Флюсы для газовой сварки меди
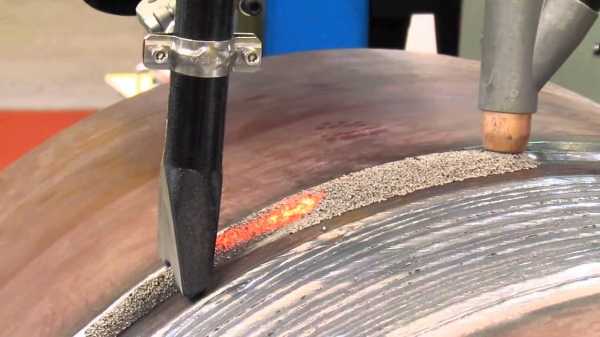
Флюсы имеют важное значение для сварочных работ. Они нужны для очистки кромок от прочной оксидной пленки химическим способом. Эта пленка находится на поверхности меди и значительно усложняет сварку изделий. Сам процесс представляет из себя растворение этой пленки и дальнейшее её включение в шлак с прочими примесями. Подобное соединение уже легко убрать, тем самым повышая качество сварного шва.
Для сварки медных изделий газовым способом обычно применяются кислые флюсы, в них в большом объеме находятся оксиды бора. Они сильно активны химически и имеют хорошую жидкотекучесть.
В составе этих флюсов находится борная кислота (H3BO3), а также бура (Na2B4O7). Это основные важные компоненты. Если толщина свариваемого медного элемента не очень большая, то возможно применение одной лишь буры. В процессе сваривания меди бура реагирует с металлом, что приводит к такой химической реакции:
Na2BO7 = 2NaBO2 + B2O3, и потом:
2NaBO2 + B2O3 + CuO = 2NaBO2*Cu(BO2)2
В итоге образовываются шлаки, которые выходят на поверхность меди.
Если поднять температуру до 140 градусов Цельсия, то борная кислота меняет свои свойства и становится тетраборной кислотой. Это можно описать формулой:
4H3BO3 = 5H2O + H2B4O7
Если продолжать повышать температуру, то в результате образуется борный ангидрид. Происходит это так:
H2B4O7 = 2HBO2 + B2O3
Этот ангидрид бора вступает в реакцию с оксидами меди с формированием легкоплавких солей, которые в виде шлака выступают на поверхность металла в месте образования шва.
Состав основных используемых флюсов для газовой сварки
Компоненты флюса | Номер флюса | |||||||
1 | 2 | 3 | 4 | 5 | 6 | 7 | 8 | |
Бура Na2B4O7 | 100 | 50 | 70 | 50 | 50 | 56 | 75 | 20 |
Борная кислота H3BO3 | 50 | 10 | 35 | — | — | 9 | 80 | |
Поваренная соль NaCl | — | — | 20 | — | — | 22 | 11 | — |
Гидрофосфат натрия Na2HPO4 | — | — | — | 15 | 15 | — | — | — |
Древесный уголь | — | — | — | — | 20 | — | — | — |
Кремниевая кислота H2SiO3 | — | — | — | — | 15 | — | — | — |
Карбонат калия K2CO3 | — | — | — | — | — | 22 | — |
Флюсы под номерами 4 и 5 имеют более сложный состав. При сварке этими видами выделяется свободный фосфор, вода и угарный газ. Фосфор также реагирует с медными оксидами, восстанавливая их из окислов.
Очень важно включать в состав вещества, которые будут не только препятствовать окислению металлов в расплавленном состоянии, но и восстанавливать медь из окислов.
Если внимательно рассмотреть таблицу, то вы придете к выводу, что бура присутствует во всех видах флюсов. Также почти все из них имеют в составе борную кислоту.
Если вы используете для сварки присадочные прутки без легирующих добавок из марки меди М1, то лучше взять флюсы под цифрами 4 или 5.
Для изделий с небольшой толщиной кромок подойдут варианты только с бурой на 100% или борной кислотой и бурой в соотношении 1 к 1. Шестой флюс можно использовать при сварке меди любой толщины. При большой толщине элементов чаще всего используется вариант номер 7 или 3. В первом случае нужно будет заменить карбонат калия на карбонат натрия, а во втором хлорид натрия на фторид натрия. Шов после сварки обязательно нужно проковать.
Все варианты флюсов производятся в виде пасты или порошка, которые возможно растворить в спирте или просто в воде.
atl-met.ru
для чего нужны и как пользоваться
Бура – это порошок, который добавляется в так называемые высокотемпературные флюсовые металлических изделий. Температура плавления буры довольно высокая – 700 – 900°С.
Бура для пайки очень удобна в техническом использовании, все ее свойства хорошо известны, удобны и описаны в специальном регулирующем документе – ГОСТе 8429-77.
Где и как бура применяется?
С химической точки зрения – это соль натрия со сложным названием «декагидрат тетрабората натрия». С ее участием в роли активного элемента в защитной флюсовой смеси проводится соединение самых разных металлов, вплоть до сложных и капризных сплавов, к примеру, меди.
По данной технологии для соединения используются дополнительные металлические припои, они также могут быть разного состава.
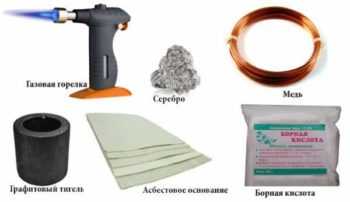
Инструменты и расходные материалы для пайки.
При высокой температуре бура начинает плавиться, вследствие чего происходит очистка свариваемых поверхностей с одновременным растворением окислов в раскаленной флюсовой смеси.
Суть этого процесса – образование солей с их последующей поверхностной кристаллизацией. Данный кристаллический налет после процесса сварки легко убирается.
Как готовится флюс с бурой?
Флюсовая борная смесь для использования в работе с металлами имеет свои особенности и готовится следующим образом: к примеру, буру для пайки латуни перемешивают с борной кислотой в равных пропорциях.
Смесь следует хорошенько перетереть в специальной химической посуде, а затем выпарить всю жидкость для финишного сухого остатка. Затем в полученное вещество добавляются соли фтора и хлора. В итоге формируется активный флюс, который станет отличным помощником в нагревании металлических деталей самого разного типа.
Достоинства применения буры в работе с металлами
Особенно ярко эти достоинства проявляются в процессах , который часто являются важными составными частями современных трубопроводов. Такие технологии сейчас в большой моде.
Они используются как при соединения новых труб, так и при качественном ремонте старых трубопроводов, бывших в эксплуатации в течение долгого времени.
Самая главная роль – это удаление оксидной пленки с металлической поверхности и активация растекания жидкого припоя по поверхности деталей.
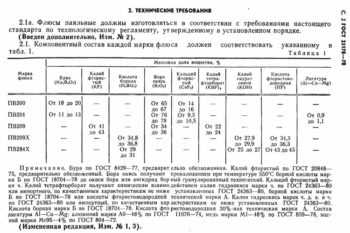
Технические требования к флюсам.
Вот ее технические преимущества:
- Слиянию поддаются детали из металла в любом, даже самом «неудобном» сочетании.
- Соединения выходят прочными и надежными даже между металлами и неметаллическими материалами.
- Работу можно начинать с металлами, имеющими любую исходную температуру.
- С помощью данной технологии детали можно не только соединять, но и эффективно разъединять – их можно без проблем распаять.
- Отличие пайки от классической сварки в том, что основной металл не плавится, и поэтому нет явления под названием «коробление». В результате детали никак не деформируются.
- Бура помогает эффективной сцепке припоя с металлическими поверхностями.
- Техническая бура незаменима при способе, который называется «капиллярной пайкой»: она влияет на ее производительность.
- Паяные соединения характеризуются высоким качеством и долговечностью.
Этапы пайки с бурой
Весь процесс состоит из последовательных этапов, выполнение которых является обязательным:
- Тщательная подготовка поверхностей заготовок перед нагревом.
- Чистка проводится для избавления от окисных пленок, здесь как раз и нужна техническая бура.
- Паяльной лампой производится нагрев свариваемых поверхностей до нужной температуры.
- В пространство между деталями вводится разогретый металлический припой в жидком состоянии.
- Суть соединения – объединение основного металла с жидким металлическим припоем в хорошо разогретом состоянии.
Пайка медных труб с использованием буры
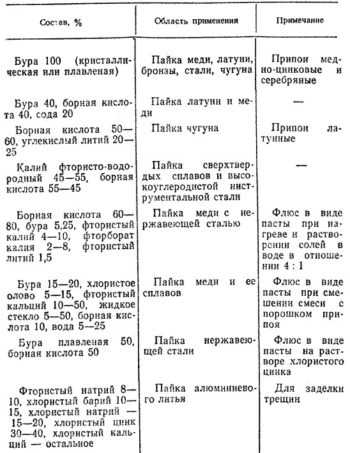
Таблица применения буры.
Для начала нужно запастись необходимыми инструментами и материалами:
- паяльная лампа или газовая горелка;
- специальный припой, выбранный с учетом природы металлов, которые нужно спаять;
- бура с оптимальными свойствами согласно ГОСТу 8429-77;
- металлические щетки для очистки деталей;
- инструмент для резки металла;
- кисти для покрытия деталей флюсовым слоем.
Отдельного предупреждения заслуживает выбор газовой горелки. Дело в том, что эти приспособления предлагаются на рынке в огромных количествах и в разных моделях.
Модным приспособлением в газовых горелках является система автоматического пьезорозжига.
Наш совет: горелку с ним можно выбрать только при полной уверенности, что продукция произведена известным и солидным предприятием. Если такой уверенности нет, лучше купить классическую модель высокого качества.
А теперь основные этапы процесса пайки с использованием буры для соединения двух медных труб:
- Тщательная чистка поверхностей внутри труб специальными щетками с металлической щетиной.
- Теперь чистка наружных поверхностей труб с помощью шкурки.
- Нанесение технической буры с помощью кисти.
- Стыковка труб, которые покрыты флюсовым слоем, друг с другом.
- Разогрев деталей газовой горелкой. Действие пламени должно длиться не меньше 20-ти секунд.
- На рабочий участок вводится припой, который также расплавляется под действием горелки. Припой наносится максимально равномерным слоем.
Контроль качества соединения с использованием флюса из буры проводится разными методами: разрушающими и неразрушающими. Чаще всего вполне достаточно внешнего осмотра для определения возможных дефектов. Это делать можно даже с лупой.
tutsvarka.ru
Флюсы для пайки меди и ее сплавов
В процессе нагрева деталей для пайки поверхность их и припоя под действием кислорода воздуха и температуры интенсивно окисляется. Образующая окисная пленка препятствует жидкому припою войти в контакт с чистым металлом деталей, припой не смачивает его и не затекает в зазоры.
Флюсы, используемые при пайке, предотвращают окисление металлов и очищают их поверхность от окисной пленки. Очень важно, чтобы разница в температурах плавления флюса и припоя была наибольшая. Тогда по мере нагрева сначала плавится флюс и, растекаясь на поверхности металла, прежде всего изолирует его от кислорода воздуха, прекращая дальнейшее образование окисной пленки.
Кроме этого, к моменту плавления припоя флюс растворит ранее образовавшуюся на поверхности металла окисную пленку и создаст условия для получения высококачественного паяного соединения. Это особенно важно при пайке твердыми припоями, когда соединяемые детали приходится нагревать до температуры 750—850°С.
Однако на практике до последнего времени эти условия не соблюдались. Так, при пайке стальных и латунных деталей стандартными серебряными припоями марок ПСр25, ПСр45 и ПСр70 с температурами плавления 720—780° С, обычно в качестве флюса использовалась бура, плавящаяся при 741°С. Отсутствие разницы в температурах плавления флюса и припоев в этом случае приводило к тому, что металл покрывался толстым слоем окисной пленки, затрудняющей пайку и резко снижающей ее качество.
Более того, удаление стекловидной пленки остатков буры с паяных швов представляло значительные технологические трудности. Поэтому теперь для пайки твердыми серебряными припоями деталей из меди, ее сплавов и в соединениях медных сплавов со сталью разработаны и широко применяются взайен буры более совершенные флюсы, марки и состав которых приведены е табл. 2.
Достоинства этих флюсов состоят в том, что они очень активно растворяют окисные пленки, имеют по сравнению с бурой резко пониженную температуру плавления, а остатки их легко удаляются с паяных узлов отмывкой в горячей воде или в 10-про — центном водном растворе лимонной кислоты.
Таблица 2 Флюсы для пайки меди и ее сплавов со сталью
|
Кроме этого, флюсы № 209 и 284 весьма эффективны при пайке серебряными припоями медных сплавов с жаропрочными, а также с конструкционными и нержавеющими сталями.
Наряду с применением известных спиртово-канифолевых флюсов для пайки деталей аппаратуры мягкими оловянно-свинцовыми, оловянно-цинк-кадмиевыми или свинцово-серебряными припоями с температурами плавления от 150 до 300°С в последние годы освоен ряд новых некоррозионных флюсов.
Среди этих флюсов очень эффективными являются флюсы ЛТИ, незначительно отличающиеся по своему составу и эффективности.
Наибольшее распространение имеет флюс известный под маркой ЛТИ-120, представляющий собой спиртовый раствор канифоли с добавками триэтаноламина и солянокислого диэтиламина.
Состав флюса ЛТИ-120, %:
Спирт этиловый 90—95% (ГОСТ 5962 — 51) . . . 63—74
Канифоль (ГОСТ 797 — 41)………………………………………….. 20—25
Диэтиламин солянокислый (ВТУ МХП 326—352) . 3—5
Триэтаноламин (ВТУ МХП 1931 —49) …. 1—2
Действие этого флюса состоит в том, что при температуре пайки происходит частичное разложение хлоргидрата амина с выделением активного хлористого водорода, который весьма энергично раскисляет окисные пленки ряда металлов.
Избыток хлористого водорода, незанятый в реакции раскисления, мгновенно связывается триэтаноламином, благодаря чему и предотвращается коррозия паяных соединений.
Остатки флюса легко удаляются с места пайки ветошью или тампоном ваты, смоченных в спирте или ацетоне. Правильно приготовленный флюс и его остатки после пайки должны давать нейтральную реакцию с лакмусом.
Флюс ЛТИ-120 применяется для пайки меди, ее сплавов, углеродистых и нержавеющих сталей, пермаллоя, а также никелированных, оцинкованных и серебряных деталей приборов.
Однако использование флюсов ЛТИ и других спиртово-кани — фолиевых флюсов при пайке погружением в производстве изде — 18
лий с печатными схемами приводит к ряду технологических трудностей.
Хорошее качество пайки достигается лишь при условии подсушивания флюса, нанесенного на печатную плату, перед ее погружением в припой.
Отмывка остатков и продуктов разложения флюса, а также удаление бумажной маски после пайки плат связаны со значительными затратами времени.
Наконец, операция удаления смолообразных продуктов разложения флюса связана с промывкой плат в очень летучих растворителях (ацетоне или спиртово-бензиновых смесях). Поэтому для пайки плат с печатными схемами методом окунания в расплавленный припой к флюсам, помимо хороших флюсующих свойств, некоррозионности и невлияния на диэлектрические свойства материала плат, предъявляются дополнительные требования:
флюсы должны обеспечить хорошее качество пайки без подсушивания их перед пайкой;
в составе флюсов не должно быть смолообразующих веществ, которые затрудняют удаление бумажных масок и увеличивают время на отмывку плат после пайки;
остатки и продукты разложения флюсов должны легко растворяться в теплой воде без применения сильно летучих растворителей.
Вот почему при пайке плат с печатными схемами в настоящее время взамен спиртово-канифольных и флюса ЛТИ-120 стали применять более технологичные флюсы, не содержащие в своем составе канифоли.
В частности, при освоении технологии. пайки изделий с печатными схемами проверен и рекомендуется для промышленного использования флюс № 6 следующего состава:
салициловая кислота………………………… 4%
триэтаноламин………………………………….. 1,5%
спирт этиловый…………………………………. остальное
ного флюса:
спирт этиловый……………………………………………………………………. 80 г
глицерин 96%……………………………………………………………………….. 20 г
уксусная кислота 45%………………………………………………………… 20 г
соляная кислота 20%……………………………………………… 1,5 г
При пайке плат, изготовленных способом травления фольги — рованного гетинакса, удовлетворительные результаты дает не
ние компонентов:
стеарин………………………………………………………………………………………. 30
парафин……………………………………………………………………………………… 68
триэтаноламин…………………………………………………………………………… 2
hssco.ru
Флюс для рафинирования меди и сплавов на медной основе
Изобретение относится к области металлургии цветных металлов, касается флюсов, применяемых при выплавке меди и медных сплавов. Предложенный флюс для рафинирования меди и сплавов на медной основе, содержащий полиметафосфат щелочного металла в качестве шлакообразователя и твердый окислитель, согласно изобретению дополнительно содержит в качестве твердого окислителя оксид марганца при следующем соотношении компонентов во флюсовой смеси, мас.%: оксид марганца 20-70, полиметафосфат щелочного металла 30-80, причем в качестве оксида марганца он содержит двуокись марганца, или полуторную окись марганца, или их смесь; причем в качестве твердого окислителя он содержит природный минерал, содержащий оксид марганца. В качестве природного минерала он содержит пиролюзит, или браунит, или их смесь. Обеспечивается повышение степени рафинирования по железу, марганцу, никелю и улучшается отделение шлака от расплава чистого металла. 3 з.п. ф-лы, 1 табл.
Изобретение относится к области металлургии цветных металлов, касается, в частности, флюсов и может быть использовано, например, в процессе выплавки меди и медных сплавов, при переработке лома и отходов меди и сплавов на ее основе.
Одним из основных методов удаления металлических примесей из медьсодержащих отходов при выплавке меди и сплавов является окислительное рафинирование с использованием флюсов. Сущность окислительного рафинирования заключается в том, что на первой стадии рафинирования происходит окисление металлических примесей с образованием соответствующих оксидов (FeO, NiO, MnO и др.). Предпочтительней окисляются те металлические примеси, которые имеют большее сродство к кислороду. Реакции окисления металлов при температурах плавления медьсодержащих отходов являются обратимыми. Для сдвига равновесия реакции окисления металла в сторону образования оксида вводят вещества, способные образовывать с оксидами устойчивые соединения. Это приводит к уменьшению скорости обратной реакции — восстановление окисленного металла до элементарного состояния. Наиболее часто для этой цели используют двуокись кремния, которая взаимодействует с оксидами металлов с образованием плавких силикатов, например: FeOSiO2, MnOSiO2, NiOSiO2 и других [1]. В качестве окислителя используют как газообразные окислители — кислород (кислород воздуха), так и твердые окислители. Известен состав флюса, применяемый при переплавке меди и медьсодержащих отходов и содержащий 96 % медной окалины + 4% SiO2 или 30 % NаNО3+45% медной окалины + 25% SiO2 [2]. Основой рафинирующего флюса является двуокись кремния. Медная окалина, состоящая в основном из Сu2O, является окислителем для большинства примесей металлов (Fe, Mn, Cr, Ni и др.), переводя их в окисленное состояние. Нитраты также являются окислителями, а возникающий при их разложении оксид натрия образует легкоплавкий силикат. По своей сущности и достигаемому эффекту наиболее близким к заявляемому является состав флюса [3], описанный в способе плавки, по которому металлические отходы из сплавов на основе меди плавят в индукционной печи с добавлением рафинирующих флюсов, имеющих температуру ликвидуса ниже точки плавления металлических отходов. В качестве рафинирующих флюсов используют полиметафосфаты щелочных металлов и смеси полиметафосфатов щелочных металлов и оксидов меди. Здесь примеси металлов окисляются и образующиеся катионы металлов взаимодействуют с полиметафосфатами щелочных металлов. Благодаря прочности образующихся соединений равновесие смещается в сторону шлакования примесей и достигаются высокие значения коэффициентов распределения примесей металлов. Оксиды меди в составе рафинирующего флюса выполняют роль окислителя, интенсифицируя процесс перевода примесей металлов в окисленное состояние. Недостатком ближайшего аналога является низкая эффективность удаления примесей металлов, имеющих термодинамические показатели (сродство к кислороду, свободная энергия образования оксидов), близкие к меди, например никель, кобальт, висмут, железо и др., это обуславливает относительно низкие коэффициенты очистки от железа, никеля при высоком содержании данных элементов в исходном сырье, в частности при переплавке отходов медно-никелевых сплавов МНЖц-5-1-1, МНЖц-33-2. Одной из причин недостаточной степени рафинирования при использовании ближайшего аналога является относительно невысокий окислительно-восстановительный потенциал применяемого окислителя — оксидов меди. Так, стандартный потенциал реакций Сu+—>Сu и Сu2+—>Сu составляет соответственно + 0,531 В и + 0,345 В [4] . Данный фактор не позволяет смещать равновесие реакции окисления металлических примесей никеля, кобальта, железа и др. в сторону образования оксидов в необходимой степени. Недостатком ближайшего аналога является то, что после окислительного рафинирования, осуществляемого при избытке оксидов меди по отношению к металлическим примесям, необходимо проводить операции раскисления для восстановления растворенных в меди ионов Сu+. Это обусловлено высокой растворимостью Сu2О в металлической меди (при 1200oС в расплаве меди растворяется 12,4% Сu2О [2]. Задача, решаемая изобретением, заключается в повышении рафинирующей способности флюса при получении меди и сплавов на ее основе в процессе переплавки медьсодержащих отходов. Сущность изобретения состоит в том, что во флюсе для рафинирования меди и сплавов на медной основе, включающем шлакообразователь — полиметафосфат щелочного металла и твердый окислитель, предложено в качестве твердого окислителя использовать оксид марганца при следующем соотношении его со шлакообразователем, мас.%: Оксид марганца — 20 — 70 Полиметафосфат щелочного металла — 30 — 80 Достигнутый технический результат заключается в повышении рафинирующей способности флюса при получении меди и сплавов на ее основе в процессе переплавки медьсодержащих отходов. Это обеспечивается за счет использования в качестве оксида марганца полуторной окиси марганца или их смеси. Кроме того, предложено в качестве твердого окислителя использовать природный минерал, содержащий оксид марганца, например пиролюзит, или браунит, или их смесь. По сравнению с наиболее близким аналогом использование при плавке медьсодержащих отходов в качестве рафинирующего флюса смеси из полиметафосфатов щелочных металлов и окислителя — оксидов марганца (МnO2, Мn2О3), позволяет повысить степень рафинирования по железу, никелю в 1,5 раза. Кроме того, продукты восстановления МnО2 и Мn2О3 не приводят к ухудшению качества получаемого слитка, т. к. восстановление MnO2 и Мn2O3 идет до двухвалентного марганца (Мn2+). Двухвалентный марганец связывается полифосфатами с образованием прочных соединений и остается в фазе шлака. Дальнейшее восстановление его до марганца не происходит, т.к. этому препятствуют термодинамические показатели марганца (свободная энергия образования оксида марганца) и связывание двухвалентного марганца в виде прочных соединений с полифосфатами. Благодаря этому он практически полностью ошлаковывается и не загрязняет расплав металла. Возможность использования оксидов марганца в качестве окислителя в составе рафинирующих флюсов на основе полиметафосфатов щелочных металлов при плавке медьсодержащих отходов не описана в литературе и не следует явным образом из уровня развития металлургической науки и техники. В настоящее время разработка (выбор) эффективных окислителей, удовлетворяющих требованиям, предъявляемым к флюсам для окислительного рафинирования меди и медных сплавов, может осуществляться только экспериментальным путем. Пример конкретного выполнения. Для проведения экспериментов использовали образцы из медноникелевого сплава МНЖМц 5-1-1, загрязненные различными примесями. Плавку осуществляли в тигельной индукционной печи марки ИСТ-0,06. Флюс равномерно добавляли в течение всего процесса плавления в количестве 5% от массы металла. В качестве флюсов использовали двуокись кремния с оксидами меди, полиметафосфаты щелочных металлов с оксидами меди, полиметафосфаты щелочных металлов с оксидами марганца (МnО2, Мn2О3), полиметафосфаты щелочных металлов с добавкой оксидов марганца и двуокиси кремния. В качестве оксидов меди использовали медную окалину, двуокиси кремния — просеянный кварцевый песок с размерами частиц не более 2 мм. В качестве полиметафосфатов использовали гексаметафосфат натрия и пирофосфат натрия. По окончании плавки шлак удаляли с поверхности расплава металла и сливали металл в изложницу. Удаленный шлак и слиток металла анализировали на содержание примесей металлов. Для количественной оценки эффективности процесса очистки металла от примесей использовали показатель R-степень рафинирования, равный отношению начальной концентрации примеси в металле к конечной концентрации примеси в слитке. Результаты экспериментов сведены в таблицу. Из результатов экспериментов видно, что наименьшая очистка наблюдается при использовании в качестве флюса смеси из двуокиси кремния и оксидов меди (поз.1). Применение флюсов на основе полиметафосфатов щелочных металлов и оксидов меди существенно повышает степень рафинирования по железу и марганцу в 10-50 раз (поз.2). Отсутствие окислителя снижает степень рафинирования (поз.3), а добавление окислителя и повышение вязкости системы за счет присутствия двуокиси кремния приводит к увеличению степени рафинирования (поз.4). Наибольшая степень рафинирования по железу, марганцу и никелю наблюдается при использовании флюсов из смеси полиметафосфатов щелочных металлов с оксидами марганца МnO2 и Мn2О3 (поз.5-12), причем более высокая очистка наблюдается при дополнительной добавке к флюсу двуокиси кремния (поз.9-12). СПИСОК ЛИТЕРАТУРЫ. 1. Взаимодействие расплавленного металла с газом и шлаком. Попель С.И., Никитин Ю.П. и др. Свердловск, изд. УПИ, 1975, 179 с. 2. Металлургия вторичных цветных металлов. Учебник для вузов. Худяков И. Ф., Дорошкевич А.П., Карелов С.В., М.: Металлургия, 1987, 528 с., 196-197 с. 3. Патент России 2004608 «Способ утилизации металлических отходов из сплавов на основе меди, загрязненных радионуклидами». Нестер А.Т., Паранин А.А. 4. Лурье Ю. Ю. Справочник по аналитической химии. 5-е изд. Пер. и дополненное, М.: Химия, 1979, 480 с., 353, 358 с.Формула изобретения
1. Флюс для рафинирования меди и сплавов на медной основе, содержащий полиметафосфат щелочного металла в качестве шлакообразователя и твердый окислитель, отличающийся тем, что в качестве твердого окислителя он содержит оксид марганца при следующем соотношении компонентов во флюсовой смеси, мас. %: Оксид марганца — 20-70 Полиметафосфат щелочного металла — 30-80 2. Флюс по п. 1, отличающийся тем, что в качестве оксида марганца он содержит двуокись марганца, или полуторную окись марганца, или их смесь. 3. Флюс по любому из п. 1 или 2, отличающийся тем, что в качестве твердого окислителя он содержит природный минерал, содержащий оксид марганца. 4. Флюс по п. 3, отличающийся тем, что в качестве природного минерала он содержит пиролюзит, или браунит, или их смесь.РИСУНКИ
Рисунок 1findpatent.ru
Флюсы для пайки — Литература — Полезные материалы — Каталог статей
Флюсы для пайки
ФЛЮСЫ Нейтральные флюсы: Канифоль и флюсы, приготовляемые на ее основе. Канифоль при пайке играет двойную роль: очищает поверхность от окислов и защищает ее от окисления. При температуре 150 С канифоль растворяет окислы свинца, олова и меди, очищая их поверхности при пайке. Очень ценным свойством канифоли является то, что она в процессе пайки не разъедает поверхность. Канифоль применяют при пайке меди, латуни и бронзы.
Флюс спиртоканифольный — (СКФ, он же КЭ, ФКЭ, ФКСп) — простой и эффективный для пайки печатных плат и радиокомпонентов. Состав: спирт 60-70%, канифоль 30-40%, нейтрален, не требует смывки.
ФТС — радиомонтажный флюс, для пайки деталей радиоаппаратуры и печатных плат, водосмываемый. Остатки флюса легко удаляются водой или спиртовым раствором.
ЛТИ 120 — флюс радиомонтажный, нейтральный. Состав: этиловый спирт (66 — 73%), канифоль (20 — 25%), активаторы — солянокислый анилин (3 — 7%), триэтаноламин (1 — 2%). Остатки флюса смывать не обязательно, при желании легко смываются спиртом, ацетоном и т.п.
ТАГС — радиомонтажный, глицериновый. Для пайки элементов радиомонтажа; а также для пайки углеродистой стали, никеля, меди и других цветных металлов легкоплавкими припоями (150-320 С). Водосмываемый. При пайке печатных плат имеет остаточное сопротивление. Требует обязательной смывки водой или спиртом!
Активные флюсы:
Паяльная кислота — для пайки углеродистых сталей, меди, никеля и их сплавов. Представляет собой водный раствор хлорида цинка (15-40%). В практике радиомонтажника не применяется, так как вызывает коррозию спая и разрушение изоляции проводов.
ЗИЛ-1 — активный флюс для пайки стали, железа, чугуна припоями с большим содержанием свинца. Температурный интервал пайки 180-400 С. Содержит хлорид цинка, хлорид олова, хлорид меди и соляную кислоту. Для пайки радиокомпонентов не применяется!
ФИМ — бесканифольный активный флюс, лучше всего подходит для пайки нержавеющих сталей, в остальном аналогичен паяльной кислоте. Состав: ортофосфорная кислота (плотность 1.7, 16%), спирт этиловый (3.7%), остальное вода. Температурный интервал пайки 290-350°C, после пайки обязательно смыть водой. В практике радиолюбителя применим также при пайке нихрома.
ВТС — активный флюс для пайки меди, серебра, золота и их сплавов. Изготовлен на основе органических кислот, благодаря чему действует в основном на окислы и загрязнения а не на сам металл. Состав: 63% технического вазелина, 6,3% триэтаноламина, 6,3% салициловой кислоты и этилового спирта. Остатки флюса удаляют протиркой детали спиртом или ацетоном.
Ф38М — высокоактивный флюс. В отличии от большинства флюсует нихром, констант, манганин, большинство нержавеющих сталей и медных сплавов (бронзы, латуни). Остатки флюса легко смываются водой. Состав: ортофосфорная кислота, глицерин, этиленгликоль, диэтиламин солянокислый.
Классификация флюсов импортного производства
Классификация флюсов импортного производства (rosin — англ. канифоль)
R (rosin) представляет собой чистую канифоль в твердом виде или растворенную в спирте, этилацетате, метилэтилкетоне и подобных растворителях. Это наименее активная группа флюсов, поэтому ее используют для пайки по свежим поверхностям или по поверхностям, которые были защищены от окисления в процессе хранения. В соответствии с рекомендациями отечественного отраслевого стандарта ОСТ4ГО.033.200, эта группа флюсов не требует удаления их остатков после пайки.
RMA (rosin mild activated — слегка активированная канифоль) — группа смолосодержащих флюсов с различными комбинациями активаторов: органическими кислотами или их соединениями. Эти флюсы обладают более высокой активностью по сравнению с типом R. Предполагается, что в процессе пайки активаторы испаряются без остатка. Но очевидно, что процесс пайки должен быть гарантированно завершен полным испарением активаторов. Такие гарантии может обеспечить только машинная пайка с автоматизацией температурно-временных процессов (температурного профиля пайки).
RA (rosin activated — активированная канифоль). Эта группа флюсов предназначена для промышленного производства электронных изделий массового спроса. Несмотря на тот факт, что данный вид флюса отличается более высокой активностью по сравнению с упомянутыми выше, он преподносится рекламой как не требующий отмывки. Поскольку его остатки якобы не проявляют видимой коррозионной активности.
SRA (super activated rosin — сверхактивированная канифоль). Эти флюсы были созданы для нестандартных применений в электронике. Они могут использоваться для пайки никелесодержащих сплавов, нержавеющих сталей и материалов типа сплава ковар. Флюсы типа SRA очень агрессивны и требуют тщательной отмывки при любых обстоятельствах, поэтому их использование в электронике строго регламентировано.
No clean (не требует смывки). Эта группа специально создана для процессов, где нет возможности использовать последующую отмывку плат или она затруднена по каким-то причинам. Основное отличие этой группы состоит в крайне малом количестве флюса на плате по окончании процесса пайки/ Пайка алюминия. Алюминий в обычных условиях покрыт плотной оксидной пленкой, препятствующей пайке. Если удалить эту пленку и защитить поверность алюминия от окисления, то пайка происходит без затруднений. Лучше всего паять чистым оловом или припоем, содержащим не менее 60% олова, удобно использовать обычный ПОС-61. Следует принять во внимание высокую теплопроводность алюминия и брать паяльник достаточной мощности. Для пайки тонкого алюминия достаточна мощность паяльника 50 вт, для алюминия толщиной 1 мм и более желателен паяльник мощностью 90 вт. Пайка без флюса На алюминий в месте пайки наносится жидкое минеральное масло и поверхность алюминия под слоем масла зачищают скребком или лезвием ножа для удаления пленки окиси. Припой наносится хорошо нагретым паяльником. Еще лучше применять оружейное масло; хорошее и удовлетворительное качество пайки получается при использовании минерального масла для швейных машин и точных механизмов, вазелинового масла. При пайке алюминия толщиной 2 мм место пайки перед нанесением масла желательно предварительно прогреть паяльником. Проще всего использовать специальные флюсы.
Ф61А — флюс для пайки алюминия. Высокоактивный флюс на основе фторборатов, предназначен для лужения и пайки деталей и поверхностей из алюминия и его сплавов. Пайка производится припоями оловянно-свинцовой группы с содержанием олова более 60% (а лучше всего паять чистым оловом) при температуре 250-350 градусов.
Ф-34 Флюс для пайки алюминия и других лёгких сплавов. Остатки удаляются водой. Флюс средней активности и невысокой кислотности остатков.
Ф-64 Флюс для пайки алюминия, других лёгких сплавов бериллиевой бронзы и др. Остатки тщательно удаляются водой. Флюс повышенной активности. Алюминий даже не приходится зачищать от плотной окисной плёнки. Известен также вариант пайки с использованием флюса, состоящего из 2-3г иодида лития и 15-20 г стеариновой кислоты.
zazsila.ru
флюс для рафинирования меди и сплавов на медной основе — патент РФ 2185454
Изобретение относится к области металлургии цветных металлов, касается флюсов, применяемых при выплавке меди и медных сплавов. Предложенный флюс для рафинирования меди и сплавов на медной основе, содержащий полиметафосфат щелочного металла в качестве шлакообразователя и твердый окислитель, согласно изобретению дополнительно содержит в качестве твердого окислителя оксид марганца при следующем соотношении компонентов во флюсовой смеси, мас.%: оксид марганца 20-70, полиметафосфат щелочного металла 30-80, причем в качестве оксида марганца он содержит двуокись марганца, или полуторную окись марганца, или их смесь; причем в качестве твердого окислителя он содержит природный минерал, содержащий оксид марганца. В качестве природного минерала он содержит пиролюзит, или браунит, или их смесь. Обеспечивается повышение степени рафинирования по железу, марганцу, никелю и улучшается отделение шлака от расплава чистого металла. 3 з.п. ф-лы, 1 табл. Изобретение относится к области металлургии цветных металлов, касается, в частности, флюсов и может быть использовано, например, в процессе выплавки меди и медных сплавов, при переработке лома и отходов меди и сплавов на ее основе. Одним из основных методов удаления металлических примесей из медьсодержащих отходов при выплавке меди и сплавов является окислительное рафинирование с использованием флюсов. Сущность окислительного рафинирования заключается в том, что на первой стадии рафинирования происходит окисление металлических примесей с образованием соответствующих оксидов (FeO, NiO, MnO и др.). Предпочтительней окисляются те металлические примеси, которые имеют большее сродство к кислороду. Реакции окисления металлов при температурах плавления медьсодержащих отходов являются обратимыми. Для сдвига равновесия реакции окисления металла в сторону образования оксида вводят вещества, способные образовывать с оксидами устойчивые соединения. Это приводит к уменьшению скорости обратной реакции — восстановление окисленного металла до элементарного состояния. Наиболее часто для этой цели используют двуокись кремния, которая взаимодействует с оксидами металлов с образованием плавких силикатов, например: FeOSiO2, MnOSiO2, NiOSiO2 и других [1]. В качестве окислителя используют как газообразные окислители — кислород (кислород воздуха), так и твердые окислители. Известен состав флюса, применяемый при переплавке меди и медьсодержащих отходов и содержащий 96 % медной окалины + 4% SiO2 или 30 % NаNО3+45% медной окалины + 25% SiO2 [2]. Основой рафинирующего флюса является двуокись кремния. Медная окалина, состоящая в основном из Сu2O, является окислителем для большинства примесей металлов (Fe, Mn, Cr, Ni и др.), переводя их в окисленное состояние. Нитраты также являются окислителями, а возникающий при их разложении оксид натрия образует легкоплавкий силикат. По своей сущности и достигаемому эффекту наиболее близким к заявляемому является состав флюса [3], описанный в способе плавки, по которому металлические отходы из сплавов на основе меди плавят в индукционной печи с добавлением рафинирующих флюсов, имеющих температуру ликвидуса ниже точки плавления металлических отходов. В качестве рафинирующих флюсов используют полиметафосфаты щелочных металлов и смеси полиметафосфатов щелочных металлов и оксидов меди. Здесь примеси металлов окисляются и образующиеся катионы металлов взаимодействуют с полиметафосфатами щелочных металлов. Благодаря прочности образующихся соединений равновесие смещается в сторону шлакования примесей и достигаются высокие значения коэффициентов распределения примесей металлов. Оксиды меди в составе рафинирующего флюса выполняют роль окислителя, интенсифицируя процесс перевода примесей металлов в окисленное состояние. Недостатком ближайшего аналога является низкая эффективность удаления примесей металлов, имеющих термодинамические показатели (сродство к кислороду, свободная энергия образования оксидов), близкие к меди, например никель, кобальт, висмут, железо и др., это обуславливает относительно низкие коэффициенты очистки от железа, никеля при высоком содержании данных элементов в исходном сырье, в частности при переплавке отходов медно-никелевых сплавов МНЖц-5-1-1, МНЖц-33-2. Одной из причин недостаточной степени рафинирования при использовании ближайшего аналога является относительно невысокий окислительно-восстановительный потенциал применяемого окислителя — оксидов меди. Так, стандартный потенциал реакцийСu+—>Сu и Сu2+—>Сu составляет соответственно + 0,531 В и + 0,345 В [4] . Данный фактор не позволяет смещать равновесие реакции окисления металлических примесей никеля, кобальта, железа и др. в сторону образования оксидов в необходимой степени. Недостатком ближайшего аналога является то, что после окислительного рафинирования, осуществляемого при избытке оксидов меди по отношению к металлическим примесям, необходимо проводить операции раскисления для восстановления растворенных в меди ионов Сu+. Это обусловлено высокой растворимостью Сu2О в металлической меди (при 1200oС в расплаве меди растворяется 12,4% Сu2О [2]. Задача, решаемая изобретением, заключается в повышении рафинирующей способности флюса при получении меди и сплавов на ее основе в процессе переплавки медьсодержащих отходов. Сущность изобретения состоит в том, что во флюсе для рафинирования меди и сплавов на медной основе, включающем шлакообразователь — полиметафосфат щелочного металла и твердый окислитель, предложено в качестве твердого окислителя использовать оксид марганца при следующем соотношении его со шлакообразователем, мас.%:
Оксид марганца — 20 — 70
Полиметафосфат щелочного металла — 30 — 80
Достигнутый технический результат заключается в повышении рафинирующей способности флюса при получении меди и сплавов на ее основе в процессе переплавки медьсодержащих отходов. Это обеспечивается за счет использования в качестве оксида марганца полуторной окиси марганца или их смеси. Кроме того, предложено в качестве твердого окислителя использовать природный минерал, содержащий оксид марганца, например пиролюзит, или браунит, или их смесь. По сравнению с наиболее близким аналогом использование при плавке медьсодержащих отходов в качестве рафинирующего флюса смеси из полиметафосфатов щелочных металлов и окислителя — оксидов марганца (МnO2, Мn2О3), позволяет повысить степень рафинирования по железу, никелю в 1,5 раза. Кроме того, продукты восстановления МnО2 и Мn2О3 не приводят к ухудшению качества получаемого слитка, т. к. восстановление MnO2 и Мn2O3 идет до двухвалентного марганца (Мn2+). Двухвалентный марганец связывается полифосфатами с образованием прочных соединений и остается в фазе шлака. Дальнейшее восстановление его до марганца не происходит, т.к. этому препятствуют термодинамические показатели марганца (свободная энергия образования оксида марганца) и связывание двухвалентного марганца в виде прочных соединений с полифосфатами. Благодаря этому он практически полностью ошлаковывается и не загрязняет расплав металла. Возможность использования оксидов марганца в качестве окислителя в составе рафинирующих флюсов на основе полиметафосфатов щелочных металлов при плавке медьсодержащих отходов не описана в литературе и не следует явным образом из уровня развития металлургической науки и техники. В настоящее время разработка (выбор) эффективных окислителей, удовлетворяющих требованиям, предъявляемым к флюсам для окислительного рафинирования меди и медных сплавов, может осуществляться только экспериментальным путем. Пример конкретного выполнения. Для проведения экспериментов использовали образцы из медноникелевого сплава МНЖМц 5-1-1, загрязненные различными примесями. Плавку осуществляли в тигельной индукционной печи марки ИСТ-0,06. Флюс равномерно добавляли в течение всего процесса плавления в количестве 5% от массы металла. В качестве флюсов использовали двуокись кремния с оксидами меди, полиметафосфаты щелочных металлов с оксидами меди, полиметафосфаты щелочных металлов с оксидами марганца (МnО2, Мn2О3), полиметафосфаты щелочных металлов с добавкой оксидов марганца и двуокиси кремния. В качестве оксидов меди использовали медную окалину, двуокиси кремния — просеянный кварцевый песок с размерами частиц не более 2 мм. В качестве полиметафосфатов использовали гексаметафосфат натрия и пирофосфат натрия. По окончании плавки шлак удаляли с поверхности расплава металла и сливали металл в изложницу. Удаленный шлак и слиток металла анализировали на содержание примесей металлов. Для количественной оценки эффективности процесса очистки металла от примесей использовали показатель R-степень рафинирования, равный отношению начальной концентрации примеси в металле к конечной концентрации примеси в слитке. Результаты экспериментов сведены в таблицу. Из результатов экспериментов видно, что наименьшая очистка наблюдается при использовании в качестве флюса смеси из двуокиси кремния и оксидов меди (поз.1). Применение флюсов на основе полиметафосфатов щелочных металлов и оксидов меди существенно повышает степень рафинирования по железу и марганцу в 10-50 раз (поз.2). Отсутствие окислителя снижает степень рафинирования (поз.3), а добавление окислителя и повышение вязкости системы за счет присутствия двуокиси кремния приводит к увеличению степени рафинирования (поз.4). Наибольшая степень рафинирования по железу, марганцу и никелю наблюдается при использовании флюсов из смеси полиметафосфатов щелочных металлов с оксидами марганца МnO2 и Мn2О3 (поз.5-12), причем более высокая очистка наблюдается при дополнительной добавке к флюсу двуокиси кремния (поз.9-12). СПИСОК ЛИТЕРАТУРЫ. 1. Взаимодействие расплавленного металла с газом и шлаком. Попель С.И., Никитин Ю.П. и др. Свердловск, изд. УПИ, 1975, 179 с. 2. Металлургия вторичных цветных металлов. Учебник для вузов. Худяков И. Ф., Дорошкевич А.П., Карелов С.В., М.: Металлургия, 1987, 528 с., 196-197 с. 3. Патент России 2004608 «Способ утилизации металлических отходов из сплавов на основе меди, загрязненных радионуклидами». Нестер А.Т., Паранин А.А. 4. Лурье Ю. Ю. Справочник по аналитической химии. 5-е изд. Пер. и дополненное, М.: Химия, 1979, 480 с., 353, 358 с.
ФОРМУЛА ИЗОБРЕТЕНИЯ
1. Флюс для рафинирования меди и сплавов на медной основе, содержащий полиметафосфат щелочного металла в качестве шлакообразователя и твердый окислитель, отличающийся тем, что в качестве твердого окислителя он содержит оксид марганца при следующем соотношении компонентов во флюсовой смеси, мас. %:Оксид марганца — 20-70
Полиметафосфат щелочного металла — 30-80
2. Флюс по п. 1, отличающийся тем, что в качестве оксида марганца он содержит двуокись марганца, или полуторную окись марганца, или их смесь. 3. Флюс по любому из п. 1 или 2, отличающийся тем, что в качестве твердого окислителя он содержит природный минерал, содержащий оксид марганца. 4. Флюс по п. 3, отличающийся тем, что в качестве природного минерала он содержит пиролюзит, или браунит, или их смесь.
www.freepatent.ru
Флюс для пайки меди и ее сплавов
Использование: пайка меди и ее сплавов . Сущность изобретения: флюс содеожит следующие компоненты, мае. % : хлористый аммоний 12 — 14; натрий тетрафторборат 29,2 — 33,5; калий тетрафторборат 10,2 — 11,7; натрий тетраборат 8,8-9,4; хлористый цинк остальное. 2 табл.
СОЮЗ СОВЕТСКИХ
СОЦИАЛИСТИЧЕСКИХ
РЕСПУБЛИК (я)з В 23 К 35/363
ЕТЕНИ
ГОСУДАРСТВЕННЫЙ КОМИТЕТ
ПО ИЗОБРЕТЕНИЯМ И ОТКРЫТИЯМ
ПРИ ГКНТ СССР
ОПИСАНИЕ ИЗОБР
К АВТОРСКОМУ СВИДЕТЕЛЬСТВУ (21) 4769885/08 (22) 13.12.89 (46) 15.12,92. Бюл. М 46 (71) Таганрогский научно-исследовательский институт связи (72) В. P. Бойко и 3. Я. Псавко (56) ОСТ 4Г0.033.200. Припои и флюсы для пайки.
Лашко С. В., Лашко Н. Ф. Пайка металлов. — Машгиз, 1988, с, 154 — 162.
Изобретение относится к пайке, в частности к составу флюса для конструкционной пайки меди и ее сплавов припоями на основе свинца.
Для ниэкотемпературной пайки меди и ее сплавов применяется большое число органических флюсов, например, ФДФс, ФКСп, ЛТИ-120 и другие, но максимальная температура их активности ограничена обугливанием органических веществ или взаимодействием кислот с металлом и переходом в соли при температурах свыше 270350 С, Флюсы резко теряют активность.
Пайка припоями (при температуре плавления 300 — 350 С) затруднена, а иногда и невозможна.
Из флюсов, имеющих промышленное применение, наиболее приемлем флюс
ФДФс.
Флюс ФДФс относится к коррозионным высокоактивным и рекомендуется для пайки в температурном интервале 200—
350 С. Недостатком флюса ФДФс состава, мас. :
„„5Q„„1780969 А1 (54) ФЛЮС ДЛЯ ПАЙКИ МЕДИ И ЕЕ СПЛАВОВ (57) Использование: пайка меди и ее сплавов. Сущность изобретения: флю содеожит следующие компоненты, мас. : хлористый аммоний 12 — 14; натрий тетрафторборат 29,2 — 33,5; калий тетрафторборат 10,2—
11,7; натрий тетраборат 8,8 — 9,4; хлористый цинк остальное. 2 табл.
Ортофосфорная кислота (плотность 1,7) 20 — 25
Солянокислый диэтиламин 20 — 25
Этиленгликоль Остальное, а является то, что при температурах 270 — ь, 300″С начинается спад активности. Падение активности флюса происходит за счет: а} превращения при температуре свыше
200 С ортофосфорной кислоты в мета- и полифосфорные кислоты, менее активные в С процессах пайки, взаимодействия их с пая- 49 емым металлом с образованием фосфатов и загустевание с переходом в ангидрид; б) разложения зтияенгликоля (Ткнп. +
+200 С) и его связывания с лолифосфорны- в ми кислотами и усиление процесса загустевания в интервале 250 — 300 С: в) взаимодействия диэтиламина солянокислого с основным (паяемым) металлом свыше 220 С, ортофосфорной кислоты и ее. продуктами взаимодействия с паяемыми металлом и припоем.
Все вышеуказанные взаимодействия составных частей флюса а процессе пайки
1780969
12,4 — 14,0
29,2 — 33,5
10,2 — 11,7 приводят к тому, что при температуре свыше 300 С ухудшается затекание припоя в зазор при сохранении достаточно светлой поверхности припоя за счет обугливания органической составляющей флюса и раскисления припоя углеродом, Наиболее близким по технической сущности к заявляемому флюсу является флюс состава, мас. :
KF 20-25
ВгОз 10 — 18
CdCI2 5 — 13
Na CI 4 — 10
Эвтектика
Na2BqQy+ KBF4 45 — 60 предназначенный для высокотемпературной пайки медных и никелевых сплавов.
OH является высокоактивным, водорастворимым, коррозионным с температурным интервалом активности 430 — 650 С и предназначен для пайки припоями с температурами плавления 450 — 650 С. Но этот флюс не приемлем для. пайки свинцовыми припоями с температурой плавления 280—
3500 С.
Целью настоящего изобретения является создание флюса с температурным интервалом активности 330 — 450 С и повышенной термостойкостью в процессе пайки.
Указанная цель достигается тем, что во флюсе (прототип) вместо борного ангидрида, фтористого калия и хлористого кадмия введен тетрафторборат натрия в виде тройной эвтектической смеси NaBF
-Na2BO7. В качестве хлорсодержащих компонентов применена эвтектическая смесь
ZflCI2 — NHaCI при следующих соотношениях компонентов, мас. :
Хлористый аммоний
Борфтористый натрий
Борфтористый калий
Тетраборнокислий натрий 8,2 — 9,4
Хлористый цинк Остальное
Флюс имеет температурный интервал активности 330 — 450 С и обеспечивает качественную пайку свинцовыми припоями марок ПСр1,5, ПСр2,5 и др, меди и ее сплавов; может быть применен при пайке в печах и газовыми горелками.
Введение во флюс тетрафторбората натрия, образующего с тетрафторборатом калия и тетраборатом натрия легкоплавкую эвтектику при соотношении компонентов, мас. : 61,3 NaBF
При содержании эвтектики менее 47,6
$ (NaBF4 — 29,2 ; КВР— 10,2 ; НагВ4078,2 ) снижается активность флюса, при содержании эвтектики более 54,6 (NBF4—
5 33,57; КВЕ4 — 11,7, ИагВ407 — 9,4ß,) флюс расслаивается при расплавлении, усиливается коррозия паяемой поверхности при высокой активности, нарушается плавная линия течения припоя, 10 Хлористый цинк в количестве ЗЗ вЂ” 36,5 мас, $ способствует лучшему смачиванию поверхности меди и медных сплавов расплавленными припоями при сохранении однородности распла ален ного фл юса. П ри l5 более высоком содержании хлористого цин. ка флюс дымит, При содержании ниже 33 течение припоя по металлу становится неравномерным.
При содержании хлористого аммония
20 ниже 12,4 флюс теряет однородность в расплавленном состоянии, выше 14,3 — сильно дымит (разлагается). Нарушение эвтектического соотношения с хлористым цинком (27,3 мас.g Nh5CI, 72,7% ЕпС!г)
25 приводит к ухудшению свойства флюса; при содержании Nh5CI меньше эвтектического — поверхность припоя теряет блеск, что указывает на плохое растекание. При содержании Nh5CI больше эвтектического — флюс
30 дымит, терял однородность при расплавлении.
Для проверки свойств флюса было испытано 5 составов, отличающихся друг от друга содержанием веществ. Составы исс35 ледованных флюсов приведены в табл. 1.
Химический состав вариантов флюса Ф400 представлен в табл, 1, критерием оценки активности данного флюса является коэффициент растекаемо40 сти припоев (ПСр1,5, ПСр2,5, ПСКВи86) по паяемой поверхности и жизнеспособность.
Результаты измерения представлены в табл, 2. Коэффициент растекаемости пропоев на меди и латуни при 400 С дан в табл. 2.
45 Использование предлагаемого флюса обеспечивает качественное выполнение конструкционной пайки в интервале температур 330 — 450ОC с использованием свинцовых припоев, плавящихся при 270- 350 С
50 на изделиях из меди, латуни и других медных сплавов, расширяет возможность ступенчатой пайки при изготовлении сложных деталей, улучшение смачиваемости паяемых по55 верхностей обеспечивает высокое качество пайки, более высокие прочностные характеристики паяного соединения. Так, например, медные стыковые соединения, паяные припоем ПСр1,5 с флюсом ФДФс при 330—
350 С, показали прочность на разрыв 51,78
1780969
Таблица 1
МПа на меди и 55,11 МПа на латуни. Образцы, паяные тем же припоем с предлагаемым флюсом, показали прочность 63,35 МПа на меди и 67,95 МПа на латуни, После коррозионных испытаний прочность паяных соединений соответственно с флюсом ФДФс 45,79 МПа и 35,3 МПа с предлагаемым флюсом 63,15 МПа и 65,12
МПа. Газопламенная пайка припоем ПСр2,5 с применение флюса ФДФс невозможна, а с предлагаемым обеспечивает прочность на меди 52,27 МПа, а на латуни — 56,88 МПа.
Пайка в печи обеспечивает получение менее пористых, более прочных паяных соединений.
Хорошая. растворимость компонентов флюса обеспечивает легкость удаления остатков флюса после облуживания и пайки.
Металлографические исследования показали, что меньшая пористость, лучшее затекание в зазор и больший коэффициент растекаемости обеспечивается при применении флюсов составов 2, 3, 4. Припои имеют сильный металлический блеск, что говорит о хорошем раскислении их поверхности.
Для флюсов составов 2, 3, 4 интервал активности составляет 330 — 450 С. При температурах нагрева выше 450 С флюсы дымят загустевают, а паяемая поверхность меди и припоя окисляется, Разработанный флюс относится к водорастворимым, коррозионным. Остатки флюса легко удаляются после пайки промывкой в горячей и холодной воде.
Предлагаемый флюс обеспечивает качественную пайку меди и ее сплавов свинцо5 во-серебрянными припоями в интервале температур 330 — 450 С в течение 10 — 15 мин.
Технико-экономический эффект при применении изобретения выражается а
10 получении качественных паяных соедине ний при использовании припоев марок
ПСр1,5, ПСр2,0, ПСр2,5, иСр3 и повышении срока службы изделий при эксплуатации в интервале температур 200-270 С, повыше15 нии коррозионной стойкости паяных соединений, Формула изобретения
Флюс для пайки меди и ее сплавов, со20 держащий эвтектическую смесь хлоридов цинка иаммония,отличающийся тем, что, с целью обеспечения достижения температурного интервала активности 330—
450 С и повышения термостойкости флюса
25 в процессе пайки, он дополнительно содержит эвтектическую смесь тетрафторборатов калия, натрия и тетрабората натрия при следующем соотношении компонентов, мас.,,ь:
Хлористый аммоний 12,4 — 14,0
30 Натрий тетрафторборат 29;2 — 33,5
Калий тетрафторборат 10,2 — 11,7
Натрий тетраборат 8,8 — 9,4
Хлористый цинк Остальное
1780969
Таблица 2
Составитель B. Бойко
Редактор С. Кулакова ТехредМ.Моргентал Корректор С. Патрушева
Заказ 4239 Тираж Подписное
ВНИИПИ Государственного комитета по изобретениям и открытиям при ГКНТ СССР
113035, Москва, Ж-35, Раушская наб., 4/5
Производственно-издательский комбинат «Патент», r, Ужгород, ул.Гагарина, 101
findpatent.ru