Устройство, работа поршневого компрессора
В этой статье мы рассмотрим устройство и работу поршневого компрессора, который чаще всего применяется в пневматической системе автосервисов и шиномонтажей.
Что же такое компрессор? – по своему устройству это машина, предназначенная для сжатия и транспортировки газов с повышением давления на соотношение более чем 1,1. В наше время область применения и работа поршневых компрессоров очень широка, они необходимы на всех предприятиях, где в качестве источника энергии используют сжатый воздух. Компрессор можно встретить на заводах, газозаправочных станциях, автосервисах, медицинских учреждениях и даже мастерских по ремонту обуви.
На сегодняшний день наиболее распространенными типами устройств являются поршневые и винтовые компрессоры. Так как винтовые компрессоры имеют более высокую стоимость, то на небольших предприятиях, в том числе и СТО, широко применяются в работе поршневые компрессоры. Потребителями сжатого воздуха в автосервисе служат пневмогайковерты, пневмодрели, краскопульты, шиномонтажные станки, установки вакуумного отбора масла и т.
Устройство поршневого компрессора
Основным элементом устройства поршневого компрессора является компрессорная головка (поршневой узел). Ее конструкция напоминает двигатель внутреннего сгорания. Она состоит из цилиндра, поршня, поршневых колец компрессора, шатуна, коленчатого вала, а также впускного и нагнетательного клапанов. В отличие от ДВС, клапаны в компрессоре представляют собой пластинку с пружиной и при работе поршневого компрессора приводятся в действие не принудительно, а от перепада давлений. Для смазки устройства поршневого компрессора, в частности трущихся деталей, в компрессорную головку заливают масло.
В случае если необходимо получить сжатый воздух высокой чистоты и без примесей масла (например, в медицинских учреждениях) применяют безмасляные компрессоры. В таком устройстве поршневого компрессора кольца выполнены с полимерных материалов, а для надежной работы поршневого компрессора применяют графитовую смазку.
Для достижения более высокой производительности поршневого компрессора компрессорные головки изготавливают с несколькими цилиндрами, которые могут иметь рядное, V-образное или оппозитное устройство.
В движение коленчатый вал приводится от электродвигателя, что обеспечивает работу поршневого компрессора. В зависимости от способа соединения с электродвигателем различают компрессоры поршневые с ременным и прямым приводом.
- При прямом приводе головка и двигатель расположены на одной оси и их валы в устройстве поршневого компрессора соединены напрямую.
- В компрессорах поршневых ременного типа привод головки и мотор расположены параллельно друг другу, а движение предается через ременную передачу. На шкиве привода головки установлены лопасти, которые обеспечивают охлаждение поршневого узла.
Другим важным элементом в устройстве и работе поршневого компрессора является ресивер, который представляет собой стальную емкость и предназначен для поддержания постоянного давления и равномерного расхода воздуха. В ресивере также установлен клапан для сброса давления в случае если будет превышено его допустимое значение.
Для обеспечения работы поршневого компрессора в автоматическом режиме в устройстве поршневого компрессора находится прессостат (реле давления), который при достижении заданного давления размыкает контакты и останавливает двигатель, а при снижении давления ниже некоторого значения замыкает контакты и запускает компрессор.
Работа поршневого компрессора
Работа поршневого компрессора осуществляется по следующему принципу: при движении поршня вниз в цилиндре создается разрежение, в результате чего открывается впускной клапан. Так как в цилиндре давление ниже атмосферного, то через клапан поступает воздух. Для очистки поступающего воздуха в устройстве поршневого компрессора применяют фильтры. Во время движения поршня вверх при работе поршневого компрессора оба клапана закрыты. При сжатии воздуха возрастает давление в цилиндре и открывается нагнетательный клапан, через который воздух поступает в ресивер. Работающие по такому принципу поршневые компрессоры носят название одноступенчатых.
Одним из недостатков устройств поршневых одноступенчатых компрессоров является ограниченное рабочее давление. Работа поршневого компрессора данного типа возможна с повышением давления только до 10 атмосфер. Это объясняется тем, что при больших давлениях сильно возрастает температура в цилиндре и может загореться масло, которое используется для смазки деталей.
Работа поршневых компрессоров на небольших предприятиях наиболее часто основывается на двухступенчатой установке с двумя цилиндрами. Цилиндр первой ступени, как правило, имеет больший диаметр чем второй.
При выборе поршневого компрессора необходимо в первую очередь учитывать характеристики потребителей сжатого воздуха. Ведь работа поршневого компрессора не должна быть постоянной. При правильном подборе компрессорной головки и ресивера время работы компрессора должно быть равным времени отдыха.
Стоит учесть, что все производители указывают на своих компрессорах производительность в л/мин только на входе.
Устройство и принцип работы поршневого компрессора
Поршневой компрессор является одним из первых видов компрессорных установок, который широко используется и на сегодняшний день. Его высокие рабочие показатели и возможность интенсивной эксплуатации при больших объемах производительности позволяют использовать поршневой компрессор в промышленном назначении и на небольших производствах.
Устройство и принцип работы поршневых компрессоров зависит от типа данных установок, которые могут быть различны:
- по количеству в оборудовании цилиндров – бывают одно-, двух- и многоцилиндровые;
- по виду расположения в установке цилиндров – W, V-образные, а также рядные;
- в зависимости от количества ступеней для сжатия воздуха в поршневом компрессорном оборудовании – многоступенчатые, одноступенчатые.
Однако, вне зависимости от своего типа, установки поршневые имеют базовое оснащение, характерное всем типам данных установок.
Поршневые компрессоры и их устройство
Устройство поршневых компрессоров является наиболее простым в одноцилиндровых установках. В состав данного оборудования входят такие элементы, как поршень, цилиндр, два клапана — для нагнетания и всасывания воздуха, которые находятся в крышке цилиндра. При работе установки, шатун, соединенный с вращающимся коленчатым валом, передает на поршень ограниченные движения по камере сжатия. В данном процессе происходит увеличение объема, находящегося между клапанами и нижней части поршня, что приводит к разрежению.
Здесь Вы можете ознакомиться с каталогом поршневых компрессоров, реализуемых ООО ГК «ТехМаш».
Превышая сопротивление пружины, которая закрывает клапан, выполняющий всасывающие функции, атмосферный воздух открывает его и поступает в цилиндр по всасывающему патрубку.
Возвратное действие поршня приводит к сжиманию воздуха и возрастанию его давления. Нагнетательный клапан, который также удерживается пружиной, открывается потоком воздуха, находящегося под высоким давлением, после чего сжатый воздух попадает в нагнетательный патрубок. При этом питание оборудование может осуществляться от электродвигателя или же автономного двигателя, который может быть дизельным или бензиновым.
При этом принцип работы поршневых компрессоров позволяет получить максимально эффективную работу оборудования. Однако есть и один незначительный минус – сжатый воздух, подаваемый данной установкой, поступает в виде импульсов, а не ровным потоком. Для выравнивания давления сжатого воздуха и его пульсации, поршневые компрессоры используются преимущественно с ресиверами, позволяющими исключить возможность перебоев, как в давлении подаваемого воздуха, так и в работе всего оборудования.
Также необходимо рассмотреть особенности конструкции и действия двухцилиндровых установок поршневого типа. В данном случае установка является одноступенчатой и оснащенной двумя одинаковыми по размеру цилиндрами. Работа цилиндров происходит в противофазе, в результате чего они всасывают воздух поочередно. Далее воздух сжимается до максимального уровня давления и вытесняется в нагнетающую часть оборудования.
В случае с двухступенчатыми двухцилиндровыми установками, оборудование оснащено цилиндрами различных размеров. Сжатие воздуха до определенного значения происходит в цилиндре первой ступени. Далее он переходит в межступенчатый охладитель, где охлаждается до необходимого уровня. Затем, попадая в цилиндр второй ступени, воздух дожимается, что позволяет получить максимально высокий уровень давления воздуха.
В качестве межступенчатого охладителя используется медная трубка, обеспечивающая охлаждение находящегося под давлением воздуха на промежутке между цилиндрами двух ступеней. Охлаждение воздуха позволяет оптимизировать процесс его сжатия и значительно повысить КПД всей установки. При этом специальным образом подбираются размеры обоих цилиндров – так, чтобы одинаковая работа проводилась на всех ступенях сжатия воздуха.
Двухступенчатые поршневые компрессоры, устройство которых позволяет получить более эффективный уровень работы оборудования, в сравнении с одноступенчатыми установками, имеют большое количество важных преимуществ. В первую очередь – это затрачивание минимального количества энергии при одинаковой мощности двигателя. Так при одноступенчатом сжатии воздуха требуется большее количество энергии, чем для сжатия этого же объема воздуха двухступенчатым оборудованием.
Кроме того, температура в цилиндрах двухступенчатых установок имеет значительно более низкий показатель, чем в компрессорах одноступенчатого класса. Низкая температура обеспечивает надежность и эффективность работы всего оборудования, а также повышает ресурс поршневой группы. При этом двухступенчатые установки имеют производительность на 20% выше, нежели компрессоры других типов.
Особенности конструкции и принцип действия компрессоров поршневого типа отличаются своей сравнительной простотой в сочетании с высокой эффективностью работы оборудования, его практичностью и длительным сроком эксплуатации при интенсивном использовании. Эти преимущества сделали установки данного типа одними из наиболее популярных, как в быту, так в полупромышленном и промышленном использовании.
Статья про устройство и принцип работы винтовых компрессоров
На сегодняшний день воздушные компрессоры представляют собой широкий выбор установок, различающихся между собой по принципу действия, оснащению и устройству, рабочим и другим характеристикам. Каждый тип оборудования имеет свои преимущества и особенности, которые делают выбор той или иной установки наиболее оптимальным. Однако при этом наиболее популярными являются винтовые компрессоры, устройство которых обеспечивает высокую эффективность и надежность работы оборудования.
Устройство компрессоров винтового типа
Установки, входящие в группу винтовых компрессоров, могут быть различны, но при этом они имеют оснащение, общее для всех видов оборудования данного типа. Входящие в состав винтовых компрессоров устройства выполняют определенные функции, обеспечивая при этом эффективную и бесперебойную работу установок.
В состав винтовых компрессоров входят следующие составляющие:
- Воздушный фильтр всасывающий – выполняет функцию очистки воздуха, который попадает в компрессорную установку. Зачастую состоит из двух элементов – предварительного фильтра, находящегося в том месте, где происходит забор воздуха, а также фильтра, расположенного перед входным клапаном.
- Входной клапан – обеспечивает регулировку производительности всего компрессора и оснащен пневматическим управлением. Регулирование работы установки обеспечивается переходом клапана на холостой ход.
- Винтовой блок – представляет собой один из главных рабочих элементов установки винтового типа.
В состав винтового блока входят два, расположенных параллельно по отношению друг к другу ротора, одни из которых имеет вогнутый винтовой профиль, а другой – выпуклый. Именно наличие роторов отличает устройство винтовых компрессоров и принцип их действия от установок других типов.
- Ременная передача – представляет собой два шкива, задающих необходимую скорость вращения роторов. Один из шкивов расположен на винтовой паре, а другой находится на двигателе.
- Электродвигатель – обеспечивает вращение винтовой пары посредством муфты, редуктора или же ременного привода.
- Масляной фильтр – проводит очистку масла, прежде чем оно возвращается в блок с винтами.
- Отделитель масла – бак, изготовленный из металла, в середине которого расположена перегородка с отверстиями. Сила инерции, возникающая при закрутке потока, приводит к очистке воздуха от масла специальным фильтром.
- Термостат – обеспечивает наиболее оптимальный температурный режим.
При низких значениях температуры масла, термостат пропускает его, не затрагивая при этом охлаждающий радиатор, что позволяет ускорить получение наиболее оптимальной температуры в установке.
- Охладитель масла – выполняет функции охлаждения масла, после того, как оно отделилось от сжатого воздуха.
- Концевой охладитель воздуха – охлаждает до необходимого уровня сжатый воздух перед тем, как он подается потребителю.
- Предохранительный клапан – обеспечивает безопасную работу устройства и предотвращает его поломку. Данный клапан срабатывает при значительном повышении уровня давления в маслоотделительном баке, которое может вывести из строя все оборудование.
- Система трубопроводов – имеет различные трубопроводы для воздушно-масляной смеси, воздуха и масла.
- Реле давления – устанавливает параметры и режим работы установки в зависимости от показателей уровня давления. Так, при достижении максимального значения давления, работа винтовых компрессоров переходит на холостой ход.
При снижении давления установка вновь начинает работать.
- Блок управления – необходим для электронного управления и контроля над работой оборудования, а также позволяет передавать на дисплей все необходимые рабочие параметры и характеристики компрессора.
- Вентилятор – предназначен для забора воздуха в компрессор с одновременным охлаждением рабочих деталей и элементов оборудования.
Принцип действия компрессоров винтовой группы
Действие винтовых компрессоров заключается в следующем. Посредством системы привода, двигатель приводит в движение винтовую пару, в которую затем поступает уже очищенный воздух. Далее происходит смешивание воздуха с маслом, которое необходимо для создания между роторами масляного клина. При вращении роторов происходит уплотнение зазора между нами и корпусом, что приводит к сжиманию воздуха и повышению давления. Кроме того, в данном процессе масло также выполняет функцию смазывания рабочих механизмов компрессорной установки.
После сжатия, смесь из масла и воздуха поступает в специальную емкость, где воздух отделяется от масла, затем охлаждается и подается на выход компрессорного оборудования. После охлаждения масло проходит дополнительную фильтрацию, а затем вновь подается в блок с винтами.
Подобное устройство и принцип работы винтовых компрессоров обеспечивает наличие в оборудовании высоких рабочих и технических показателей, позволяющих значительно повысить эффективность работы и производительность установки. Благодаря этому винтовые компрессоры сегодня являются одними из наиболее часто используемых установок, которые могут применяться как в промышленном масштабе, так и на небольших производствах.
Установки винтового типа могут быть различны в зависимости от типа привода, использованию масла, количеству ступеней и другим параметрам, исходя из которых необходимо выбирать наиболее оптимальный тип установки.
Категория в каталоге:
устройство, схема, преимущества, особенности эксплуатации.
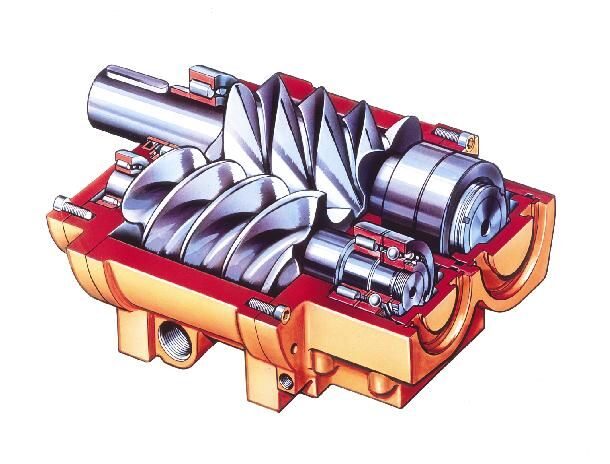
Винтовым называется компрессор, понижение давления в котором достигается за счет вращения двух винтов (роторов). По конструкции такие устройства принадлежат к ротационному компрессорному оборудованию. Впервые винтовая модель была запатентована в 1934 г. На сегодня агрегаты данного типа являются наиболее распространенными в своем сегменте. Этому способствует их относительно небольшая масса и компактные габариты, надежность, способность функционировать в автономном режиме, экономичность в плане потребления электроэнергии и затрат на обслуживание. Невысокий уровень вибрации позволяет монтировать такие системы без обустройства специального фундамента, как в случае с поршневыми аналогами. В ряде направлений (судовые рефрижераторы, мобильные компрессорные станции и т. п.) роторные модели практически полностью вытеснили компрессоры других разновидностей. Такие устройства могут подавать воздух, сжатый до 15 атм., и обладать производительностью 1–100 м3/мин.
Преимущества винтовых компрессоров
По сравнению с центробежными и поршневыми моделями, устройства описываемого типа имеют следующие базовые преимущества.
- Крайне низкий (порядка 2–3 мг/м3) расход масла, что в разы меньше, чем у крупных поршневых моделей с лубрикаторной смазкой. Следовательно, воздух, подаваемый посредством винтовых агрегатов, будет намного качественнее и чище. Его можно применять для питания новейшего пневматического оборудования без установки фильтров дополнительной очистки.
- Пониженный уровень вибрации и шума (у некоторых моделей – соразмерный с шумностью бытовой техники). С учетом небольшого веса и габаритов это позволяет устанавливать описываемые устройства без специального фундамента непосредственно на производствах, где потребляется сжатый воздух, а также оснащать ими разноплановые мобильные комплексы.
- Наличие воздушного охлаждения. Во-первых, это устраняет необходимость устанавливать системы оборотного водоснабжения.
Во-вторых, появляется возможность вторично использовать тепло, которое выделяется в результате функционирования компрессора, к примеру, для обогрева помещений.
- Надежность работы, безопасность и простота эксплуатации, способность длительное время функционировать без обслуживания. Это становится возможным благодаря наличию автоматических систем, посредством которых осуществляется управление и контроль над работой агрегата.
Устройство винтового компрессора
Стандартная модель состоит из следующих элементов.
- Фильтр, необходимый для очищения воздуха, поступающего в агрегат. Обычно состоит из первичного фильтра, монтируемого непосредственно на корпус в месте забора воздушных масс из атмосферы, и вторичного, который устанавливается перед клапаном 2.
- Всасывающий клапан. Позволяет предотвратить выброс масла и сжатого воздуха из компрессора в момент остановки последнего. Работает на пневматическом управлении. По конструкции представляет собой обычный подпружиненный клапан.
Некоторые устройства оснащены аналогами пропорционального типа.
- Винтовой блок. Представляет собой основную рабочую часть агрегата. Состоит из двух винтов (роторов), изготовленных посредством высокоточной механической обработки и помещенных в корпус. Самый дорогой элемент устройства. Роторная пара оснащена датчиком термозащиты, вмонтированным возле патрубка 18. Данный контроллер выключает мотор, если температура на выходе роторов превысит отметку в 105 °С.
- Ременной привод (высокомощные модели оснащены прямой муфтовой передачей или редукторами). Задает скорость, с которой вращаются винты. Представляет собой 2 шкива, один из которых установлен на роторной паре, другой – на двигателе. Чем больше скорость, тем выше производительность компрессора, однако максимальное давление (рабочее) при этом снижается.
- Шкивы, размер которых задает скорость оборотов винтовой пары 4.
- Двигатель. Вращает роторы 4 посредством ременной передачи (в более новых моделях – муфты или редуктора). Оснащен датчиком термозащиты, который отключает мотор от сети при достижении максимально допустимых значений потребляемого электротока. Вместе с датчиком, описанным в пункте 3, обеспечивает безопасность функционирования устройства и защищает его от возникновения аварийных ситуаций.
- Масляный фильтр. Он очищает масло перед его возвратом в роторы.
- Маслоотделитель первичной очистки. Здесь воздух освобождается от масла под действием центробежной силы (поток закручивается, вследствие чего и отделяются частицы).
- Маслоотделительный фильтр. Обеспечивает второй этап очистки. Такой комплексный подход позволяет минимизировать остаточные масляные пары на выходе до 1,3 мг/м3, что является недостижимым значением для поршневых агрегатов.
- Предохранительный клапан. Необходим для обеспечения безопасности. Клапан срабатывает, если давление в маслоотделителе 8 превысит допустимый лимит.
- Термостат, обеспечивающий нужный температурный режим. Пропускает масляный состав, не разогретый до 72 °С, мимо охлаждающего радиатора 9. Это позволяет ускорить достижение оптимальной температуры.
- Маслоохладитель. После отделения от сжатого воздуха горячее масло попадает в данный резервуар, где охлаждается до нужной температуры.
- Воздухоохладитель. Перед подачей потребителю сжатый воздух охлаждается здесь до температуры, которая будет выше на 15–20 °С, чем окружающая среда.
- Вентилятор. Осуществляет забор воздуха, охлаждает рабочие элементы.
- Клапан холостого хода (электропневматический). Управляет функционированием всасывающего клапана 2.
- Реле давления. Обеспечивает работу агрегата в автоматическом режиме. В новых компрессорах реле заменено электронной системой управления.
- Манометр. Находится на лицевой панели, показывает давление внутри компрессора.
- Выходной патрубок.
- Прозрачное цилиндрическое утолщение на трубке, необходимое для визуального контроля над процессом возврата масла.
- Клапан минимального давления. Пока последнее не превышает 4 бар, он всегда будет закрытым. Также данный элемент выполняет функцию обратного клапана, поскольку отделяет пневмолинию и компрессор при остановке последнего или работе в холостом режиме.
Устройство помещено в корпус, который обычно изготавливается из стали. Он покрывается негорючим звукопоглощающим составом, устойчивым к маслу и прочим сходным веществам. Это конструкция наиболее распространенной модификации. В зависимости от модели и производителя схема и комплектация роторного компрессора может варьироваться.
Принцип действия компрессора
Через клапан 2 воздух из атмосферы, очищенный посредством фильтров 1, попадает в роторную пару 3. Здесь он смешивается с маслом. Последнее подается в резервуар сжатия для выполнения следующих задач.
- Уплотнить зазоры между винтами 3 и корпусом 16, а также между полостями роторов. Это позволяет минимизировать перетечки и утечки.
- Устранить касание винтов, обеспечив масляный клин между ними.
- Отводить тепло, которое индуцируется в процессе сжатия воздуха.
Сжатая в блоке 3 воздушно-масляная смесь подается в маслоотделитель 7, где разделяется на составляющие. Отсепарированное масло очищается на фильтре 6 и возвращается в блок 3. В зависимости от температуры предварительно оно может охлаждаться в радиаторе 9, что регулируется термостатом 8. В любом случае, масло будет циркулировать по замкнутому кругу. Воздух поступает в охлаждающий радиатор 13. После достижения нужной температуры он подается на выход компрессора.
Режимы работы
- Пусковой (Start). Данный режим служит для оптимизации нагрузки на электросеть в момент запуска компрессора. Включение двигателя осуществляется по схеме «звезда», а через 2 секунды (отсчитываются по таймеру, который включается в момент нажатия на кнопку Start) он переключается на схему «треугольник», что соответствует рабочему режиму. Маломощные винтовые модели работают на прямом пуске.
- Рабочий. В системе начинает увеличиваться давление. Для его контроля имеется 2 манометра. Первый находится на лицевой панели и показывает параметры внутри компрессора. Второй – на ресивере, он служит для контроля линии. После достижения максимально допустимого давления срабатывает соответствующее реле, в результате чего агрегат переходит на холостой ход из рабочего режима.
- Холостой ход. Двигатель и роторы вращаются, перемещая газ по внутреннему контуру. Это необходимо для охлаждения воздушных масс. Данный режим служит для перевода компрессора в состояние ожидания или выступает в качестве подготовки перед полным выключением. В поршневых моделях холостого хода нет. Детальное описание работы устройства на таком режиме выглядит следующим образом. Реле 16 дает команду, запускающую пневмоклапан холостого хода и временное реле. Параметры последнего можно настроить. Пневмоклапан открывает канал между фильтром маслоотделителя 9 и всасывающим клапаном 2, вследствие чего давление внутри компрессора начинает снижаться с такой скоростью, чтобы достичь минимальной отметки (2,5 бар) в течение установленного времени. Это позволяет остановить двигатель без выброса масла в область фильтра 1. По истечении указанного периода реле времени дает команду отключить мотор. Система переходит в состояние ожидания. Если сжатие достигло минимальной величины раньше, чем сработало временное реле, снова включается рабочий ритм.
- Ожидание. Продолжается, пока рабочее давление не опустится ниже минимальной отметки, после чего реле 16 вновь запускает механизм. Длительность данного режима зависит от скорости расходования воздуха.
- Стоп (Stop). Служит для штатного выключения агрегата. Если при этом компрессор находился в рабочем ритме, он на некоторое время перейдет на холостой ход и только после этого отключится.
- Alarm—stop – экстренное выключение. Соответствующая кнопка находится на панели управления. Режим используется в случаях, если понадобилось срочно остановить двигатель. Агрегат выключается сразу, без промежуточного перехода на холостые обороты.
Разновидности винтовых компрессоров
Маслозаполненные. Один ротор в них является ведущим, второй – ведомым. Физический контакт между данными элементами предотвращается посредством впрыскиваемого масла (на 1 кВт мощности устройства подается 1 л/мин). Шумность работы подобного оборудования находится на уровне шума от бытовой техники – 60–80 Дб (при условии использования звукопоглощающих кожухов). Мощность двигателей может варьироваться в пределах 3–355 кВт, а объемные расходы – 0,4-54 м3/мин. Такое оборудование можно устанавливать непосредственно в рабочих цехах.
Безмасляные. Делятся на два подвида.
- Компрессоры винтовые сухого сжатия. Оснащены синхронными электромоторами, которые приводят в движение оба винта, исключая контакт между ними. Они менее производительны по сравнению с моделями маслозаполненного типа. Из-за отсутствия масла нет и отвода тепла. Поэтому уровень сжатия достигает лишь 3,5 бар в одной ступени. Данный показатель можно поднять до 10 бар, если использовать вторую ступень и промежуточный рефрижератор. Но это, как и применение двух электромоторов вместо одного, увеличивает стоимость устройства.
- Водозаполненные компрессоры. Самая технологичная модель, сочетающая все достоинства безмасляных и маслозаполненных вариантов. Водозаполненные агрегаты отличаются оптимальной производительностью и позволяют достигать сжатия 13 бар в одной ступени. Важным преимуществом подобных моделей является их экологичность, ведь традиционное компрессорное масло заменено на чистую, натуральную и не такую дорогостоящую воду. При этом обеспечивается внутреннее охлаждение. Вода обладает высокой удельной теплопроводностью и теплоемкостью. Вне зависимости от уровня конечного сжатия температура в ходе данного процесса повышается максимум на 12 °С. Этому способствует в том числе применение дозированного впрыска. Тепловая нагрузка на элементы устройства минимальна, следовательно, возрастает срок службы, надежность и безопасность агрегата в целом. Сжатый воздух не нуждается в дополнительном охлаждении. Циркулирующая в системе вода охлаждается до температуры окружающей среды. А влага, имеющаяся в сжатых воздушных массах, конденсируется и вновь возвращается в контур. В маслозаполненных моделях именно конденсат был загрязняющим веществом. Здесь же он используется в циркуляционном контуре за несколько часов (при нормальных условиях и непрерывной эксплуатации устройства). Следовательно, накопление отходов на станции практически нивелируется. Еще одно значимое достоинство водозаполненных компрессоров – возможность снизить на 20 % энергозатраты. Процесс сжатия в подобных устройствах приближается к идеальному изотермическому. Изготовление устройства обходится дешевле за счет отсутствия масляных фильтров, емкостей для отработанной масляной жидкости. Не приходится нести издержки и на переработку конденсата.
Безмаслянные модели используются в различных областях, но самые популярные сферы применения – пищевая, фармацевтическая и химическая промышленности.
Почему выгодно перейти на винтовое компрессорное оборудование
Как отмечалось выше, роторные модели постепенно вытесняют поршневые и центробежные варианты. Многие предприятия переходят именно на такие агрегаты, считая их более надежными, совершенными и экономичными. При этом стоимость роторных устройств выше, чем поршневых аналогов. Да и на замену оборудования (если речь идет именно о модернизации системы, а не о сборке новой установки) необходимо потратить определенную сумму. Разберемся более детально, в чем именно заключается выгода для предпринимателей, проведя сравнение винтовых и поршневых моделей. Но для начала необходимо понять, из каких статей расходов формируется стоимость любого компрессора. Окончательная сумма включает в себя следующие затраты.
- Приобретение агрегата.
- Оплата монтажных работ.
- Покупка расходных материалов.
- Оплата электроэнергии, потребляемой устройством.
- Ремонтные расходы.
- Покупка дополнительного оборудования. Например, это может быть очистительный комплекс для сжатого воздуха.
Расходы на приобретение агрегата
В этом плане более выгодными являются поршневые модели, цена которых на 20–40 % ниже стоимости винтовых аналогов. В то же время, это средства, затрачиваемые непосредственно на покупку оборудования. Но ведь его необходимо еще и установить. Поршневые модели имеют более значительные габариты и массу, в процессе работы они ощутимо вибрируют, поэтому нуждаются в обустройстве специального фундамента. Это существенно увеличивает стоимость монтажа. Если сравнивать общую сумму, которую необходимо потратить на покупку оборудования и его установку, то более выгодными оказываются именно роторные варианты.
Расходы на электроэнергию
КПД роторных компрессоров существенно больше. И чем выше производительность агрегата, тем более заметной будет эта разница. Имеет значение и тип устройства. Например, водозаполненные модели обеспечивают более высокую экономию энергоресурсов. Но даже маслозаполненные варианты низкой производительности, оснащенные традиционной схемой управления, на протяжении эксплуатационного периода несколько раз окупают свою стоимость за счет одной только экономии электричества. По критерию энергозатрат на генерирование одинакового объема сжатого воздуха поршневые агрегаты заметно проигрывают.
Некоторые винтовые модели позволяют еще больше увеличить экономию энергоресурсов. Речь идет о двухступенчатых агрегатах и устройствах с изменяемой частотой оборотов мотора. Подобное оборудование дает дополнительную экономию на 30 %. Важно и то, что имеется возможность регулировать производительность агрегата. Другими словами, компрессор будет генерировать столько сжатого воздуха, сколько потребляет оборудование в каждый конкретный момент. При таком режиме работы не возникнет ни переизбытка, ни дефицита. Оборудование будет функционировать с нужной производительностью, затрачивая энергоресурсы только на полезную работу.
Расходы на обслуживание и ремонт
Поршневые компрессоры нуждаются в регулярной замене колец поршней, клапанов, вкладышей и прочих элементов механизма. Роторные модели полностью избавляют пользователя от подобных проблем. В их механизме нет быстро изнашивающихся элементов. Потребность в ремонте возникает гораздо реже, а плановое обслуживание обходится гораздо дешевле. При соблюдении инструкции по эксплуатации такой агрегат способен прослужить около 20 лет, работая без ремонта в трехсменном режиме.
Удешевление обслуживания происходит еще и потому, что пропадает необходимость в постоянном присутствии рядом с оборудованием обслуживающего персонала. Роторные модели оснащены защитой, предотвращающей возникновение аварийных ситуаций. Например, оборудование отключается при перегреве или пиковых значениях электрического тока и способно работать в полностью автономном режиме.
В отличие от поршневых моделей, роторные аналоги поддерживают возможность комплектации блоками электронного управления, которые позволяют на программном уровне задать параметры функционирования агрегата на несколько недель вперед. Посредством электронного блока можно управлять и группой из нескольких механизмов, останавливая или запуская некоторые из них в зависимости от производственных потребностей в сжатом воздухе. Таким образом, комплекс функционирует с максимальной продуктивностью и без перерасхода ресурсов.
Покупка расходных материалов
Винтовые компрессоры имеют более эффективную систему маслоотделения, которая позволяет существенно снизить количество масляных фракций, смешивающихся со сжатым воздухом. Если уменьшается объем затрат основного расходного вещества, то снижается и стоимость его приобретения. Подобные агрегаты имеют более совершенную конструкцию (если сравнивать с поршневыми аналогами), которая позволяет установить современные СОЖ. Последние способны в несколько раз сократить частоту замены масляного состава.
Приобретение дополнительного оборудования
Поскольку в винтовых моделях масляные фракции отделяются эффективнее, нет необходимости покупать дополнительные комплексы очистки. А если сделать выбор в пользу более дешевого поршневого агрегата, придется приобрести еще и ресивер, который гасит возникающие в пневматической системе пульсации давления. Роторные аналоги не генерируют подобные пульсации. В большинстве случаев это позволяет избежать покупки дополнительных ресиверов.
Шумность работы винтовых агрегатов значительно ниже, чем у поршневых устройств. Посредством установки шумопогашающих кожухов можно еще сильнее снизить уровень звука и вибрацию, возникающие при функционировании компрессорного оборудования. Это позволяет монтировать его прямо в цехах, куда подается сжатый газ. Чем короче расстояние, на которое перемещается воздух, тем меньше появляется в нем конденсированной влаги и твердых фракций, которые способны серьезно навредить производственному превмооснащению.
Децентрализация компрессорного оборудования данного типа позволяет запускать только те единицы, которые понадобились в конкретный момент времени для обеспечения производства сжатым газом в необходимых объемах. Следует упомянуть и дополнительную выгоду, которая заключается в возможности задействования генерируемого компрессором тепла для нужд предприятия. Зачастую оно используется для отопления цехов.
Резюме
Роторные модели уступают поршневым аналогам равной производительности только по стоимости покупки. По всем остальным статьям (затраты на ремонт, закупку дополнительного оснащения и расходных материалов, оплату потребляемой энергии и работу обслуживающего персонала) они гораздо выгоднее и несколько раз окупают себя за эксплуатационный период. Таким образом, покупка винтового компрессорного оборудования – экономически оправданное и выгодное для предприятия решение.
Модели с частотным приводом
В середине 1990 гг. были созданы роторные компрессоры, оснащенные частотным приводом. Появление такого оборудования стало большим шагом к развитию и внедрению энергосберегающих технологий на производстве. Стоимость энергорессурсов постоянно увеличивается. Закономерно, что предприятия при модернизации своих мощностей стараются подобрать максимально экономичные варианты для замены устаревшего оснащения. И их выбор часто останавливается именно на роторных агрегатах с частотным приводом. Кроме надежности работы и способности функционировать в автономном режиме подобные агрегаты позволяют существенно оптимизировать энергозатраты.
Особенности конструкции и эксплуатации частотных приводов
Привод данного типа состоит из частотного преобразователя и асинхронного мотора. Последний преобразует электричество в механическую энергию, приводя в движение роторную пару. Частотный преобразователь служит для управления мотором. Он модифицирует переменный электроток одной частоты в переменный ток другой частоты.
В технической литературе чаще встречается термин «частотно-регулируемый электропривод». Подобное название обусловлено тем, что регулировка скорости оборотов мотора осуществляется посредством вариации частоты питающего напряжения, которое подается частотным преобразователем на двигатель. На сегодня подобные приводы широко применяются в различных сферах промышленности. Например, они задействованы в насосах, обеспечивающих дополнительную подкачку жидкости для сетей тепло- и водоснабжения.
Компрессорное оборудование с частотным приводом
Оснащение такого оборудования частотными приводами позволило получить агрегаты, обладающие рядом значимых достоинств по сравнению с простыми винтовыми моделями.
- Плавный запуск. При включении обычного асинхронного электромотора возникают пусковые токи, превышающие номинальные в более чем 4 раза. Это провоцирует возникновение перегрузки в сети и накладывает ограничения на количество включений компрессорного оборудования в течение часа. Аналог с двигателем, оснащенным частотным преобразователем, запускается плавно, не провоцируя перегрузок в сети. Число пусковых операций у него будет меньше.
- Способность поддерживать постоянное давление с высокой (до 0,1 бар) точностью, немедленное реагирование на все скачки данного параметра в сети. Каждый дополнительный бар нагнетания – это 6–8-процентное увеличение энергопотребления оборудования.
- Обеспечение точного соответствия производительности компрессора и реальной потребности подключенного к нему оборудования в сжатом газе. Это позволяет минимизировать количество переходов агрегата в режим холостых оборотов. А ведь именно в моменты подобных переходов асинхронный электромотор обычной модели потребляет до 1/4 собственной номинальной мощности.
Посредством несложных расчетов получаем, что модель с частотным приводом за пятилетний период эксплуатации позволяет сэкономить до 25 % электроэнергии по сравнению с роторными моделями без частотного преобразователя. Некоторые производители обещают, что их оборудование способно сэкономить до 35 % ресурсов.
Другие способы оптимизации энергозатрат
На практике эффективность работы оборудования напрямую зависит от режима его функционирования. Нередко встречаются случаи, когда производители завышают показатели экономичности своего оборудования или в рекламных целях предоставляют неполную информацию. Пользователи компрессорных установок должны знать, что существуют и другие способы оптимизации энергозатрат, которые часто более просты и экономически выгодны. В качестве примера можно привести децентрализованный комплекс обеспечения сжатым газом. Он предусматривает установку нескольких компрессоров небольшой мощности вместо одного мощного агрегата, не всегда работающего на полную силу. Каждая единица подбирается в зависимости от объемов воздухопотребления конкретного оборудования. Поскольку не все производственные мощности могут быть задействованы в один момент времени, компрессорные агрегаты подключаются по мере необходимости.
Альтернативный вариант предусматривает монтаж нескольких винтовых моделей в единую сеть, которая оснащается одним пультом управления. Такая станция работает на 100 % своей мощности при пиковой нагрузке в сети. Как только потребность в сжатом газе снижается, ненужные мощности отключаются.
Кроме экономии энергоресурсов подобные мультикомпрессорные группы позволяют создать энергетический резерв. Если одна из единиц выйдет из строя, комплекс продолжит функционировать. Потеря мощности будет незначительной. Например, если в сеть входит 4 агрегата, то поломка одного из них снизит суммарную производительность только на 1/4.
Если же на предприятии будет установлен всего один, хоть и высокомощный агрегат, то его внезапная поломка может привести к полной остановке производственного цикла со всеми вытекающими убытками от простоя.
В настоящий момент степень изношенности компрессорного оборудования на многих предприятиях достиг критического уровня. Вопрос модернизации устройств подачи сжатого газа является очень актуальным. Надеемся, что данная статья поможет вам определиться с выбором компрессора, удовлетворяющего производственным потребностям вашего предприятия и современным требованиям к энергоэффективности, безопасности и надежности оборудования.
Устройство, применение и преимущества центробежных компрессоров
Центробежный компрессор представляет собой динамический компрессор радиального типа. В отличие от компрессоров, работающих по принципу вытеснения, центробежные компрессоры работают при постоянном давлении. Прямое назначение таких установок — это сжатие газа в небольшом объеме, при этом одновременно увеличивается давление и температура сжимаемой среды.
Итак, как работает центробежный компрессор?
Воздух засасывается в центр вращающегося рабочего колеса с радиальными лопастями и прижимается к центру центробежной силой. Это радиальное движение воздуха приводит к повышению давления и генерированию кинетической энергии. Перед тем, как воздух направляется в центр рабочего колеса, кинетическая энергия также преобразуется в давление, проходя через диффузор и спираль.
Схема многоступенчатого однопоточного центробежного компрессора
а – продольный разрез; б – разрезы рабочего колеса и лопаточного диффузора; 1 – вал; 2 – диффузор; 3 – лопатки ОНА; 4,5 – уплотнения; 6 – рабочее колесо; 7 – рабочие лопатки; 8 – корпус компрессора
На каждой ступени компрессора давление воздуха повышается. В зависимости от требуемого давления число ступеней сжатия в центробежном компрессоре может варьироваться для достижения более высокого давления. Такое многоступенчатое сжатие часто используется в нефтегазовой и перерабатывающей промышленности. В установках очистки сточных вод, напротив, используются одноступенчатые установки низкого давления для достижения желаемого перепада давления.
В современных моделях центробежных воздушных компрессоров для привода рабочих колес используются сверхскоростные электродвигатели. Благодаря этому достигается компактность компрессора, так как отсутствует редуктор и соответствующая система смазки. Таким образом, такой компрессор подходит для применения там, где необходим стопроцентный безмасляный сжатый воздух.
Одним из наиболее важных факторов для центробежного компрессора является эффективность компрессора при полной нагрузке. Однако потребление воздуха на заводе всегда колеблется, поэтому система контроля мощности необходима для обеспечения стабильной работы компрессора. Это достигается с помощью направляющих лопаток, которые устанавливаются перед входом в первую ступень сжатия. Это необходимо для подачи воздуха с постоянным давлением нагнетания в соответствии с требованиями расхода воздуха.
Преимущества центробежных компрессоров
- Низкий вес, легкость проектирования и производства.
- Подходит для непрерывного подачи сжатого воздуха, например, в систему охлаждения.
- Безмасляный воздух н выходе из компрессора.
- Меньшее количество трущихся деталей.
- Высокая скорость потока.
- Относительно энергоэффективен.
- Широкий диапазон скоростей вращения рабочих колес.
- Центробежные компрессоры надежны и недороги в обслуживании.
- Для установки центробежного компрессора не требуется специальный фундамент.
Стоит отметить, что центробежные компрессоры не подходят там, где требуется сжатие до высоких давлений, а также, важно избежать вибраций установки из-за высокой скорости вращения рабочих колес, так как даже незначительный дисбаланс может привести к выходу компрессора из строя.
Применение центробежных компрессоров
- Пищевая промышленность — центробежный компрессор обеспечивает отсутствие масла.
- Центробежный компрессор удовлетворяет самым высоким требованиям к сжатому воздуху.
- Нефтеперерабатывающая отрасль, переработка природного газа.
- Охлаждение, кондиционирование воздуха, системы HVAC.
- Воздухоразделительные установки.
Последней тенденцией в производстве центробежных компрессоров стал их модульный принцип проектирования — компрессорные установки собирают из типовых модулей, дабы сократить затраты и эксплуатационные расходы. Использование таких модулей сокращает общее количество компонентов, затраты и ускоряет последующую сборку агрегата.
Наша компания предлагает приобрести современные центробежные компрессоры SAMSUNG TECHWIN, а также другое высокоэффективное компрессорное оборудование на выгодных условиях!
Устройство и принцип работы воздушного винтового компрессора
Воздушные компрессоры сегодня используются на самых разных производствах. Каждое предприятие стремится выбрать лучшее оборудование, однако большинство производств останавливается на интеграции винтовых компрессоров. Достаточно простое устройство таких установок, тем не менее, нуждается в детальном анализе. Только понимая тонкости работы компрессора, можно применять его для решения профессиональных задач. Именно поэтому, сегодня мы расскажем вам о принципе работы винтового компрессора, а также о том, как устроено такое оборудование. Без лишних слов, приступим.
Небольшая историческая справка
Давайте для начала мельком рассмотрим историю создания винтового компрессора. Предыстория становления объекта нашей статьи позволит лучше прочувствовать достоинства подобного решения. Примечательно, что подобное оборудование появилось относительно недавно, первые винтовые установки получили распространение в 1940х годах. Да, за историю своего существования техника претерпевала небольшие изменения, установки становились компактнее, эффективнее и дешевле, но принцип действия оставался всё тем же. Для наглядности, мы можем сравнить винтовые компрессоры с обычными винтовыми насосами. И там и тут эффективное решение поставленных задач обеспечивается, благодаря большому числу двигательных оборотов.
В России исторически прижились 11 разновидностей подобных машин, включая:
-
Одноступенчатые
-
Двухступенчатые компрессоры;
-
Сухие компрессоры, работающая фактически без смазочного масла;
Всё это подкатегории для главного разделения на поршневые и винтовые компрессоры. Не волнуйтесь, далее мы подробно обсудим главные разновидности. А пока что рассмотрим сферы, в которых применяется описываемое оборудование.
Какие задачи решает такая техника?
На самом деле, спектр областей, в которых может применяться подобное оборудование, очень велик. Крупные предприятия, связанные с энергетической, машиностроительной промышленностью, наравне с добывающими и обрабатывающими компаниями широко ценят качественные винтовые компрессоры. Конечно, в зависимости от задач и газа, с которым работает техника, изменяется и сам тип установки. Зачастую на технику возлагаются обязанности по сжатию кислорода, однако на некоторых предприятиях необходимо продуктивно сжимать хлор. Для каждой задачи есть свои компрессоры.
На большинстве предприятий интегрированы такие виды техники как:
Поршневой компрессор
Один из самых дешевых и менее требовательных типов винтовой техники. Установки, функционирующие благодаря поршням, служат верой и правдой долгие годы, не требуя постоянного технического обслуживания. Отличный выбор, если на вашем предприятии требуется надежная техника, обеспечивающая давление выше 30 атмосфер. Для профилактики после 500 мото-часов работы необходимо проведение сервисного обслуживания. Необходим приезд сервисного инженера, чтобы он проверил сохранность поршней и других компонентов установки.
Однако при всех своих достоинствах такой тип компрессоров постепенно уходит в прошлое. Современные предприятия стремятся сократить уровни шума и вибрации, а поршневая техника, наоборот, создает слишком много звуковых и вибрационных колебаний. Это вариант для тех, кто может себе позволить организацию дополнительного фундамента для одного станка или же выделить специальное помещение для размещения этого устройства.
Выбор требовательных профессионалов. В основе лежат не шумные громоздкие поршни, а вращающаяся винтовая пара, которая сжимает не сам воздух, а воздушно-масляную смесь. Полученная смесь заполняет винтовой блок, который состоит из винтовой пары — лопастей, закреплённых на валу электродвигателя.
Готовая, сжатая до требуемого давления смесь, поступает в маслоотделитель, где выделяется непосредственно воздушная масса под давлением, а после этого происходит процесс фильтрации и очистки сжатого воздуха с последующей его подачей потребителю.
Основными преимуществами компрессоров винтового типа являются:
-
отсутствие ударных и вибрационных нагрузок;
-
более длительный срок эксплуатации;
-
низкий уровень шума;
-
долгие периоды между обслуживанием устройств;
-
большой показатель времени непрерывной работы.
Удобная, в меру компактная конструкция не только радует глаз, но и экономически выгодна, поскольку устройство требует меньше электроэнергии. Практически полное отсутствие издаваемых шумов позволяет интегрировать данный вид в любое производственное помещение. Его легко разместить в цеху, он не будет докучать шумом и вибрацией.
Несмотря на такую видовую сегрегацию, все установки имеют примерно одинаковое устройство, а значит, мы можем уверенно переходить к принципу работы и устройству винтового компрессора.
Что внутри установки?
Большинство моделей, за редчайшим исключением, содержит в себе 20 основных компонентов. О них – прямо сейчас:
-
Фильтр, предназначенный для очистки воздуха. Изначально в целях качественного функционирования станка стоит провести очистку воздуха, попадающего в фильтр, это поможет избавиться от пыльных и твердых частиц.
-
Обычно он имеет вид патрона в форме цилиндра, материал изготовления — гофрированная бумага. Установка фильтра возможна и внутри корпуса, и вне его. Фильтр оснащен специальными сетками для некрупного мусора, расположенными на корпусе, а также прежде клапанов;
-
Регулятор всасывания (другое название – всасывающий клапан), предназначенный для втягивания воздуха в сам винтовой блок.
Специфика моделей такого типа заключается в имеющемся винтовом компрессоре, он располагается у входа во всасывающий клапан, иными словами регулятор всасывания. Благодаря закрывающемуся всасывающему клапану компрессор свободно подвергается переводу в режим действия при отключенной нагрузке, а благодаря его открытию – переводится в работу под ее воздействием.
Вентиль всасывающего клапана представляет собой поворотный либо упорядоченно приходящий в движение диск вместе с уплотнением. В результате воздействия на регулирующую арматуру сжатого воздуха, поступающего из резервуара для масла посредством управляющего соленоидного клапана во внутренний либо внешний пневматический цилиндр, запорный элемент меняет свое положение.
Винтовой компрессор перед запуском нуждается в обязательном закрытии всасывающего клапана, который оснащен каналом малого сечения с механизмом обратного клапана. Это обеспечивает плотность сжатого воздуха с необходимым уровнем давления в ёмкости для масла с таким объемом, которого будет хватать для дальнейшего влияния направляющего пневмоцилиндра на поршень.
Винтовой блок для компрессора – самое нужное звено в функционировании компрессора. Здесь при помощи входного фильтра осуществляется сжатие поступающего воздуха.
Винтовой блок для компрессора
Корпус винтового блока состоит из пары совершающих обороты турбин – ведущей и ведомой. Вращаясь, они обеспечивают перемещение воздушных струй от поглощающей к нагнетающей стороне, при этом объем межтурбинных полостей синхронно снижается, иными словами сжимается.
Схема сжатия воздушных струй в винтовом блоке
Масло, содержащееся в корпусе винтового блока, обеспечивает уплотнение просвета между роторами, кроме этого оно используется при смазке деталей и для теплоотвода, возникающего в момент сжатия воздуха.
Кроме этого винтовой компрессор может иметь безмасляную основу, в таком случае отсутствует уплотняющая жидкость. В данных моделях вместо масла используются водяные впрыскивания в камеру сжатия.
Электродвигатель
Трехфазным асинхронным электродвигателем обеспечивается поставка вращения до ведущего ротора винтового блока.
Электродвигатель
Не беря в расчет модели мобильных винтовых компрессоров, где назначение механизма вращения осуществляется посредством дизельного двигателя.
Дизельный компрессор
Существует два варианта передачи вращения до ведущего ротора:
— используется клиноременная передача
Ременной привод
Либо используется механическое устройство с гибким компонентом.
Муфта эластичная
Если компрессор обладает высокой производительностью, то в таком случае возможно употребление шестеренчатого привода.
Зачастую возникает необходимость в урегулировании продуктивности винтового компрессора путем изменения частотности круговращения вала двигателя. При таких условиях используется электропривод – особый механизм, обеспечивающий снабжение двигателя электроэнергией.
Электропривод
Использование электропривода дает возможность в значительной степени корректировать результативность винтового компрессора согласно существующей необходимости в сжатом воздухе, исключая установку устройства в режим холостого хода перекрыванием всасывающего клапана.
Резервуар для масла
Резервуар для масла имеет ключевое значение в функционировании винтового компрессора:
-
служит главным накопителем сжатого воздуха;
-
повышает размер системы смазки компрессора, объем масла, обеспечивающий качественное отведение тепла, которое появляется в процессе воздушного сжатия;
-
действует в качестве разделителя основного объема масла от сжатого воздуха, поскольку воздушные струи проникают в стационарный сосуд из винтового блока по касательной, попадая затем на цилиндрическую поверхность, иными словами происходит завинчивание.
Резервуар для масла
Сепаратор
Разделитель – особый элемент, входящий в винтовой компрессор. Применение механизма обусловлено необходимостью достижения как можно меньшего количества масел в высвобождающемся из компрессора воздухе.
Те компрессоры, которые обладают невысокой степенью мощности обычно имеют внешний разделитель, а остальные – встраиваемый в емкость для масла.
Встроенный разделитель выглядит следующим образом:
Сепаратор встроенный
Внешний сепаратор выглядит так:
Сепаратор внешний
Общая схема разделителя в разрезе, где указанно направление движения масляных и воздушных масс:
Сепаратор в разрезе
Разделитель обеспечивает стабильный уровень присутствия масел в сжатом воздухе, по итогу его значение находится в пределах з-х мг/м3.
Клапан минимального давления
Поддержание такого давления масленой емкости, которое бы не становилось менее фиксированного в наименьшей мере соответствующего норме уровня, гарантирует качественную циркуляцию масла во время действия винтового компрессора.
Этот критерий исполняется, если в магистрали, с направленной на нее деятельностью винтового компрессора, в этот момент есть давление. Иначе, когда компрессор осуществляет заполнение незаполненного резервуара для сжатого воздуха, чтобы создать в нем повышенное давление, применяется специальный клапан наименьшего давления.
Клапан минимального давления в разрезе
Открытие этого клапана происходит во время давления на его входе, когда превышается то значение, которое было задано регулировкой сжатия пружины, закрывающей клапан.
Характерным давлением, при котором открывается клапан у винтовых устройств, признается его значение 4÷4,5 бар
Термостат
Винтовой компрессор схож с автомобильным двигателем, поскольку в нем так же присутствует два круга (большой и малый), служащих для охлаждения системы.
В момент, когда осуществляется пуск компрессора, по малому кругу начинает циркулировать масло, это способствует активному увеличению уровня температуры. Целесообразность этого заключается в том, чтобы во время сжатия воздуха блокировалось смешение выпадающего конденсата и масел, поскольку от этого напрямую зависит функционирование устройства.
Малый круг системы охлаждения
Когда необходимый показатель температуры масла будет достигнут, термостат откроется и будет обеспечивать циркуляцию в большом круге посредством охлаждаемого вентилятором радиатора.
Большой круг системы охлаждения
Чаще всего открытие термостата происходит при набирании маслом температуры выше 55°С, а целиком заканчивается при установлении температуры уже свыше 70°С.
Масляный фильтр
При функционировании винтового компрессора возможно появление в масле посторонних веществ (к ним относятся элементы износа двигающихся частей, а также мельчайшие пылевые частицы). Когда в циркуляционном контуре компрессора работает масляный фильтр, масло очищается от подобных вредных примесей.
Масляный фильтр в разрезе
Радиатор масляный и воздушный; вентилятор
Чтобы сжимаемые под воздействием винтового компрессора воздушные потоки могли охлаждаться, их стоит обработать посредством обдуваемого вентилятором радиатора. При выходе компрессора сжатый воздух будет обладать температурой, превышающей значение температуры внешней среды в границе +30 °С.
Масляный радиатор является отличным механизмом понижения температурного показателя циркулирующего масла. Преимущественно компрессоры оснащены общим, обдуваемым с помощью вентилятора блоком, включающим в себя оба радиатора: масляный и воздушный (без учета компрессоров высокой мощности).
Наиболее предпочтительным считается обеспечение работы вентилятора с помощью особого электродвигателя.
Вентиляторы охлаждения
Маленькие компрессоры очень часто оснащаются вентилятором с целью обеспечить обдув радиаторов. Такой вентилятор включается в комплект приводного двигателя.
Обратный клапан / Сетчатый фильтр
Особая масловозвратная линия, содержащая обратный клапан и сетчатый фильтр, служит для возвращения отделившегося от сжатого воздуха в сепараторе масла в циркуляционный контур компрессора.
Масловозвратная линия
С целью диагностики процесс реверсии масла следует контролировать в режиме реального времени. Поэтому отдельные компоненты масловозвратной линии имеют специфичный прозрачный вид.
Вывод сжатого воздуха
Когда наступает момент техобслуживания или ремонтных работ, следует удалить компрессор из магистрали сжатого воздуха, поэтому на выходном патрубке винтового компрессора следует разместить запорный кран.
С целью исключить воздействие термических и вибрационных искажений трубопровода на соединение, при соединении компрессорного выхода с магистралью важно пользоваться металлорукавом.
Винтовой компрессор
Винтовой (роторный, ротационный) холодильный компрессор представляет собой механизм с винтовыми роторами, для сжатия и подачи паров холодильного агента в холодильных машинах.
Принцип действия винтового компрессора
Поверхности винтовых роторов компрессора, при вращении валов на которых они находятся, создают полости (камеры), в которых и происходит процесс компрессии (сжатия и разряжения паров хладагента), в результате уменьшения и увеличения объема этих камер.
Конструкция и устройство винтового компрессора
Особенностью устройства винтового компрессора является наличие ведомого и ведущего валов с винтообразными поверхностями. А также отпадает необходимость применения клапанов, что значительно упрощает и, соответственно, облегчает обслуживание винтовых компрессоров.
Обычно, винтовой холодильный компрессор снабжен корпусом, электродвигателем, маслоотделителями, холодильником масла, фильтрами, и прочими дополнительными устройствами, в зависимости от особенностей конструкции компрессора.
Область применения винтового холодильного компрессора
Благодаря своим характеристикам и преимуществам, винтовые холодильные компрессоры обрели большую популярность в холодильных установках на судах и на передвижных компрессорных станциях.
Винтовые холодильные компрессоры часто используют в схемах параллельного включения для холодильных установок.
Разновидности винтовых холодильных компрессоров
Винтовые компрессоры можно классифицировать по многим признакам. Предлагаем Вашему вниманию систематизацию винтовых холодильных компрессоров по наиболее важным критериям:
Классификация винтовых холодильных компрессоров по количеству роторов
- винтовой компрессор с одним ротором;
- винтовой компрессор с двумя роторами;
Классификация винтовых холодильных компрессоров по типу привода
- винтовой компрессор с прямым приводом;
- винтовой компрессор с ременным приводом;
Классификация винтовых холодильных компрессоров по способу исполнения
- вертикальный винтовой компрессор;
- горизонтальный винтовой компрессор;
Классификация винтовых холодильных компрессоров по способу смазки
- маслозаполненные винтовые компрессоры — наиболее популярны сегодня. Это объясняется тем, что благодаря маслу компрессор более тихий, работает с меньшими потерями, может быть выполнен одноступенчатым;
- винтовые компрессоры сухого сжатия;
Классификация винтовых холодильных компрессоров по степени герметичности
- герметичный винтовой компрессор;
- полугерметичный винтовой компрессор — наиболее частое исполнение современных винтовых холодильных компрессоров;
Материал изготовления винтовых компрессоров
Изготовление винтовых компрессоров требует качественных материалов и высокой точности исполнения.
Свойства и особенности винтового компрессора
Винтовые холодильные компрессоры отличают надежность; компактные размеры; малые вибрации; долгий срок службы; легкость монтажа, дальнейшей эксплуатации компрессора, и обслуживания; плавность системы регулирования холодопроизводительности компрессора.
Винтовой компрессор сегодня, это компактное устройство, в виде отдельного модуля, которое легко интегрируется в систему, при помощи стандартных средств коммуникаций (трубы и кабели электропитания).
Компрессоры
Эта страница предназначена для учащихся колледжей, старших и средних школ. Для младших школьников более простое объяснение информации на этой странице: доступно на Детская страница. |
Большинство современных пассажирских и военных самолетов оснащены двигателями газотурбинные двигатели, также называемые реактивными двигатели.Есть несколько разных типы газотурбинных двигателей, но все газотурбинные двигатели имеют некоторые общие детали. Все турбины двигатели имеют компрессор для повышения давления поступающий воздух до того, как он попадет в камеру сгорания. Производительность компрессора имеет большое влияние на общий двигатель представление.
Как показано на рисунке выше, существует два основных типа компрессоры: осевой и центробежный .На картинке компрессор слева называется осевым компрессором, потому что поток через компрессор проходит параллельно оси вращения. В компрессор справа называется центробежным компрессор, потому что поток через этот компрессор повернут перпендикулярно оси вращения. Центробежные компрессоры, которые использовались в первых реактивных двигателях, до сих пор используются на малых турбореактивных двигателях а также турбовальный двигатели и как насосы на ракета двигатели.Современный большой турбореактивный и турбовентилятор в двигателях обычно используются осевые компрессоры.
Почему переход на осевые компрессоры? Средняя, одноступенчатая, центробежный компрессор может увеличить давление в 4 раза. аналогичный средний, одноступенчатый осевой компрессор увеличивает давление только на коэффициент 1,2. Но связать вместе несколько ступеней и изготовить многоступенчатый осевой компрессор . в многоступенчатый компрессор, давление перемножается из ряда в ряд (8 ступеней на 1.2 на ступень дает коэффициент 4,3). Это намного больше сложно изготовить эффективный многоступенчатый центробежный компрессор потому что на каждой ступени поток должен возвращаться к оси. Поскольку поток направлен перпендикулярно оси, двигатель с центробежный компрессор, как правило, шире, имеет большее поперечное сечение площадь, чем соответствующая осевая. Это создает дополнительные нежелательные сопротивление самолета. По этим причинам наиболее высокая производительность, высокое сжатие В турбинных двигателях используются многоступенчатые осевые компрессоры.Но если бы только требуется умеренная степень сжатия, центробежный компрессор намного проще в использовании.
Действия:
Экскурсии с гидом
Навигация ..
- Руководство для начинающих Домашняя страница
Microsoft Word — 1847731.docx
% PDF-1.5 % 97 0 объект > эндобдж 96 0 объект > поток application / pdf
Основы турбокомпрессора
Основы турбокомпрессораХанну Яэскеляйнен, Магди К.Хаир
Это предварительный просмотр статьи, ограниченный некоторым исходным содержанием. Для полного доступа требуется подписка DieselNet.
Пожалуйста, войдите в систему , чтобы просмотреть полную версию этого документа.
Abstract : Турбокомпрессоры — это центробежные компрессоры, приводимые в действие турбиной выхлопного газа и используемые в двигателях для повышения давления наддувочного воздуха. Производительность турбокомпрессора влияет на все важные параметры двигателя, такие как экономия топлива, мощность и выбросы. Прежде чем перейти к более подробному обсуждению специфики турбокомпрессора, важно понять ряд фундаментальных концепций.
Конструкция турбокомпрессора
Турбокомпрессор состоит из крыльчатки компрессора и колеса турбины выхлопного газа, соединенных сплошным валом и используемого для повышения давления всасываемого воздуха двигателя внутреннего сгорания. Турбина выхлопного газа извлекает энергию из выхлопного газа и использует ее для привода компрессора и преодоления трения. В большинстве автомобильных применений и компрессор, и турбинное колесо являются радиальными. В некоторых приложениях, таких как средне- и низкооборотные дизельные двигатели, можно использовать колесо турбины с осевым потоком вместо турбины с радиальным потоком.Поток газов через типичный турбокомпрессор с радиальным компрессором и турбинными колесами показан на Рисунке 1 [482] .
Рисунок 1 . Конструкция турбокомпрессора и расход газов(Источник: Schwitzer)
Центр-Жилье. Общий вал турбина-компрессор поддерживается системой подшипников в центральном корпусе (корпусе подшипника), расположенном между компрессором и турбиной (Рисунок 2). Узел колеса вала (SWA) относится к валу с прикрепленными колесами компрессора и турбины, т.е.е., вращающийся узел. Узел вращения центрального корпуса (CHRA) относится к SWA, установленному в центральном корпусе, но без корпусов компрессора и турбины. Центральный корпус обычно отлит из серого чугуна, но в некоторых случаях может использоваться и алюминий. Уплотнения предотвращают попадание масла в компрессор и турбину. Турбокомпрессоры для систем с высокой температурой выхлопных газов, таких как двигатели с искровым зажиганием, также могут иметь охлаждающие каналы в центральном корпусе.
Рисунок 2 . Турбонагнетатель в разрезеТурбонагнетатель отработавших газов бензинового двигателя, вид в разрезе, показывающий колесо компрессора (слева) и колесо турбины (справа). Подшипниковая система состоит из упорного подшипника и двух полностью плавающих опорных подшипников. Обратите внимание на охлаждающие каналы.
(Источник: BorgWarner)
Подшипники турбокомпрессора
Подшипники. Система подшипников турбонагнетателя выглядит простой по конструкции, но она играет ключевую роль в ряде важных функций.К наиболее важным из них относятся: контроль радиального и осевого движения вала и колес и минимизация потерь на трение в подшипниковой системе. Подшипниковым системам уделяется значительное внимание из-за их влияния на трение турбокомпрессора и его влияние на топливную эффективность двигателя.
За исключением некоторых крупных турбонагнетателей для тихоходных двигателей, подшипники, поддерживающие вал, обычно расположены между колесами в выступе. Эта гибкая конструкция ротора гарантирует, что турбокомпрессор будет работать выше своей первой и, возможно, второй критических скоростей, и, следовательно, может подвергаться динамическим условиям ротора, таким как завихрение и синхронная вибрация.
Уплотнения. Уплотнения расположены на обоих концах корпуса подшипника. Эти уплотнения представляют собой сложную конструктивную проблему из-за необходимости поддерживать низкие потери на трение, относительно больших перемещений вала из-за зазора в подшипниках и неблагоприятных градиентов давления в некоторых условиях.
Эти уплотнения в первую очередь служат для предотвращения попадания всасываемого воздуха и выхлопных газов в центральный корпус. Давление во впускной и выпускной системах обычно выше, чем в центральном корпусе турбокомпрессора, который обычно находится на уровне давления в картере двигателя.По существу, они в первую очередь предназначены для уплотнения центрального корпуса, когда давление в центральном корпусе ниже, чем во впускной и выпускной системах. Эти уплотнения не предназначены для использования в качестве основного средства предотвращения утечки масла из центрального корпуса в выхлопную и воздушную системы. Попадание масла в контакт с этими уплотнениями обычно предотвращается другими средствами, такими как масляные дефлекторы и вращающиеся пальцы.
Уплотнения турбокомпрессора отличаются от уплотнений с мягкой кромкой, которые обычно используются во вращающемся оборудовании, работающем при гораздо более низких скоростях и температурах.Уплотнение с поршневым кольцом — это один из наиболее часто используемых типов уплотнений. Он состоит из металлического кольца, внешне похожего на поршневое кольцо. Уплотнение остается неподвижным при вращении вала. Иногда используются уплотнения лабиринтного типа. Обычно уплотнения вала турбокомпрессора не предотвращают утечку масла, если перепад давления меняется на противоположный, так что давление в центральном корпусе выше, чем во впускной или выпускной системах.
###
Компрессорная станция Кастлера, аэропорт (US-0045) VFR, секционный корпус Samsung
КартыVFR в разрезе легко узнаваемы.Это наша страна с воздуха, усеянная достопримечательностями днем и ожидаемым освещением ночью. Это ваша возможность запечатлеть окрестности вашего любимого аэропорта с помощью личной части секции в аэропорту компрессорной станции Кастлер (US-0045) в штате Юта.
Эти высококачественные репродукции, полученные с помощью секционных данных высокого разрешения непосредственно от отдела цифровых услуг FAA, включают в себя мельчайшие детали. Обратите внимание, как точные цвета и четкие линии действительно выделяют их.
Обратите внимание, что изображения макетов не отражают фактическое качество изображения на репродукциях с высоким разрешением, поставляемых вместе с вашим заказом.
Нравится изображение, но не на чехле для телефона? Смотрите этот же рисунок в другом месте.
Этот элегантный чехол Samsung защищает ваш телефон от царапин, пыли, масла и грязи. У него прочная задняя часть и гибкие стороны, которые позволяют легко снимать и снимать, с точно выровненными надрезами и отверстиями.
- Гибридный термопластичный полиуретан (ТПУ) и поликарбонат (ПК), не содержащий бисфенола А
- Прочная, прочная задняя крышка из поликарбоната
- Гибкие полиуретановые борта
- .5-миллиметровая приподнятая рамка
- Прозрачные стороны
- Точно выровненные отверстия портов
- Совместимость с беспроводной зарядкой
- Графика нанесена УФ-печатью на корпус с гладкой матовой поверхностью
Все чехлы для телефонов напечатаны на заказ на нашем современном предприятии в Шарлотте, Северная Каролина.
100% пилотов считают этот обзор полезным
Купил этот чехол два месяца назад, и он на телефоне, которым я пользуюсь. Этот случай имел большой успех на работе, где я работаю летным инструктором, и дома в аэропорту Сан-Карлос.Возможно, я захочу купить еще один в Пало-Альто (ПАО).
1 0
100% пилотов считают этот обзор полезным
Корпус привлекает внимание. Всякий раз, когда я нахожусь на личной встрече — они все еще случаются иногда с COVID — я кладу телефон экраном вниз на стол, что почти всегда приводит к тому, что кто-то спрашивает: «Что у вас на телефоне?». Все думают, что чехол очень красивый. Кстати, обещаю не использовать чехол для навигации. 😁
1 0
94% пилотов считают этот обзор полезным
Кейс отправлен в течение дня после заказа.Идеально подошел к моему iPhone 11 Pro. Печать карты на обратной стороне подробно описана. Я пользуюсь этим футляром уже несколько недель, и изображение на обратной стороне все еще в идеальном состоянии — оно кажется довольно прочным и кажется, что это часть футляра, а не то, что было напечатано на нем.
17 1
Microsoft Word — 1847731.docx
% PDF-1.5 % 97 0 объект > эндобдж 96 0 объект > поток application / pdf
Вид в разрезе — обзор
10.3.2 Гибридный двигатель
Поперечный разрез типичного гибридного двигателя 1,8 ° показан на рис. 10.6. Статор имеет 8 основных полюсов, каждый с 5 зубьями, и каждый основной полюс имеет простую катушку. Ротор имеет две стальные торцевые крышки, каждая с 50 зубьями, разделенных постоянным магнитом.
Рис. 10.6. Гибридный (200 шагов / об) шаговый двигатель. Деталь показывает соосности зубьев ротора и статора, а также указывает угол шага 1,8 °.
Зубья ротора имеют тот же шаг, что и зубцы на полюсах статора, и смещены так, что осевая линия зуба на одной торцевой крышке совпадает с прорезью на другой торцевой крышке.Постоянный магнит намагничен в осевом направлении, так что один набор зубцов ротора имеет северную полярность, а другой — южную. Дополнительный крутящий момент достигается за счет добавления дополнительных пакетов и растяжения статора, как показано на рис. 10.7.
Рис. 10.7. Ротор типоразмера 34 (диаметр 3,4 дюйма или 8 см) 3-х слойный гибридный шаговый двигатель 1,8 °. Размеры торцевых крышек ротора и соответствующего аксиально намагниченного постоянного магнита оптимизированы для односекционной версии. Дополнительный крутящий момент достигается за счет добавления второго или третьего блока, при этом статор просто растягивается, чтобы приспособиться к более длинному ротору.
(Любезно предоставлено Astrosyn International Technology Ltd.)Когда в обмотках нет тока, единственным источником магнитного потока через воздушный зазор является постоянный магнит. Магнитный поток пересекает воздушный зазор от торцевой крышки N к полюсам статора, проходит в осевом направлении вдоль корпуса статора и возвращается к магниту, пересекая воздушный зазор к S-торцевой крышке. Если бы не было смещения между двумя наборами зубьев ротора, то при повороте ротора был бы сильный периодический момент выравнивания, и каждый раз, когда набор зубцов статора находился на одной линии с зубьями ротора, мы получали бы устойчивое положение равновесия.Однако есть смещение, и это приводит к тому, что момент выравнивания из-за магнита практически устраняется. На практике остается небольшой «фиксирующий» крутящий момент, и это можно почувствовать, если вращать вал, когда двигатель обесточен: двигатель имеет тенденцию удерживаться в своих ступенчатых положениях с помощью фиксирующего крутящего момента. Иногда это очень полезно: например, обычно достаточно удерживать ротор в неподвижном состоянии при отключении питания, чтобы двигатель можно было оставить, не опасаясь, что его случайно подтолкнут в новое положение.
8 катушек соединены в две фазные обмотки. Катушки на полюсах 1, 3, 5 и 7 образуют фазу A, а катушки на 2, 4, 6 и 8 образуют фазу B. Когда фаза A несет положительный ток, полюса статора 1 и 5 намагничиваются как южные, а полюса 3 а 7 становятся Севером. Зубья на северном конце ротора притягиваются к полюсам 1 и 5, в то время как смещенные зубцы на южном конце ротора притягиваются на одной линии с зубьями на полюсах 3 и 7. Чтобы сделать шаг ротора, фаза A переключается. выключен, и фаза B получает питание либо положительным, либо отрицательным током, в зависимости от требуемого направления вращения.Это заставит ротор переместиться на четверть шага зуба (1,8 °) в новое положение равновесия (шаг).
Двигатель постоянно шагает путем подачи питания на фазы в последовательности + A, — B, — A, + B, + A (по часовой стрелке) или + A, + B, — A, — B, + A (против часовой стрелки). Из этого будет ясно, что необходим биполярный источник питания (то есть такой, который может обеспечивать ток + ve или — ve). Когда двигатель работает таким образом, он называется «двухфазным с двухполюсным питанием».
Если биполярный источник питания недоступен, такая же схема включения полюсов может быть достигнута другим способом, если обмотки двигателя состоят из двух идентичных («бифилярная намотка») катушек.Для намагничивания северного полюса 1 положительный ток подается в один набор катушек фазы А. Но для намагничивания южного полюса 1 такой же положительный ток подается в другой набор катушек фазы A, которые имеют противоположное направление обмотки. Всего имеется четыре отдельных обмотки, и когда двигатель работает таким образом, он называется «4-фазным с однополярным питанием». Поскольку каждая обмотка занимает только половину пространства, m.m.f. каждой обмотки составляет только половину от полной обмотки, поэтому номинальная тепловая мощность явно снижается по сравнению с биполярным режимом работы (для которого используется вся обмотка).
Гибрид 200 шагов / об — это наиболее широко используемый шаговый двигатель общего назначения, доступный в различных размерах, как показано на рис. 10.8.
Рис. 10.8. Гибридные шаговые двигатели 1,8 °, типоразмеров 34 (диаметр 3,4 дюйма), 23, 17 и 11.
(любезно предоставлено Astrosyn International Technology Ltd.)Мы завершаем этот раздел, посвященный гибридным двигателям, комментариями по идентификации обмоток и предупреждение. Если детали двигателя неизвестны, обычно можно идентифицировать бифилярные обмотки путем измерения сопротивления от общего к двум концам.Если двигатель предназначен только для униполярного привода, один конец каждой обмотки может быть объединен внутри корпуса; например, 4-фазный униполярный двигатель может иметь только пять выводов, по одному на каждую фазу и один общий. Провода также обычно имеют цветовую кодировку для обозначения расположения обмоток; например, бифилярная обмотка на одном наборе полюсов будет иметь один конец красного цвета, другой конец — красно-белый, а общий — белый. Наконец, не рекомендуется снимать ротор гибридного двигателя, потому что он намагничивается на месте: удаление обычно вызывает уменьшение магнитного потока на 5–10% с соответствующим уменьшением статического момента при номинальном токе.
Генетический алгоритм оптимизации формы спиральной камеры центробежного компрессора
Представлена численная модель для генетической оптимизации спиральной камеры центробежного компрессора для легких коммерческих автомобилей. Форма поперечного сечения спиральной камеры представлена кубическими B-шлицами, а ее контрольные точки используются в качестве расчетных переменных. Цель глобальной оптимизации — максимизировать средний изоэнтропический КПД компрессора и перепад полного давления при проектной скорости и четырех рабочих точках.Численная модель состоит из решателя на основе плотности в сочетании с SST — моделью турбулентности с поправкой на вращение / кривизну и подходом с несколькими опорными системами. Первоначальная проверка показывает хорошее соответствие между численной моделью и измерениями на испытательном стенде. В результате оптимизации среднее повышение общего давления и КПД увеличиваются более чем по сравнению с первоначальными проектами оптимизации, в то время как максимальное повышение КПД составляет почти 2,5% при кг / с.
1.Введение
В связи с повышением экологической осведомленности и ужесточением политики в области загрязнения окружающей среды спрос на низкоуглеродные автомобили неуклонно растет. В результате получаются высокоэффективные двигатели меньшего размера. Одним из ключевых элементов этой разработки является турбонагнетатель, который помогает уменьшить объем двигателя, повысить эффективность и снизить выбросы.
Типичный компрессор турбокомпрессора для легковых и легких коммерческих автомобилей состоит из впускного отверстия, крыльчатки компрессора и улитки с выпускной трубой.Колесо компрессора хорошо изучено и интенсивно исследуется на протяжении последних десятилетий [1–4]. Напротив, спираль менее исследована. Тем не менее, эта часть играет важную роль в потоке компрессора по следующим причинам [5]: (1) влияние общей производительности центробежного компрессора, (2) искажение давления в нестандартных условиях и (3) ) влияют на пределы устойчивости компрессора. Кроме того, Уорстер [6] утверждает, что улитка определяет точку наилучшего КПД насосов и компрессоров, а не крыльчатку компрессора.Следовательно, очень важно понимать влияние проектных параметров на улитку и производительность компрессора.
Исследования различных геометрических параметров спирали проводились еще в 1940-х годах. Однако экспериментальные исследования различных конфигураций спиральной камеры ограничены из-за производственных затрат и времени. В последние годы было проведено больше исследований в отношении конструкции спиральной камеры в компрессорах, вентиляторах и насосах с использованием численного моделирования [7–11]. Одним из преимуществ является то, что конструкции можно тестировать виртуально, и при этом не возникают производственные затраты.Тем не менее общее количество исследований в открытой литературе по геометрии спирали невелико.
Обзор литературы . Из-за увеличения вычислительной мощности математическая оптимизация все больше и больше используется в процессе проектирования турбомашин. На рисунке 1 показано количество публикаций в год, перечисленных в Scopus [12], посвященных оптимизации компрессоров с использованием CFD. С начала прошлого десятилетия количество исследовательских работ по данной теме неуклонно увеличивается.Это результат растущего спроса на турбомашины с более высокими характеристиками, эффективностью и меньшим воздействием на окружающую среду. Из-за сложности современных силовых установок эти улучшения больше не могут быть достигнуты с помощью тематических исследований. По этой причине необходимо использовать оптимизацию, основанную на математических моделях и численном моделировании. Хотя данный обзор состоит только из публикаций, цитируемых Scopus, тем не менее, тенденция заметна, и общее количество исследовательских работ по этой теме как в академических кругах, так и в промышленности будет выше.
Несмотря на рост оптимизации на основе CFD, огромное количество исследовательских работ в одностороннем порядке сосредоточено на улучшении конструкции крыльчатки и лопаток компрессора. К этой части компрессора относится больше исследованных публикаций. Одна из причин — более простая геометрия и создание сетки для рабочего колеса. Геометрию лезвия можно легко создать с помощью специализированных коммерческих инструментов, таких как ANSYS® BladeGen и ANSYS TurboGrid. Кроме того, параметризация формы поперечного сечения может быть достигнута с помощью шлицев в сочетании с экструзией в продольном направлении.Это позволяет быстро создавать геометрию и сетку, что очень важно для автоматической оптимизации. Кроме того, упрощения, такие как двухмерное или осесимметричное моделирование, могут использоваться для быстрой оценки характеристик лопастей в осевых и радиальных машинах.
Напротив, только небольшая часть работы по оптимизации была выполнена на геометрии спиральной камеры. Автоматическое создание геометрии спиральной камеры и создание сетки очень сложно из-за сложной формы. Кроме того, нельзя делать никаких геометрических упрощений, и необходимо моделировать полную трехмерную спиральную камеру.Это часто включает крыльчатку компрессора перед улиткой, чтобы обеспечить взаимодействие между обеими частями. Следовательно, это требует больше времени по сравнению с исследованиями лопастей или крыльчатки. По этим причинам исследовательская работа в области оптимизации спиральной камеры очень ограничена или ограничена упрощенными геометрическими вариациями. Важная работа по этой теме представлена ниже.
Jang et al. [13] численно проанализировали центробежный вентилятор с коэффициентом расхода 0,139, коэффициентом давления 1.29 и КПД в расчетной точке. Рабочее колесо имеет выходной диаметр при расчетной скорости. Улитка имеет трапециевидную форму с симметричным входным отверстием (см. Рисунок 2). Высота и ширина используются в качестве параметров конструкции со справочными значениями и соответственно. Повышение давления и изоэнтропическая эффективность определены как целевые функции. Экспериментальные точки определяются с использованием плана экспериментов (DoE), а целевая функция в каждой точке оценивается с использованием стационарного моделирования.Наконец, поверхность отклика рассчитывается с использованием полинома второго порядка.
Коэффициент давления нагнетателя и КПД оптимизированной модели увеличены на и, соответственно, по сравнению с эталонной моделью. Общий разброс для разной ширины и высоты приблизительно соответствует эффективности. Основная причина разницы в эффективности определяется вторичным потоком в углах.
Baloni et al. [14] исследовали спиральную конструкцию, используя метод оптимизации и дисперсионного анализа Тагучи (ANOVA).Работа основана на численном моделировании центробежного нагнетателя с выходным диаметром 10 мм при проектной скорости. Коэффициент расхода и коэффициент давления эталонной модели составляют 0,245 и 0,69 соответственно. В качестве переменных конструкции определены три геометрических параметра: ширина улитки нагнетателя, угол язычка и радиальное положение улитки. Целевая функция состоит из изменения статического давления на выходе из крыльчатки, потерь внутри улитки и общего давления на выходе улитки.Моделирование выполняется с использованием стационарного подхода. Оптимизированная численно геометрия подтверждается измерениями на испытательном стенде.
Усовершенствования оптимизированной геометрии спиральной камеры показаны в Таблице 1. Повышение эффективности значительно с примерно. Однако базовая эффективность довольно низкая при. Следовательно, улучшения более осуществимы. Исследователи предполагают, что ширина воздуходувки в 1,5 раза больше ширины крыльчатки для оптимальной производительности. Кроме того, угол язычка должен быть таким, чтобы свести к минимуму колебания статического давления на выходе рабочего колеса и уменьшить общее давление на выходе улитки.