Ремонт автохолодильника своими руками — поломки и их устранение
Холодильники для автомобилей используются периодически, на относительно короткое время. Однако и они ломаются, как любая техника. Причинами неисправности могут быть:
- нарушения правил эксплуатации;
- некачественные комплектующие;
- ошибки, допущенные при сборке модели.
Для облегчения задачи мы собрали наиболее распространенные признаки, свидетельствующие о нарушениях в работе автомобильных холодильников:
- Термоэлектрических.
- Компрессорных.
- Абсорбционных.
Внимательное отношение к охлаждающему оборудованию зачастую избавляет от риска столкнуться с его поломками во время поездки, позволяет своевременно проводить ремонт автохолодильника и своими руками в том числе.
Признаки неисправности автохолодильников
Принципы работы холодильного оборудования авто обуславливают причины, приводящие к неисправности. Здесь мы рассмотрим признаки наиболее распространенных поломок, свойственных автомобильным холодильникам трех типов.
Стук, дребезжание, посторонние шумы
- Электролитные реакции проходят тихо. Поэтому шумы, звуки не свойственны термоэлектрическим моделям.
- Холодильная техника с компрессором состоит из мотора, кожуха, рамы, вентилятора и других блоков. В ней предусмотрено много механических соединений. Ослабление креплений может привести к возникновению шумов. Для их устранения достаточно подтянуть болты. Дребезжащие звуки появляются, если теплообменник плотно прилегает к стенке корпуса. Если крепления в порядке, проверьте положение реле относительно метки.
- Проверка надежности креплений насоса, теплообменника, емкости для хладагента помогут устранить шумы, вибрацию в конструкциях абсорбционного типа.
Охлаждение отсутствует
Вне зависимости от типа оборудования проверьте его соединение с источником тока, механизм закрывания дверцы. Причиной возникновения поломки может стать удар, падение прибора, вибрация, тряска при движении машины.
Если электропитание исправно:
- В термоэлектрических моделях проверяют:
- соблюдена ли полярность подключения источника питания;
- исправность электромотора;
- нет ли утечки хладагента.
- исправность датчика термореле;
- целостность электроцепи;
- сопротивление проводов в рабочем температурном режиме;
- мощность абсорбционного холодильника обследуют, переключая ручку датчика-реле. Если мощность при этом не меняется, значит, сгорел один из элементов нагрева аммиачного раствора. Его нужно менять.
Стальные элементы корпуса бьются током
Из-за невысокого напряжения электросети автомобиля такое случается не часто. Воздействие тока можно ощутить, когда автохолодильник подключают к сети 220-240В на даче, например. Это признак того, что есть утечка тока на корпус по причине неисправности проводки, или нарушения ее изоляции.
Без опыта и знаний ремонт автохолодильника своими руками в этом случае не возможен. Устранение поломки производится электриком со специальным тестирующим оборудованием.
Холодильник не включается
Это говорит о нарушении работы электрических цепей или поломке электродвигателя. Если нет знаний электротехники, тестера, чтобы прозвонить проводку, лучше доверить диагностику и ремонт электрику.
Быстро намерзает слой снега в морозильной камере
Это свойственно компрессорным, абсорбционным моделям, оборудованным морозильными камерами, создающим температуру охлаждения ниже нуля. Признак свидетельствует о нарушениях:
- уплотнительных элементов дверцы;
- в работе запорных механизмов;
- при закрывании двери;
- требований эксплуатации техники. Нельзя хранить жидкости в открытых емкостях, горячую пищу.
Если есть щели между дверцей и корпусом, их необходимо ликвидировать. Неисправность можно устранить заменой уплотнителя, ремонтом замков, проверкой плотности прилегания.
Появление запахов, вкус продуктов портится
Причина этого кроется в небрежности владельцев. Автохолодильник, как любая охлаждающая техника, нуждается в уходе. Требуется:
- его размораживать, мыть;
- хранить упакованные продукты;
- открывать дверцу, когда агрегат не работает, не используется.
Утечка хладагента
Может стать причиной, если в автохолодильнике:
- не снижается температура;
- мотор работает без отключения;
- не включается компрессор;
- обледенел испаритель;
- видны следы утечки.
Эта неисправность свойственна моделям компрессорного и абсорбционного типа. Провести ремонт автохолодильника своими руками при утечке сложно. Опасность разгерметизации охлаждающей системы, выделения вредных испарений аммиака, фреона требует проводить ремонт в заводских условиях, с применением специализированного оборудования.
Автохолодильник “Mobicool”, устройство, ремонт. — Радиомастер инфо
Эта модель AC/DC, значит она предусматривает работу от сети 220 В и от прикуривателя автомобиля. Автохолодильник использовался при работе от сети и перестал работать.
Рассмотрим из чего состоит автохолодильник. Устройство его довольно простое. Это термоящик с установленным в верхней части охлаждающим устройством, выполненном на модулях Пельтье. Модули Пельтье состоят из последовательно соединенных полупроводниковых p-n переходов, расположенных между двумя керамическими пластинами. На рисунке ниже показано устройство модуля Пельтье. ТЭЭ – это термоэлектрический элемент р-типа или n-типа.
При пропускании прямого тока одна пластина модуля нагревается, а другая охлаждается. Вот как выглядит реальный модуль Пельтье.
Этот же модуль Пельтье обладает обратным эффектом. При нагревании одной его стороны и охлаждении другой он выдает напряжение. Этот эффект называется эффектом Зеебека. Но кпд при этом довольно низкий.
Конечно, автохолодильник на модулях Пельтье не заморозит содержимое при положительных температурах окружающей среды. Согласно паспортных данных он способен создать температуру внутри ящика максимум на 180С ниже температуры вне ящика, но и это существенно продлит время хранения продуктов.
Принцип работы ясен. Вернемся к нашему холодильнику. Вот как выглядит охлаждающий модуль сверху:
И снизу:
Открываем крышку и осматриваем элементы схемы. Видимых повреждений нет.
Как было сказано выше от сети 220 В автохолодильник не работает. Проверяем его работу от 12 В. Работает нормально. Значит модули Пельтье и вентиляторы исправны. Проверяем блок питания, который из 220 В формирует напряжение 12 В.
На него сетевое напряжение приходит.
На выходе отсутствует.
Блок питания не работает. Проверяем прохождение напряжения 220 В по схеме блока питания и обнаруживаем, что оно не поступает на диодный мост. Выключаем из сети и проверяем предохранитель. Он в обрыве.
Проверяем сопротивление нагрузки после предохранителя на предмет короткого замыкания. Все в норме. Есть потемневший диод в мостике, но звонится нормально. Возможно предохранитель сгорел от скачка напряжения. Для повышения надежности можно заменить пару сомнительных на вид диодов 1N4007.
Меняем предохранитель, если под рукой нет такого, можно запаять медный провод. Для тока до 1А, как указано возле предохранителя, диаметр медного провода около 0,039 мм. Подробнее о такой замене предохранителей смотрите здесь.
Включаем холодильник в сеть. Он заработал. Проверяем напряжение на выходе блока питания. Оно составляет 10,8 В. При токе потребления около 3 А немного падает.
В принципе, это и весь ремонт. Он оказался довольно простым. Плюс в том, что познакомились с новым устройством. Автохолодильники редко попадают в ремонт.
Автохолодильник из кулера своими руками

Автору понадобился небольшой холодильник, который можно было бы использовать в машине. Пробежавшись по магазинам и узнав цены на подобные приборы его посетила мысль о том, что возможно создание самодельного мини холодильника будет гораздо предпочтительнее, чем покупка фирменного устройства. Поэтому оценив имеющиеся у него материалы, которые могли бы пригодиться для создания самодельного автохолодильника, решил приступить к сборке подобного устройства.
Материалы:
— кулер для воды, который вышел из строя
— элемент Пельтье
— теплопроводная паста КПТ-8
— радиатор
— вентилятор
— компьютерный блок питания
— монтажная пена
— фольга
— переключатель и дополнительные провода.
— терморегулятор работы вентилятора
Описание изготовления автомобильного холодильника своими руками.
Шаг первый: выбор корпуса холодильника.
В качестве основной части корпуса будущего холодильника, автор решил взять имеющийся у него корпус от не работающего кулера, а точнее его нижнюю часть.
Вот фотография кулера целиком:
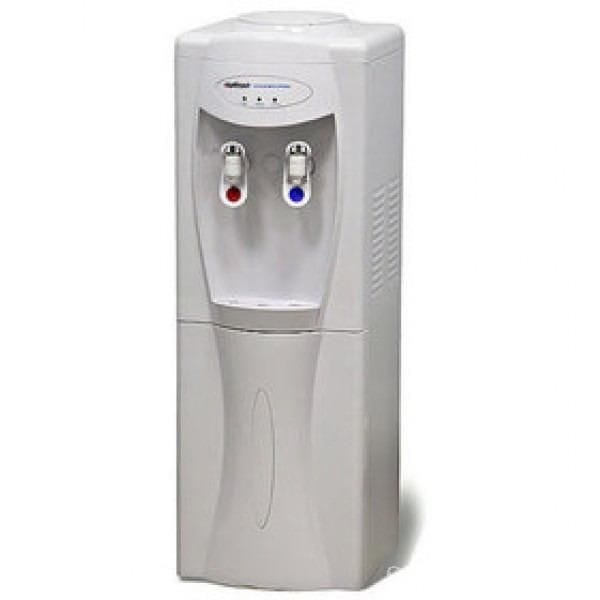
Вот из этой части кулера будет делаться автомобильный холодильник:
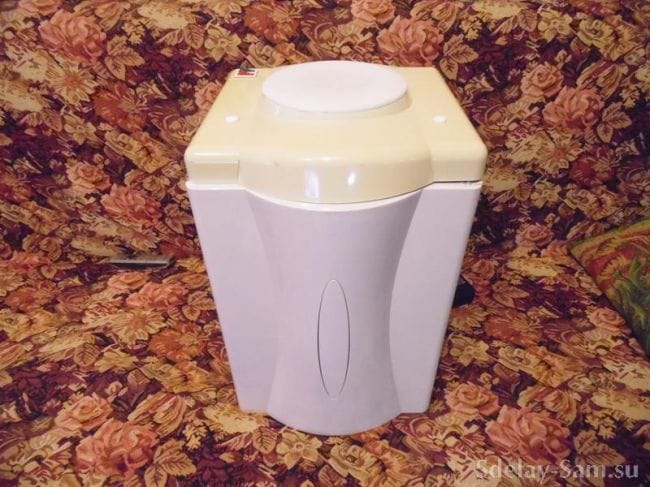
Это его вид спереди, а вот так он выглядит сзади:
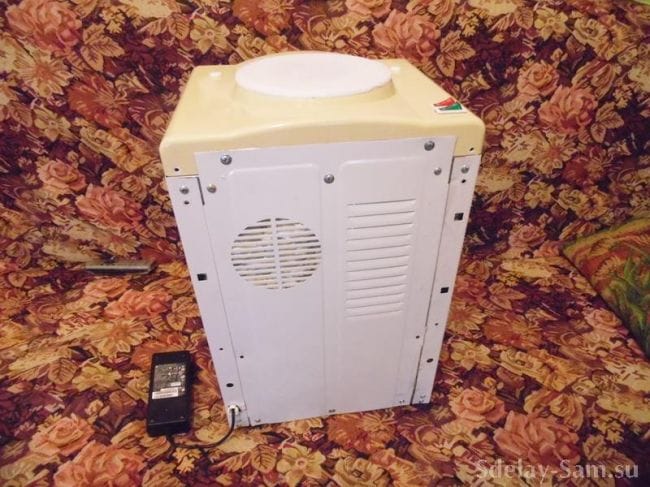
Шаг второй: доработка корпуса холодильника.
Выбрав корпус для будущего холодильника, автор приступил к его модернизации под свои нужды. Для начала кулер был разобран. Была снята верхняя часть пластиковой оболочки. Так как стандартные крепления двери находились именно там, что ему пришлось делать свои собственные крепления. Для этого было использовано несколько болтов и пара металлических пластин. В итоге получились вот такие своеобразные петли, на которых удерживается дверца камеры холодильника.
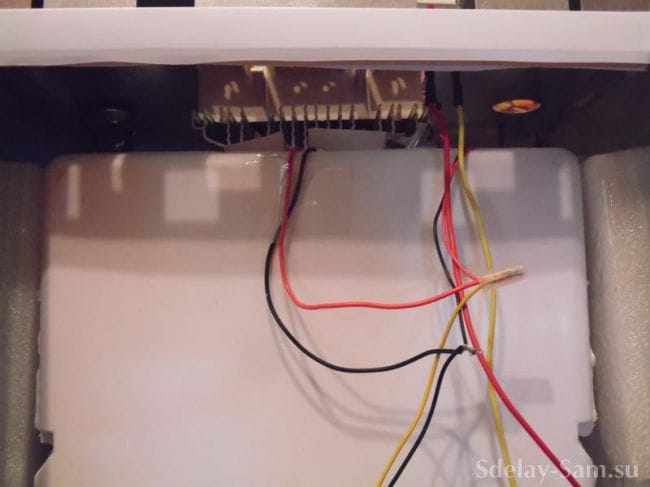
Шаг третий: выбор и установка охлаждающего элемента.
В качестве охлаждающего устройства для камеры холодильника, автор решил использовать элемент Пельтье. В общем-то практически все современные модели холодильников, для использования в автомобиле, работают именно на таком принципе.
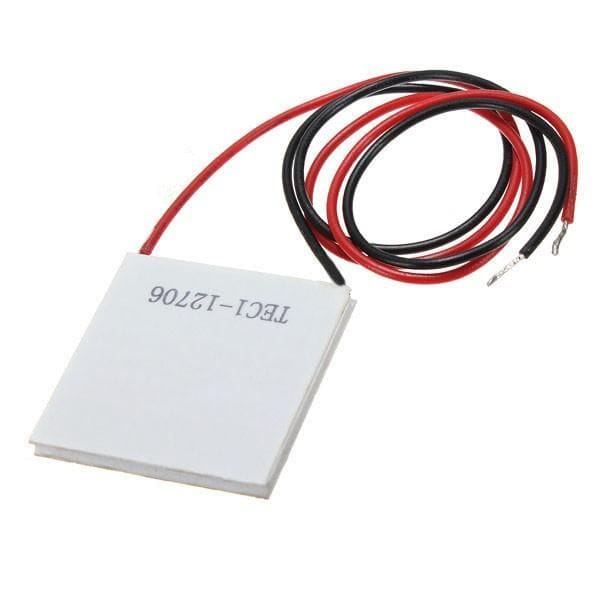
Шаг четвертый: создание охлаждающей системы для элемента.
Очень важно максимально плотно прикрепить элемент Пельтье к радиатору охлаждения. Для более лучшей передачи тепла, выделяемого обратной стороной элемента Пельтье, на радиатор может помочь использование теплопроводящей пасты, он использовал пасту КПТ-8. причем прикрепил и верхнюю и нижнюю части, для более бережной работы элемента.
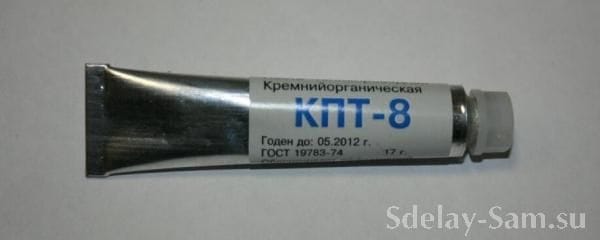
Шаг пятый: подключение питания для холодильника.
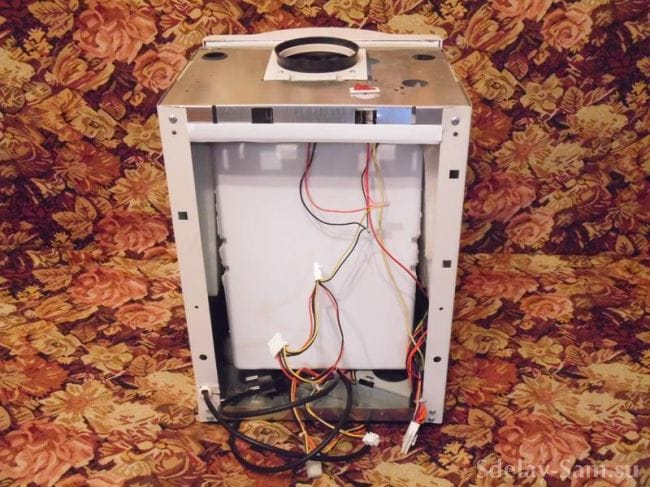
В качестве питания для данного прибора, использовал компьютерный блок питания, а точнее блок питания для ноутбука, так как он довольно удобен и его можно вывести наружу. Главное, чтобы этот блок питания был способен подавать напряжение в 12 В, а так же силу тока от 5 А.
При работе блок питания может довольно сильно нагреваться, поэтому автор посчитал, что целесообразнее вывести блок питания наружу из камеры будущего холодильника, для сохранения холода в камере.
Шаг шестой: работа над теплоизоляцией.
Для того, чтобы минимизировать передачу тепла с корпуса прибора внутрь его холодильной камеры, решил залить заднюю стенку холодильника при помощи монтажной пены.
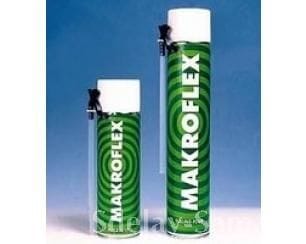
А так же, для того, чтобы максимально сохранять холодную среду внутри холодильной камеры и избежать теплопередачи со внешних стенок, застелил внутренние стенки камеры фольгой.
Шаг седьмой: установка вентилятора и создание терморегулятора его работы.
На радиатор к которому прикреплен элемент Пельтье установил сверху вентилятор. Таким образом будет осуществляться активное охлаждение радиатора и самого элемента соответственно. А для того, чтобы регулировать скорость работы вентилятора, автор нашел схему терморегулятора, который в зависимости от температуры радиатора может уменьшат или увеличивать свои обороты вращения.
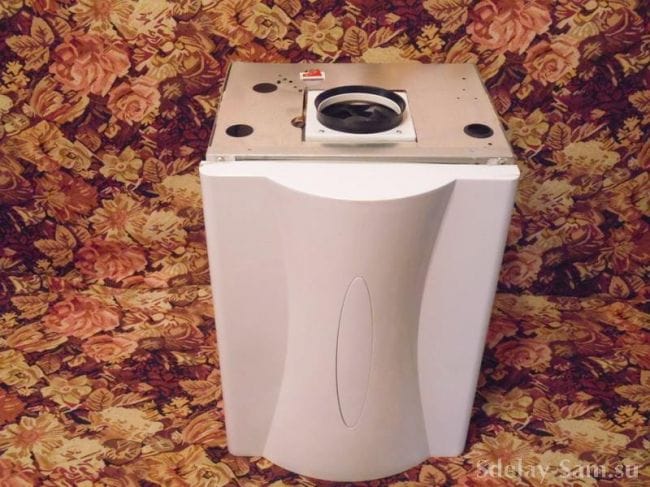
Схема терморегулятора для управления работой вентилятора:
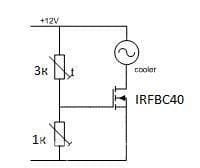
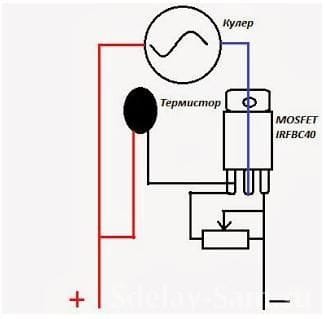
Так же вы можете посмотреть видео, которое снял, там вы можете узнать еще несколько дополнительных нюансов, а так же фрагменты работы над холодильником во время его сборки.
Видео-ролик автора о создании данного холодильника:
Источник
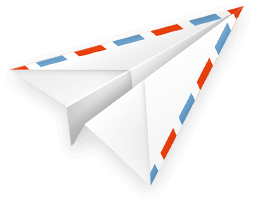
Получайте на почту подборку новых самоделок. Никакого спама, только полезные идеи!
*Заполняя форму вы соглашаетесь на обработку персональных данных
Становитесь автором сайта, публикуйте собственные статьи, описания самоделок с оплатой за текст. Подробнее здесь.Автохолодильник компрессорный и Пельтье своими руками
Нежелание питаться всухомятку во время длительных путешествий на автомобиле оправдывает популярность использования автомобильного охлаждающего оборудования. Его можно купить или с целью экономии сделать самому. Сборка автохолодильника своими руками требует технической подготовки, навыков, понимания принципа действия хладотехники.
Создание холодильника для автомобиля отличается трудоемкостью, затратностью, но имеет ряд общих принципов. Планируя постройку изделия, вы должны:
- посчитать расходы;
- решить, насколько вы хотите охлаждать продукты;
- подобрать тип агрегата, зависящий от:
- длительности ваших поездок;
- количества продуктов;
- температуры за бортом;
- энергопотребления оборудования и емкости аккумулятора автомобиля.
Монтаж холодильника делится на три этапа:
- Постройка корпуса.
- Изготовление охлаждающих элементов, зависящих от вида оборудования. В авто используют холодильники:
- компрессорные;
- абсорбционные;
- термоэлектрические;
- сумки-холодильники.
Рассмотрим некоторые типы холодильников для автомобиля подробнее.
На элементах Пельтье
Относится к термоэлектрическому типу оборудования. Элемент Пельтье, положенный в основу системы охлаждения, использует принцип разницы температур верхней (нагретой) и нижней (охлажденной) частей. Устройство передает тепло из камеры наружу. Эффективность работы оборудования зависит от температуры воздуха вокруг, эффективности термоизоляции корпуса, объема камеры.
Изготовление автохолодильника своими руками на элементах Пельтье оправдано экономией денег и универсальностью оборудования. Его можно подключать к штатной системе авто 12В, сети переменного тока 220В. Первый вариант не требует монтажа дополнительных блоков питания, вентиляторов, обойдется значительно дешевле.
Достоинства холодильника Пельтье:
- небольшие размеры и вес;
- простота использования;
- долговечность;
- экономная эксплуатация;
- постоянное поддержание температурного режима.
Минусы:
- охлаждение воздуха на 10-15 градусов ниже температуры окружающей среды;
- для достижения заданных параметров охлаждения требуется более одного часа.
Компрессорный
Это металлическая морозильная камера с термоизоляцией, оснащенная компрессором и испарителем. Принцип действия похож на работу традиционного домашнего агрегата. Жидкий хладагент становится газом в испарителе, забирает тепло. С помощью компрессора вещество удаляется, конденсируется, снова становится жидкостью под давлением.
Преимущества сборки автохолодильника компрессорного своими руками:
- экономия. Промышленные аналоги техники дорого стоят;
- охлаждение продуктов до 18°С градусов мороза;
- быстрое достижение нужных характеристик холода внутри камеры;
- экономичность;
- вместительность;
- универсальность.
Водители часто отказываются от изготовления охлаждающего оборудования, работающего по этому принципу, но выбор типа на основании цены ошибочен. Если вам достаточно иметь рядом прохладную бутылку воды, можно довольствоваться недорогими вариантами. Когда нужно везти быстро портящиеся продукты, детское питание или предстоит долгий переезд, лучше использовать компрессор.
Сравнительный анализ типов автомобильных холодильников позволяет сделать вывод, что наиболее оптимальным вариантом являются компрессорные устройства. Хотя они дороже термоэлектрических. Это компенсируется эффективностью работы, экономичностью и возможностью замораживать продукты, независимо от жары на улице. Абсорбционные системы обходятся так же, как компрессорные. Однако уступают по степени охлаждения.
Ремонт автомобильного термоэлектрического холодильника Ezetil, Краснодар, Белецкий А. И.
Чтобы понять что представляет собой в ремонте термоэлектрический холодильник, привожу серию фотографий его внутреннего устройства.
1. Внешний вид термоэлектрического холодильника Ezetil.

2. Внутренний охладитель — холодный радиатор. В качестве радиатора, примерен алюминиевый радиатор, а для быстрого охлаждения холодильной камеры служит вентилятор. Вся конструкция держится на двух болтах, обведенных красными линиями.
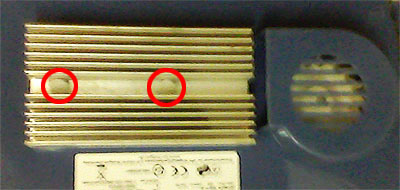
3. Наружный охладитель — горячий радиатор. По площади в два раза больше внутреннего, холодного радиатора, алюминиевый. Для быстрого и большего охлаждения, так же применен вентилятор. Это позволяет эксплуатировать холодильниу при достаточно высоких температурах воздуха.
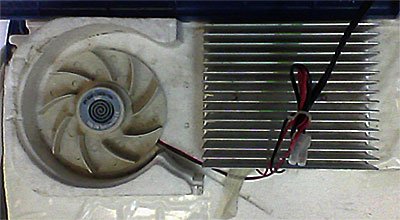
Между двумя алюминиевыми радиаторами, посажен на термопасту и зажат термоэлектрический модуль элементов Пельтье. В англоязычной литературе элементы Пельтье обозначаются TEC (от англ. Thermoelectric Cooler — термоэлектрический охладитель).
Термоэлектрический модуль элементов Пельтье вид с плоскости.
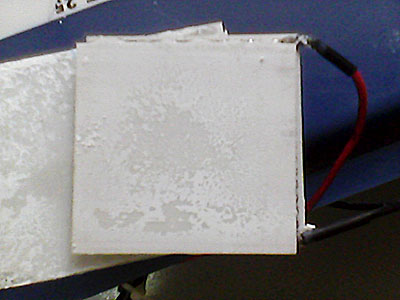
Термоэлектрический модуль элементов Пельтье, вид с торца.
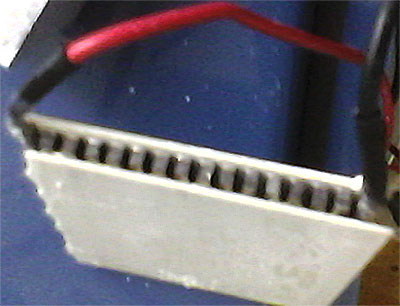
Термоэлектрический модуль находится между двумя термопроводными тонкими и хрупкими керамическими пластинами из из оксида или нитрида алюминия. При сборке, радиаторы сильно стягивать нельзя, полопаются керамические пластины.
Вот схематическая конструкция термомодуля Пельтье.
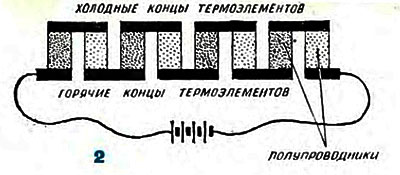
Вот внутренняя конструкция термомодуля Пельтье.
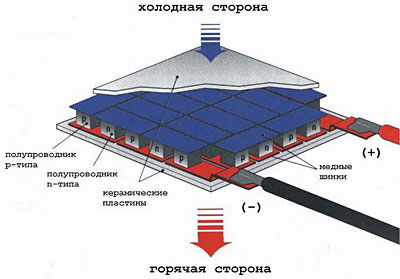
Классические 12 Вольтовые элементы Пельтье — это 127 полупроводниковых элементов, обычно из теллурида висмута и германида кремния, включенных последовательно и спаянных перемычками.
Модули Пельтье паяются легкоплавким припоем с температурой плавления 138С , так что если элемент случайно останется без охлаждения и перегреется — то достаточно будет отпаяться одному из 127*
2 =254 контактов чтобы выкинуть элемент на свалку.
Все детали модуля Пельтье, очень хрупкие, как сами элементы, так и керамические теплопроводные изолируюшие пластины.
Для работы модуля необходимо, чтобы через него протекал постоянный ток. Пульсации постоянного тока не должны превышать 5 %. Если уровень пульсаций будет выше, параметры модуля будут хуже.
На модули обычно подается напряжение питания, примерно 75 % от величины Umax.
При использовании модуля Пельтье необходимо обеспечить эффективный отвод тепла с его горячей стороны.
Вот стандартные характеристики большинства модулей.
Температура горячей стороны 25° C 50° C
Максимальная разность температур 66° C 75° C
Максимальный ток потребления 6,4 А 6,4 А
Максимальное напряжение 14,4 В 16,4 В
Достоинством элемента Пельтье являются небольшие размеры, отсутствие каких-либо движущихся и механических частей, шума, газов и жидкостей. Меняя местами плюс и минус напряжения питания возможно как охлаждение, так и нагревание — это даёт возможность термостатирования при температуре окружающей среды как выше, так и ниже температуры термостатирования.
Недостатком элемента Пельтье является более низкий коэффициент полезного действия, чем у компрессорных холодильниках.
Основной проблемой в построении элементов Пельтье с высоким КПД является то, что свободные электроны в веществе являются одновременно переносчиками и электрического тока, и тепла. Материал для элемента Пельтье должен одновременно обладать двумя взаимоисключающими свойствами — хорошо проводить электрический ток, но плохо проводить тепло.
С ув. Белецкий А. И. 10.08.2014г. Кубань Краснодар.
Как сделать автохолодильник своими руками
Для пикника и поездки к морю не помешает запастись хорошими и сытными продуктами питания. Чтобы не ограничиваться стандартным набором туриста из консервов и сухарей, заполните вкусностями автохолодильник. Он сделает реальным благом мечту о прохладительных напитках в самую жару. Как сделать этот практичный и компактный агрегат своими руками, мы расскажем в статье.
Автомобильный холодильник, созданный собственноручно, имеет массу достоинств.
№ |
Достоинства |
Недостатки |
1 |
Сравнительная дешевизна. Чтобы изготовить агрегат своими руками, можно использовать подручные средства и материалы. Благодаря этому стоимость холодильника для автомобиля будет минимальной. |
Необходимость затратить некоторое количество времени для создания агрегата. |
2 |
Экономичность — ему не понадобится много энергии. Работает устройство тогда, когда необходимо владельцу, что исключает траты ресурса вхолостую. |
Чтобы изготовить автохолодильник, потребуется иметь некоторые навыки. |
3 |
Компактность. Можете изготовить агрегат, отлично помещающийся в небольшом легковом автомобильчике. |
|
4 |
Пожаро- и электробезопасность. |
|
5 |
Универсальность. Агрегат может работать в автономном режиме. Это исключает риск отключения от питания во время остановки транспортного средства. |
|
Совет: хотите пользоваться преимуществами автохолодильника, однако не имеете желания и умений, чтобы мастерить его? Всегда можно купить автохолодильник требуемого объема в магазине MOYO.UA!
Читайте также: Как можно использовать компрессор от холодильника в качестве аэрографа.
Этап первый: Создаем корпус автохолодильника
Прежде, чем приступить к изготовлению корпуса, определитесь с целями будущего агрегата:
- Если запланирована непродолжительная поездка, соорудите автохолодильник из фанерного ящика, фольги и листов пенопласта. Можно взять другой теплоизолирующий материал. Автономные хладагенты помогут создать и поддерживать нужную температуру.
- Для продолжительного отдыха вдали от благ цивилизации с гаджетами и электричеством, нужно оснастить самодельный автохолодильник, отдельным охладительным модулем. На его конструкции мы остановимся подробнее.
Для создания ящика берется фанера, стойкая к воздействию влаги. Снаружи стенки проклеиваются слоем дермантинового материала. С внутренней стороны корпуса будущего агрегата плотно укладывается материал с теплоизоляционными свойствами. Это, например, пенопласт, пенополиуретан, пенополистирол.
Слой теплоизоляции для холодильника объемом в 40 литров составляет порядка 2 сантиметров. Внутрь большого ящика со слоем утеплителя на внутренней поверхности помещается ящик поменьше, который используется для хранения продуктов. Объем “вкладки” должен соответствовать вашим потребностям. Оптимально подойдет для этого пластиковая емкость, в которую помещается двухлитровая бутылка воды, или другая посуда для хранения, которую планируете использовать транспортировки продуктов.
Совет: слой теплоизоляции должен быть как можно более плотным. Это обеспечит должное качество поддержания холода. Следите за тем, чтобы между теплоизоляционным материалом не было зазоров, сквозь которые может просачиваться теплый воздух.
Читайте также: Как сделать походный холодильник.
Этап второй: Изготовление охладителя
Чтобы аппарат сохранял холод сутки там, где нет возможности использовать стационарный холодильник, работающий от сети, хватит хладоэлементов, установленных в ящик. Если планируете более длительный рейд, уделите созданию охладителя больше времени и вдохновения.
В качестве источника холода могут использоваться:
- Селитра;
- Элементы Пельтье.
Расскажем подробнее, как использовать каждое из описанных веществ.
Селитра, растворяясь в воде, выделяет холод. Создавая хладоэлементы на ее основе, заполните на 40 % бутылки, и добавляйте по необходимости воду.
Для создания хладоэлементов “длительного действия” предварительно заморозьте в морозилке бутылку, наполовину заполненную водой, и только потом насыпьте в нее селитры.
Совет: если используете для охлаждения смесь воды и селитры, побеспокойтесь о безопасности окружающей среды! Концентрация для охлаждения, является слишком значительной для растений и водоемов. Слив отработанной жидкости способен травмировать корневую систему растений. Хотите вылить нагретую воду? Без проблем! Только предварительно хорошенько разведите ее хотя бы в складной туристической посуде!
Элементы Пельтье также часто применяются для того, чтобы создать холод в агрегате. Мощность этих деталей размерами 40х40 милиметров, основанных на термоэлектрике, составляет 50 Вт. Количество элементов подбирается исходя из индивидуальных габаритов. В среднем хватит одного термоэлемента на каждые 10 литров объема внутренней камеры автохолодильника.
Элементы склеивают термопастой, герметизируют, изолируют. Хладоэлемент вставляют в заднюю стенку автохолодильника и закрепляют батарею, подобную той, что применяют в кулерах компьютерной техники.
Для усиления эффективности с внешней стороны устанавливают вентилятор — он поможет поддерживать разницу температур порядка 20 градусов. Это, конечно, меньше, чем в стационарных морозильных камерах, но все-таки кое-что.
Работа автохолодильника с элементами Пельтье потребует значительного расхода топлива — примерно 0,5 литра бензина в час. При этом коэффициент полезного действия устройства является невысоким.
Читайте также: Как сделать кондиционер из старого холодильника.
Этап третий: Выбор провода и подключение автохолодильника
Подключают автомобильный холодильник проводами автомобильной проводки, длина которых не должна превышать 2 метров. Если если создаете универсальный агрегат, лучше взять удлинитель.
Выбор сечения зависит от конкретных размеров агрегата и потребляемой мощности. Для описанного выше агрегата емкостью 50 литров с 5-ю элементами Пельтье пригодится кабель со стандартным сечением. Его можно подсоединять напрямую, через клеммы в 220 вольт, или в 12-ваттный прикуриватель.
Чтобы соорудить универсальный агрегат, потребуются дополнительные вложения, ведь установка встроенных блоков влетает в копеечку. Применение штатной системы, которой оснащено транспортное средство, повышает экономичность устройства. Приобретите штатный разъем, используя прикуриватель как источник питания, и установите его на провод от элементов Пельтье.
Выбирая, как подключить автохолодильник, проанализируйте свои планы относительно его использования.
Переносному холодильнику на даче хватит питания от розетки. Модификация автохолодильника в любом случае обойдется дешевле, чем приобретение нового агрегата.
Совет: неохота «играться» со сборкой автохолодильника, однако нет средств на приобретение агрегата? Купите необходимую технику в кредит!
Самостоятельно создать автомобильный холодильник можно, если есть желание и должный уровень мастерства. Для этого нужно запастись терпением и основательно подойти к делу. В результате привезете с рыбалки богатый улов даже жарким летом!
Видео о том, как создать автохолодильник, смотрите здесь.
Ремонт автомобильного усилителя своими руками.
Реальные примеры ремонта усилителей для авто
Здесь я поделюсь своим скромным опытом в области ремонта автомобильных усилителей.
Надеюсь, информация пригодиться начинающим радиомеханикам в их нелёгком деле восстановления аудиоаппаратуры, а также автолюбителям, знакомым с электроникой и желающим починить свой усилитель самостоятельно.
Для начала, хотелось бы рассказать о том, как включить автоусилитель без автомагнитолы и в домашних условиях. Подробнее об этом читайте здесь. Это понадобиться при ремонте автоусилителя.
Если под рукой нет достаточно мощного блока питания, то подойдёт любой на напряжение 12V и ток 1 — 3 ампера. Но тут стоит понимать, что он нам нужен лишь для того, чтобы включить и наладить усилитель. Эксплуатировать на полной мощности мы его не будем, поэтому потребляемый ток будет минимальный.
Также настоятельно рекомендую прочитать или взять на заметку материал по устройству преобразователя автомобильного усилителя. Эта информация очень важна.
Ну, а теперь, примеры ремонта из реальной практики. В основном они касаются одного из главных блоков любого автоусилителя – преобразователя напряжения, или по-другому, инвертора.
Ремонт автомобильных усилителей CALCELL.
1. Неисправность: автоусилитель уходит в защиту. На передней панели светится красный светодиод PRT (Protect – «защита»). После пары включений усилитель вообще перестал подавать признаки жизни — светодиод PRT перестал светиться.
Причиной неисправности оказался транзистор 2N4403 в цепи микросхемы TL494CN (преобразователь). Один из его переходов был пробит. Кроме этого сгорел резистор на 10Ω (Ом). На фото R7 – это он. Пока резистор «терпел» – усилитель включался, но уходил в защиту. Как перегорел – усилитель перестал включаться вообще.
Цоколёвка биполярного P-N-P транзистора 2N4403.
Почему усилитель уходил в защиту? Дело в том, что данный транзистор входит в состав цепи вкл./откл. Из-за пробоя P-N перехода транзистора усилитель не включался и уходил в защиту.
Под рукой подходящей замены PNP транзистору 2N4403 не оказалось. Поэтому была предпринята рискованная попытка взять такой же транзистор из предварительного каскада одного из каналов усилителя. Благо они там были. Да, подумаешь, решил я, ну вытащу оттуда транзистор, запаяю взамен неисправного, проверю усилитель. Ай, да, так и сделал. Но после нескольких секунд после включения я почуял запах гари. Оказалось, что из-за отсутствия 1 маааленького транзистора мощные комплементарные транзисторы выходного каскада УМЗЧ стали жутко греться. К счастью, транзисторы уцелели. Поэтому я не советую так «хитрить».
Замену транзистора осложняло то, что он был заляпан каким-то резиновым клеем, которым приклеены к плате бочонки электролитов.
2. Усилитель CALCELL POP 80.4 не включается. Перегорают защитные предохранители.
Аппарат пришёл «дохлый», видимо после некорректного подключения. После беглого осмотра деталей без выпаивания обнаружилось, что пробит стабилитрон на 11V в «обвязке» микросхемы ШИМ-контроллера TL494CN. Также обнаружился пробой самой микросхемы TL494CN. При замере сопротивления между выводом 12 (+ питания, Vcc) и 7 (- питания, GND) мультиметр показал «0». По всей видимости было сильно завышено напряжение питания усилителя.
После замены микросхемы TL494CN и стабилитрона на 11V была предпринята попытка включить усилитель. Но, после включения засвечивался красный светодиод PRT на несколько секунд (как и должно быть), а затем полная тишина… . Блок питания, от которого запитывался усилитель уходил в защиту из-за перегрузки по току.
Оказалось, что одна из двух групп MOSFET-транзисторов на плате преобразователя сильно греется. Транзисторы другой группы – холодные. После проверки 3-ёх транзисторов STP75NF75 которые грелись, выяснилось, что они пробиты (Исток – Сток). Также был пробит транзистор 2N4403, который является буферным для данного плеча преобразователя. Более подробно со схемой типового преобразователя (инвертора) автоусилителя можно ознакомиться тут.
После замены буферного транзистора 2N4403 и трёх MOSFET’ов STP75NF75 (маркированы как P75NF75), автоусилитель стал исправно работать.
3. Усилитель CALCELL POP 80.4. При включении усилителя загорается красный светодиод «PROTECT» и через несколько секунд тухнет. Усилитель не включается – индикации нет.
Такое бывает, когда преобразователь уходит в защиту из-за большого потребления тока или короткого замыкания в нагрузке. Нагрузкой в данном случае является все четыре усилителя, блок фильтров и предусилители.
Наиболее вероятная причина срабатывания защиты – выход из строя выходных транзисторов. В усилителе CALCELL POP 80.4 в качестве выходных транзисторов применяются мощные биполярные транзисторы. Оценить их исправность можно вот по этой методике, причём выпаивать транзисторы вовсе не обязательно. Как правило, пробой перехода транзистора определяется легко, мультиметр начинает противно пищать зуммером – сигнал того, что между выводами транзистора нулевое сопротивление.
Стоит учесть, что при такой быстрой проверке связанные с проверяемым транзистором детали (маломощные транзисторы и т.п.) могут влиять на показания. Поэтому если есть сомнения – выпаиваем и проверяем транзистор отдельно. Нередки случаи, что пробитыми бывают как раз элементы, связанные с нашим транзистором, а не он сам. В некоторых усилителях, например, таком как SUPRA SBD-A4240, в качестве выходных транзисторов применяются MOSFET’ы. MOSFET-транзисторы можно проверить универсальным тестером, так как для таких целей обычный мультиметр годится не всегда.
Вернёмся к нашему усилителю. Для большей наглядности я буду ссылаться на принципиальную схему данного усилителя – схема автоусилителя CALCELL POP 80.4. При проверке выходных транзисторов у одного из них переход База – Коллектор (B-C) «звонился» как пробитый. На схеме он обозначен как Q312 (2SA1694). Чтобы проверить работоспособность усилителя, я выпаял неисправный транзистор и его комплементарную пару – транзистор 2SC4467 (Q311). Включил усилитель, но он снова ушёл в защиту. Значит где-то осталось что-то горелое. Кроме того сильно грелись маломощные транзисторы Q309 (MPSA06) и Q310 (MPSA56). Проверка показала, что у транзистора Q309 (MPSA06) пробиты оба перехода.
Так как в продаже комплементарной пары 2SC4467/2SA1694 не было, то решил заменить более мощными аналогами – парой 2SA1943/2SC5200 производства фирмы TOSHIBA. Вот такими. На ощупь тяжёленькие и внушают доверие .
После установки новых транзисторов 2SA1943/2SC5200 оказалось, что они крупноваты и из-за этого плата не влазит в корпус.
Пришлось выкусить небольшую часть печатной платы, чтобы они убирались в корпус и плотно прилегали к поверхности.
После замены усилитель стал исправно работать.
Во время электропрогона я заметил, что даже без нагрузки маломощные транзисторы в предусилителях довольно ощутимо греются. При проигрывании музыки с обильными басами нагрев усиливается. Усилитель работал на два сабвуфера (по одному в мост).
Возможно, длительная работа на максимальной мощности привела к перегреву и выходу из строя маломощного транзистора MPSA06 (Q309), а это в свою очередь к пробою перехода Б-К мощного транзистора 2SA1694 (Q312) в выходном каскаде усилителя.
4. Нестандартный случай. В ремонт принесли только что купленный в магазине усилитель CALCELL. По словам владельца после подключения питания из вентиляционных отверстий усилителя пошёл дым.
После вскрытия и осмотра печатной платы оказалось, что на выводах одного из MOSFET транзисторов преобразователя есть следы паяльной пасты, шариков припоя. Вот фото.
Судя по всему, через остатки припойной пасты при включении пошёл ток. Из-за этого канифоль в пасте нагрелась и стала испаряться в виде белого дымка. После этого усилитель не включался из-за припойной перемычки, образовавшейся при оплавлении паяльной пасты. Не секрет, что дешёвая электроника, сделанная в Китае, не проходит предпродажной проверки. Отсюда вот такие «ляпы».
Ремонт автомобильного усилителя Lanzar VIBE 221.
Диагноз: автоусилитель не включается. Нет индикации светодиодов. Судя по внешнему виду печатной платы, усилитель пытались чинить, и даже были заменены ключевые MOSFET транзисторы в одном из плеч преобразователя. Вместо родных IRFZ44N были установлены STP55N06. Но усилитель приказал долго жить. Также в цепи затворов МОП-транзисторов были «подгоревшие», но исправные резисторы на 100 Ом. При проверке буферных транзисторов 2SA1023, которые «раскачивают» мосфеты IRFZ44N, выяснилось, что они исправны.
После замены микросхемы ШИ-регулятора TL494CN усилитель заработал. На всякий случай были заменены буферные транзисторы 2SA1023 и диоды 1N4148 в цепи база-эмиттер этих транзисторов.
Ремонт автомобильного усилителя Mystery.
Проблема: усилитель включается, но звука нет. Автомобильный усилитель Mystery 1.300 типичный представитель так называемых моноблоков. То есть это монофонический усилитель. Заявленная производителем звуковая мощность — 300W. Такие усилители обычно используют для работы на мощный низкочастотный динамик, то бишь сабвуфер или саб.
После вскрытия и осмотра печатной платы выяснилось, что несколько транзисторов (2SB1367 и 2SD2058) плохо пропаяны, имеет место деградация пайки и чрезмерный нагрев мест пайки. Транзисторы, судя по всему, являются частью стабилизаторов на 15V во вторичных цепях питания. Служат эти стабилизаторы для питания операционных усилителей и фильтров усилителя. По-другому этот узел можно назвать предусилителем. Именно к нему мы подключаем те самые «тюльпаны», по которым подаётся звуковой сигнал с автомагнитолы. Естественно, если нет питания предусилителя, то и звука не будет.
Почему так произошло? Дело в том, что транзисторы, которые перегревались, не имеют радиатора, корпус их пластиковый. Держатся они на собственных выводах. Дополнительного крепления нет. Из-за перегрева и постоянной тряски (в авто ведь установлен), пайка разрушилась и контакт нарушился. Поэтому стабилизаторы перестали работать. Ещё чуть-чуть и транзисторы просто бы выпали из установочных отверстий!
После восстановления пайки транзисторов, усилитель полностью заработал, но ощутимый нагрев транзисторов наводил на мысль, что через некоторое время будет повтор.
Было решено установить греющиеся транзисторы на самодельный радиатор, чтобы уменьшить нагрев. Также обновить пайку выводов и сделать её более надёжной. Вот что из этого вышло.
Заодно на радиатор были посажены соседние транзисторы, которые грелись меньше — для придания жёсткости конструкции. Так как транзисторы в пластиковом корпусе и не имеют металлического фланца, нанёс на место теплового контакта с радиатором ещё и теплопроводной пасты КПТ-19.
Кроме всего прочего на печатной плате моноблока имелся явно «вспученный» электролитический конденсатор на 3300 µF * 63V во вторичном выпрямителе. В блоке питания – инверторе обычно ставиться 2 электролитических конденсатора, так как питание усилительных каскадов двухполярное, в районе ± 28 – 37 вольт. Соседний электролит выглядел лучше и не был «вспучен».
Было решено на всякий случай заменить тот электролит, который вздулся новым на 4700 µF * 63V (такой был в наличии). Во время электропрогона автоусилителя выяснилось, что заменённый электролитический конденсатор слегка нагревается. Оказалось, что его подогревают расположенные рядом мощные резисторы. Для справки – у соседнего электролита таких резисторов рядом нет. Это явная недоработка. Как известно, нагрев плохо действует на электролитические конденсаторы, так как электролит быстрее высыхает и их ёмкость уменьшается.
Ремонт автомобильного усилителя Fusion FP-804.
Неисправность: автоусилитель не включается. Индикации нет. После вскрытия причину долго искать не пришлось. В преобразователе сгорели все MOSFET-транзисторы HFP50N06 (оригинал – STP50N06), а также несколько резисторов на 47 Ом в цепи затвора некоторых из этих транзисторов. Также выбило буферные транзисторы 2SA1266.
Взамен сгоревших транзисторов HFP50N06 были установлены IRFZ48N, заменены новыми буферные транзисторы 2SA1266, сгоревшие резисторы 47 Ом, а также на всякий случай микросхема ШИ-контроллер TL494CN.
Аппарат включился и стал работать исправно. Но радость моя была недолгой. Спустя три дня мне позвонил владелец усилителя и сообщил, что появился слабый монотонный свист в тыловых динамиках. Свист был слышен только при работающем двигателе.
Первая мысль, что пришла в голову – помехи от генератора, которые попадают в звуковой тракт усилителя. Такое бывает при сделанной наспех проводке и близком расположении питающих и сигнальных (межблочных) цепей. Но электропроводка и межблочные кабели были выполнены качественно, в чём я и убедился. Через день мне привезли уже «дохлый» усилитель Fusion FP-804 со знакомым диагнозом: не включается.
Самое интересное было в том, что индикатор питания «Power» еле заметно светился. Но на это я не обратил внимание. После вскрытия оказалось, что опять вышибло всё те же MOSFET’ы. Так данный усилитель оказался у меня в груде лома – отдали на детали.
Спустя некоторое время решил восстановить этот усилитель, да и хотелось разобраться, в чём же причина повального выгорания довольно дорогих мосфетов в преобразователе. Купил новые транзисторы взамен неисправных, установил и…
При первом запуске стал свидетелем феерического шоу. Сразу после включения послышался нарастающий свист – медленный запуск преобразователя, а потом увидел проскакивающие искры из центра тороидального трансформатора.
Вот она – неисправность! Пробой обмоток в трансформаторе. Если бы замешкал и не выключил, то выжег бы напрочь и эту партию MOSFET’ов.
После этого стало ясно, почему тускло светился зелёный светодиод «Power» при подключенном питании 12V. Ток попадал во вторичную цепь через пробой между обмотками трансформатора и слегка «подсвечивал» светодиод индикации питания. С такой неисправностью я столкнулся первый раз. Единственный выход – перемотка тороидального трансформатора.
Принципиальная схема автоусилителя Fusion FP-804 (он же Blaupunkt GTA-480) приведена тут.
Ремонт автомобильного усилителя SUPRA.
Автомобильный усилитель SUPRA SBD-A4240.
Неисправность: Включается штатно – «зелёный светодиод«. Но при подаче сигнала на входы звука нет ни в одном канале. Усилитель молчит.
Данная неисправность не типовая. Для лучшего пояснения методики поиска и устранения поломки, я буду ссылаться на схему данного усилителя. Схема автомобильного усилителя Supra SBD-A4240 (откроется в новом окне).
Замеры напряжения питания во вторичных цепях ничего не дали – всё в норме. После беглой проверки был обнаружен пробитый стабилитрон 7,5V (на схеме обозначен как ZD4).
Пробитый стабилитрон приводил к отключению сигнальных цепей всех усилителей, так как установлен он в цепи блокировки входных сигналов (Q3, Q101, Q201, Q301, Q401, ZD3, ZD4).
Эта цепь блокирует прохождение сигнала звуковой частоты на входы предусилителей. «Блокировка» сигнала происходит на короткое время, сразу после включения усилителя. Делается это для того, чтобы избежать «щелчка» в динамиках.
Так как в наличии стабилитрона на 7,5V не было, то вместо пробитого был установлен стабилитрон на 5,6V (это привело к небольшим искажениям сигнала, позднее установил стабилитрон на 7,5V). После этого стали работать 3 канала с небольшими искажениями, а 1 канал выдавал сильные искажения с признаками самовозбуждения усилителя. При касании пинцетом входа звукового сигнала («тюльпанов») в динамике слышалось периодическое «бульканье».
Подозрение пало на блок входных фильтров, тот, что реализован на операционных усилителях – микросхемах KIA4558 (на схеме U1-A и U2-A). Поэтому, чтобы определить, где же кроется неисправность, была разорвана сигнальная цепь, идущая с выхода блока входных фильтров ко входу предусилителя. Делается это просто – выпаивается один вывод электролитического конденсатора (на схеме это C108).
Далее касаемся пинцетом вывода резистора R115 или вывода базы транзистора Q103. Тем самым мы подаём на вход предусилителя «сигнал-помеху». При этом если усилитель исправен, то в динамиках мы услышим характерный гул. Но в данном случае вместе с гулом в динамике, я опять услышал противное «бульканье». Стало понятно, что проблему нужно искать в предусилителе, а не блоке входных фильтров.
Поиск неисправного элемента в предусилителе осложняло то, что он выполнен на маломощных транзисторах (на схеме Q102 — Q116), которых довольно много. Проверка этих транзисторов без выпайки из платы (на предмет пробоев переходов) результата не дала. Поэтому было решено выпаять все транзисторы предусилителя и проверить их уже более тщательно.
Результата это также не дало, хотя и удалось обнаружить два транзистора 2N5551, которые вызывали недоверие. Проверял их универсальным тестером, и они через раз определялись как пробитые. Пришлось их заменить новыми. Все остальные транзисторы оказались исправны, как и другие элементы схемы: диоды (D3 — D5) и конденсаторы. НО! Резисторы я не проверял!
При внешнем осмотре заметил, что на корпусе одного из резисторов (на схеме R124 — 47 Ом) еле заметный подгар. При проверке, оказалось, что резистор в обрыве.
Так как резистор R124 установлен в цепи эмиттера транзистора Q106 (2N5551), то его обрыв приводил к некорректной работе усилителя и тому самому «бульканью». После замены неисправного резистора усилитель стал работать исправно. Также был заменён новым транзистор Q106. Как уже говорил, при проверке пара транзисторов 2N5551 попала под подозрение. Возможно, один из них и есть транзистор Q106, в цепи которого и сгорел резистор R124.
Другая неисправность такого же усилителя.
В ремонт принесли уже знакомый нам автоусилитель SUPRA SBD-A4240 (V1M07) с «выдранными» электролитами во вторичных цепях преобразователя. На мой вопрос: «Как это произошло?», – владелец ответил, что усилитель был в машине, попавшей в аварию. В результате усилитель исправно работал, но в динамиках был жуткий фон – импульсные помехи от преобразователя делали своё дело. На место родных конденсаторов были установлены новые, ёмкостью 2200 мкФ * 35V. Фон пропал.
Если есть возможность, то, конечно, лучше ставить электролиты с большей ёмкостью (2200 — 4700 мкФ).
Бывают случаи, что найти электролитический конденсатор большой ёмкости довольно сложно. Не беда! Можно сделать составной конденсатор из нескольких, ёмкость которых невелика. О том, как правильно соединять конденсаторы читайте вот тут.
Ремонт усилителя AVATAR ATU-2000.1D
Ещё один пример ремонта, о котором бы хотелось рассказать. Аппарат – одноканальный усилитель AVATAR ATU-2000.1D для сабвуфера.
Усилитель способен выдавать номинальную мощность до 2000W на нагрузку 1Ω (при напряжении питания 14,4V и THD 1%). Очень мощный агрегат.
Интересен тем, что звукоусилительный тракт выполнен в классе D, но ремонтировать всё также приходится преобразователь напряжения питания после того, как на усилитель подали напряжение обратной полярности (переполюсовка). Процесс ремонта во всех подробностях я описал здесь.
Другие мелочи.
Все активные элементы – транзисторы, как полевые, так и мощные комплементарные пары транзисторов устанавливаются на радиатор через изоляционную прокладку из слюды. Для улучшения теплопередачи применяется теплопроводная паста.
В некоторых случаях приходится демонтировать печатную плату с корпуса усилителя, который ещё является радиатором. Естественно, теплопроводная паста размазывается, пачкает всё вокруг, к ней прилипает пыль и грязь. Поэтому приходиться убирать её с радиатора и корпусов транзисторов, очищать от неё изолирующие прокладки из слюды. Занятие не из приятных.
После ремонта, всё нужно восстановить, как было. Под рукой должна быть теплопроводящая паста КПТ-8 или КПТ-19. Наносить пасту лучше с обеих сторон, и на металлическую подложку транзистора и на радиатор. В таком случае слюда будет посередине и с обеих сторон покрыта слоем термопасты. Наносить много пасты не советую, главное, чтобы на поверхности образовался ровный, тонкий слой пасты.
Советую по случаю также прикупить слюды. Я, например, купил слюдяную пластинку размером 10 * 5 см. и толщиной около 1 мм. Слюду можно легко «расслоить» с помощью острого лезвия ножа. Получиться несколько изоляционных прокладок из слюды. Их можно использовать взамен сломанных, испорченных, потерянных изоляционных прокладок. Слюда легко нарезается ножом на пластинки подходящего размера.
Где взять детали для ремонта?
При ремонте автоусилителя нередко требуются детали для замены неисправных. Бывает, что найти такие не удаётся. Где купить? Можно купить радиодетали через интернет. Я, например, заказывал на AliExpress. В наших интернет-магазинах не всегда удаётся найти нужное.
Главная » Мастерская » Текущая страница
Также Вам будет интересно узнать: