостатков наглядно демонстрирует главную причину популярности и востребованности рассматриваемой технологии. Она заключается в сочетании хороших эксплуатационных свойств получаемого на выходе сварного шва с высокой производительностью и доступной стоимостью выполняемых монтажных работ. Очевидным и легко предсказуемым следствием настолько впечатляющего перечня достоинств технологии становится крайне обширная сфера применения термитной сварки в сегодняшних условиях.
Технические стандарты, регулирующие требования к проведению работ
Немаловажным достоинством термитной сварки рельсовых путей выступает наличие детально проработанного стандарта, четко регламентирующего требования к технологическому процессу и правила проведения сварочных работ. Речь в данном случае идет о национальном стандарте РФ – ГОСТ Р 57181-2016. Нормативный документ был введен в действие с 1 июня 2017 года и актуален до настоящего времени.
Положения стандарта содержат рекомендации в области грамотной организации работ по монтажу рельсовых путей любого типа – железнодорожных, трамвайных или для других разновидностей городского электротранспорта. Кроме того, стандарт дает основные определения терминам и понятиям, которые используются для описания технологии термитной сварки, а также устанавливает базовые методы контроля над качеством сварного шва.
Термитная сварка рельсов и проводов
- Термитной называют сварку,
- для осуществления которой применяют порошкообразные смеси (термиты), состоящие из различных элементов, обладающих большим сродством с кислородом, и окислов металлов с небольшой теплотой образования.
Такие смеси быстро сгорают, образуя продукты, нагретые до высокой температуры.
Получение перегретого расплавленного шлака и металла лежит в основе процессов термитной сварки.
Термитная сварка рельсов
Термитную сварку можно осуществлять в двух основных вариантах:
- плавлением (способом промежуточного литья) и
- давлением.
В первом случае процесс выполняется без применения механического усилия за счет теплоты экзотермической реакции термита, достаточной для доведения кромок соединяемых деталей до расплавленного состояния.
Термитная сварка давлением представляет собой химико-механический процесс, при котором соединяемые детали нагреваются в зоне сварки только до пластического состояния с последующим приложением внешнего сжимающего усилия.
В настоящее время находят применение следующие виды термитов:
- алюминиевый,
- магниевый и
- медно-алюминиевый.
Алюминиевый термит состоит из 20—22% алюминия и 80—78% железной окалины, измельченных в порошок с размерами частиц до 1 мм. При нагреве этой смеси, хотя бы в одной точке, до температуры 800° С с помощью специальных запалов или электрической дуги возникает бурное горение, идущее по реакции
3Fe304 + 8Аl = 4Аl203+9Fe.

Температура реакции достигает 3000° С. Таким образом ее продукты: железо (Тпл ~ 1500° С) и глинозем (Тпл ~ 2050° С) — оказываются значительно перегретыми.
Для раскисления и улучшения механических свойств термитной стали практикуется добавка ферромарганца и ферросилиция.
Сварка алюминиевым термитом применяется для стыковых соединений рельсов, труб, массивных отливок и при ремонтных работах.
Техника сварки заключается в том, что концы стыкуемых изделий, помещенные в форму из огнеупорного материала, предварительно нагревают до 700—800° С нефтяными или керосиновыми горелками, а затем заливают формы термитным металлом и шлаком из специального тигля.
При сварке давлением (рис. 1, а) продукты термитной реакции используются только как носители запаса тепла, достаточного для нагрева изделий до пластического состояния, после чего путем сжатия осуществляется их соединение.
При сварке плавлением: (рис. 1, б) детали заформовывают с большим зазором между торцами. Термитный металл оплавляет поверхности изделий, сливается с ними в одно целое, образуя после охлаждения сварное соединение.
При сварке рельсовых стыков применяется разработанный инж. М. А. Карасевым комбинированный способ, схема которого представлена на рис. 1, в.
Рис. 1. Способы термитной сварки: а — давлением; б — плавлением; в — комбинированный способ
Между торцами точно обработанных головок рельсов зажимается пластинка толщиной 3 мм из малоуглеродистой стали.
Затем на стык устанавливают форму и подогревают его. Порция термита подбирается так, чтобы при заливке формы нижняя часть была заполнена жидким металлом почти до нижней кромки головки рельсов. Остальная часть формы заполняется шлаком, после чего рельсы сжимают.
Таким образом, головка рельсов сваривается по способу давления, а остальная часть сечения сваривается по способу плавления.
После снятия формы производятся обработка зубилом выступающих кромок промежуточной пластины и зачистка рабочей поверхности головки рельсов.
Термитно муфельная сварка
Представляют интерес разработанные А. Н. Кукиным и А. А. Талыковым новые способы сварки магниевыми медно-алюминиевым термитами.
Так, на основе реакции
Fe304 + 4Mg = 3Fe +4MgO
осуществляется термитно-муфельная сварка.
Особенностью магниевого термита является выделение окиси магния в твердом состоянии, так как температура реакции (до 2500° С) недостаточна для ее расплавления. Таким образом, продукты реакции представляют собой рыхлую массу окиси магния, пропитанную расплавленным железом.
Термитная сварка проводов
Важнейшей областью применения магниевого термита является муфельная сварка стальных проводов воздушных линий связи.
Для этой цели используют прессованные цилиндрические шашки с осевым каналом и выемкой с торца для вкладывания запала (рис. 2).
Рис. 2. Схема сварки проводов магниевым термитом: 1 — корпус шашки; 2 —запал; 3 — свариваемые стержни
Для осуществления сварки стык проводов, закрепленных в специальных клещах, располагают посередине шашки и затем зажигают ее запал пламенем спички или тлеющим фитилем. После сгорания шашки разогретые концы проводов сваривают путем осадки с помощью клещей.
Для приваривания деталей небольшого сечения к массивным изделиям применяют медно-алюминиевый термит.
В частности, он применяется для таких работ, как приварка заземляющих проводников к стальным конструкциям и медных стыковых соединителей к железнодорожным рельсам. В обоих случаях используется термитная смесь, состоящая из 64% окиси меди, 16% ферромарганца и 20% специального медно-алюминиевого сплава, в свою очередь состоящего из 54% меди и 46% алюминия.
Термитно тигельная сварка
Для осуществления процесса сварки используют специальные разъемные графитовые тигель-формы, плотно прикрепляемые к изделию.
После сгорания термита образовавшийся перегретый металл — марганцовистая бронза — заполняет форму, в которой находится конец проводника, и приваривает его к изделию.
особенности процесса и его преимущества
В наше время разработано множество технологических методов, позволяющих проводить соединение металлических деталей друг с другом. Не последнее место занимает термитная сварка – технология, которая обладает большим количеством преимуществ, совмещая в себе отменную эффективность и невысокую себестоимость. Благодаря этому, такая методика получила достаточно широкое распространение в сфере тяжелой промышленности и строительства.
Стоит отметить, что в отличие от других способов сварки, данная технология максимально автономна. Другими словами, ее можно использовать при работе на объектах, которые отдалены от источников электропитания, необходимых для подключения привычных видов сварочного оборудования – инверторов или полуавтоматов. При этом с ее помощью можно сваривать различные виды металлов, например, нержавеющую сталь, чугун и некоторые виды изделий из алюминия.
В этом материале мы расскажем о некоторых особенностях проведения термитной сварки. Кроме того, вы узнаете о ее главных преимуществах и нюансах, на которые необходимо обратить внимание.
Что представляет собой термитная сварка?
Это метод соединения металлических деталей, основанный на применении термита – специальной порошкообразной смеси, которая содержит в своем составе алюминий и оксиды металлов. Суть процедуры заключается в том, что концам соединяемых элементов придают нужную форму за счет использования термостойких материалов, а затем нагревают их, заливая место соединения предварительно зажженной термитной смесью. В итоге раскаленное железо сваривается с металлом самих деталей, что приводит к созданию прочного, надежного и долговечного соединения, обладающего высокими техническими характеристиками.
В настоящее время эта методика применяется для соединения самых различных изделий из металла, в том числе труб, кабелей, проводов, элементов заземляющего контура и прочих. Особое место при этом отводится работам, проводимым при установке железнодорожных рельсов. Технология применения термита позволяет надежно соединять рельсы друг с другом, без необходимости применения электродугового метода, нуждающегося в наличии поблизости источника электропитания. При этом возможностей газового сварочного оборудования было бы недостаточного для сваривания столь толстых и плотных деталей, как рельсы. Кстати, для описываемого процесса есть ГОСТ Р 57181-2016 (Сварка рельсов термитная).
подготовка процесса
Для кабеля:
В целом, методика применения термита на основе алюминия и оксидов металлов является востребованной, но, как и сварка взрывом, используется лишь в тех случаях, когда в этом есть особая необходимость.
Какие преимущества такой технологии следует выделить
Если говорить о главных достоинствах рассматриваемого процесса, то к ним следует отнести:
- Высокую скорость выполнения работ. Нужно отметить, что это один из наиболее быстрых методов соединения изделий из металла. К примеру, для стыковки железнодорожных рельсов требуется в среднем около 50 минут. При этом если одновременно будет работать несколько бригад, то эффективность такой работы будет лишь возрастать (всего за 2 часа три бригады могут сваривать до 12 стыков).
- Хорошее качество швов. Места стыковки деталей обладают высокой стойкостью к механическим нагрузкам и воздействию химических веществ. Кроме того, такие швы выглядят эстетически привлекательно.
- Легкость выполнения задачи. Такая технология не требует наличия особых навыков и знаний, так как справиться с ней может любой специалист при условии прохождения непродолжительного обучения. Количество задействованных работников также невелико.
- Доступность материалов. Необходимые для этого порошковые смеси и дополнительные материалы можно приобрести в специализированных магазинах, при этом их цена не будет высокой.
- Отсутствие необходимости использования дорогостоящего оборудования. В отличие от методов контактного сваривания металлических элементов, при использовании термитных смесей не обязательно использовать дорогую сварочную технику. Это особенно актуально для работы на отдаленных объектах, когда нет возможности найти источник электрического тока или транспортировать громоздкие газовые баллоны.
При этом есть и некоторые недостатки, к которым можно отнести необходимость соблюдения строгих правил по безопасности. Во-первых, сам по себе термит является легко воспламеняемым веществом, поэтому следует проявлять особую осторожность при его транспортировке и хранении. Во-вторых, во время выполнения задачи нужно позаботиться о том, чтобы вода или любые другие жидкости не попали в горящую смесь, так как это может стать причиной взрыва.
Какие альтернативные методы существуют
Безусловно, по уровню популярности и распространенности эта технология уступает электрическому дуговому методу. С целью получения дополнительной информации о нем, вы можете ознакомиться с материалом о применении газов и сварочных смесей для создания защитной среды при использовании электродуги.
Также предлагаем вам изучить ассортимент продукции нашей компании «ПРОМТЕХГАЗ». Сделать это можно, проследовав по этой ссылке. Обращайтесь!
Сварка рельсов — Страница 44
Страница 44 из 66
РАЗДЕЛ 19.
Сварка рельсов и сварочные работы.
Износ рельсовых концов из-за ударов колес подвижного состава и, следовательно, ударное воздействие изношенных рельсовых концов на всю систему рельс — шпала — балласт было в течение ряда лет главной проблемой текущего содержания всех железных дорог.
Идея сварки стыков, впервые примененной на трамвайных линиях, была быстро подхвачена железнодорожными компаниями. Там, где стыки все еще соединены механически, стало обычным для многих железных дорог при укладке новых рельсов закаливать рельсовые концы и наращивать изношенные рельсовые концы с помощью наплавки.
Большое внимание уделяется устранению колесных ползунов до развития трещин на поврежденной поверхности, в результате чего происходят изломы рельсов.
Восстановление крестовин, глухих пересечений и остряков с помощью наплавки также стало частью программы текущего содержания пути.
Сварка рельсов стыков.
Самый старый и все еще наиболее распространенный способ соединения рельсов — механический стык, но из-за его низкой жесткости, тенденции к ослаблению и высокой концентрации напряжений у болтовых отверстий в нем быстро развиваются повреждения. Перед началом сварки концы рельсов очищают от загрязнителей, затем зачищают в местах контакта с токопроводящими электродами на головке рельса и подошве.
Несмотря на то, что существует большое число процессов контактной сварки, основными положениями для выполнения электроконтактной сварки рельсов являются следующие: после размещения на сварочной машине рельсовые концы подвергаются предварительному нагреву током силой от 20 000 до 100 000 А при напряжении в 5—10 В.
Концы рельсов приводятся в соприкосновение и разводятся несколько раз, что повышает температуру до 1100 °C. После достижения этой температуры электрическая дуга инициируется вновь и один рельс продвигается вперед с установленной скоростью. В течение этого времени неровности на концах рельсов быстро плавятся и удаляются. Как только искрение прекращается, подвижной рельс приводится в движение таким образом, чтобы рельсовые концы были осажены до отказа с постоянной сжимающей скоростью или под воздействием ударной нагрузки.
После выключения сварочного тока и снятия электродов стык остается под давлением не менее 10 с, пока место сварки достаточно не остынет.
Хорошее качество выполнения электроконтактной сварки в пути явилось результатом развития в недавнее время специальной технологии электроконтактной сварки в пути в Советском Союзе, которая была применена в Соединенных Штатах.
Особый тип сварочной машины, в которой сварочная головка выполнена в виде большой скобы, зажимает шейку рельсов специальными зажимами для вертикальной и продольной центровки. Машина производит непрерывное оплавление в течение 3-минутного цикла, который завершается осадкой в 1/2 дюйма, но не до отказа, под воздействием 50-тонной нагрузки.
В период действия осаживающей силы протекает полный сварочный ток. Место сварки выдерживается в осаженном состоянии до тех пор, пока оно не охладится настолько, что выйдет из пластического состояния.
По сравнению со стационарной сварочной машиной для сварки в пути требуется лучшая подготовка поверхности для получения оплавления по всему поперечному сечению рельсового конца. Сварочная машина для сварки в пути использовалась для стыкования длинных рельсовых плетей и для соединения обычных рельсов в бесстыковые рельсовые плети. В последнем случае рельсовые концы должны быть обрезаны с помощью газовой резки или отпилены. Ржавчина, заводское клеймо и смазка должны быть удалены с обеих сторон рельса в местах, где электроды зажимают рельс.
Газопрессовая сварка.
Газопрессовый сварочный процесс конкурирует с электроконтактной сваркой. Однако в последние годы электроконтактная сварка стала предпочтительнее из-за своих технических преимуществ — производительности и качества сварки. Рельсовые концы должны быть отпилены для получения чистой, ровной стыкуемой поверхности. Если это не будет выполнено надлежащим образом, отдельные места будут недостаточно проварены по окончании сварки.
В процессе сварки оба конца рельса нагреваются газовым пламенем, образующимся от сгорания горючего газа в кислороде. Концы рельсов зажимаются в сварочной машине и при достижении температуры около 2000 °F происходит осадка под давлением 3000 фунтов/дюйм2.
После достижения температуры 2250 °F рельсовая сталь становится достаточно мягкой: каждый рельс можно переместить на дюйма для создания осадочной области. Сварка происходит в жидком состоянии благодаря росту зерен, их сращиванию и диффузии вокруг поверхности соприкосновения. Выдавленный при сварке металл можно удалить гидравлическим или газовым резаком.
В отдельных случаях, когда место сварки остывает до температуры около 900 °F, металл нормализуется при повторном нагреве до 1500 °F. Таким образом достигается однородность свойств металла в месте сварки и в смежных сечениях, что придает стыку более высокую механическую прочность.
Впервые газопрессовый сварочный процесс применен в Соединенных Штатах в 1939 г. В Японии на рельсосварочных предприятиях этим способом сваривают короткие рельсы в бесстыковые рельсовые плети.
Недавно в Соединенных Штатах сконструирован портативный сварочный аппарат, предназначенный для сварки в пути. Аппарат плотно прикрепляют к рабочей площадке, где рельсы длиной 39 футов сваривают в плети длиной 1140 или даже 1800 футов. Портативный генератор мощностью 55 л. с. вырабатывает энергию для оборудования. Рельсы подогреваются кислородно-ацетиленовым пламенем.
Термитная сварка.
Алюминотермитная реакция, на которой базируется термитный сварочный процесс, была впервые успешно проведена в 1898 г. проф. X. Голдсмидтом. С того времени термитная сварка рельсов успешно применяется во всем мире. Эта алюминотермитная реакция происходит в соответствии с таким химическим уравнением:
Термитный порошок состоит из окиси железа, чистого алюминия и некоторых видов сплавов для получения такого химического состава стали, который обеспечивает прочность и твердость, аналогичные свариваемым рельсам1.
Однажды начавшись, с использованием внешнего источника тепла реакция термитной смеси будет протекать благодаря большой разнице в теплоемкости у А12О3 и Fe3O4 до тех пор, пока окись железа полностью не заменится алюминием. Из-за различия плотности у А12О3 (шлак) и Fe (термитная сталь) они отделяются самостоятельно сразу же после завершения реакции. Большое количество тепла, выделяемого при реакции, приводит к очень сильному нагреву металла, что необходимо для плавления рельсовых концов и достижения полного сплавления термитной и рельсовой стали. В течение многих лет развивались различные сварочные процессы, использующие идею алюминотермитной реакции.
Подготовка рельсовых концов перед термитной сваркой.
Большинство сварочных процессов требует, чтобы концы рельсов были сухими (в процессе сварки выделяется водород), очищенными от смазки и ржавчины. Рельсы с болтовыми отверстиями, близко расположенными к их концам, нельзя использовать: болтовые отверстия — концентраторы напряжений. У болтовых отверстий развиваются трещины, которые приведут к излому сварного стыка.
При необходимости установки рельса с накладками и последующего восстановления пути при помощи термитной сварки болтовые отверстия обычно не сверлят в непосредственной близости к рельсовым концам. Если рельсовые концы можно шлифовать, то это самый простой способ их очистки. В противном случае их можно отрезать абразивным кругом, газовым резаком или отпилить.
При газовой резке обычную углеродисто-марганцовистую сталь не нужно подогревать. Но для уменьшения времени, требуемого для начала резания, рекомендуется предварительно нагревать рельсовые концы до 600 °F, особенно при низких температурах воздуха.
Легированные рельсовые стали, которые появились недавно, нужно подогревать перед обрезкой газовым резаком. Шлак, образующийся при газовой резке, должен быть удален.
При обычном термитном сварочном процессе нужно подогревать концы рельсов в течение 50 мин. Модифицированные в настоящее время процессы позволяют обходиться без предварительного подогрева, ограничиваться подогревом в течение короткого времени или длительным подогревом продолжительностью до 20 мин.
‘ По данным железных дорог СССР прочность стыка, сваренного термитной сваркой, составляет только 65—80% прочности целого рельса (примеч. ред. перевода).
Для всех термитных процессов (с длительным или коротким предварительным подогревом) нужны инвентарные принадлежности: тигель для внешней реакции термитного порошка и оборудование для предварительного подогрева. Термитный процесс без предварительного подогрева не требует дополнительного оборудования.
Если нет времени на подогрев, нужное для подогрева количество тепла должно компенсироваться дополнительным количеством термитной стали, которая используется в этом случае для предварительного нагрева концов рельсов.
В термитных процессах без предварительного нагрева рельсовых концов с помощью внешнего источника тепла около 1/3 термита расходуется только для предварительного нагрева.
При использовании термитного процесса с коротким подогревом для завершения сварки затрачивается суммарное время 20 мин. Это время включает в себя время на предварительный нагрев, срезку и удаление шлифовкой лишнего металла с головки рельса. Термитная сварка, первоначально примененная на Немецких Федеральных Железных дорогах, успешно использовалась даже на пути с очень высокой интенсивностью движения*.
Стыки, сваренные при помощи термитной сварки, больше похожи на литые, чем на сварные. Механические свойства таких стыков несколько ниже, чем у прокатного рельса.
* На железных дорогах СССР термитная сварка практически не применяется (примеч. ред. перевода).
Станок с абразивным диском для обрезки рельсовых концов
Однако их работа в эксплуатации при наличии строгого контроля за процессом сварки и детальной разработки технологии ее выполнения сопоставима с работой сварных стыков, полученных с помощью других сварочных процессов.
Термитная сварка рельсов — эффективный процесс соединения рельсов в пути из-за его портативности и низкой стоимости. Наиболее широко используется для соединения плетей, сваренных на рельсосварочных предприятиях, после их укладки в путь. Термитная сварка — типовой сварочный процесс для сварки рельсов в пути выполняется также на рельсосварочных предприятиях.
Термитная сварка с предварительным (слева) и без предварительного подогрева (справа)
Для соединения рельсовых концов используется ряд электродуговых сварочных процессов. Наиболее распространенные процессы сварки — электрошлаковая, электродуговая под флюсом и закрытая электродуговая. Все виды электродуговой сварки должны выполняться высококвалифицированными рабочими. Электродуговая сварка углеродисто-марганцовистой рельсовой стали с металлургической точки зрения подвергается критике, так как при ее выполнении образуются трещины. Это происходит, главным образом, из-за высокого содержания водорода, который получается при высокой скорости охлаждения нагретых участков основного металла.
Электрошлаковая сварка
Электрошлаковая сварка — процесс, в котором слой расплавленного флюса (шлака) плавит электрод и поверхность основного металла. При сварке рельсов нужна керамическая или охлаждаемая водой медная форма такой же конфигурации, как рельс, для удержания расплавленного шлака и металла в зазоре между концами рельсов.
Электрошлаковая сварка применяется в основном на подъездных, подкрановых путях, несмотря на то, что сложная форма сечения рельса затрудняет достижение однообразного нагрева без перегрева отдельных участков.
Электро-дуговая сварка под флюсом и электрошлаковая сварка.
При электродуговой сварке под флюсом тепло для сварки получают от электрической дуги, образующейся между электродом и основным металлом. Дуга защищается слоем флюса, который покрывает расплавленный присадочный и основной металл и предохраняет место сварки от загрязнения.
Подошвы рельсов сваривают при помощи электродуговой сварки под флюсом, а шейку и головку — электрошлаковой сваркой. Такой процесс разработан в Японии. На Японских национальных железных дорогах сконструирован специальный вагон для сварки рельсов в пути этим методом.
Закрытая электродуговая сварка.
Закрытый электродуговой сварочный процесс был разработан на основе процесса резки металла защищенной дугой и используется с более тяжелыми рельсами. Тепло для сварки получается от электрической дуги между электродом, покрытым флюсом, и основным металлом.
Электрод сваривает металл, а электрическая дуга защищается от атмосферных воздействий газами, образующимися при сгорании флюса.
Механизм для срезки грата с обеих сторон
Перед началом сварки концы рельсов должны быть предварительно нагреты приблизительно до 930 °F.
Срезка грата на участке термитной сварки
Термитная сварка рельсов. Видео на железной дороге
Многим известен такой вид сварки, как электродуговая и газовая. Они широко применяются как на производстве, так и в строительстве. Но термитная сварка мало кому известна. Поэтому речь пойдет о ней. Благодаря использованию термитной сварки, получаются, ничем не хуже по качеству соединения, как при электро или газосварке, притом не требуется источник электропитания или газовые баллоны.
Сферы применения
Термитную сварку на сегодняшний день используют для сваривания чугуна, электрических и телефонных коммуникаций, труб, частей двигателя и так далее. Особо часто термит используют для сваривания железнодорожных рельсов. Соединения получаются достаточно надёжные. Место ремонта может быть на любом участке дороги, даже в несколько сот километров от населенного пункта.
Термитная сварка
Появление термитной сварки было обусловлено необходимостью стыкового соединения металлов без использования громоздкого оборудования и наличия электросети. Поэтому в 1859 г. Бекетов Н. Н. обнаружил способ, в основе которого лежит алюминотермия ― процесс получения металла восстановлением их окислов алюминия. Он определил, что смесь порошка алюминия и оксида железа, горя при 3000° C, превращаются в сталь и шлак.
В 1898 г. исследователь из Германии Гольдшмидт, впервые применил термитную сварку на практике, соединив два железных бруска. Сделал он это, образовав форму вокруг места стыка и засыпав его термитным порошком. Сгорев, термитный порошок превратился в расплавленное железо, соединив таким образом два металлических бруска. При этом шлак всплывал на поверхность и мог свободно отделиться.
С того времени состав термита практически не изменился. Чаще всего термит имеет в своём составе опилки алюминия ― 23%, и окись железа― 77%. Фракция порошка составляет ― 0,5 мм. В момент поджига порошка, возникает химическая реакция, благодаря которой выделяется много тепла. Плавясь, окись железа переходит в чистое железо, а расплавленный алюминий окисляется.
Термитная сварка рельсов
Процесс сваривания рельсов термитом заключается в следующем:
- обрезка рельс с двух сторон, чтобы промежуток между ними был 23 ― 25 мм. Притом они должны быть выставлены горизонтально и вертикально;
- в зазор между рельсами вставляется пластина из углеродистой стали, для образования зазора;
- стык рельсов зажимается прессом;
- на место соединения монтируется огнеупорная форма, а стыки формы с рельсами, засыпаются песком, или замазываются специальной пастой;
- поверх форм прикрепляется тигель (конус в виде лейки из огнеупорного материала) в котором первоначально сжигается термит. Расплавленный жидкий металл полученный в тигле, в последствии выливают в форму на стыке рельс;
- термит в тигле поджигается термитным карандашом, после чего происходит горение основной смеси 20 ― 30 секунд;
- снизу в воронке тигля установлена заглушка, которая расправляется и освобождает проход жидкому металлу в форму. Сталь и шлак заполняя форму, образуют соединительный шов, притом шлак частично вытесняется наружу в специальные чаши, прикрепленные сбоку тигля;
- горячая сталь заливаемая в форму, проплавляет торцы рельс. После, убирается тигель, и форма сжимается прессом;
- форму снимают, и пока металл ещё горячий, удаляют его избыток;
- получившийся шов, тщательно шлифуют до образования однородной плоскости с рельсой.
Термитные карандаши
В продаже можно найти термитные карандаши. Это кусок проволоки состоящей из углеродистой стали, диаметром до 5 мм. На неё наносят термитную смесь перемешанную с клеем. С одной стороны карандаша имеется место для запала. Что-то вроде бертолетового шнура, но нанесенного в виде дорожки на сам карандаш. Карандаш вставляют в держатель ― как для электросварки, ― и поджигают верхнюю часть. Когда огонь доходит до основного состава на другом конце карандаша, происходит запал термита. Сварку необходимо производить с защитным щитком и рукавицами. Этот же карандаш применяется для поджига основной смеси в тигле. Его поджигают и бросают в тигель с термитной смесью.
Кроме карандашей, существуют ещё термитные шашки и патроны. По принципу работы они схожи с термитным карандашом.
Достоинства термитной сварки- крепкое и надежное сварочное соединение с высокой стойкостью к разрушению;
- технология сварки отличается простотой и доступностью, что предполагает ее использование как в промышленности, так и в быту;
- самый оптимальный вариант сварки при аварийных ситуациях.
- высокое поглощение влаги;
- смесь из-за способности воспламенятся, считается пожароопасной, что требует бережного отношения и хранения;
- попадание влаги на термитную шашку приводит к образованию взрыва;
- неспособность контролировать процесс горения термита.
Оборудование для термитной сварки рельс
- вольфрамовый или керамический тигель с плавящейся заглушкой, и приспособленный для слива жидкого металла в форму;
- отливочные формы для придания расплавленному металлу формы рельсов;
- пресс для сжатия форм после заливки металла;
- дополнительное оборудование: подставка для тигля, термометр, горелка;
- дополнительные материалы и инструменты: болгарка, шлифовальные круги, кувалда, зубило, металлическая щётка, термостойкая одежда, рукавицы, защитные очки для глаз и другое.
Все это обеспечит качественную работу и защитит персонал от разрушительного воздействия тепла и грязи получаемых при сгорании термосмеси.
https://www.youtube.com/watch?v=kuydZx-ckTs
Условия для сварки рельс термитом
Чтобы соединение при процессе сварки получилось качественным и крепким, необходимо соблюдать следующие условия:
- количество порошка термита необходимо просчитать столько, сколько нужно для заполнения металлом формы вокруг рельса;
- важно, чтобы смесь шихты была тщательно измельчена и перемешана;
- температура горения зажигательного элемента (шашка, карандаш), как катализатора поджига основной смеси, должна быть не менее 1400°C.
Несмотря на свои незначительные недостатки, термитная сварка может с успехом конкурировать по безопасности и качеству с такими сварками, как электродуговая и газовая. Например, газовая взрывоопасна, а электрическая не исключает поражение электротоком. Да и многое в этих видах сварок напрямую зависит от квалификации самого сварщика. В термитной же, большую роль играет качество смеси и сохранение технологии, а остальное получится само ― собой.
Термитная сварка
Термитная (алюминотермитная) сварка применяется при сварке рельсов — для сварки применяется термит, расфасованный определенными порциями. Работу выполняет бригада из двух-трех человек. Общий вес используемого оборудования не превышает 350 – 400 кг. При выполнении сварки и сопутствующих технологических операций используются автономные источники энергии.
Алюминотермитная сварка рельсов имеет ряд преимуществ перед контактной сваркой: она не требует сложного дорогостоящего оборудования, большого количества рабочих, продолжительных перерывов в движении поездов. Кроме того она может применяться при сварке на стрелочных переводах. Процесс сварки одного рельсового стыка занимает около 50 минут, а благодаря возможности работы нескольких бригад одновременно, можно добиться большей производительности в «окно». Например, за двухчасовое «окно» силами трех бригад можно изготовить до 12 стыков.
История развития производства термита и термитной сварки рельсов
В Москве термитную сварку впервые применили в 1915 г., когда было сварено 126 стыков. В 1918 г. сварили еще 151 стык. С 1923 г. в трамвайных путях столицы начинают регулярно варить стыки термитом. До 1925 г. стыки сваривали импортным термитом. В 1925 г. на Московском термитно-стрелочном заводе инженером М. А. Карасевым было налажено промышленное производство термита.М. А. Карасев внес крупный вклад в развитие алюминотермии, организовав на базе отечественной технологии выпуск термитных смесей для народного хозяйства. Он предложил рациональные способы производства алюминиевого порошка и термита.
В последующие годы в путях московского трамвая было сварено термитом свыше 100 000 стыков.
Сварка производилась двумя способами: комбинированным и врасклинку. Ввиду того, что стыки, свариваемые последним способом, Часто выходили из строя, к 1931 г. этот способ перестали применять. Вместо него начали внедрять способ сварки промежуточным литьем. Одновременно начали применять способ сварки «дуплекс» (способ промежуточного литья с последующим прессованием). Однако этот способ не получил широкого распространения из-за сложности технологического процесса.
Качество сварки термитных стыков за первые 10 лет ежегодно улучшалось, и количество лопнувших (в течение года) стыков в среднем не превышало 0,8%.
Применение отечественного термита для сварки рельсовых стыков показало его превосходство перед импортировавшимся термитом. В стыках рельсов, сваренных отечественным термитом, значительно меньше процент брака. Это подтверждают результаты эксплуатации первой очереди Московского метрополитена. Так, например, каждый рельсовый стык на участке Сокольники — Парк культуры в 1938 г. выдержал 13,4 млн. ударов с грузонапряженностью 53 млн. т-км.
В 1936 г. вышло из строя 0,17% от количества эксплуатируемых в путях стыков, в 1937 и 1938 г. — по 0,5%.
Из приведенного количества выбывших из строя стыков 75% разрушились из-за наличия болтовых отверстий в зоне сварки.
В эти же годы термит стали внедрять в другие отрасли народного хозяйства. В частности, была разработана и успешно осуществлена термитная сварка стыков легированных труб первого прямоточного котла высокого давления; начали применять также термитную сварку для ремонта крупногабаритных стальных деталей: валов, колонн и т. п.
Принцип получения трудновосстанавливаемых металлов из их окислов впервые был выдвинут крупнейшим русским ученым-химиком, основоположником современной физической химии Н. Н. Бекетовым. В 1865 г. в своей докторской диссертации «Исследования над явлениями вытеснения одних элементов другими» Бекетов превратил этот принцип в научную теорию, заложив основу алюминотермии. Он установил, что алюминий обладает очень большой активностью, соединяясь с кислородом, и что при определенных условиях алюминий легко восстанавливает из окислов другие металлы, стоящие правее его в таблице напряжений химических элементов.
Железнодорожный путь для термитной сварки | JLC Онлайн
Железнодорожные пути соединялись с помощью рыбных накладок, металлических косынок, прикрепляемых болтами по бокам стыков между путями. Теперь они сварены в непрерывные стальные ленты. Но процесс отличается от того, что вы можете себе представить; вместо использования дуговой сварки, кислородно-ацетиленовых сварочных аппаратов или оборудования для сварки в среде защитного газа люди, выполняющие работу, скорее всего, будут использовать процесс, называемый термитной сваркой (видео ниже).
После того, как концы рельсов были отшлифованы и установлены на расстоянии приблизительно один дюйм, они помещаются в полую форму и предварительно нагреваются мощной горелкой.Тигель помещается на форму и заполняется термитом, легко воспламеняющимся порошком на основе алюминия, который горит при температуре около 4500 градусов по Фаренгейту. После зажигания чем-то похожим на бенгальский огонь 4 июля термит превращает составляющие его части в расплавленный металл, который заливается в форму ниже — заполняя зазор между рельсами и сваривая их в цельный кусок стали. Форма снимается, излишки металла отбиваются или растачиваются, а стык между рельсами шлифуется. От начала до конца, процесс может занять около часа.
Это не единственный способ сваривать железнодорожные пути (автоматические аппараты для дуговой сварки тоже могут это делать), но, безусловно, на него приятно смотреть, потому что кто не любит искры и расплавленный металл? Кстати, в термитной сварке нет ничего нового; он был изобретен в 1890-х годах и десятилетиями использовался военными для менее «конструктивных» целей.
Это видео было снято в Швеции, что имеет смысл, учитывая скандинавские рабочие штаны, которые носят парни, выполняющие работу.Примерно на отметке 3:30 вы можете увидеть потрясающее газовое шлифовальное устройство.
Это было снято в Фолкстоне, штат Джорджия, и показывает весь процесс. Он начинается с фотографий и переключается на видео примерно на отметке 40 секунд. Некоторые крутые гидравлические шлифовальные машины (2) появляются примерно на отметке 7:30. Мне нравятся его протекторы для голеней и ступней — они выглядят как что-то из рыцарских доспехов.
Этот был снят где-то в Сибири.Я включил его, потому что мне нравится, как вы слышите кипение расплавленного металла внутри тигля (начинается примерно с 1:58). В тигле содержится достаточно термитов, чтобы шлак от реакции не попал в стык. Он всплывает наверх и выходит последним, разливая по лоткам с обеих сторон формы после заполнения стыка.
Thermit Welding Guide: Process & Equipment
Процесс сварки thermit® является результатом плавления, возникающего в результате химической реакции, которая возникает из-за разницы в свободной энергии между алюминием и оксидом металла.
Эта разница производит достаточно тепла для производства жидкой стали или любого другого металла и позволяет без применения внешней энергии.
Возникает без давления или с приложением давления. Использование присадочного металла не обязательно.
Все компоненты алюминотермического процесса используются в виде порошков или гранул.
Когда реакция инициируется внешним источником тепла, алюминий восстанавливает кислород из оксида металла, что приводит к образованию жидкого перегретого оксида алюминия (Al (2) O (3).
Поскольку эти два компонента различаются по плотности, они разделяются автоматически, и жидкий металл можно использовать для производства сплавов, специальных металлов или для различных сварочных работ. (см. видео ниже)
Этот процесс был открыт Гансом Гольдшмидтом в 1898 году. С начала века термитный процесс используется для соединения рельсов поездов, а также для других применений в транспортной отрасли.
Пример термитной сварки
Ключевые определения:
- Тигель : химическая реакция термита происходит в сосуде, называемом тиглем
- Смесь : Смесь тонкодисперсного алюминия и оксида металла с добавлением любых требуемых легирующих металлов
- Форма : это форма, которая формируется вокруг деталей, которые необходимо сварить.В режим поступает расплавленный металл.
- Реакция : Химическая реакция между алюминием и оксидом металла. В результате реакции образуется шлак из оксида алюминия и перегретый расплавленный металл.
Материал
Материал Thermit представляет собой механическую смесь металлического алюминия и обработанного оксида железа.
Расплав стали получают реакцией термита в тигле, облицованном магнезитом.
На дне тигля обжигается магнезитовый камень, в который вставлен наперсток из магнезитового камня.
Эта гильза обеспечивает проход, через который расплавленная сталь выгружается в кристаллизатор.
Отверстие в гильзе заглушено метчиком, которое залито огнеупорной шайбой и огнеупорным песком.
Тигель загружается путем помещения в него правильного количества тщательно перемешанного термитного материала.
Процесс
При подготовке стыка к термитной сварке свариваемые детали необходимо очистить, выровнять и прочно удерживать на месте.
При необходимости металл удаляют из стыка, чтобы обеспечить свободное течение термитного металла в стыке.
Затем вокруг стыка делается восковая модель по размеру и форме предполагаемого сварного шва.
Форма из тугоплавкого песка строится вокруг воскового рисунка и соединения, чтобы удерживать расплавленный металл после его заливки.
Песочная форма затем нагревается, чтобы расплавить воск и высушить форму. Форма должна иметь надлежащую вентиляцию, чтобы обеспечить выход газов и правильное распределение термитного металла в стыке.
Тигель и форма для термитной сварки показаны на рисунке 5-41 ниже.
Процесс сварки рельсов: (см. Видео выше)
- Подготовить рельс к сварке
- Установить сварной зазор
- Зажим
- Применить формы
- Поместите порцию Thermit в тигель
- Подогреть концы рельсов
- Зажигать и заливать сталь
- Демонтаж
- Избыточный сдвиг металла головки
- Черновое шлифование
- Окончательное шлифование
Схема термитной сварки и тигля
Рисунок 5-41 Анимационное видео процесса термитной сварки
Комплекты для термитной сварки
На рисунке: Набор инструментов для запуска от Orgo ThermitНаборы могут варьироваться в зависимости от требуемого процесса сварки:
- Inch SKV Process: Общий подход к соединению двух рельсов поезда
- 1.5-дюймовый процесс SKV: новый процесс, снижающий риск внутренних включений.
- Сварной шов с широким зазором 2,75 дюйма: Используется при замене дефектного сварного шва или сварного шва Thermit.
- Ремонтный шов с полной головкой: Используется для заполнения после удаления поврежденного участка на головке рельса.
Набор инструментов для крановых балок Thermit
Набор инструментов для крановых балок ThermitКаталожные номера
Orgo Thermit
Что такое термитная сварка железных дорог? | Железнодорожная технология для стальных рельсов
Это информационный пост. Если вы ищете продукт, посетите страницу, посвященную термитной сварке рельсов.
Железнодорожная термитная сварка — распространенный метод в строительстве железных дорог. Как известно, на стыке двух стальных рельсов имеется стык. Есть проблема в железнодорожной отрасли. Когда поезд уходит, огромное давление вызовет тряску, даже трещину. Эти проблемы поставят под угрозу срок службы стальных рельсов и безопасность поездов. Итак, как решить интерфейс — важный проект для железнодорожной техники.С развитием обрабатывающей промышленности существует два основных метода сварки железнодорожных путей.Один из них — электрическая пайка, другой — термитная сварка. Что такое термитная сварка? Железнодорожная термитная сварка считается наиболее высокоэффективным методом сварки железнодорожных путей. Благодаря высокой эффективности, надежному качеству и высокой технологичности, термитная сварка железных дорог становится самым популярным способом в строительстве железных дорог. Широко распространена термитная сварка. В железнодорожном строительстве используется для сварки железнодорожных путей. Цельнотянутый рельс может быть изготовлен методом термитной сварки.
Принцип работы понятен. После настройки аппарата для термитной сварки предварительно нагреваем стальные рельсы до 600 градусов. Затем поместите сварочную часть в тигель и зажгите сварочную часть. Сварочная часть будет производить расплавленную сталь и шлак. Жароплавкая сталь расплавит поверхность раздела между двумя стальными рельсами.
Термитная сварка проста в эксплуатации. Компания AGICO Rail предоставляет комплекты для термитной сварки, такие как сварочная часть, песчаная форма, воспламенитель и другие отдельные части для термитной сварки на железных дорогах.Как сварить железнодорожные пути? Какова процедура термитной сварки? AGICO Rail предлагает вам простое руководство.
Процесс железнодорожной термитной сварки
Процедура сварки железнодорожным термитом состоит из 13 этапов. Мы можем разделиться на три части. Первая часть — это подготовка, вторая часть — операция, а третья часть — проверка. Сначала мы познакомимся с подготовительной работой.
Подготовительные работы
- Для начала подготовим сцену сварки.Нам нужно вырыть яму глубиной 300 мм, и в нее поставить тигель. Затем разгрузите железнодорожные крепления и измерьте температуру железнодорожных путей. Тем временем проверьте модель железнодорожного пути и убедитесь, что термит подходит для этих железнодорожных путей.
- Во-вторых, надо проверить железнодорожный путь. Проверьте, есть ли на поверхности оксид или нет, и проверьте правильность положения конца рельса. Расстояние между концом рельса и железнодорожной шпалой должно быть более 10 см, иначе нам нужно отрегулировать положение рельса.
- В-третьих, это важный шаг. Нам нужно убедиться, что концы рельсов выровнены. Четыре основных параметра, которые необходимо проверить: расстояние, вертикальное выравнивание, горизонтальное выравнивание и кручение.
Расстояние между концами направляющих должно составлять 23-27 мм. горизонтальное выравнивание означает сохранение выравнивания центральной линии каждого железнодорожного пути. Вертикальное выравнивание означает, что расстояние между железнодорожными шпалами должно составлять 1,5 мм. (Расстояние между деревянными шпалами должно быть 3.2 мм.) Скручивание означает, что головка рельса и конец рельса находятся на одном уровне.
Рабочий процесс
После того, как все подготовлено, приступаем к сварке железнодорожного полотна.
- Сначала поместите песчаную форму на стальные рельсы и покрасьте герметичный материал. Более того, рабочие должны поддерживать на одном уровне центральную линию песчаной формы и оси стального рельса.
- Следующий этап — предварительный нагрев.Предварительный нагрев направлен на устранение сырости и повышение температуры песчаной формы, чтобы избежать исчезновения пузырей и шлака. Топливо — кислород и пропан. Во время этой процедуры вы можете подготовить термит и тигель.
- Затем рабочие выливают термит в форму для песка. Спустя 5 минут рабочие забирают тарелку для отходов и тигель и разбирают песчаную форму.
Инспекция
- Перед использованием необходимо выполнить горячее и холодное шлифование.Следует обратить внимание на несколько советов во время процесса горячего шлифования. Сначала уберите клин через 15 минут. Во-вторых, сварочная головка внутри и снаружи находится на одном уровне с обеими сторонами направляющих.
- Холодное шлифование направлено на удаление любых геометрических неоднородностей, вызванных сваркой. Холодное измельчение должно начаться через 1 час после заливки.
Ведь рабочие должны очистить место сварки и сделать отметку на сварном шве.
На данный момент мы внедрили метод железнодорожной термитной сварки.Если вас интересует эта железнодорожная техника, вы можете связаться с нами для получения более подробной информации. AGICO Rail поставляет вам комплект для термитной сварки. Более того, как производитель железнодорожных компонентов, мы поставляем различные стандартные стальные рельсы и железнодорожные крепежные детали, такие как анкерная пластина рельса и стыковочный узел . Кроме того, при необходимости мы предоставляем профессиональные услуги!
Остаточные напряжения в рельсах, сваренных термитной сваркой: значение дополнительной ковки
Термические свойства
Модель FE включает два различных материала: рельсовую сталь марки R260 для рельса и металл сварного шва.Предполагается, что они имеют одинаковые термические и механические свойства. Тепловые свойства стали R260 оценены по Тучковой [22]. На рис. 4 показано изменение плотности, теплопроводности и теплоемкости в зависимости от температуры. Обратите внимание, что конвекция в бассейне с жидкостью была аппроксимирована искусственным увеличением проводимости выше температуры плавления ( T ≥ T liq = 1465 ° C) в пять раз, см. Chen et al. [2].
Фиг.4a Изменение плотности, проводимости и теплоемкости в зависимости от температуры, рассчитанное по Тучковой [22]. b Температурная зависимость модуля Юнга E (слева) и коэффициента Пуассона ν (справа) по оценкам Skyttebol и Josefson [10]. c Температурная зависимость предела текучести и модуля упрочнения, по Skyttebol и Josefson [10]. d Коэффициент теплового расширения рельса и металла шва при нагреве и охлаждении.Из Ahlström [23]
Скрытая теплота и фазовые превращения
Эффект фазовых превращений был учтен в термическом анализе путем определения скрытой теплоты, которая моделирует большие изменения внутренней энергии из-за фазовых изменений материала. Фазовое превращение из жидкости в твердое происходит при T liq = 1465 ° C и T sol = 1380 ° C, см., Например, Тучкова [22], с полной внутренней энергией, связанной с фазовый переход, соответствующий 277 кДж / кг. {\ mathrm {th}} $$
(1)
, где Δ ε e , Δ ε p и Δ ε th обозначают изменения упругой, пластической и термической деформации соответственно.Вязкопластическими деформациями и деформациями ползучести можно пренебречь, поскольку время, проведенное при более высоких температурах, относительно невелико. Чтобы снизить вычислительные затраты, участки материала, которые не представляют особого интереса, то есть участки рельса вдали от зоны плавления (FZ), считаются упругими во время процесса ATW. В этих областях не ожидается значительных температурных градиентов или пластической деформации.
Поведение эластичного материала
Предполагается, что металл рельса и сварного шва представляет собой изотропный эластичный материал с модулем Юнга E и коэффициентом Пуассона ν , взятыми из Skyttebol и Josefson [10].На рис. 4б показаны температурные зависимости E и ν .
Обратите внимание на рис. 4b, что жесткость уменьшается с повышением температуры, что означает, что материал размягчается. Однако нижний предел для E при более высоких температурах является неопределенным из-за ограниченных экспериментальных данных для высоких температур. Здесь было выбрано минимальное значение 100 МПа при температурах выше 1000 ° C. Это значение подтверждается ограниченными экспериментальными результатами из литературы [22].
Коэффициент Пуассона увеличивается до величины 0,5, как показано на рис. 4b. Однако, чтобы избежать численных проблем с несжимаемым материалом, это значение нельзя принимать слишком близким к 0,5.
Поведение пластического материала
Предел текучести и упрочнение при комнатной температуре и при 600 ° C были определены на собственном предприятии, см. Skyttebol и Josefson [10]. Дальнейшее изменение предела текучести при температуре принимается таким образом, чтобы оно соответствовало таковому в Еврокоде (EN 93-1-1 Еврокод 3: Проектирование стальных конструкций — Часть 1–1: Общие правила и правила для зданий).Металлы рельса и сварного шва моделируются с использованием линейного изотропного упрочнения, поскольку процесс ATW включает только ограниченную обратную текучесть при более низких температурах; хотя циклические эксперименты с рельсом R260 ограничены, Skyttebol и Josefson [10] показывают, что кинематическое упрочнение или, скорее, нелинейное кинематическое упрочнение может быть лучшим представлением. Температурное изменение предела текучести и модуля упрочнения показано на рис. 4c.
При более высоких температурах материал считается эластичным идеально (идеально) пластичным.Более того, при этих температурах доступных данных мало, см. Выше. Здесь нижнее предельное значение предела текучести принято равным 25 МПа для температур выше 1000 ° C, что также подтверждается ограниченными экспериментами в литературе, Линдгрен [24].
Когда материал охлаждается после заливки, он будет подвергаться твердофазным превращениям из аустенита в перлит, как описано ниже. Предполагается, что мера упрочнения, то есть эффективная пластическая деформация, накопленная в более ранней фазе, не повлияет на упрочнение в новой фазе.Следовательно, накопленная эффективная пластическая деформация сбрасывается при определенной температуре, в данном случае выбранной как 700 ° C, с использованием функции отжига ABAQUS.
Объемные изменения во время фазовых превращений
Тепловое расширение перлита и аустенита при нагревании и охлаждении соответственно следует по Альстрему [23] и показано на рис. 4d. Объемное расширение, наблюдаемое при превращении аустенита в перлит (при быстром охлаждении), моделируется соответствующим уменьшением коэффициента теплового расширения в температурном интервале фазового превращения.{\ mathrm {th}} = \ alpha \ (T) \ cdotp \ left (T- \ mathrm {Tref} \ right) \ hbox {-} \ upalpha \ \ left (\ mathrm {Tin} \ right) \ cdotp \ left (\ mathrm {Tin} — \ mathrm {Tref} \ right) $$
(2)
, где α , T , T ref и T в — это, соответственно, коэффициент теплового расширения, температура, эталонная температура и начальная температура. {\ mathrm {th}} = \ alpha \ (T) \ cdotp \ mathit {\ Delta T} $ $
(3)
За эталонную температуру подаваемого расплавленного материала принимается температура, которую он имеет при заполнении сварного зазора, см., Например, Линдгрен [24].Здесь эта температура принята при температуре плавления 1465 ° C. Это также означает, что объемные изменения, возникающие при затвердевании металла шва, предполагаются в верхней части формы над зазором сварного шва.
Процедура моделирования методом конечных элементов
Как упоминалось выше, процесс ATW моделируется как последовательно связанный термомеханический анализ. Таким образом, настраиваются два разных анализа, один термический анализ и один механический анализ. Поле температуры, вычисленное в термическом анализе, импортируется в механический анализ как нагрузка.Параметр связи в термическом анализе (относящийся к пластической деформации) обычно очень мал в задачах сварки, и им можно пренебречь. Более того, влияние поля деформации на тепловые граничные условия считается здесь несущественным, поскольку маловероятно возникновение больших деформаций там, где эти граничные условия находятся.
Коммерческое программное обеспечение ABAQUS версии 6.14.2 использовалось в моделировании КЭ с использованием формулы большого смещения и большой деформации. Линейные кирпичные элементы DC3D8 (термический) и C3D8R (механический) использовались для рельса, тогда как линейные тетраэдрические элементы DC3D4 (термический) и C3D4 (механический) использовались для металлической части сварного шва.Обратите внимание, что в металлической части сварного шва использовались кирпичные элементы, поперечное сечение термитов которых соответствует поперечному сечению рельса. Сетка уточняется в области металла сварного шва и рядом с концом рельса. Одна и та же сетка используется как для теплового, так и для механического полей. Всего было использовано 282 824 элемента, что дало 643 539 степеней свободы, на основе исследования сходимости для более простой двумерной модели.
На рисунке 5 показаны различные этапы обычного процесса ATW, смоделированные с помощью ABAQUS.Из-за добавления нового материала на этапе заливки процесс пришлось разделить на три различных моделирования, а результаты перенести между моделированиями с помощью опции импорта в ABAQUS. Тем не менее, можно отметить, что в термическом FEA моделирование заливки и сдвига / охлаждения объединено в одно моделирование. В случае дополнительной поковки, см. Рис. 2, дополнительное заданное смещение применяется в третьем анализе сдвига и охлаждения.
Рис. 5Процедура моделирования FE для обычного ATW
Этап предварительного нагрева и выпуска газа
На первом этапе кислородно-пропановая горелка помещается над головкой рельса во время начальной фазы ATW для сушки и очистки формы и рельса для уменьшения риска образования газовых пор внутри сварного шва и снижения скорости охлаждения.Это моделируется заданием теплового потока к свободным поверхностям рельса внутри сварного зазора в течение периода времени 180 с (3 мин). Процедура соответствует экспериментам Бэнтона [20], в которых температуры регистрировались в разных местах поверхности рельса, в 10 мм от конца рельса, на головке рельса (беговая поверхность, поверхность поля), перемычке (рыболовные поверхности и центральная перемычка), и стопа.
Энергия, подводимая горелкой для предварительного нагрева, моделируется как два распределенных тепловых потока, которые действуют на границу раздела рельсов и беговую поверхность.Предполагается, что эти потоки изменяются в зависимости от времени, высоты и ширины рельса. Они были определены путем вычисления разницы между экспериментальными температурами по Бантону [20] и расчетными температурами FE в соответствующих точках. Эта разница минимизируется с помощью аппроксимации методом наименьших квадратов (функция fminsearch в MATLAB). Во время периода выпуска, который составляет около 55 с (1 мин), тепловой поток прекращается, и рельс охлаждается, пока тигель прикреплен к верхней части формы.
На этапах предварительного нагрева и выпуска металлический шов включается для анализа, чтобы он соответствовал последующим расчетам, и для задания граничных условий горизонтальной симметрии на этом этапе, чтобы предотвратить движение твердого тела.Металл сварного шва является бесшумным материалом, т. Е. Ему придается очень низкая жесткость и предел текучести, чтобы гарантировать, что он не влияет на поведение рельса, пока он не будет активирован на стадии разливки.
Этап заливки
На этом этапе температура металла сварного шва повышается за 1 с до 750 ° C, что является температурой конца рельса в конце этапа предварительного нагрева и нарезания резьбы. Вылив жидкости моделируется увеличением температуры металла сварного шва до пространственного распределения, допустимого после завершения заливки.Расплавленный металлический материал сварного шва имеет температуру около 2050 ° C в тигле над формой, но охлаждается, оставаясь жидкостью, когда стекает вниз в каналы формы, а затем вверх в зазор сварного шва. Здесь это пространственное изменение температуры в момент заливки было предписано следовать расчетному пространственному изменению в Тучковой [22]. Обратите внимание, что это означает, что предполагается, что разливка произойдет за очень короткое время, и что весь столб металла сварного шва рассматривается с начала этого шага.На этом этапе параметры материала металла сварного шва изменяются на параметры материала рельса. Чтобы предотвратить значительное объемное расширение при непрерывном повышении температуры металла шва, на этом этапе тепловое расширение металла шва устанавливается равным нулю.
Этап резки и охлаждения
По завершении этапа разливки металл рельса и сварного шва остынет. Термическая деформация металла шва сбрасывается, см. Уравнение. (3) для моделирования того, что теперь он охлаждается из расплавленного состояния.Это также относится к частям конца рельса, которые плавятся во время разливки. Через некоторое время излишки материала удаляются гидравлическими ножницами. Это моделируется удалением элементов, моделирующих металл шва, см. Рис. 3, и переопределением свободных поверхностей для конвективных граничных условий и продолжением процесса охлаждения. Предполагается, что сдвиг как таковой не создает дополнительных напряжений. В случае использования дополнительного давления ковки модуль ALFONS с заданным смещением 6 мм прикладывается к стенке рельса на определенном расстоянии от конца рельса, см. Рис.2, 120 с (2 мин) после завершения заливки. Еще через 30 с (2 мин и 30 с) смещение деактивируется.
Термический анализ процесса ATW: результаты
Расчетные температуры FE и зарегистрированные температуры, предоставленные Banton [20] в рассматриваемых точках данных на стадиях предварительного нагрева и выпуска, показаны на рис. 6. Показано время, когда предварительный нагрев заканчивается. на рис. 6. Этот результат показывает, что модель подводимой энергии достаточно точна при моделировании воздействия горелки предварительного нагрева в большинстве рассматриваемых точек.Также обратите внимание на большую разницу в максимальных температурах беговой поверхности и поверхности поля.
Рис. 6Расчетные и измеренные температуры в рельсе на расстоянии 10 мм от конца рельса на этапах предварительного нагрева и нарезания резьбы. Указывается время, когда предварительный нагрев прекращается, 180 с (3 мин).
Для фазы разливки температура металла сварного шва и материала на конце рельса повышается до значения, показанного на рис. 7a, в качестве начального условия. После этого тепловое граничное условие деактивируется, и возможна передача тепла между различными секциями, что приводит к более физическому распределению тепла, сравнимому с расчетным с использованием CFD Тучковой [22].На рисунке 7b показано распределение температуры через 17,5 с (0,3 мин) после деактивации граничных условий. На рисунке 7c показано температурное поле после того, как материал остынет в течение значительного периода времени (почти при комнатной температуре).
Рис. 7Расчетное распределение температуры в начале заливки ( a ), 17,5 с после заливки ( b ) и через несколько минут после заливки ( c )
На рисунке 8 показаны расчетные температуры в различных точках 10 мм от конца рельса по сравнению с температурами, измеренными в экспериментах Бантона [20].Время срезания лишнего материала показано на рис. 8. В целом достигается хорошее согласие с экспериментальными результатами. Обратите внимание, что эффект сдвига материала внутри формы можно увидеть в узлах рабочей поверхности и поверхности поля. По мере удаления материала эти узлы подвергаются прямому воздействию окружающего воздуха, что приводит к увеличению скорости охлаждения.
Рис. 8Расчетные и измеренные температуры в рельсе на расстоянии 10 мм от конца рельса во время охлаждения после заливки
Механический анализ процесса ATW: результаты
Развитие деформаций и напряжений моделировалось в соответствии с шагами, описанными выше, см. Рис. .5. На рис. 9 показаны рассчитанные вертикальное (S22) и продольное (S33) напряжения в рельсе и металле сварного шва сразу после заливки, т. Е. Когда металл сварного шва был наплавлен и все еще находится в расплавленном состоянии (но рассматривается как твердое тело с очень низкие напряжения). Можно отметить, что после нарезания резьбы конец рельса покрывается формой, которая не видна на рис. 9 (но моделируется с изолирующим эффектом, см. Выше). Хотя градиент температуры от расплавленного металла сварного шва к рельсу велик, эта часть будет иметь температуру достаточно низкую, чтобы испытывать более высокие уровни напряжения, что также наблюдается в частях, находящихся дальше от формы, выше, где температура составляет около 700 ° C.Следовательно, уровни напряжения могут быть высокими и не ограничиваться очень низкими значениями предела текучести.
Рис. 9Расчетные вертикальные S22 (слева) и продольные S33 (справа) напряжения (МПа) в рельсе и металле шва сразу после заливки
На рисунке 10 показана эволюция вертикального S22 и продольного S33 компоненты напряжения со временем в разных местах для обычного процесса ATW и для процесса ATW с применением дополнительной ковки (модуль ALFONS).Графики начинаются с начала ковки, т. Е. Через 120 с (2 мин) после заливки, и длится до конца охлаждения. Обратите внимание, что ковка заканчивается через 150 с (2 мин и 30 с). Отметим также, что напряжения на рис. 10, 11, 12 и 13 показаны для металла сварного шва в профиле рельса (UIC60), т.е. напряжения в металле сварного шва за пределами профиля, который не был срезан (см. Рис. 3 и 7c), не показаны. В целом эволюция обычных ATW и ATW с ALFONS аналогична, давая качественно одинаковые уровни остаточного напряжения.В стенке возникают большие растягивающие напряжения как в вертикальном, так и в продольном направлениях. Изменения объема во время фазовых превращений из жидкой фазы в твердую, от 12 до 18 минут, показаны как небольшие изменения напряжения, тогда как окончательное фазовое превращение аустенита в перлит приведет к большему падению напряжения как в вертикальном (S22), так и в продольном направлении. (S33) компоненты. Это падение напряжения восстанавливается во время окончательного охлаждения до комнатной температуры. Разница в уровне напряжения при использовании ALFONS аналогична для компонента поперечного напряжения (S11).Однако, поскольку S11 в целом будет иметь меньшие величины, чем S22 и S33, изменение, наблюдаемое при использовании процедуры ALFONS, будет относительно большим.
Рис. 10Расчетное развитие напряжений во времени в центре сварного шва после заливки, поковка начинается через 2 мин (120 с) после заливки и заканчивается через 2 мин 30 с (150 с). Обычный ATW, слева, и для процесса ATW с дополнительной ковкой (модуль ALFONS), справа
Рис. 11Расчетное изменение напряжения в зависимости от температуры после заливки в центре сварного шва.Традиционный ATW, слева, и для процесса ATW с дополнительной штамповкой (модуль ALFONS), справа
Рис. 12Поле расчетного остаточного напряжения (МПа) после обычного процесса ATW. S22 — вертикальный, а S33 — продольный компонент напряжения.
Рис. 13Поле расчетного остаточного напряжения (МПа) после обычного процесса ATW с добавлением дополнительной ковки (модуль ALFONS). S22 — вертикальный, а S33 — продольный компонент напряжения
На рисунке 11 показана соответствующая эволюция компонентов вертикального (S22) и продольного (S33) напряжения в разных местах теперь с понижением температуры во время охлаждения после заливки для обычного процесса ATW и для Процесс ATW с применением дополнительной ковки (модуль ALFONS).Графики начинаются с начала ковки, т. Е. Через 120 с (2 мин) после заливки, и длится до конца охлаждения. Обратите внимание, что ковка заканчивается через 150 с (2 мин 30 с). Отметим также, что окончательное фазовое превращение аустенита в перлит начинается при температуре 700 ° C и заканчивается при 660 ° C. На рис. 11 отчетливо видно падение составляющих напряжения из-за увеличения объема при этом фазовом превращении.
На рисунках 12 и 13 показано поле остаточных напряжений в рельсе и металле сварного шва после охлаждения до комнатной температуры.Компоненты как вертикального (S22), так и продольного (S33) напряжения имеют большие значения растяжения в стенке рельса вблизи металла сварного шва, а компонента продольного напряжения также в металле сварного шва стенки рельса. Введение процедуры ALFONS не приведет к значительному изменению поля остаточных напряжений, хотя ширина растягивающей зоны вертикального напряжения (S22), похоже, несколько уменьшится. Компонент поперечного напряжения (S11) не показан, поскольку он имеет более низкие значения, чем два других компонента напряжения.Однако компонент поперечного напряжения (S11) имеет высокое значение внутри рельса при переходе от стенки к основанию, возможно, из-за плохого зацепления в этом пересечении. Однако это не влияет на вертикальные и продольные напряжения. Разница в остаточном поперечном напряжении (S11) после использования дополнительной ковки (модуль ALFONS) также незначительна.
На рисунке 14 показано изменение составляющих остаточного напряжения по толщине в средней плоскости рельса на центральной линии сварного шва и на расстоянии 50 мм от центральной линии сварного шва (т.е.э., в рельс). Как видно также выше, при дополнительной ковке в этих местах наблюдаются лишь незначительные изменения остаточного напряжения; самые большие различия наблюдаются в центре сварного шва на стыке перемычки нижней головки рельса. Также в средней плоскости рельса обнаруживаются большие растягивающие вертикальные и продольные остаточные напряжения в стенке в центре сварного шва и в рельсе вблизи металла шва. Это область, где часто возникают трещины. Для продольного напряжения (S33) растягивающие остаточные напряжения в стенке уравновешиваются сжимающими напряжениями на беговой поверхности и у подошвы рельса.Поперечное напряжение (S11) имеет более низкие значения, за исключением, возможно, области верхней стенки нижней головки рельса. S11 также изменяется на положительное значение на беговой поверхности, если используется ALFONS. Возможно, это связано с большими поперечными пластическими деформациями, возникающими при ковке.
Рис. 14Расчетное изменение остаточного напряжения в средней плоскости рельса в центре сварного шва (слева) и на расстоянии 50 мм от центральной линии шва (справа). S 11 — поперечное, S 22 — вертикальное и S 33 — продольное напряжение
Рассчитанное поле остаточных напряжений можно сравнить с экспериментально определенными полями остаточных напряжений для термитных сварных швов из Webster et al.[7] (с использованием нейтронографии) и частично Jezzini-Aouad et al. [8] (дифракция рентгеновских лучей) и Маттона и Солейлемана [9] (с использованием тензодатчиков). Наблюдается хорошее согласие с этими ссылками, подтверждающее наличие высоких вертикальных напряжений в стенке и нижней головке рельса и сжимающих продольных напряжений в головке рельса. Как обсуждалось выше, FBW включает шаги, аналогичные шагам в ATW, поэтому поле остаточных напряжений будет аналогичным, что видно в численных и экспериментальных исследованиях [10,11,12,13].
Риск образования горячих трещин
При использовании модуля ALFONS к охлаждающему металлу шва и рельсам сразу после заливки (1–3 мин), то есть когда материал еще очень теплый, прилагается давление ковки. Заданное смещение соответствует средней деформации около 1,3%. Это приведет к проталкиванию материала в металл сварного шва, что приведет к большим пластическим деформациям в этой области. Существует опасение, что риск образования горячих трещин, то есть трещин, образовавшихся во время окончательного затвердевания, увеличивается.При таких высоких температурах, когда материал только что затвердел, сведения о поведении материала ограничены. Также скорость охлаждения высокая. Существует несколько предлагаемых способов механической количественной оценки этого эффекта сварки, вызванного металлургией материала. Одной мерой этого риска горячего растрескивания является изменение механической деформации, то есть сумма упругой и пластической деформации, между двумя температурами, например, от 1450 ° C до 1350 ° C, см. [25, 26]. На рисунке 15 показано расчетное изменение максимальной основной механической деформации во время охлаждения между двумя температурами, 1450 ° C и 1350 ° C для случая дополнительной ковки, начинающейся через 120 с (2 мин) после заливки и продолжающейся еще 180 с (3 мин. ) с заданным смещением в 6 мм влево и в соответствующей ситуации при обычном ATW (справа).
Рис. 15Расчетное изменение максимальной основной механической деформации между температурами 1450 ° C и 1350 ° C после ATW с дополнительной ковкой (слева) и после обычного ATW (справа)
Видно, что эта мера дает значения растяжения в верхняя часть стенки и нижняя часть головки рельса с нанесенной дополнительной поковкой. Следовательно, верхняя часть поперечного сечения рельса, головка рельса и верхняя часть стенки кажутся чувствительными к горячим трещинам. Горячие трещины были обнаружены в нескольких испытанных сварных швах на ГТГ в этом месте для выбранной комбинации смещения ковки и времени ковки.Было также обнаружено, что ковка раньше или позже, чем предполагаемые 120 с (2 мин) после заливки, приводила соответственно к несколько более низким или более высоким пластическим деформациям. Можно отметить (см. Рис. 10), что во время приложения давления ковки в области стенки возникает небольшое вертикальное напряжение растяжения. Однако напряжения не используются в качестве меры для образования трещин, они также являются более неопределенной мерой из-за ограниченных знаний о поведении материала при температурах выше 1000 ° C. Можно также сказать, что горячие трещины не появлялись при выполнении обычного ATW, как ожидалось.
Микроструктура и твердость сварного шва и ЗТВ
Микроструктуру рельса после охлаждения можно оценить по расчетным скоростям охлаждения, показанным на Рис. 8, и диаграмме CCT, показанной на Рис. 16. Диаграмма CCT была построена JMatPro на основе от химического состава стали марки R260 в таблице 1. Было обнаружено, что микроструктура в рассматриваемых точках будет полностью перлитной. Сварной шов рельса и ЗТВ некоторых сварных швов также были исследованы металлографическим методом для подтверждения предсказанной микроструктуры.На рисунке 17 представлены изображения микроструктуры сварного шва с оптической микроскопии от центральной линии сварного шва до основного материала (R260) слева направо. Он также сравнивает микроструктурный градиент, вызванный обычным процессом, с градиентом, создаваемым дополнительной ковкой. Металлографическое исследование проводилось в двух положениях, в головке рельса и в подошве, в соответствии с европейским стандартом EN 14730-01. Вкратце, процедура микроскопического исследования требует осмотра области на 3–15 мм ниже рабочей поверхности и на том же расстоянии от кончика подошвы рельса.После зеркальной полировки образцы протравливались 4% -ным раствором Nital. На всех изображениях преобладающей микроструктурой является перлитная структура, что подтверждает термический КЭ анализ. Даже при дополнительной ковке, см. Рис. 17а и b, сканирование подобластей сварного шва не показывает присутствия нежелательных фаз, таких как мартенсит или бейнит. Аналогичные микроструктуры получены в ФЗ. Он содержит перлитную фазу коричневого цвета с доэвтектоидным ферритом (белый цвет), образованным вокруг включений (черный цвет) и по границам зерен.В некоторых частях ЗТВ внутри крупных зерен также возможно образование доэвтектоидного феррита.
Рис. 16Кривые охлаждения для различных точек в поперечном сечении рельса и диаграмма CCT для стали R260 (построенная JMatPro)
Рис. 17Микроструктурный градиент, вызванный обычным ATW с дополнительной ковкой. a Головка рельса. b Опора рельса, обычная ATW. c Головка рельса. d Подножка рельса.
Помимо перлитной структуры на рис.17 также иллюстрирует микроструктурный градиент, создаваемый теплом во время сварки. В районе, ближайшем к СЗ, наблюдается быстрое и сильное повышение температуры. Это приводит к росту зерна и образованию после охлаждения подобласти зоны термического влияния крупных зерен. Вдали от ЗТВ процесс перекристаллизации способствует заметному уменьшению размеров зерен, образуя подобласть второй зоны ЗТВ. Присутствие металлургических подобластей в ЗТВ влияет на распределение твердости.
Измерение твердости сварного шва
На рисунке 18 показано среднее распределение твердости в головке, стенке и подошве сварных швов, изготовленных традиционным ATW и с дополнительной ковкой (модуль ALFONS), соответственно.Средние значения рассчитываются по трем сварным швам каждого процесса. Для обычных сварных швов, показанных для справки на рис. 18а, среднее значение показывает, что высокая твердость в стенке и подошве рельса расположена на одинаковом расстоянии от центра сварного шва. Для сравнения, зона высокой твердости головки рельса немного смещена, что приводит к большей ЗТВ.
Рис. 18Распределение продольной твердости в головке, стенке и подошве рельсов в зависимости от процесса сварки. a Обычные сварные швы ATW. b Технологические швы ALFONS (с дополнительной поковкой)
Что касается дополнительной поковки (модуль ALFONS), профили твердости имеют асимметричное распределение. Кажется, что твердость увеличивается с левой стороны на правую на рис. 18b. Кроме того, подошва рельса имеет самую низкую твердость по сравнению с перемычкой и головкой. Это противоречит эталонному результату сварки, см. Рис. 18a. Можно отметить, что несимметричные профили наблюдаются и в отдельных швах, выполненных с дополнительной ковкой.Причина этого асимметричного профиля неясна. Могут быть различия в процедуре применения предписанных смещений в головке рельса, то есть в расположении цилиндров, создающих предписанное смещение, и в устойчивости всей машины во время ковки, что может привести к асимметричному изменению твердости.
Ширина зоны термического влияния
Ширина ЗТВ является важной мерой в проекте WRIST [19], поскольку уменьшение ширины ЗТВ и ЗТВ является основной целью проекта.Основываясь на измерениях твердости выше, ширину ЗТВ можно оценить в соответствии с европейским стандартом 14370-01. На рисунке 19 показана взаимосвязь между градиентом микроструктуры и изменением твердости на одной стороне термитного шва, от FZ до основного материала. Обычно наплавленный металл и основные материалы имеют почти одинаковую твердость. Изменение твердости происходит в ЗТВ. Согласно европейскому стандарту длина зоны низкой твердости не должна превышать 20 мм, известной как зона размягчения при нагревании.Сварной шов рельса, рис. 19, имеет смягченную ширину около 16 мм. Общая длина HAZ является суммой ширины низкой твердости (LH) и высокой твердости (HH), что дает общую длину около 33 мм для обоих случаев, обычного ATW или при использовании ALFONS.
Рис. 19Взаимосвязь между металлургическим градиентом и изменением твердости в термитном шве
Ширина зоны FZ + HAZ также была оценена на основе моделирования методом КЭ. Затем была определена ЗТВ для узлов, температура которых превысила эвтектоидную точку 723 ° C в любой момент во время процесса сварки, вместо использования определения, основанного на твердости.На рисунке 20 показаны места, где была рассчитана ширина.
Рис.20Измерения ширины FZ и HAZ, использованные при моделировании FE и в таблицах 2 и 3
Таблица 2 дает приблизительную ширину FZ и HAZ для обычных ATW и ATW с ALFONS (с общей смещение 12 мм). Как упоминалось выше, во время ковки в металл сварного шва (FZ) будут возникать большие пластические деформации. Во время дальнейшего охлаждения в металл сварного шва и рельс вблизи сварного шва будут возникать дополнительные пластические деформации.После охлаждения будут возникать большие остаточные пластические деформации в центре сварного шва (растяжение в поперечном и сжатие в продольном направлении) и на границе раздела для сварки металлических колонн в кристаллизаторе (позже срезанных). Результирующее уменьшение ширины FZ будет примерно на 6%, 1 мм, (небольшое), когда будет введен ALFONS. Также видно, что ЗТВ незначительно уменьшается. Поскольку ширина ЗТВ в рельсе в основном определяется подводимым теплом, как и при использовании ALFONS, эта разница для ЗТВ обусловлена пластической деформацией материала рельса во время ковки.В Таблицу 2 также включена оценка соответствующей ширины ЗТВ на основе измеренных профилей твердости. Основа для сравнения несколько отличается, поскольку сварной зазор, использованный при моделировании КЭ, составлял 25 мм, см. Рис. 2, в то время как сварной зазор, использованный для сварных швов (полученных на более позднем этапе), исследованных на рис. 18 и 19 было 50 мм. Из измеренных профилей твердости также видно, что использование дополнительной поковки может дать несколько меньшую ширину ЗТВ. Похоже, так оно и было, если были изменены условия дополнительной ковки, т.е.е. время начала ковки, продолжительность дополнительной ковки и величина заданного смещения. Различие между экспериментами и моделированием КЭ можно также объяснить неконтролируемым изменением расстояния поковки во время сварки. Компания GTG сообщила об отклонении от 6 до 9 мм в случае условий сварки в полевых условиях. Этот факт также является причиной отклонений по сравнению с продольным профилем твердости вдоль сварного шва.
Таблица 2 Сравнение ширины FZ и HAZ с использованием обычного ATW или ATW с дополнительной поковкойШирину HAZ, смоделированную FE, также можно сравнить с экспериментальными результатами из литературы, Chen et al.[2], где обычный ATW проводился с использованием разного времени предварительного нагрева. В таблице 3 показано это сравнение, описанное здесь как FZ и HAZ. Обратите внимание, что здесь использовалось то же определение HAZ, то есть точки, которые испытали температуру, превышающую 723 ° C, определены как находящиеся в HAZ. Моделирование FE достигает значений ширины, которые находятся в верхнем пределе экспериментального диапазона, особенно в центре полотна и области перехода от полотна к опоре. При рассмотрении смещения поковки на 12 мм уменьшение ширины зоны FZ + HAZ в этом случае составляет примерно половину, т.е.е., 6 мм. Отметим, что ширина ЗТВ определяется подводимой теплотой и не связана напрямую с дополнительной поковкой; однако материал, который станет ЗТВ, возможно, был пластически деформирован во время ковки. Согласие с Chen et al. [2] достаточно хорош, учитывая некоторые различия в процедуре термитной сварки, использованной в Chen et al. [2] и в проекте WRIST [19].
Таблица 3 Сравнение ширины FZ + HAZ с экспериментами, выполненными Chen et al. [2]Обучение сварщиков железнодорожных путей алюмотермической сварке
EUROJOIN 6, Сантьяго-де-Компостела, Испания, 28-30 июня 2006 г.
Сводка
1 октября 2004 г. стартовал европейский проект RAILSAFE.Целью проекта является гармонизация обучения, подготовки, квалификации и сертификации сварщиков железнодорожных путей в области алюмотермической сварки в Европе.
В 5 странах были проведены семинары по формулированию требований к алюминотермическим сварщикам и по согласованному обучению и обучению.
В этом документе рассказывается, как можно решить существующие национальные и международные различия.
Введение
Что такое алюмотермическая сварка?
В процессе алюмотермической сварки расплавленная сталь заливается в форму, окружающую зазор между соединяемыми концами рельсов.Концы рельсов соединены жидким металлом. Принцип алюминотермической сварки основан на экзотермической химической реакции порошка алюминия и оксида железа с выделением тепла, достаточного для плавления.
Перед началом плавления концы рельсов обрезаются для создания заданного зазора, и рельсы выравниваются. Затем огнеупорную форму крепят вокруг зазора с помощью стальных башмаков. Утечки в формах предотвращаются специальным фиксирующим материалом. После предварительного нагрева обоих рельсов начинается экзотермическая реакция порошка алюминия и оксида железа в повторно используемом или «одноразовом» тигле, и жидкий металл течет в форму.Металл заполняет изложницу, и шлак выгружается в шлаковые чаши. После периода охлаждения излишки металла в головке рельса удаляются, и можно начинать шлифование рельса.
Поскольку сварка довольно часто проводится на действующих путях, скорость сварки и безопасность сварщиков являются важными аспектами сварки на железнодорожных путях.
Почему RAILSAFE?
Безопасность железнодорожного движения во многом зависит от качества путей, сварных швов на путях и, следовательно, от навыков сварщика.Во всей Европе наблюдается отсутствие единообразия в обучении и тестировании алюмотермических сварщиков, отсутствие общих учебных программ и отсутствие мобильности квалифицированных сварщиков. Это верно не только между странами, но и внутри некоторых стран. Направление сварщиков для работы в других компаниях или в других странах часто затрудняется из-за различных процедур и разной квалификации сварщиков.
Политика Европейской комиссии заключается в содействии взаимодействию между отдельными национальными железнодорожными системами и повышении безопасности.(См. Белую книгу ЕС: Европейская транспортная политика на 2010 год: время решать, 2001 год).
Другая политика Европейской комиссии состоит в том, чтобы стимулировать через «Программу действий Сообщества Леонардо да Винчи по профессиональному обучению» образование и обучение в рамках процесса обучения на протяжении всей жизни, чтобы улучшить возможности трудоустройства и сделать работу вне национальных границ возможной: свободное перемещение людей в Европейском Союзе.
Европейская организация по стандартизации, CEN, и в частности TC256 / SC1 / WG4, разрабатывает стандарты по процедурам сварки железнодорожных путей и по обучению сварщиков алюмотермической сварке, prEN 14730.Эти стандарты предназначены для комментариев и еще не вступили в силу.
1 октября 2004 г. стартовал трехлетний европейский проект: «Разработка гармонизированной системы обучения, квалификации и сертификации сварщиков железнодорожных путей», RAILSAFE. Проект частично финансируется программой ЕС «Программа профессионального обучения сообщества Леонардоды Винчи».
Целью проекта RAILSAFE является разработка согласованной системы обучения, квалификации и сертификации сварщиков железнодорожных путей.
Гармонизированное образование, обучение и квалификация делают возможным обмен сварщиками как внутри страны, так и в Европе. Сертификация гарантирует непрерывное профессиональное образование для получения компетенций на протяжении всей жизни. Квалификация и сертификация также обеспечивают видимую проверку компетентности сварщика в соответствии с согласованными европейскими директивами, которые признаются и принимаются соответствующими работодателями и властями по всей Европе. Таким образом можно избежать многократных или повторных испытаний сварщиков.
Результаты проекта также способствуют улучшению «взаимодействия» между национальными железнодорожными системами, более эффективному обслуживанию, сокращению времени владения путями и повышению безопасности рабочей силы, а также свободному перемещению сварщиков в ЕС.
Новые стандарты prEN 14730 служат основой для деятельности RAILSAFE, особенно стандарта по процедурам. Однако в проектах стандартов подробно не указывается уровень подготовки или компетентности сварщиков.Результаты RAILSAFE будут включать эти детали.
Ожидаемые результаты проекта:
- Отраслевые требования в отношении рабочих характеристик для алюминотермических сварщиков и согласованного обучения и подготовки.
- Руководство по обучению, обучению, квалификации и сертификации сварщиков железнодорожных путей
- База данных квалифицированных и сертифицированных сварщиков
- Пилотные курсы с экзаменом и квалификацией
- План организации эксплуатации системы
- Распространение результатов проекта в Европе
Проект выполняется 9 партнерами из 7 разных стран: подрядчиком по строительству железных дорог, консультантом по качеству и гармонизации сварки, европейской организацией, представляющей институты сварки и сами институты сварки, обладающие опытом в области образования, обучения, квалификации и сертификации сварщики.
Во время семинаров в 5 европейских странах специалисты по железнодорожным путям определили отраслевые требования к образованию и обучению сварщиков.
Требования к образованию и обучению
Мастерские
Около 50 специалистов по сварке рельсов приняли участие в семинарах в Копенгагене, Кембридже, Генуе, Ганновере и Братиславе. В нем приняли участие представители железнодорожных властей, подрядчиков, поставщиков технологических процессов, исследовательских и консультационных организаций, учебных заведений и институтов сварки.
Эксперты обсудили проекты предложений по рабочим характеристикам, процедурам технических требований к сварке, базе данных для сертифицированных сварщиков и структуре для работы согласованной системы.
Из — иногда противоречивых — комментариев были получены следующие результаты, которые снова являются предметом обсуждения среди участников семинара.
Структура обучения, повышения квалификации, квалификации и сертификации
Гармонизированная система предусматривает теоретическое обучение и практическую подготовку алюмотермических сварщиков, их экзамен, выдачу Диплома, действительного в течение всего срока действия владельца, и Сертификатов с ограниченным сроком действия.
Квалификация, в результате которой выдается диплом, требует теоретического образования, практической подготовки, а также теоретических и практических экзаменов.
Для сертификациитребуется квалификация, указанная выше, плюс удовлетворительный опыт сварки гусениц.
Теоретическое образование и экзамен на получение диплома являются общими, а практическая подготовка и экзамен на получение диплома зависят от конкретного процесса. После сдачи экзаменов сварщик получит общий диплом, действующий на протяжении всей жизни.
Обладатели диплома должны продемонстрировать годичный контролируемый, документально подтвержденный и удовлетворительный опыт, чтобы получить Сертификат, который зависит от процесса. Это относится к Сертификату процесса, в котором сварщик был обучен для получения Диплома, а также к дополнительным Сертификатам в других процессах. Чтобы получить сертификат в других процессах, сварщик также должен пройти практическое обучение в этом процессе.
Сертификаты действительны в течение двух лет.Чтобы продлить Сертификат еще на двухлетний период, держатели должны продемонстрировать подтвержденный документально подтвержденный и удовлетворительный опыт в процессе, за который был выдан сертификат, в течение срока действия сертификата.
Общая конструкция
Европейская организация по сварке рельсов (будет назначена или создана европейским сообществом по сварке рельсов) разрабатывает специальные правила для уполномоченных национальных органов (ANB) в каждой стране, которая желает внедрить схему обучения, квалификации и сертификации сварщиков рельсов.Эти правила потребуют от ANB создать Национальный комитет специалистов по сварке рельсов для этой деятельности с представителями национального сектора железнодорожной промышленности. Презентация этого комитета будет включать:
- железнодорожные власти
- подрядчики по сварке рельсов
- поставщики сварочного оборудования рельсов, действующие в соответствующей стране
- организации по обучению сварщиков рельсов.
Этот национальный комитет специалистов по сварке рельсов будет отвечать за реализацию схемы на национальном уровне от имени правления ANB.
ANB оценивают и утверждают утвержденные учебные органы (ATB) и уполномоченных экзаменаторов (AE) ANB.
Группа специалистов по сварке рельсов создана на европейском уровне для соблюдения согласованных руководящих принципов и правил. В эту группу будут входить железнодорожные власти, подрядчики, поставщики процессов, обучающие организации и ANB.
Рабочие характеристики
Участники семинара определили рабочие характеристики алюмотермического сварочного аппарата.Цели деятельности — это утверждения, которые определяют конкретные знания и навыки, которые человек должен получить и продемонстрировать в результате своего образования и обучения. Они описаны в терминах «ожидаемых результатов». Рабочие цели лягут в основу Руководства «Минимальные требования к образованию, обучению, квалификации и сертификации» европейского алюмотермического сварщика.
В следующей таблице представлена структура, в которой определены целевые показатели эффективности.
Также включено указание количества учебных часов.
Модуль | Подмодуль | Рекомендуемые часы обучения |
---|---|---|
I. Теоретическое образование |
| 8 24 8 |
Общий модуль I | 40 | |
II.Практические занятия |
| 64 16 |
Общий модуль II | 80 | |
Общий курс | 120 |
В следующих таблицах приведены два примера целевых показателей производительности с точки зрения ожидаемых результатов: один в модуле «Теоретическое образование», подмодуле «Материалы и их поведение во время сварки» и один в модуле «Практическое обучение», подмодуль «Алюминотермическая сварка».
Модуль I — Теоретическое образование | 40 |
I.1 Материалы и их поведение при сварке | |
I.1.1 Основы металлургии | 4 |
Ожидаемые результаты | |
|
Модуль II — Практическое обучение | 80 |
II.1.1 Алюминотермическая сварка | 64 |
Ожидаемые результаты | |
|
Сварочные процедуры
В связи с появлением стандарта prEN 14730-1 CEN многие участники семинара подумали, что документ о процедуре сварки не потребуется.
Введена форма «Спецификация практического теста» для определения обучения и проверки практической части квалификации (диплома).
База данных
База данных все еще вызывает споры. Большинство подрядных компаний и железнодорожных властей имеют базы данных для квалифицированных и сертифицированных сварщиков. Международная база данных рассматривается многими участниками семинара как крайне необходимая мгновенная общеевропейская проверка квалификации / сертификации сварщика.Однако другие считают, что такая база данных не нужна.
Поскольку база данных является продуктом проекта, RAILSAFE разработает базу данных, которая будет основана на Интернете. Данные будут предоставляться ATB и вставляться ANB.
Данные основаны на одном пожизненном дипломе и одном или нескольких сертификатах с ограниченным сроком действия, выданных сварщику, и сварщик / работодатель должен согласиться (или не согласиться) с данными, хранящимися в базе данных.
Продолжение
Принимая во внимание все отраслевые требования, в рамках проекта будет продолжена разработка Руководства по обучению, квалификации и сертификации сварщиков, Спецификации практических испытаний, базы данных квалифицированных и сертифицированных сварщиков, пилотных курсов с квалификацией и сертификацией, а также дальнейшего распространения система в Европе.
Партнеры по проекту организуют в конце 2006 г. общеевропейский семинар для обсуждения результатов проекта с экспертами по сварке железных дорог из всех европейских стран.
Наблюдения
Из обсуждений на семинаре можно сделать вывод, что RAILSAFE принесет пользу в плане мобильности и признания, а также принесет национальную и европейскую гармонизацию существующей компетенции сварщиков.
RAILSAFE добавит детали к стандартам CEN: единые цели производительности для сварщиков и руководство по образованию, обучению, квалификации и сертификации, чтобы подкрепить стандарты, и обеспечит надежную мгновенную проверку квалификации / сертификации сварщика по всей Европе по базе данных.
Механические свойства термитных сварных швов рельсов из высококачественных сплавов
Реферат
В данной статье представлены результаты исследования свойств 13 термитных сварных швов рельсов, выполненных с использованием рельсов из хромомолибденовых, хромистых и хромистых сплавов, Американская ассоциация железнодорожного машиностроения. Сообщается о рельсах с контролируемым охлаждением (т. е. стандартных рельсах) и рельсах с термической закалкой. Различные комбинации рельсов соединялись с металлом шва, полученным в результате алюмотермической реакции «стандартных» и «легированных» термитных зарядов.После сварки были определены профили твердости, свойства при растяжении, энергия удара, а также макроструктура и микроструктура сварных швов. Детальные исследования микроструктуры зон термического влияния и металлов сварного шва показали, что процесс термитной сварки позволяет получить сварные швы, совместимые с рельсовым транспортом, поскольку мартенсит никогда не наблюдался ни в одном из сварных швов, независимо от состава рельса или металла шва. состав. Несмотря на отсутствие мартенсита, очень низкие энергии удара (1.5–2,8 Дж при 293 К) были измерены на образцах Шарпи с V-образным надрезом, снятых с металлов шва. Металлы сварного шва также показали уменьшение площади пластичности при растяжении только на 2–6%. Как и следовало ожидать, все поверхности излома металла шва имели транскристаллический скол хрупкого типа. Также было показано, что легированный металл шва тверже и прочнее, чем стандартный металл шва. В зависимости от времени предварительного нагрева твердость сплава металла шва по шкале С по Роквеллу составляет примерно 28–34 HRC, тогда как твердость стандартного металла шва составляет 20–27 HRC.Соответственно, предел прочности и предел текучести легированного металла шва были примерно на 100–150 МПа выше, чем у стандартного металла шва. Также были изучены свойства и структура образцов, которые находились в области минимальной твердости по внешнему краю зоны термического влияния.
Рекомендуемые статьиЦитирующие статьи (0)
Полный текстCopyright © 1984 Издано Elsevier B.V.
Рекомендуемые статьи
Цитирование статей
[IRFCA] Термитная (алюминотермическая) сварка рельсовых соединений
, автор — Раджив Шривастава
Это описание сварки на месте стыков рельсов с использованием термитной или алюмотермической сварки.В этом процессе сильно экзотермическая реакция между оксидами алюминия и железа приводит к получению жидкой стали, которая заливается в форму вокруг свариваемого зазора. Перегретый расплавленный металл вызывает плавление рельсов по краям свариваемого зазора, и он также является присадочным металлом, так что материал рельсов сливается с добавленной расплавленной сталью и соединяется с ней по мере ее затвердевания, образуя сварной шов. Термит — это торговое название одной из используемых гранулированных смесей металлического алюминия и порошкового оксида железа (также известного как термит ).Зажигание термитов обычно осуществляется путем зажигания магниевой ленты или бенгальского огня. Дополнительная информация ниже.
Методики алюмотермической сварки:
- Рельсы обрезаны под квадрат, а зазор под сварку подготовлен в заданных пределах 1 . (Если концы рельсов обрезаны с перекосом, зазор будет неравномерным, а сплавление рельсов будет асимметричным.)
- Обрезанные поверхности очищают керосиновым маслом и металлической щеткой для удаления ржавчины, пыли, жирных материалов и т. Д.(В противном случае этот материал может сплавиться со сварочным материалом, что может привести к дефекту сварного шва.)
- Стальная линейка длиной 1 м используется для выравнивания рабочей кромки 2 головки рельса. Концы рельсов имеют «остроконечные» формы для компенсации усадки во время затвердевания и охлаждения стали «Thermit». Если не выполнить «подъем» рельсов, соединение будет провисать из-за дифференциального охлаждения головки рельса (где доступно больше материала и, следовательно, охлаждение медленнее) и подошвы рельса после охлаждения.Провисание сустава ухудшает езду и становится проблемой при техническом обслуживании. Такое соединение будет подвергаться большим нагрузкам из-за динамического увеличения. Для бокового и вертикального выравнивания используются клинья.
- Подставки для тигля и горелки закрепляются на головке рельса в соответствующих местах, на противоположных сторонах сварочного зазора и положения, а высота стойки горелки проверяется и регулируется путем размещения на ней горелки предварительного нагрева или сварочной горелки, которую затем снимают. и отложите для дальнейшего использования.
- Выбирается набор готовых форм соответствующего сечения рельса и проверяется на пригодность 3 . Профиль рельса формы проверяется 4 путем размещения формы напротив свариваемой стороны рельса. При необходимости можно внести небольшие изменения в профиль пресс-формы, осторожно потерев пресс-форму о боковые стороны рельса. Затем формы помещают в башмак формы (т. Е. Зажим), правильно устанавливая его с помощью замазывающего песка. Форма должна располагаться по центру над зазором, иначе при заливке расплавленного металла один конец рельса будет получать больше тепла, чем другой, и сплавление металла на другом конце рельса может быть неполным.Выемка, если таковая имеется, между формой и профилем рельса заделывается цементным песком. Чаша для шлака прикреплена к башмаку кристаллизатора для сбора переливающегося шлака и расплавленного металла во время разливки.
- Тигель с магнезитовыми линиями установлен на поворотной подставке для тигля на правильной высоте и соосно. Закрывающий штифт помещается внизу над проемом. Головка этой булавки покрыта примерно 5 г асбестового порошка, поэтому он не плавится при контакте с расплавленным металлом, и происходит «автоматическое постукивание».
- Тигель отодвигается от рельса, и «порция» (самовоспламеняющаяся смесь, которая дает расплавленный металл) заливается в тигель с горкой конической формы.
- При использовании сжиженного нефтяного газа (баллоны для коммерческого использования) и кислорода (или бензина и сжатого воздуха, устаревшая технология, но все еще используемая) зажигается горелка предварительного нагрева или сварочная горелка и регулируется пламя. Эта горелка помещается на подставку, которая закреплена над зазором, и пламя направляется в форму через центральное отверстие.Пламя нагревает концы рельса, и это происходит в течение определенного времени для каждой секции рельса и используемых газов предварительного нагрева.
- Когда предварительный нагрев завершен, реакция Thermit инициируется путем зажигания бенгальского огня и помещения его в тигель. Реакции дают определенное время, и позволяют отделить шлак от расплавленного металла. После этого закрывающий штифт постукивается снаружи, таким образом выгружая металл в верхнюю центральную полость формы.После этого тигель и подставки для горелки снимаются.
- Избыток стали Thermit над головкой рельса (верхний подступенок) удаляется после затвердевания (но когда металл все еще раскален докрасна) либо ручным долблением, либо с помощью гидравлических сварочных триммеров.
- Остающийся огнеупорный материал удаляется, а стальные вентиляционные стояки, прикрепленные к воротнику основания сварного шва, отламываются.
- Клинья и т. Д. Удаляются, все снятые крепления снова фиксируются, а головка рельса шлифуется вручную или на шлифовальных станках.
Время для каждого действия | ||||||||
---|---|---|---|---|---|---|---|---|
Номинальный зазор | Зазор 25 мм | Зазор 50 мм | Зазор 75 мм | |||||
Ширина зазора | 251 мм | 501 мм | Вес | 501 мм | 75 кг) | 10,8 | 13,5 | 22,0 |
Вертикальное выравнивание, с обеих сторон 1-метровой линейки | 1,0-1,25 мм в высоту | 1.25-1,50 мм в высоту | 2,5-3,0 мм в высоту | |||||
Боковое выравнивание (со стороны манометра) на конце 1-метровой линейки | 0-0 | 0-0 | 0-0 | |||||
Время нагрева с бензин и сжатый воздух под давлением 7-7,7 кг / см, 100-110 фунтов на кв. дюйм 2 (минут) | 10-12 | 18-20 | 20-25 | |||||
Время нагрева сжиженным нефтяным газом при 2,0-2,5 кг / см 2 и O 2 при 7-8 кг / см 2 (минут) | 2.0-2,5 | 2,5-3,0 | 3,0-4,0 | |||||
Время реакции (секунды) | 203 | 203 | 255 | |||||
Время ожидания пресс-формы (минуты) | 4-5 | 6- 7 | 10-12 | |||||
Время выкрашивания — вручную (минуты) | 4 | 5-6 | 8-9 | |||||
Время выкрашивания — подстроечный резистор (минуты) | 0,5-1 | 0,5 -1 | 0,5-2 | |||||
Время прохождения поезда после заливки (минуты) | 30 | 30 | 30 | |||||
Вертикальный допуск готового сварного шва | 0.4 мм в центре 10-сантиметровой линейки | 0,4 мм в центре 10-сантиметровой линейки | 0,4 мм в центре 10-сантиметровой линейки | |||||
Боковой допуск для готового шва | 0-0,3 мм в центре 10-сантиметровой линейки | 0-0,3 мм в центре 10-сантиметровой линейки | 0-0,3 мм в центре 10-сантиметровой линейки |
Такая сварка выполняется при типичном пробке в 55 минут. После сварки сварной шов покрывают специальными пластинами с выступами и зажимами до тех пор, пока сварной шов не будет проверен на ультразвуковых машинах для проверки рельсов и будет признан «хорошим».Воротник сварного шва окрашен антикоррозийной краской, поскольку выступ, как известно, собирает капающие отходы из открытых сливных туалетов поездов и вызывает коррозию на стыке стенки рельса и втулки.
Сноски
1. 1 мм для сварки с зазором 25 мм, 50 мм или 75 мм
2. Верхняя и измерительная поверхность, где шина колеса соприкасается с фланцем.
3. На нем не должно быть трещин, износа и т. Д.
4. Иногда из-за износа головки рельса между формой и профилем рельса остаются зазоры, которые необходимо заделать замазочным песком.
Детали реакции Термита Алюминий реагирует с оксидами железа, особенно с оксидом железа, в сильно экзотермических реакциях, восстанавливая оксиды железа до свободного железа и образуя шлак оксида алюминия.
3Fe 3 O 4 + 8Al = 4Al 2 O 3 + 9Fe (3088 ° C, 719.3ккал ↑)
3FeO + 2Al ⇒ Al 2 O 3 + 3Fe (2500 ° C, 187,1 ккал ↑)
Fe 2 O 3 + 2Al ⇒ Al 2 O 3 + 2Fe (2960 ° C, 181,5 ккал ↑)
Различные оксиды железа используются в соответствующих пропорциях, чтобы получить правильное количество и температуру расплавленной стали. Приблизительно равные количества расплавленной стали и жидкого оксида алюминия разделяются при температуре около 2400 ° C после нескольких секунд экзотермической реакции.Железо, полученное в результате такой реакции, является мягким и непригодным для использования в качестве сварочного металла для соединения рельсов. Чтобы получить сплав правильного состава, сплавы, такие как ферромарганец, добавляются к смеси вместе с кусками мягкой стали, как в виде мелких частиц, чтобы обеспечить быстрое растворение в расплавленном чугуне, чтобы контролировать температуру и увеличить металл. восстановление’. Полное отделение шлака за короткое время и лучшая текучесть расплавленного металла достигается за счет добавления таких соединений, как карбонат кальция, плавиковый шпат и т. Д.
Предварительный нагрев концов рельсов (примерно до 1000 ° C) необходим, чтобы помочь разлитому расплавленному металлу смыть поверхностное окисление на концах рельсов, так как в противном случае расплавленный металл может охладиться и затвердеть сразу же при контакте с холодом. концы рельсов, не смывая окисления поверхности.
Процедура «контролируемой локальной реакции» для удержания под контролем воспламенения термитной смеси была изобретена доктором Гольдшмидтом, и поэтому этот процесс иногда также называют процессом Гольдшмидта.Индивидуально запатентованные процессы привели к появлению различных торговых наименований, таких как «Thermit», «Boutte», «Argothem» и т. Д.
.