основы пайки, пайка печатных плат и технология. Монтаж SMD домашних условиях
Хорошая пайка хотя и не так важна, как правильно размещение радиоэлементов, но она тоже играет немалую роль. Поэтому мы рассмотрим SMD монтаж — что для него нужно и как его следует проводить в домашних условиях.
Запасаемся необходимым и проводим подготовку
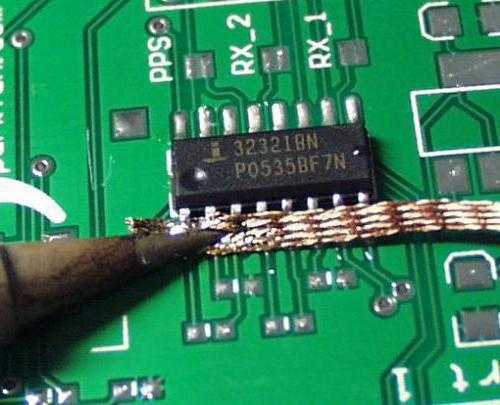
- Припой.
- Пинцет или плоскогубцы.
- Паяльник.
- Небольшую губку.
- Бокорезы.
Для начала необходимо включить паяльник в розетку. Затем смочите водой губку. Когда паяльник нагреется до такой степени, чтобы он мог плавить припой, то необходимо покрыть им (припоем) жало. Затем протрите его влажной губкой. При этом следует избегать слишком длительного контакта, поскольку он чреват переохлаждением. Для удаления остатков старого припоя можно протирать жало об губку (а также чтобы поддерживать его в чистоте). Подготовка проводится и по отношению к радиодетали. Делается все с помощью пинцета или плоскогубцев. Для этого необходимо согнуть выводы радиодетали так, чтобы они без проблем могли войти в отверстия платы. Теперь давайте поговорим о том, как проводится монтаж SMD компонентов.
Начало работы с деталями
Первоначально необходимо компоненты вставить в отверстия на плате, которые предназначаются для них. При этом внимательно следите за тем, чтобы была соблюдена полярность. Особенно это важно для таких элементов, как электролитические конденсаторы и диоды. Затем следует немного развести выводы, чтобы деталь не выпадала из установленного места (но не перестарайтесь). Непосредственно перед тем как начинать пайку, не забудьте протереть жало губкой ещё раз. Теперь давайте рассмотрим, как происходит монтаж SMD в домашних условиях на этапе паяния.
Закрепление деталей
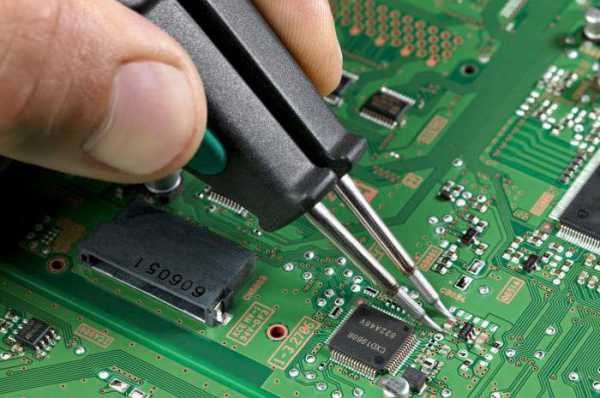
Проверка качества работы
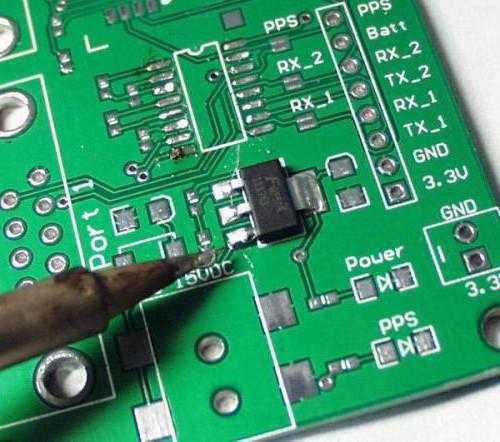
- В идеале должна быть соединена контактная площадь и вывод детали. При этом сама пайка должна обладать гладкой и блестящей поверхностью.
- В случае получения сферической формы или наличия связи с соседними контактными площадками необходимо разогреть припой и удалить его излишки. Учитывайте, что после работы с ним на жале паяльника всегда есть его определённое количество.
- При наличии матовой поверхности и царапин расплавьте припой ещё раз и, не сдвигая детали, дайте ему остыть. В случае необходимости можно добавить его ещё в небольшом количестве.
Для удаления остатков флюса с платы можно воспользоваться подходящим растворителем. Но эта операция не является обязательной, ведь его наличие не мешает и не сказывается на функционировании схемы. А теперь давайте уделим внимание теории пайки. Потом мы пройдёмся по особенностям каждого отдельного варианта.
Теория
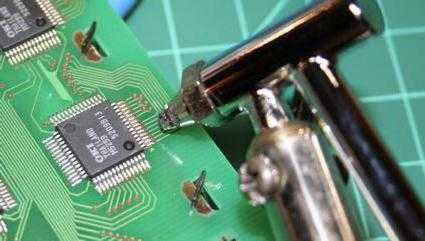
- Необходимо, чтобы были зачищены поверхности деталей, которые будут паяться. Для этого важно удалить все пленки оксидов, которые образовываются со временем.
- Деталь должна в месте пайки нагреваться до температуры, которой достаточно, чтобы плавить припой. Определённые трудности здесь возникают, когда есть большая площадь с хорошей теплопроводностью. Ведь элементарно может не хватить мощности паяльника для нагрева места.
- Необходимо позаботиться о защите от действия кислорода. Эту задачу может выполнить колофоний, который образует защитную пленку.
Наиболее частые ошибки
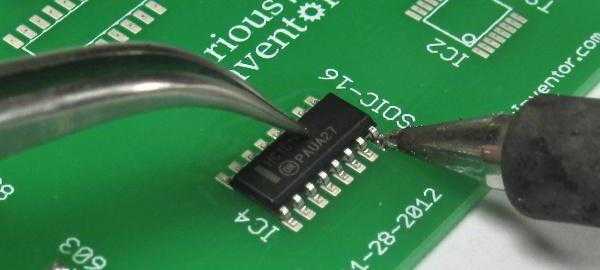
- Места пайки касаются кончиком жала паяльника. При этом подводится слишком мало тепла. Необходимо жало прикладывать таким образом, чтобы между жалом и местом пайки создавалась наибольшая площадь контакта. Тогда SMD монтаж получится качественным.
- Используется слишком мало припоя и выдерживаются значительные временные промежутки. Когда начинается сам процесс, уже успевает испариться часть флюса. Припой не получает защитный слой, как результат – оксидная пленка. А как правильно совершать монтаж SMD в домашних условиях? Для этого профессионалы места пайки качаются одновременно и паяльником, и припоем.
- Слишком ранний отвод жала от места пайки. Нагревать следует интенсивно и быстро.
Можно взять конденсатор для SMD монтажа и набить на нём руку.
Пайка свободных проводов
Сейчас мы будем проходить практику. Допустим, у нас есть светодиод и резистор. К ним нужно припаять кабель. При этом не используются монтажные платы, штифты и иные вспомогательные элементы. Для выполнения поставленной цели нужно выполнить такие операции:
- Снимаем изоляцию с концов провода. Они должны быть чистыми, поскольку были защищены от влажности и кислорода.
- Скручиваем отдельные проводки жилы. Этим предотвращается их последующее разлохмачивание.
- Залуживаем концы проводов. Во время этого процесса необходимо разогретое жало подвести к проводу вместе с припоем (который должен равномерно распределиться по поверхности).
- Укорачиваем выводы резистора и светодиода. Потом необходимо их залудить (независимо от того, старые или новые детали используются).
- Удерживаем выводы параллельно и наносим небольшое количество припоя. Как только им будут равномерно заполнены промежутки, необходимо быстро отвести паяльник. Пока припой не затвердеет полностью, деталь трогать не нужно. Если это всё же произошло, то возникают микротрещины, которые негативно сказываются на механических и электрических свойствах соединения.
Пайка печатных плат
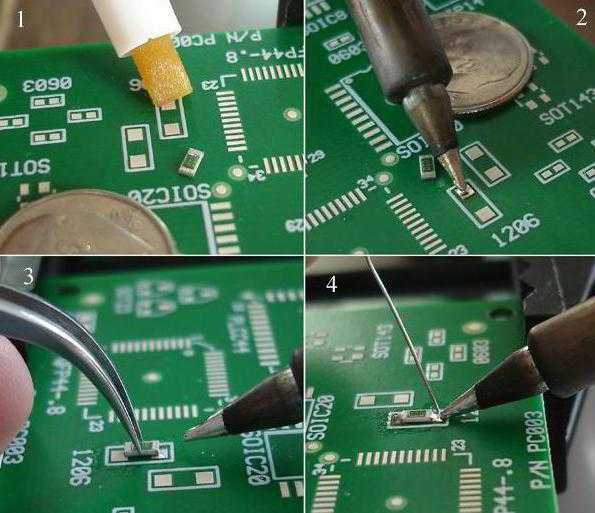
Теперь давайте разберёмся, как происходит SMD монтаж в данном случае. Первоначально жало паяльника и припой одновременно подводят к месту пайки. Причем нагреваться должны и обрабатываемые выводы, и плата. Необходимо держать жало, пока припой равномерно не покроет всё место контакта. Затем его можно обвести по полукругу вокруг обрабатываемого места. При этом припой должен перемещаться во встречном направлении. Наблюдаем, чтобы он равномерно распределился на всей контактной площади. После этого убираем припой. И последний шаг – это быстрый отвод жала от места пайки. Ждём, пока припой приобретёт свою окончательную форму и застынет. Вот так в данном случае проводится монтаж SMD. Печатная плата при первых попытках будет выглядеть не ахти, а вот со временем можно научиться делать на таком уровне, что не отличишь и от заводского варианта.
fb.ru
Какое оборудование применяют для пайки
Одним из действенных и надежных способов соединения материалов считается пайка. Раньше ее применяли для металлов и их сплавов, но пайка также подходит для соединения кусков стекла, пластмассы, керамики.
Существует множество видов пайки, для каждого из них используется специальное паяльное оборудование, инструменты и приспособления.
Паяльник
К наиболее часто используемым инструментам при паяльных работах относится паяльник. Без него сложно представить оборудование рабочего места. Паяльники применяют любители и профессионалы. Все зависит от вида инструмента.
Молотковый
Для соединения больших, массивных деталей применяют молотковые паяльники, названные так из-за своей формы, похожей на молоток. Они разогреваются в печах или жаровнях и, обладая большой тепловой инерцией, долго остаются нагретыми.
Такое оборудование используют для пайки крупных деталей.
Электрический
Самый традиционный способ пайки – при помощи электрического паяльника. Устроен он очень просто – в металлическом корпусе заключен нагревательный элемент, который разогревает жало – медный стержень. От мощности нагревательного элемента зависит температура нагрева паяльника.
Содержание процесса паяльных работ заключается в том, чтобы разогреть контактным способом соединяемые детали и скрепить их специальным составом, называемым припоем. После остывания получается прочное соединение, способное проводить электричество, если соединяемые детали являются проводниками.
Профессиональный электропаяльник может быть с регулятором напряжения. В этом случае возможна регулировка температуры жала, что очень важно при сборке и монтаже электронных схем.
Особый интерес представляет индукционное оборудование. В индукционных паяльниках происходит саморегуляция нагрева, они экономно расходуют электричество.
Выпускают ультразвуковое паяльное оборудование. Ультразвуковой паяльник снабжен генератором, вырабатывающим сигнал высокой частоты.
Помимо паяльника, работающего от бытовой сети, в состав оборудования поста для пайки может входить паяльный инструмент, питающийся напряжением 12 или 24 вольта. Он подходит для отладки работы электронных схем и для монтажа деталей и компонентов, которые могут выйти из строя от перегрева.
Электрические паяльники могут быть и беспроводными, работающими от пальчиковых аккумуляторов.
Газовый
Очень удобны в работе газовые паяльники, разогрев которых происходит от сгорания газа. Газовое оборудование представлено огромным количеством моделей, отличающихся размерами, системой розжига, наличием регулятора температуры.
С помощью газового паяльного оборудования можно плавить твердые высокотемпературные припои. Выпускают посты для газовой пайки медных труб, в которые входят баллоны, редукторы, платформа и горелка.
Недостатками электрического или газового паяльников является невозможность одновременного прогрева большой площади при малой мощности. В этом случае используются другие виды оборудования.
Инфракрасные станции и фены
Модели термовоздушного паяльного оборудования (фены) используются в основном для демонтажа и объемного монтажа микросхем на платах электронных устройств. Очень часто фен входит в комплектацию паяльной станции, состоящей еще из электрического паяльника и блока управления.
Паяльная станция позволяет производить установку и контроль параметров инструментов, входящих в нее, обеспечивая высокое качество шва.
Нередко в состав оборудования для паяльной станции входит стол с возможностью прогрева деталей или монтажных плат снизу.
Эта установка использует инфракрасные источники тепла – лампы, нагревательные элементы. Некоторые конструкции столов для подогрева снабжены кронштейнами и штативами, что позволяет закреплять платы.
Схожим действием с паяльным феном обладает инфракрасное оборудование. С его помощью также можно обеспечить нагрев большой площади, не допуская контакта с элементами микросхем.
Инфракрасные паяльные станции позволяют контролировать паяние и обеспечивать плавное остывание металла. Это дорогостоящее оборудование, которое представляет собой целые вычислительные комплексы с наборами датчиков, процессорами и целым перечнем вспомогательных инструментов.
Инструменты и приспособления
При ручной пайке недостаточно наличия только паяльного оборудования. Не имея необходимых дополнительных приспособлений, невозможно бывает не то чтобы качественно, а вообще что-нибудь спаять. К таким приспособлениям относятся:
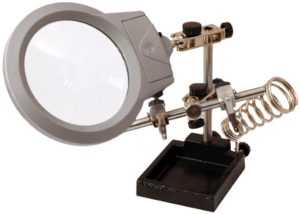
- паяльная лампа;
- пинцет;
- набор надфилей;
- кусачки;
- увеличительное стекло и штатив;
- струбцины;
- подставки.
Один из необходимых инструментов – это пинцет. Он служит для того, чтобы удерживать мелкие детали в положении, в котором их нужно припаять.
Кроме того, зачастую металлический пинцет, зажимая выводы, служит теплоотводом, когда происходит пайка полупроводников или иных требовательных к температуре предметов.
Еще одним инструментом, часто используемым при работе, является надфиль. Плоским надфилем можно очистить жало паяльника от нагара перед тем, как облудить его.
Круглым надфилем с острым концом можно аккуратно прочистить монтажные отверстия на плате. Иногда приходится зачищать выводы компонентов схем, перед тем как смонтировать их на место.
Для работы с проводами и кабелями понадобятся кусачки-бокорезы. С их помощью отрезают провода, зачищают изоляцию, иногда механически снимают лишний припой.
Для демонтажа электронных компонентов и плат из корпусов электроприборов могут понадобиться отвертки различных видов. А так как некоторые компоненты могут выйти из строя при воздействии даже слабого магнитного поля, понадобится устройство для размагничивания стальных инструментов.
Очень часто приходится паять крупные детали. Нагреть их паяльником, даже самым мощным, невозможно. В этом случае детали около места будущей пайки прогревают паяльной лампой, а после этого уже пропаивают паяльником. Паяльные лампы могут работать на бензине, керосине, газе. Некоторые модели работают на спирте.
Чтобы зафиксировать детали между собой и на столе, неплохо иметь под рукой набор металлических струбцин. При их использовании можно точно сориентировать детали одну относительно другой и сохранить это положение в течение всего времени пайки и остывания.
Полезное приспособление для пайки – поставка. На нее можно не опасаясь возгорания помещать горячий паяльник. Такое простейшее оборудование зачастую делают своими руками.
Для соединения мелких деталей, что очень часто происходит при ремонте ювелирных изделий, понадобится лупа со стеклом большого диаметра, установленная на штатив.
При постоянных частых паяльных работах неплохо установить в помещении оборудование для думоудаления.
Промышленная пайка
На предприятиях тяжелой промышленности используются совершенно иные виды паяльного оборудования. Соединение больших деталей и конструкций в промышленных условиях происходит в печах.
В этом случае достигается наиболее высокое качество, так как при использовании печного оборудования можно постоянно контролировать состояние металла, поддерживать необходимую температуру и давление. Защита металла от окисления производится путем введения в камеру печи флюсов.
Печи для пайки различаются по принципу нагрева. Они бывают индукционными, газовыми, электрическими. Подаются и извлекаются заготовки различными способами в зависимости от конструкции печного оборудования. Это может быть ручная подача, ленточный конвейер, шахтная и элеваторная подачи.
В печах с ручной подачей нагрев и остывание деталей, паяльной камеры происходит в пределах одного цикла пайки. После остывания загружаются новые детали. В этой печи легче всего контролировать течение процесса и его продолжительность.
В конвейерном паяльном оборудовании нагрев происходит постоянно, а остывают детали уже после извлечения из камеры. Такие печи используются для создания большого количества одинаковых, серийных изделий.
Шахтные и элеваторные печи используют для изготовления крупногабаритных объемных конструкций, которые собирают прямо в печи и затем производят процесс пайки при полностью контролируемых параметрах.
Вакуумное паяльное оборудование используют для соединения изделий из сильноокисляющихся материалов. Паяные швы, произведенные в таких печах, отличаются чистотой и однородностью, что обеспечивает их прочность.
По причине менее высокой температуры и совершенно иного, чем при сварочных работах, воздействия на металл, паяные соединения более стойки к коррозии и к механическим воздействиям.
Несмотря на давнее изобретение пайки и создание новых методов соединения металлов и сплавов, паяльные работы с использованием специального оборудования остаются востребованными и в настоящее время.
svaring.com
Советы начинающим радиолюбителям. Секреты пайки.
Как и при других работах, так и при пайке деталей есть свои секреты и особенности. Некоторые думают: всё просто — включил паяльник, взял припой, канифоль и паяй себе сколько угодно!
Но если разобраться во всём по порядку — оказывается, это не так просто. Уметь правильно паять — это своего рода искусство и опыт приходит со временем. Чтобы хорошо и качественно паять нужно знать некоторые основные секреты пайки, о которых и пойдёт речь в этой статье.
Хороший паяльник
Конечно первое, что вам нужно — это паяльник. На рынке сегодня есть много различных дешевых паяльников. Большинство из них работают от сети ~ 220В и не контролируют температуру нагрева жала. На более дорогих имеется регулятор, когда паяльник нагрелся — снижается напряжение и температура паяльника поддерживается одинаковой.
Есть множество схем по регулированию температуры паяльника, поэтому вы можете использовать и простой обычный паяльник через схему регулирования напряжения.
Один из секретов качественной пайки — чистота жала паяльника и его нагрев. Если жало грязное, им трудно работать — плавиться припой будет, а к поверхности жала не прилипнет. Жало надо обязательно зачистить и залудить — покрыть тонким слоем припоя. Делают это так. Разогрейте паяльник и зачистите его жало напильником или шлифовальной шкуркой. Опустите жало в канифоль, а затем прикоснитесь им к кусочку припоя. В слое расплавленного припоя поводите жало по деревянной палочке (или по подставке) так, чтобы вся поверхность его покрылась слоем припоя. Со временем жало будет покрываться окисным налетом темного цвета, мешающим пайке. Вот тогда снова залудите его.
Для тонкой работы необходим паяльник с тоненьким кончиком, особенно если вы работаете с поверхностным монтажом SMD компонентов.
Обычно хватает паяльника с мощностью от 30 до 40 Вт для общей работы. Вы должны держать паяльник при пайке в течение примерно 3 — 4 секунды для избежания перегрева радиоэлементов.
Дополнительные инструменты и приспособления
Кроме паяльника есть несколько других вещей, которые я считаю необходимым для хорошего пайки. Конечно, один из которых — это припой. Припоем называется легкоплавкий металлический сплав, которым спаиваются провода и выводы деталей. При радиомонтаже чаще применяют оловянно-свинцовые припои, представляющие сплав олова и свинца. Температура плавления припоя 180 — 200° С. Обозначаются они тремя буквами — ПОС (припой оловянно-свинцовый), например: ПОС-40, ПОС-60 цифры — это содержание олова в процентах. Я предпочитаю припой ПОС-60 (60/40) — это самый распространенный припой. Он состоит из 60% олова и 40% свинца с флюсом в центре припоя.
Флюсы — это противоокислительные вещества. Они применяются для того, чтобы подготовленные к пайке места деталей или проводников не окислялись во время пайки. Без флюса припой может не прилипнуть к поверхности металла. Припой бывает различных диаметров и вы можете использовать какой вы предпочитаете в зависимости от того что паяете. Лично мне нравится тонкий вещи 0.56 мм для большинства работ. Чтобы можно было паять в труднодоступных местах, неплохо запастись жидким флюсом, о котором говорилось выше. Флюс можно приготовить самому: для этого измельчают канифоль в порошок и всыпают в борный спирт или глицерин. Помешивая раствор палочкой, подсыпают канифоль до получения густой кашицы. Такую канифоль наносят на спаиваемые места тонкой палочкой или кисточкой.
Обязательно, соблюдайте правила безопасности при работах с припоем: мойте руки после пайки теплой водой с мылом, не вдыхайте пар от расплавленного припоя! Это правило актуально для всех типов припоя!
Помните, что при пайке выделяются вредные для здоровья пары олова и свинца. Ни в коем случае нельзя наклоняться над местом пайки и вдыхать испарения. Летом старайтесь паять у открытого окна, зимой чаще проветривайте помещение. Хорошо бы иметь вытяжку над рабочим местом!
Держатель для паяльника
Вы должны иметь удобный держатель для паяльника. Есть подставки вместе с очисткой наконечника жала паяльника.
Другой инструмент, которым я часто пользуюсь — это вакуумный всасыватель припоя. Я считаю, что это один из недорогих и лучших способов освободить деталь от припоя.
Конечно, есть и другие вещи, которые помогут с пайкой, например, хорошо освещенное место работы, пинцет с защёлкой и т.д. У меня есть некоторые канавки и отверстия, просверленные в деревянном бруске, для того чтобы можно было прижать например, вал потенциометра и держать его во время пайки, а также для спайки проводов и т.д.
Полезные советы хорошей пайки
Я например, паяю деталь, а затем обрезаю их выступающие выводы. Конечно, некоторые сначала обрежут по размеру, а потом паяют детали и это может выглядеть аккуратнее и удобнее. Но я считаю — обрезка после пайки быстрее и проще. Используете для этого хорошие острые кусачки, чтобы не повредить дорожки.
Если вы паяете радиодетали, чувствительные к перегреву — используйте теплоотвод. Это может быть обычный пинцет, утконосы или плоскогубцы. Придерживайте ножку радиодетали во время пайки. Если надо спаять концы двух залуженных проводников, плотно прижмите их друг к другу и к месту касания приложите паяльник с каплей припоя на конце жала. Как только место спайки прогреется, припой растечется и заполнит промежутки между проводниками. Плавным движением паяльника распределите припой равномерно по всему месту спайки. Продолжительность пайки не должна превышать 3-5 с, особенно это касается радиодетали, чувствительные к перегреву (транзисторов, микросхем, диодов, стабилитронов…) после этого паяльник убирают. Припой быстро затвердеет и прочно скрепит детали, в это время надо следить, чтобы детали или проводники не смещались в течение 10 с. Для быстроты остывания можно подуть, заодно мы будем сдувать испарения припоя от себя в сторону.
Особенности монтажа платы
Во время налаживания конструкций приходится перепаивать проводники или заменять детали. Это нужно учитывать при монтаже. Так, концы деталей, соединяющиеся согласно схеме с общим проводником, следует припаивать не в одной точке, а на некотором расстоянии друг от друга. Не рекомендуется закручивать концы деталей вокруг проводника.
Если вы делаете плату с большим количеством компонентов, сначала подумайте о порядке, чтобы все радиодетали уместились на ней. Учитывайте размер деталей, а также нагрев во время работы. Не располагайте близко к нагреваемым радиоэлементам другие компоненты, особенно электролитические конденсаторы. Ели необходимо оставьте место под радиатор.
Пайка проводов
Если вы паяете многожильный провод — сначала снимите с него необходимый отрезок изоляции, скрутите жилки провода, а затем облудите его припоем.
Если вы будете залуживать лакированный провод (ПЭЛ, ПЭВ), зачистите это место шлифовальной шкуркой или перочинным ножом и поднесите кусок канифоли. Плавным движением паяльника равномерно распределите припой по залуживаемой поверхности.
Места проводников и деталей, предназначенных для пайки, должны быть зачищены до блеска. Тщательно зачищенный проводник кладут на кусок канифоли и хорошо прогревают паяльником. Канифоль быстро расплавится, а имеющийся на паяльнике припой растечется по проводнику. Поворачивая проводник и медленно двигая по нему жало паяльника, добейтесь равномерного распределения припоя по поверхности проводника.
Я мог бы добавить еще несколько советов, но я надеюсь, что вы нашли что-то полезное для себя и в скором времени сами будете давать полезные советы новичкам. 🙂
Теперь берите паяльник в руки и воплотите свои мечты в реальность, произведите впечатление на своих друзей своими интересными электронными самоделками!
Зотов А., Волгоградская обл.
П О П У Л Я Р Н О Е:
- Какой планшет лучше купить?
- Ремонтируем стул или табурет своими руками
- Учимся печатать быстро на клавиатуре
Планшетный компьютер (планшетник) — это практически полноценный персональный компьютер, с возможностью подключения мыши и клавиатуры. Такие планшеты работают под операционными системами: Windows, MacOS X, Android и вполне совместимы с обычными настольными компьютерами. Такие устройства сейчас всё большей популярностью становятся, особенно у детей. Они будут отличным выбором для рабочего использования, учёбы и конечно, для игр.
Подробнее…
Весёлые мухоморы
Со временем стул или табурет под стройными или грузными телами 🙂 теряет былую красоту своего внешнего вида. Их обычно красят и используют ещё несколько лет.
Если немного приложив старание и выдумку, то получатся замечательные новенькие стульчики, вписывающиеся в дизайн Вашей комнаты. Будут иметь окрас, который нравится именно Вам!
Подробнее…
Сейчас компьютеры прочно вошли в нашу жизнь. Работая на компьютере приходится часто печатать. А вы умеете быстро печатать на клавиатуре? Вы ищите буквы и печатаете одним пальцем? Небольшая бесплатная программка Rapid Typing Tutor поможет вам освоить клавиатуру компьютера и научит вас в игровой и непринуждённой форме печатать быстро.
Подробнее…
— н а в и г а т о р —
Популярность: 4 601 просм.
ПОДЕЛИТЕСЬ С ДРУЗЬЯМИ
www.mastervintik.ru
Современные технологии пайки в условиях российского производства
Роль пайки в современном машиностроении
Пайка получила бурное развитие в 5060х годах ХХ столетия, когда человечество устремило свои взгляды на покорение воздушного и космического пространства. Для реализации идей требовались новые материалы со способностью работать в экстремальных режимах, а также технологии их соединения. В этот период пайка превращается из технологии ремесленников в самостоятельное научнотехнологическое направление. Жизнь расставила по местам области применения технологий пайки и сварки, хотя порой возникают необоснованные споры по поводу старшинства или значимости. Пайку следует рассматривать как самостоятельную технологию соединения, основанную прежде всего на явлениях физической химии и законах металловедения.
Применение пайки открыло перед учеными и технологами новые возможности конструирования соединения, новые материалы и сплавы для их производства. Причем сплавы для пайки отличались сложностью и точностью химического состава. Большое разнообразие способов нагрева расширило возможности технологии пайки. В основном главными инициаторами и потребителями новых решений являлись авиационная отрасль и ракетостроение. Создание сотовых конструкций, решетчатых крыльев, высокоэффективных теплообменников было возможным только благодаря технологии пайки. Ее самым главным достижением явилось создание прочных соединений, обеспечивающих высокую герметичность. Причем прочность рассматривалась как при статических, так и при знакопеременных нагрузках. Также несомненной заслугой пайки является возможность соединения разнородных материалов, а также композитов, которые часто нельзя соединить другими методами.
Таким образом, наряду со сваркой и склеиванием пайка заняла достойное место в научнотехническом прогрессе благодаря уникальным возможностям. Однако пайка до сих пор является сложным процессом, зависящим от правильного выбора материалов, подготовки поверхностей, конструкции соединения и фиксации необходимого зазора, среды или флюса, способов нагрева. Наконец после формирования паяного шва жидким припоем имеются широкие возможности получения разнообразных структур шва, которые, в конечном счете, определяют свойства соединения. Получается, что технология основана на самопроизвольном процессе смачивания и растекания припоя по поверхности соединяемых материалов, заполнения зазора с последующей кристаллизацией. Человек обеспечивает условия протекания указанных процессов созданием наиболее благоприятных условий.
Благодаря этому пайка получила широкое распространение в мире для создания массовых производств, отличающихся высокой производительностью и уровнем автоматизации и механизации. Это достигается только при наличии стабильности входных параметров процесса: качества припоя и флюсов, технологических режимов и автоматического управления нагревом изделий и их охлаждения. При правильной организации производства получают стабильный прогнозируемый выход с заранее заданными свойствами.
Поэтому пайка в современном мире широко используется в транспорте, в частности, в автомобилестроении, а также в энергетике, холодильной и криогенной технике, производстве приборов и электронных схем, горнодобывающего и металлорежущего инструмента, теплообменной аппаратуры и т.п.
Рис. 1 Элементы создания паяного соединения
При этом не следует считать, что существует только один уникальный способ соединения пайкой конкретной конструкции. Так как в процессе участвует несколько компонентов (рис. 1), то, управляя их наполнением, можно варьировать технологию пайки для создания мелкосерийного или массового производства. Выбор элементов определяет стоимость процесса, его гибкость и возможность адаптации к изготовлению других изделий. Таким образом, получить одно и то же соединение можно различными материалами, технологиями нагрева и применяя различное оборудование.
Особенности пайки обусловили следующие мировые тенденции в ее развитии:
- Создание крупных автоматизированных производств;
- Высокая степень стандартизации материалов и процессов;
- Снижение роли человеческого фактора;
- Расширение сферы пайки разнородных и композиционных материалов;
- Локализация и обособление производства припоев и флюсов.
Все это в основном касается массового производства паяных конструкций. Следует отметить, что пайка все еще остается на уровне «искусного ремесла» при выполнении ремонтных работ, производстве отдельных мелкосерийных партий изделий. Многие сложные процессы пайки применяются в ограниченном масштабе изза того, что отсутствует массовый спрос на продукцию, созданную на острие научнотехнического прогресса. Это относится к изделиям авиационной техники, космической промышленности. Однако, именно мелкосерийное производство изделий с уникальными свойствами требует нестандартных подходов, разработки новых материалов и процессов.
Особенности внедрения технологий пайки в российской промышленности:
Литература в области пайки, написанная в 6070е годы ХХ века, изобилует идеями и результатами многочисленных новаторских исследований. Однако, к сожалению, в настоящее время большинство из этих процессов не используется в российской промышленности. Экономический спад 90х годов прошлого столетия ухудшил ситуацию. Состояние технологий пайки в России отличается следующими чертами:
- Огромный научно технологический багаж по созданию паяных соединений;
- Устаревшее оборудование и технологии;
- Отсутствие стандартизованных правил применения материалов и проведения процессов;
- Отсутствие современной методической литературы;
- Дефицит специалистов;
- Примитивизация промышленного производства;
- Исчезновение и деградация производств некоторых сплавов.
- Исходя из этого при необходимости создания или расширения производств, включающих процесс пайки, возможны два варианта развития событий.
Первый вариант заключается в закупке импортной технологии с оборудованием, которая уже обкатана за рубежом, по сути не представляет собой новаторскую технологию, но способна решить задачи создания массового производства паяных конструкций. При этом следует учитывать то, что западные технологии ориентируются на стандартные материалы зарубежного производства. Цены на эти материалы значительно выше, чем на аналоги в России. Также немаловажным является факт различия законов об обращении драгоценных металлов. Большинство припоев зарубежного производства содержит в своем составе значительное количество серебра. Это усложняет организационные стороны нового производства. Следует отметить, что в отличие от зарубежных стран в России существовали многочисленные разработки сплавов припоев для замены серебросодержащих. Это иллюстрирует тот факт, что практически одно и то же соединение можно получить, варьируя входными элементами процесса. Таким образом, чтобы применять отечественные материалы на импортном оборудовании, часто необходимо внести коррекцию в технологический процесс.
Второй вариант заключается в создании собственных технологических процессов, отличающихся от стандартных зарубежных, тем более, что при отсутствии полной уверенности в будущем развитии рынка российские потребители хотят иметь производственные комплексы, позволяющие выпускать продукцию в масштабах мелкосерийного и среднесерийного производства с элементами гибкости. Собственные разработки должны отличаться нестандартным подходом относительно как оборудования, так технологии и применяемых материалов.
Если создание нового оборудования допускает использование импортных элементов, то ориентация на импортные припои и флюсы могут привести к исчезновению производства отечественных припоев. Во всем мире изготовление припоев выделено в отдельное направление как производство прецизионных сплавов. В масштабах нашей страны оно не является массовым. Поэтому важно ориентироваться на применение отечественных материалов как в первом варианте, так и во втором. Иначе ситуация сведется к простому заимствованию иностранных технологий и материалов.
Определенный позитивный опыт в этом направлении имеет ЗАО «АЛАРМ» (Москва), занимающееся разработкой и производством высокотемпературных припоев и флюсов. Производство некоторых сплавов пришлось, в буквальном смысле, восстанавливать. Для сохранения отечественного производства припоев, таким образом, надо следовать следующим принципам:
- Достижение уровня качества продукции западных аналогов;
- Разработка материалов для альтернативных технологических решений;
- Адаптация импортируемых технологий к отечественным материалам;
- Кооперация инжиниринговых фирм с университетами в сфере разработок и обучения.
Примерами успешного решения задач создания гибких среднесерийных производств может явиться использование современных российских установок для индукционного нагрева. Применение процессорного управления и программирования нагрева, охлаждения позволяют создавать производства, заменяющие использование громоздких проходных печей с восстановительной атмосферой. Например, для пайки кронштейнов для котлов, имеющих 7 паяных швов и паяемых за рубежом в проходных печах, с участием «Союза профессиональных паяльщиков им. С.Н. Лоцманова» был разработан процесс индукционной пайки на автоматизированном оборудовании (рис. 2). Для успешного технологического решения был также разработан новый боратный флюс, который легко смывается водой и оставляет минимум остатков после пайки. Таким образом, с помощью кооперации российских компаний в области разработки оборудования индукционного нагрева, материалов для пайки и технологии процесса удалось решить проблему создания серийного производства изделий, которые по стандартному варианту паялись бы затратным методом в проходных печах при ежемесячной потребности 34 тысячи изделий.
Рис. 2 Автоматизированная пайка стального кронштейна. Одновременная пайка трех деталей латунным припоем с легко смываемым флюсом
Аналогичным примером может служить создание линий для пайки изделий дорожной техники, когда на импортной элементной базе с применением отечественных припоев и флюсов удалось создать достаточно элегантные установки конвейерного типа для пайки дорожного инструмента.
Рис. 3 Индукционная пайка изливов бытовых смесителей с помощью порошка припоя П14 (медь-фосфор-олово)
Иллюстрацией нестандартного подхода может служить технология пайки изливов бытовых смесителей из латуни. Паяное соединение образуется сложной линией сопряжения треугольной трубы с цилиндром. Причем сопряжение поверхностей происходит под некоторым углом. Применение гранул припоя посредством засыпки через трубу позволило уйти от стандартного применения пасты серебросодержащего припоя (рис. 3).
Заключение
Таким образом, для сохранения собственного производства паяных конструкций, исключения простого заимствования импортных технологий и материалов необходимо движение в следующем направлении:
- Сохранение самостоятельности производства отечественных припоев – основа импортозамещения материалов и технологий;
- Комплексное решение проблемы за счет объединения усилий инжиниринговых, производственных фирм и университетской базы;
- На основе знаний и опыта осуществлять взаимную адаптацию материалов и технологий пайки;
- Совершенствование технологии получения припоев для приближения качества материалов к современным мировым аналогам.
Перечисленные направления будут способствовать развитию технологических линий для серийного и массового производства изделий, содержащих паяные соединения, с учетом специфики отечественной промышленности на базе технологического потенциала, накопленного за все предшествующие годы.
И.Н. Пашков, А.И. Пашков
НП «Союз профессиональных
паяльщиков им. С.Н. Лоцманова МоскваInternet: www.atsost.ru
mirprom.ru
Паяемость выводов электронных компонентов
Технологии в электронной промышленности №4’2010
Заказать этот номерПроблема улучшения качества паяных соединений и повышения надежности изделий электроники вызывает необходимость применения эффективных методов контроля паяемости выводов электронных компонентов и финишных покрытий печатных плат. Методы должны обеспечивать автоматизацию контроля, высокую достоверность и возможность применения в промышленности для широкого круга электронных компонентов.
Выбор метода оценки паяемости
Проблемы формирования качественных паяных соединений в технологии электронных модулей имеют особую актуальность по целому ряду причин. Операции сборки и монтажа являются до сих пор самыми трудоемкими и занимают до 50-70% общей трудоемкости изготовления изделий. Микроминиатюризация электронных компонентов, применение поверхностного и комбинированного монтажа, создание функционально сложных микроэлектронных устройств, в частности, сверхбольших интегральных микросхем и быстродействующих микропроцессоров — все это вызывает особые трудности при формировании соединений.
Высокую функциональную сложность и степень интеграции невозможно реализовать без принципиального совершенствования системы контактных соединений. Освоение электронных сборок V поколения — многокристальных модулей (тонкопленочных многослойных гибридных конструкций, выполненных на керамических, кремниевых или металлических подложках, к которым бескорпусные кристаллы присоединяются методами пайки) — повысило количество выводов в 100 раз по сравнению с технологией монтажа в отверстия [1]. Традиционные процессы монтажа не обеспечивают высокого процента выхода годных изделий с плотным монтажом. Статистические данные показывают, что 50-80% всех отказов в ИЭ происходит вследствие дефектов соединений, причем стоимость обнаружения и исправления отказа на этапе сборки блока обходится в 100 раз дешевле, чем при испытаниях аппаратуры [2]. Качество паяных соединений во многом зависит от свойств покрытий деталей и выводов электронных компонентов.
Переход на бессвинцовые припои при монтаже электронных модулей ставит ряд задач по обеспечению хорошей смачиваемости поверхностей, оптимизации температурных профилей нагрева, контролю качества соединений. Обеспечение этих требований невозможно без разработки высокоэффективных и производительных методов контроля, особое место среди которых занимают методы контроля паяемости.
Паяемость — это способность материала смачиваться расплавленным припоем и образовывать с ним качественное паяное соединение. Паяемость определяется физико-химической природой материалов и припоя, способом и режимами пайки, флюсующими средами, условиями подготовки паяемых поверхностей и т. д. Для образования паяного соединения необходимо и достаточно смачивания поверхности металла расплавом припоя, что определяет возможность дальнейшего образования между ними химических связей. Паяное соединение должно иметь низкое переходное электрическое сопротивление, герметичность и требуемую прочность при различных условиях работы.
Паяемость выводов компонентов трудно оценить визуально, к тому же опыт показывает, что покрытия теряют паяемость при хранении. Постепенная диффузия меди в оловянное покрытие или припой приводит к образованию интерметаллических соединений, которые, увеличиваясь на паяемых поверхностях, вызывают отсутствие смачивания. Поэтому необходимо проверять паяемость таких поверхностей после хранения с целью обеспечения высокой надежности и выхода годных изделий на операциях пайки.
Для оценки паяемости предложены различные методы испытаний, которые можно подразделить на следующие виды: растекание припоя, погружение в припой, время смачивания, высота мениска и сила смачивания. Критическая оценка различных методов испытаний позволяет правильно выбрать материалы при пайке для получения высокой надежности соединений и обеспечить минимальный брак на операциях пайки (табл. 1).
Таблица 1. Методы испытаний на паяемость для электронных компонентов
Оцениваемый параметр | Площадь растекания припоя | Высота капли припоя | Время смачивания | Высота мениска | Сила смачивания |
Информативность | ■ | ■ | ■ | ■ | ■ |
Достоверность | □ | ■ | □ | □ | ■ |
Оперативность | □ | □ | □ | □ | ■ |
Точность | □ | □ | □ | □ | ■ |
Применимость для различных типов компонентов | □ | □ | ■ | ■ | ■ |
Примечание. ■ — полное соответствие результатов; □ — неполное соответствие результатов
В методе на растекание припоя на тестовые образцы наносят определенный объем припоя и флюса, затем образцы нагревают до заданной температуры. Величина площади растекания припоя зависит от типа флюса, основного металла и состава припоя. После растекания припоя образец охлаждается. Площадь может быть измерена либо планиметром, либо увеличена на экране микроскопа для облегчения измерений и повышения их достоверности. Коэффициент растекания припоя по поверхности образца определяют как [3]:
Kp = Sp/Sc, (1)
где Sp, Sc — площади растекшегося припоя и дозированной заготовки припоя.
Если известна площадь растекания и объем припоя, то значение теоретического контактного угла капли припоя на поверхности определяют, используя выражение:
θ = 7,12 V/√Sp3, (2)
где θ — угол в градусах; V — объем припоя.
Выражение предполагает, что объем припоя небольшой, гравитационное воздействие отсутствует и позволяет дать количественную оценку паяемости. Отличной паяемости соответствуют значения θ < 10°, Kp > 1, хорошей — 10° < θ < 25°, удовлетворительной — θ < 90°.
Величина контактного угла и площадь растекания зависят от массы заготовки припоя (рис. 1) [4]. Растекание припоя по поверхности образца часто носит неправильный характер вследствие неоднородности химических и физических свойств испытываемых поверхностей, а также различной степени их очистки. При испытаниях гальванических оловянных покрытий с толстыми оксидными пленками показано, что припой растекался под ними, что затрудняло контроль площади. Поэтому метод оценки площади растекания может дать значительную погрешность.
Рис. 1. Зависимость контактного угла от диаметра площади растекания и массы припоя
Разновидностью метода растекания является определение коэффициента растекания по максимальной высоте расплавленного припоя на поверхности:
Kp = (D -Hp)/D, (3)
где D — диаметр сферы, имеющий объем, эквивалентный используемому припою; Нр — высота капли припоя после растекания (рис. 2).
Рис. 2. Схема определения коэффициента растекания припоя: 1 — основной металл; 2 — припой; 3 — дозированная заготовка
Однако этот метод больше подходит там, где площадь растекания припоя приблизительно круглая. Учитывая, что в реальных условиях пайки высота «лежащей» капли расплавленного припоя Нпр всегда меньше диаметра гипотетической сферы припоя D и высоты дозы припоя Нр, то для более точного расчета коэффициента растекания припоя предложено выражение [5]:
Kp = (Нпр-Нр)/Нпр, (4)
где Нпр — высота «лежащей» капли расплавленного припоя, определяемая как:
Здесь σ — поверхностное натяжение припоя, g — ускорение силы тяжести, ρ — плотность припоя.
Методы погружения являются наиболее ранними испытаниями на паяемость, поскольку выводы компонента просто погружаются сначала во флюс, а затем в расплавленный припой, и по степени покрытия их припоем оценивается паяемость. Выводы компонента с помощью установки (рис. 3) выдерживают в ванне 1-2 с, затем удаляют из ванны, охлаждают и очищают изопропиловым спиртом.
Рис. 3. Схема установки для погружения выводов компонентов в припой: 1 — ванна с припоем; 2 — компонент; 3 — возвратная пружина; 4 — двигатель; 5 — кулачок для задержки образца в припое; 6 — микровыключатель
Значительное растекание припоя по длине вывода (на 95%) свидетельствует о хорошей паяемости (рис. 4), а образование шарика припоя с большими контактными углами — о плохой паяемости. Оставшиеся 5% несмочен-ной поверхности могут приходиться на поры и пустоты, при условии, если они концентрируются не в одном месте. Оценка результатов испытаний иногда затруднительна, поскольку недостаточно четко различаются грубые и ровные покрытия.
Рис. 4. Внешний вид выводов транзисторов после погружения в припой
Испытания на время смачивания позволяют воспроизводить довольно точно условия операции массовой пайки и могут быть использованы для определения качества пайки выводов элементов. Для проверки на паяемость материалов выводов электронных компонентов предложен метод шарика припоя (glob test). Определенный объем припоя (зависящий от размера испытываемого провода) расплавляется на нагретом блоке, а офлюсованный вывод горизонтально опускается в шарик припоя, расщепляя его надвое (рис. 5а). Время, в течение которого припой обтечет провод и в конечном итоге закроет верх провода, является временем смачивания. Для обнаружения тенденции к несмачиванию необходимо удалить провод из шарика припоя, стереть излишек припоя и повторить испытания. Для имитации длительного хранения выполняют искусственное старение в течение 16 часов при 155 °С на воздухе.
Рис. 5. Схема (а) и прибор (б) контроля времени смачивания выводов компонентов
На нагретый столик 1 укладывают дозу припоя, которая, расплавляясь, образует каплю 2. К капле подводят вывод 3, который делит ее на две части. По мере нагрева вывода припой начинает его смачивать и обтекать. В момент полного смыкания над выводом припой касается зонда 4, и отсчет времени прекращается (рис. 5а). Такие приборы выпускаются фирмой Multicore (Великобритания) и Wazau (Германия) (рис. 5б).
Для определения паяемости выводов компонентов применяют более простой — мениско-метрический метод, заключающийся в измерении высоты мениска припоя, поднявшегося по выводу над зеркалом ванны под действием сил поверхностного натяжения. Высоту мениска над зеркалом припоя измеряют с помощью специальной оптической головки или бинокулярного микроскопа. Высота мениска обратно пропорциональна контактному углу смачивания. Чем больше высота мениска, тем лучше смачивание. Это следует из формулы [6]:
где Рф — плотность флюса; H — высота мениска припоя на выводе, Fжф — сила, действующая на границе «жидкий припой — флюс»; θ — угол смачивания.
Для измерения высоты мениска применяют установку, состоящую из миниатюрной ванны с припоем, сменных держателей для закрепления компонентов, микроскопа для замера высоты мениска, щупа для настройки микроскопа на уровень припоя и пульта управления. Ванну с припоем ПОС 61 разогревают до температуры 240.250 °C, время выдержки вывода в припое — 2-3 с в зависимости от диаметра вывода. Микроскоп устанавливают так, чтобы нулевая линия шкалы микроскопа располагалась между концом щупа и его изображением в зеркале припоя. После этого щуп удаляют и закрепляют в держателе компонент, выводы которого перед испытанием рихтуют, обезжиривают растворителем и сушат.
По достижении рабочей температуры в ванне включают электродвигатель перемещения держателя и, наблюдая в микроскоп за мениском припоя на выводе, определяют по шкале микроскопа его высоту, по которой судят о паяемости (табл. 2).
Таблица 2. Оценка паяемости по высоте мениска припоя
Высота мениска припоя, мм | Оценка паяемости |
0,95-0,65 | Хорошая |
0,55-0,40 | Удовлетворительная |
Менее 0,40 | Неудовлетворительная |
Менискометры фирмы Metronelec (Швейцария) имеют диапазон измерения высоты подъема мениска 0-1,5 мм с погрешностью ±0,05 мм. Производительность контроля — до 30 шт./ч. Оценка паяемости выводов по высоте мениска трудоемка и имеет значительную погрешность.
Смачивание поверхности расплавленным припоем сопровождается постепенным уменьшением контактного угла по мере изменения в силе поверхностного натяжения вследствие взаимодействия припоя и основного металла. Следовательно, измеряя поверхностное натяжение припоя, можно оценить паяемость. Метод баланса смачивания (Wetting Balance Test) состоит в прямом измерении сил смачивания и работы адгезии. Исследуемый образец 1, закрепленный на датчике 2, погружается в ванну с припоем 7, которая с помощью привода 6, управляемого системой 5, движется вверх (рис. 6а). Датчик тензометрического типа преобразует усилие в электрический сигнал, который через тензометрический усилитель 3 подается на самописец 4.
Рис. 6. Схема (а) и прибор (б) менискографического контроля
Пока образец не нагрет, смачивание отсутствует, мениск припоя вогнут вниз, на образец действует только выталкивающая сила припоя F:
Fa = S*h*g, (7)
где S — площадь образца, h — глубина погружения.
При полном смачивании в точке В значение силы смачивания равно F1, при отрыве образца в точке С сила смачивания достигает F2 (рис. 7). Скорость погружения образцов выбирается в пределах 0,2-0,4 мм/с, время погружения 4-5 с, глубина — 0,8-2,0 мм. Мерой паяемо-сти служат сила F1 и время t1, за которое она достигает этого значения. Косинус краевого угла смачивания находят по формуле:
cosθ = (Fl+Fa)/F2· (8)
Рис. 7. Кривая менискографического контроля силы смачивания
Процесс смачивания носит релаксационный характер, и изменение силы смачивания описывается уравнением [7]:
где f0 — натяжение смачивания, равное максимальному значению силы смачивания на единицу длины периметра нижнего торца образца; τ — время релаксации смачивания; t — время, отсчитываемое от момента контакта образца с расплавом.
Время релаксации τ определяют как время достижения силы смачивания, равной [(e-1)/e]f0,. Величина натяжения смачивания:
f0 = σcosθ· (10)
Этот метод введен в европейские и международные стандарты (MIL, DIN, JIN, IPC) и применяется для оценки паяемости разнообразных покрытий, образцов печатных плат, выводных и чиповых компонентов, эффективности активированных флюсов и бессвинцовых припоев.
Менискографы выпускаются фирмами Metronelec (Швейцария) и General Electric (Англия). Менискограф MeniscoST60 Wetting Balance (рис. 6б) обеспечивает глубину погружения образцов в расплав припоя от 0,1 до 1,0 мм с шагом 0,1 мм со скоростью от 1 до 50 мм/с. Время выдержки и наблюдения составляет от 1 до 30 с. Хорошей смачиваемости соответствуют значения поверхностного натяжения припоя от 350 до 450 мН/м, а менее 200 мН/м указывает на неудовлетворительную паяемость. Тензометрический метод контроля паяемости позволяет изучать процессы длительностью не менее 1·10-3 с с чувствительностью 5·10-5 Н. Точность измерения f составляет ±(2-3)%, τ — ±5%, точность расчета краевого угла смачивания O — ±1°, σ — ±(4-5)%.
Значения натяжения смачивания оловянно-свинцовым припоем для различных типов покрытий приведены в таблице 3 [8].
Таблица 3. Параметры смачивания покрытий оловянно-свинцовым припоем
Покрытие (медный подслой) | Натяжение смачивания, мН/м |
Золото 99,99 | 270 |
Золото — олово (80) | 140 |
Золото — серебро (68) | 200 |
Золото — медь (70) | 400 |
Палладий | 450 |
Родий | 100 |
Олово химическое | 480 |
Олово электрохимическое матовое | 480 |
Олово электрохимическое блестящее | 270 |
Никель химический | 260 |
Никель гальванический | 280 |
Никель гальванический блестящий | 240 |
Никель — фосфор (90) | 200 |
Никель — бор | 150 |
Олово — никель (70) | 60 |
Олово — свинец (60) | 480 |
Параметры смачивания безвыводных электронных компонентов поверхностного монтажа, а именно их контактных площадок, оцененные менискографическим методом, зависят от типа барьерного слоя и качества слоя лужения. Время смачивания находится в пределах 0,5-2,0 с, а натяжение смачивания — в пределах 400-440 мН/м [9].
Методика испытаний выводов на паяемость с помощью менискографа также имеет некоторые недостатки. Время смачивания связано со скоростью погружения образца в припой и зависит от ряда факторов: массы образца, теплопроводности материала, активности флюса, состояния поверхности торца образца и других. В результате данные по силе смачивания и времени смачивания могут не коррелировать или даже противоречить друг другу.
Предложена методика и прибор оценки паяе-мости по обобщенному параметру, в качестве которого взята площадь петли гистерезиса смачивания (рис. 8), имеющая размерность работы. Эта работа, отнесенная к единице облуженной поверхности образца, получила название «работа облуживания» Wo6rl. Для получения петли гистерезиса после достижения заданной глубины погружения движение образца реверсируют и при этом регистрируют когезионную силу [10]. Параметры смачивания различных поверхностей в присутствии флюса ФКСп приведены в таблице 4. Снижение натяжения смачивания и увеличение работы облуживания свидетельствует об ухудшении паяемости поверхности.
Рис. 8. Диаграмма изменения силы смачивания во время испытаний
Таблица 4. Параметры смачивания оловянно-свинцовым припоем ПОС 61
Параметр | Латунь Л63 | Медь | Золото | Серебро |
Натяжение смачивания, мН/м | 238 | 221 | 260 | 165 |
Время смачивания, с | 1,0 | 1,6 | 1,0 | 2,5 |
Работа облуживания, Дж/м2 | 0,12 | 0,27 | 0,135 | 0,25 |
Лучше всего смачиваются припоем оловянные химические и матовые покрытия. Гальванические блестящие покрытия отличаются высокой чистотой поверхности, что значительно увеличивает время релаксации смачивания. Наличие до 3% фосфора в никелевом химическом покрытии, а также его пористость обуславливают некоторое замедление смачивания и увеличение краевого угла до 58° [11].
Хорошей паяемостью обладают золотое и серебряное покрытия, а также покрытия Pd, Sn-Pb и Au-Cu. По никелевым сплавам спир-токанифольные флюсы имеют низкую активность, а также образуют трудно удаляемые остатки на паяемых поверхностях. Для увеличения активности по медным и никелевым поверхностям необходимо использовать активированные флюсы на основе этиленгликоля, содержащие поверхностно-активные вещества и активаторы в виде щавелевой кислоты и гидрохлоридов, производных бензиламина. Такие флюсы обладают в 1,6-2 раза большей активностью, чем флюс ФКСп, а его остатки легко удаляются с поверхности деталей промывкой в теплой проточной воде.
Существенным отличием свинцовых и бессвинцовых сплавов является их время смачиваемости (табл. 5) [12]. Время смачиваемости сплава Sn-Pb-Ag при температуре 245 °C составляет 8 мс. При увеличении температуры на 15 °C время смачиваемости уменьшится всего до 7 мс. Время смачиваемости SAC при температуре 245 °C составляет 460 мс, а при температуре 260 °C оно резко уменьшается до 10 мс. Более длительное время смачиваемости требует более длительного и интенсивного нагрева, что увеличивает энергозатраты. Необходимо использовать более мощные печи с двумя зонами пикового нагрева.
Таблица 5. Параметры смачиваемости оловянных сплавов
Тип сплава | Со свинцом | Без свинца | Без свинца | |||
Sn-Pb-Ag | Sn-Ag-Cu | Sn-Ag | ||||
Температура плавления, °С | 179 | 217 | 221 | |||
Температура в печи, °С | 245 | 260 | 245 | 260 | 245 | 260 |
Натяжение смачивания, мН/м | 311 | 304 | 315 | 319 | 307 | 345 |
Время смачивания, мс | 8 | 7 | 460* | 10 | 720* | 124* |
Примечание. * Большие энергозатраты на нагрев из-за длительной смачиваемости.
Исследования параметров смачивания наиболее распространенными бессвинцовыми припоями — Sn-3,4Ag-4,8Bi, Sn-4,0Ag-0,5Cu, Sn-3,5-Ag и Sn-0,7Cu — поверхностей печатных плат показало, что на свежеприготовленных образцах сила смачивания составляет 4,7-5,2 мН, а время смачивания — 2-3 с. После двух циклов нагрева в связи с ростом оксидной пленки SnO2 сила смачивания снижается до 2 мН, а время смачивания растет до 8-10 с [12]. Сравнение параметров смачивания оловянными припоями различных финишных покрытий печатных плат (лужение, NiAu, серебрение и органическое паяемое покрытие (OSP)) приведено в таблице 6.
Таблица 6. Сравнение параметров смачивания оловянными припоями покрытий печатных плат
Припой | Максимальная сила смачивания | Время смачивания |
Sn37Pb | Sn > Ag = OSP > NiAu* | Sn = Ag = OSP = NiAu |
Sn3,4Ag4,8Bi | Sn > Ag>NiAu > OSP | Sn = Ag = NiAu > OSP |
Sn3,8Ag0,7Cu | Ag > NiAu > Sn > OSP | Sn > NiAu > Ag > OSP |
Sn3,5Ag | Ag > NiAu > Sn > OSP | Ag = NiAu = Sn > OSP |
Sn0,7Cu | Sn > NiAu > Ag > OSP | NiAu > Sn = Ag > OSP |
Примечание. * Лучше > хуже.
В бессвинцовом процессе флюс должен обеспечить смачиваемость наиболее трудно смачиваемых припоев и металлических поверхностей контактных площадок и компонентов при более высокой температуре, поэтому его активность должна быть выше. Более активный флюс уменьшает число оксидов и улучшает смачиваемость.
Выводы
Для обеспечения высокого качества паяных соединений в электронике необходимы совершенные и оперативные методы контроля паяемости выводов и контактных площадок электронных компонентов. Современный метод баланса сил смачивания припоями позволяет объективно и достаточно точно оценить паяемость выводов различных типов электронных компонентов, финишных покрытий контактных площадок для различных припоев и флюсов при заданной температуре формирования соединений. Этот метод может успешно применяться в промышленности, что позволяет значительно сократить брак после пайки.
Литература
- Ли Н.-Ч. Технология пайки оплавлением, поиск и устранение дефектов: поверхностный монтаж, BGA, CSP и flip-chip технологии. М.: ИД «Технологии», 2006.
- Manko H. H. Solders and Soldering: materials, design, production and analysis for reliable bonding. N. Y., 2000.
- ГОСТ 23904-79. Пайка. Метод определения смачивания материалов припоем.
- Wassink K. R. J. Soldering in Electronics. Ayr, Scotland, Electrochem. Publ., 2002.
- Ланин В. Л., Хмыль А. А. Контроль паяемости выводов элементов радиоэлектронной аппаратуры // Неразрушающий контроль и системы управления качеством сварных и паяных соединений. Материалы семинара. М.: ЦРДЗ, 1992.
- Городецкая М. С., Казаков Н. И. Метод оценки паяемости выводов электрорадиоэлементов и микросхем // Обмен опытом в радиопромышленности. 1982. Вып. 11.
- Бородина Е. К., Крашенников М. Г. Контроль паяемости металлических покрытий // Заводская лаборатория. 1989. Т. 53. № 11.
- Груев И. Д., Матвеев Н. И., Сергеева Н. Г. Электрохимические покрытия изделий радиоэлектронной аппаратуры. М.: Радио и связь, 1988.
- Becker G. Solderability Testing of Surface-Mount Devices // Electronic Packaging and Production. 1987. V. 27. No 10.
- Подлесных В. Г., Ткачев М. А., Радковский С. Г. Контроль паяемости по обобщающему параметру // Электронная техника. Сер. 7. 1981. Вып. 3.
- Емельянов В. А., Ланин В. Л., Кушнер Л. К., Хмыль А. А. Оценка паяе-мости гальванических покрытий токопроводящих элементов электронной аппаратуры // Электронная техника. Сер. 7. 1990. Вып. 3.
- Левданский А. Изменение технологического процесса при переходе на бессвинцовую пайку // Технологии в электронной промышленности. 2006. № 1.
- Sattiraju S. V., Dang B., Johnson R. W., Li Y., Smith J. S., Bozack M. J. Wetting Characteristics of Pb-Free Solder Alloys and PWB Finishes // IEEE Trans. on Electronics Packaging Manufacturing. 2002. Vol. 25. No 3.
www.tech-e.ru
При самостоятельном их изготовлении нужно стараться, чтобы пальник прочно держался и не падал, если случайно задеть его провод. В любом случае подставку следует дополнительно снабдить металлической щеткой для очистки жала.
Припой
Флюсы Жидкая канифоль особенно удобна при пайке в труднодоступных местах, на которые она может быть нанесена кисточкой. Приготовить жидкую канифоль можно самому. Для этого одну часть размельченной канифоли надо растворить в двух-трех частях денатурированного, борного, винного или медицинского спирта. Хранят жидкую канифоль в стеклянных баночках, закрываемых крышкой или пробкой. Предыдущая страница – Следующая страница Оставить комментарийнаверх |
nauchebe.net
Литература
Ивченко В.Г. Конструирование и технология ЭВМ. Конспект лекций. — /Таганрог: ТГРУ, Кафедра конструирования электронных средств. – 2001. — http://www2.fep.tsure.ru/russian/kes/books/kitevm/lekpart1.doc
Конструкторско-технологическое проектирование электронной аппаратуры: Учебник для вузов. – М.: Изд. МГТУ им. Н.Э. Баумана, 2002. – 528 с. URL: http://slil.ru/22574041/529407141/Konstruktorsko-tehnologicheskoe_proektirovanie_elektronnoj_apparatury.rar
Технология приборостроения: Учебник / Под общей редакцией проф. И.П.Бушминского. – М.: МГТУ им. Н.Э.Баумана. URL: http://www.engineer.bmstu.ru/res/RL6/book1/book/metod/tpres.htm
Тупик В.А. Технология и организация производства радиоэлектронной аппаратуры. – СПб: Издательство: СПбГЭТУ «ЛЭТИ» – 2004. URL: http://dl10cg.rapidshare.de/files/31510061/4078542704/tehnologiya.i.organizaciya.proizvodstva.radioelektronnoj.apparatury.pdf.rar
Тема: пайка и контроль печатных плат
Содержание:
Пайка на печатных платах. Общие сведения. Пайка волной припоя. Пайка в парогазовой среде. Пайка инфракрасным нагревом. Конвекционная пайка. Другие методы пайки. Припойная паста. Технология нанесения припойной пасты. Технологии изготовления трафаретов. Процесс трафаретной печати. Очистка плат после пайки.
Контроль в сборочном производстве печатных плат. Автоматическая оптическая инспекция. Рентгеновские контрольные технологические установки. Электрический контроль. Тестирование многослойных ПП. Платы для ВЧ-схем. Методы тестирования сборок. Внутрисхемное тестирование. Функциональное тестирование. Ремонт печатных плат.
Производство печатных плат на заключительной стадии сборочно-монтажных операций включает в себя следующие основные этапы: оплавление припоя с помощью печей или в машинах; отмывка плат; выходной контроль; ремонт дефектных плат, если он возможен; влагозащита плат; упаковка.
Пайка на печатных платах [4]
Общие сведения.
Пайка представляет собой распространенный способ монтажа компонентов в производстве радиоэлектронных узлов. При этом обеспечивается и механическое крепление выводов компонентов, и электрическое контактирование в соответствии с электрической принципиальной схемой. При пайке две металлические детали (или детали с металлическим покрытием) соединяются при помощи припоя — третьего металла или сплава. Соединяемые детали не расплавляются сами, расплавляется только припой. Поэтому пайка имеет более щадящий тепловой режим для деталей, чем сварка. Для получения качественного паяного соединения, обладающего хорошими электропроводящими и прочностными свойствами, необходимо обеспечить несколько условий:
Получить чистые металлические поверхности у соединяемых деталей (удалить загрязнения и пленки окислов) с помощью технологического флюса;
Нагреть припой выше точки плавления;
Обеспечить вытеснение флюса с помощью наступающего припоя;
Обеспечить растекание жидкого припоя по металлической поверхности;
Обеспечить диффузию атомов из твердой металлической фазы в жидкий припой и наоборот – образование сплавных зон.
Среди припоев в радиоэлектронике наиболее широкое распространение получили припои на основе композиции олова и свинца (ПОС). Сплав имеет особую точку, называемую точкой эвтектики. В этой точке температура кристаллизации припоя составляет 183 °С, что значительно ниже точек плавления Sn и Pb (232 °С и 327 °С).
Флюс является материалом, под воздействием которого происходит быстрое и совершенное смачивание металлической поверхности соединяемых деталей расплавленным припоем благодаря влиянию сил поверхностного натяжения. Кроме того, флюс обладает свойством растворения и удаления окисных слоев на контактируемых металлах и защиты очищенной поверхности от нового окисления. Остатки флюса должны легко удаляться, быть не изменять электрические параметры исходного материала и не вызывать коррозии. Распространены флюсы на основе органических кислот из смол хвойных пород деревьев (канифоль). Известно и большое количество синтетических материалов.
Рис. 16.1.1
Смачивание, как решающий фактор процесса пайки, может улучшаться посредством поверхностно-активных веществ флюсов. Качество смачивания можно определить по краевому углу смачивания (рис. 16.1.1). Уменьшение поверхностного натяжения припоя в расплавленном состоянии приводит к уменьшению угла смачивания. Именно в процессе смачивания создаются условия (наряду с высокой температурой) для создания диффузионных сплавных зон на границах раздела припоя и соединяемых металлов, которые определяют прочностные характеристики паяного соединения. Зачастую прочность диффузионных сплавных зон превышает прочность соединяемых металлов.В последнее время набирает силу движение за исключение свинца как токсичного металла из электронных сборок. В поисках сплавов на замену традиционной композиции SnPb исследовано большое количество материалов, однако абсолютно равноценной замены пока не найдено. ПОС обладает практически оптимальными свойствами для РЭА: хорошей смачиваемостью, прочностью, пластичностью, удобной точкой плавления, коррозионной стойкостью, усталостной прочностью, и, наконец, стоимостью.
Появление на ПП поверхностно монтируемых компонентов существенно изменило технологию пайки. Пайка волной припоя была внедрена в середине прошлого века и до настоящего времени является единственным групповым методом пайки компонентов, устанавливаемых в отверстия ПП. Она выполняется чаще всего погружением обратной стороны платы с выступающими выводами в ванну с припоем. Для пайки плат со смешанным монтажом (компоненты, монтируемые в отверстия с одной стороны платы и простые, монтируемые на поверхность с другой) был разработан метод пайки двойной волной припоя.
Для пайки поверхностно монтируемых компонентов была разработана технология оплавления дозированного припоя. Методами трафаретной печати припой в виде пасты наносится на контактные площадки ПП, затем на него устанавливаются компоненты. В ряде случаев припойную пасту просушивают после нанесения с целью удаления из ее состава летучих ингредиентов или предотвращения смещения компонентов непосредственно перед пайкой. Оплавление припоя и получение паяных соединений происходит в нагревательном устройстве.
В 1973 г. появилась пайка в парогазовой фазе (ПГФ), когда фирма DuPont разработала и запатентовала специальные жидкие материалы, имеющие температуру кипения 215 °С. С 1983 г. основным конкурентом пайки в ПГФ стала пайка расплавлением дозированного припоя с помощью инфракрасного нагрева (ИК-пайка). Примерно с этого же времени развивается пайка в конвекционных печах. В Японии пайка компонентов, устанавливаемых на поверхность недорогих плат с низкой плотностью монтажа, производится с применением нагретого инструмента. Для чувствительных к тепловому воздействию и сложных микросборок с поверхностным монтажом ведущими японскими компаниями была разработана лазерная пайка. Ведущие поставщики сборочно-монтажного оборудования обычно включают установки для пайки в состав выпускаемых производственных линий.
Пайка волной припоя применяется только для пайки компонентов в отверстиях плат (традиционная технология), хотя некоторые изготовители утверждают, что с ее помощью можно производить пайку поверхностно монтируемых компонентов с несложной конструкцией корпусов, устанавливаемых на одной из сторон ПП.
Процесс пайки прост. Платы, установленные на транспортере, подвергаются предварительному нагреву, исключающему тепловой удар на этапе пайки. Затем плата проходит над волной припоя. Сама волна, ее форма и динамические характеристики являются наиболее важными параметрами оборудования для пайки. С помощью сопла можно менять форму волны. В настоящее время каждый производитель использует свою собственную форму волны (в виде греческой буквы «омега», Z-образную, Т-образную и др.). Могут варьироваться направление и скорость движения потока припоя, достигающего платы, но они должны быть одинаковы по всей ширине волны. Регулируется также угол наклона транспортера для плат. Некоторые установки для пайки оборудуются дешунтирующим воздушным ножом, который обеспечивает уменьшение количества перемычек припоя. Нож располагается сразу же за участком прохождения волны припоя и включается в работу, когда припой находится еще в расплавленном состоянии на ПП. Узкий поток нагретого воздуха, движущийся с высокой скоростью, уносит с собой излишки припоя, тем самым, разрушая перемычки и способствуя удалению излишков припоя.
Когда появились ПП, с обратной стороны которых устанавливались поверхностные компоненты, их пайка производилась волной припоя. При этом возникло множество проблем, а именно: непропаи и отсутствие галтелей припоя из-за эффекта затенения другими компонентами, преграждающими доступ волны припоя к соответствующим контактным площадкам, а также наличие полостей с захваченными газообразными продуктами разложения флюса, мешающих доступу припоя. Потребовалось изменить технологический процесс пайки волной, внедрив вторую волну припоя. Первая волна делается турбулентной и узкой, исходит из сопла под большим давлением. Турбулентность и высокое давление потока припоя исключает формирование полостей с газообразными продуктами разложения флюса. Однако турбулентная волна все же образует перемычки припоя, которые разрушаются второй, более пологой волной с малой скоростью истечения. Вторая волна устраняет перемычки припоя, а также завершает формирование галтелей. Для обеспечения эффективности пайки параметры каждой волны должны быть регулируемыми, волны должны иметь отдельные насосы, сопла и блоки управления.
Пайка двойной волной припоя применяется в настоящее время для одного типа ПП: с традиционными компонентами на лицевой стороне и простыми компонентами (чипами и транзисторами) на обратной. Некоторые компоненты (даже пассивные) могут быть повреждены при погружении в припой во время пайки. Поэтому важно учитывать их термостойкость и принимать меры предосторожности: применять поверхностно монтируемые ИС, не чувствительные к тепловому воздействию; снизить скорость транспортера; проектировать ПП таким образом, чтобы исключить эффект затенения. Хорошо разнесенные, не загораживающие друг друга компоненты способствуют попаданию припоя на каждый требуемый участок платы, но при этом снижается плотность монтажа. При высокой плотности монтажа с помощью данного метода практически невозможно пропаять поверхностно монтируемые компоненты с четырехсторонней разводкой выводов.
Пайка в парогазовой среде
Пайка в парогазовой среде (ПГФ) с расплавлением дозированного припоя применима только к сборкам с поверхностным монтажом. Суть процесса: специальная жидкость нагревается до кипения, затем ее пары конденсируются на ПП, отдавая скрытую теплоту парообразования открытым участкам сборки. При этом припойная паста расплавляется и образуется паяное соединение между выводом компонента и контактной площадкой платы. Когда температура платы достигает температуры жидкости, процесс конденсации прекращается, тем самым заканчивается и нагрев пасты. Повышение температуры платы от ее начальной температуры до температуры расплавления припоя осуществляется очень быстро и не поддается регулированию. Поэтому необходим предварительный подогрев платы с компонентами для уменьшения термических напряжений в компонентах и местах их контактов с платой. Температура расплавления припоя также не регулируется и равна температуре кипения используемой при пайке жидкости. Такой жидкостью является инертный фторуглерод (например, FC-70).
Рис. 16.1.2.
В первых установках для пайки в ПГФ применялись две рабочих жидкости. С целью предотвращения утечки паров дорогого фторуглерода и припоя поверх основной технологической среды из инертного фторуглерода создавалась дополнительная технологическая среда из более дешевого фреона. Основной недостаток этих установок состоял в том, что на границе двух технологических сред происходило образование различных кислот и для защиты ПП требовались системы их нейтрализации. Затем стали выпускаться установки для пайки в ПГФ конвейерного типа, встраиваемые в технологические сборочно-монтажные линии. Такие установки имеют относительно небольшие входное и выходное отверстия, позволяющие реализовать систему с одной технологической средой (рис. 16.1.2).Пайка инфракрасным нагревом
Пайка инфракрасным нагревом (ИК-пайка) аналогична пайке в ПГФ, за исключением того, что нагрев платы с компонентами производится не парами жидкости, а ИК-излучением. Основным механизмом передачи тепла, используемым в установках пайки с ИК-нагревом, является излучение. В отличие от пайки в ПГФ, в процессе пайки с ИК-излучением скорость нагрева регулируется изменением мощности каждого излучателя и скорости движения транспортера с ПП. Поэтому термические напряжения в компонентах и платах могут быть снижены посредством постепенного нагрева сборок.
Инфракрасные печи применяются при изготовлении несложных плат. Обусловлено это тем, что инфракрасный тип нагрева имеет ряд отрицательных эффектов. Наиболее существенно влияют на работу следующие:
количество энергии излучения, поглощаемой компонентами и платами, зависит от поглощающей способности материалов, из которых они изготовлены. Поэтому нагрев осуществляется неравномерно в пределах монтируемого устройства;
высокие элементы могут закрывать более низкие, создавая «тень», где высока вероятность непропая;
некоторые элементы корпусом могут закрывать свои собственные выводы (кристаллоносители без выводов или с J-образными выводами).
В некоторых установках для пайки с ИК-нагревом вместо ламп ИК-излучения применяются панельные излучающие системы. Излучение такой системы не нагревает непосредственно компоненты на сборке, а поглощается технологической средой (воздух или газ), которая в свою очередь передает тепло на ПП за счет конвекции. Этот способ пайки устраняет ряд недостатков, присущих пайке с ИК-нагревом, таких, как неравномерный прогрев отдельных частей сборки и невозможность пайки компонентов в корпусах, непрозрачных для ИК-излучения. Панельные излучатели обеспечивают намного меньшую скорость нагрева, чем традиционные источники ИК-излучения.
Конвекционная пайка
Конвекционная пайка лишена недостатков, связанных с теплопередачей излучением. Но управлять горячим воздухом труднее и технически сложнее. Конвекционная пайка реализуется в камерных или конвейерных печах. Камерные печи используются в лабораторных условиях, в единичном или мелкосерийном производстве. Конвейерные печи встраиваются в сборочные линии и используются, как правило, в крупносерийном производстве.
В камерных печах отработка профиля пайки осуществляется путем изменения температуры внутри камеры со временем, в конвейерных – перемещением платы по конвейеру через несколько зон печи (зоны нагрева и охлаждения). Как правило, максимальная температура, при которой происходит непосредственно оплавление пасты, составляет 210÷220 °C. Плата находится в печи при максимальной температуре в течение всего нескольких секунд, после чего производится ее охлаждение.
В ряде случаев применяется пайка в инертной среде, при которой осуществляется впуск азота в рабочую область печи. Эта операция используется для сведения к минимуму окислительного процесса. Однако необходимо оценивать необходимость этой операции. В случае если процесс пайки длится небольшой промежуток времени, припой не успеет окислиться, так как в его состав входит флюс, обеспечивающий растворение окислов на поверхности частиц порошка припоя. Пайка в инертной среде потребует большого расхода азота, что повлечет за собой использование азотной станции с существенными дополнительными расходами. Использование азотной среды при конвекционной пайке оправдано только в условиях серийного производства при изготовлении сложных модулей, требующих высокого качества исполнения.
Другие методы пайки.
Метод пайки расплавлением дозированного припоя с помощью нагретого приспособления разработан в Японии применительно к изделиям бытовой электроники с невысокой плотностью монтажа. ПП с компонентами помещается на теплопроводящий транспортер, содержащий набор специальных пластин, температура которых контролируется. Пластины подбираются по габаритам компонента, прижимают выводы к контактным площадкам и передают тепло для оплавления припоя. Метод рекомендован к применению для пайки ТАВ корпусов и flat-pack, имеющих весьма тонкие выводы, подверженные изгибанию. Во время прижима осуществляется разогрев соединения до точки оплавления припоя по запланированному графику, а затем идет процесс охлаждения паяного контакта, и только затем убирается инструмент. Процесс последовательный, достаточно медленный, однако обеспечивает надежную пайку для ответственных и дорогих деталей.
Пайка расплавлением дозированного припоя с помощью лазерного излучения также является последовательным процессом. Для нагрева соединений применяются твердотельные либо газовые лазеры. Главное достоинство лазерной пайки заключается в том, что пучок лазерной энергии хорошо фокусируется. Метод особенно эффективен для пайки термочувствительных компонентов и компонентов с малым шагом выводов. Некоторые из наиболее сложных сборок на платах (например, центральные процессоры вычислительных машин) размером 254×305 мм могут иметь до 10000÷15000 паяных соединений. Главным здесь является качество и надежность паяных соединений, а не производительность установки.
На качество паяных соединений узла влияет множество факторов, в том числе и выбранный конструктором вариант размещения компонентов. Корпуса для больших и сверхбольших интегральных микросхем изготавливаются из материалов, которые должны обеспечивать хороший теплоотвод от корпуса ИМ в процессе эксплуатации. Низкое тепловое сопротивление корпуса, большая масса и теплоемкость крупных корпусов не позволяют получить одинаковую температуру в области выводов при пайке малых и больших корпусов, расположенных на плате в непосредственной близости. Такой эффект необходимо иметь в виду и технологу, и конструктору.
Припойная паста.
Для нанесения методом трафаретной печати через металлический трафарет или для нанесения дозатором разрабатываются различные варианты паяльных паст. Характеристики припойных паст в первую очередь определяются их составом.
Припойные пасты представляют собой смесь мелкодисперсного порошка материала припоя со связующей жидкой основой, в которую входит флюс. Содержание порошка припоя составляет приблизительно 88% от веса пасты. Состав паст выражают через соотношение ингредиентов материала припоя. Так, например, 63/37 означает содержание в составе материала припоя 63% олова и 37% свинца.
Характеристики частиц материала припоя в пасте оказывают существенное влияние на качество паяного соединения. Наиболее важным параметром является размер частиц припоя. Если припойная паста наносится на ПП через сеточный трафарет, рекомендуется применять припойную пасту, у которой максимальный размер частиц припоя составляет половину размера ячейки трафарета. Форма частиц материала припоя также оказывает влияние на процесс трафаретной печати. Частицы припоя сферической формы облегчают процесс трафаретной печати и позволяют получать хорошую воспроизводимость технологического процесса от одной партии изделий к другой при формировании рисунка припойной пасты. Наличие в пасте частиц другой формы может способствовать появлению загрязнений, затрудняющих процесс печати, и ускорению процессов окисления материалов припоя. Пульверизация расплавленного припоя, с помощью которой наиболее просто получить порошкообразные припои, образует частицы преимущественно сферической формы.
Флюс в составе припойных паст служит не только для активации металлических поверхностей, удаления с них окислов и предотвращения окисления припоя в процессе пайки, но и обеспечивает требуемую растекаемость и изменение вязкости со временем при нанесении припойной пасты на ПП. Если состав припойной пасты имеет недостаточную вязкость, она будет растекаться, что приведет к потере точности рисунка. Для уменьшения растекания пасты можно увеличить процентное содержание в ней порошка припоя или изменить химический состав флюса путем введения в него специальных вяжущих добавок (загустителей). Но здесь нужно соблюдать меру, ибо в противном случае может произойти закупорка сопла дозатора или ячеек трафарета.
Флюс должен удалять окислы с контактируемых металлических поверхностей при пайке. Для эффективного протекания этого процесса очень важно правильно выбрать необходимый температурно-временной режим пайки (температурный профиль). Если во время разогрева платы температура повышается слишком быстро, то растворитель, входящий в припойную пасту в составе флюса, быстро испаряется, что приводит к потере активности флюса, неравномерному расплавлению припоя, разложению или выгоранию его компонентов. Если же нагревательный цикл завершен преждевременно, то окислы в местах паяных соединений могут быть не полностью удалены.
Для избегания окисления припоя формирование слоя припойной пасты рекомендуется производить в химически инертной атмосфере. Хранение пасты рекомендуется осуществлять в прохладном месте с температурой от +5 до +10 °С. Минимальный срок хранения паяльной пасты с флюсом при такой температуре составляет 6 месяцев с даты производства. Перед применением емкость с пастой необходимо выдержать при комнатной температуре до полной стабилизации в течение 2÷8 часов. Не рекомендуется открывать холодную емкость, это может вызвать конденсацию влаги и ухудшение параметров паяльной пасты. Категорически не допускается подогрев пасты нагревательными приборами.
Как правило, паяльные пасты с флюсом полностью готовы к применению и не требуют дополнительных разбавителей. Паяльная паста, которая не была использована в течение рабочей смены, не должна смешиваться со свежей пастой. Остатки пасты рекомендуется складывать в отдельную тару и использовать в начале следующей смены. Не рекомендуется использовать пасту, которая находилась на трафарете две рабочих смены. Если устройство трафаретной печати не использовалось в течение четырех часов, рекомендуется произвести полную очистку трафарета от остатков паяльной пасты.
Распространенными материалами выводов и внешних контактов электронных компонентов являются золото, серебро, палладий-серебро, медь, луженая медь, и припойная паста должна выбираться таким образом, чтобы исключить выщелачивание этих материалов. Большинство паяльных паст с флюсом обладают хорошими клеящими свойствами, достаточными для удержания компонентов после установки до пайки в течение до 8 часов. Клеящие свойства пасты зависят от температуры и влажности, поэтому рекомендуется произвести испытания для определения максимального времени удержания пастой компонентов в условиях реального производства. Печатные платы могут быть запаяны в течение 24 часов после нанесения паяльной пасты без ухудшения качества пайки, высокая температура и влажность могут сокращать это время.
Рекомендуемые режимы процесса пайки для наиболее популярных сплавов Sn63/Pb37 и Sn62/Pb36/Ag2, входящих в состав паст, таковы:
стадия предварительного нагрева от 20 до 140 °С, скорость нагрева 1 °С/сек;
стадия предварительной сушки от 140°С до 160°С, скорость нагрева 0,5 °С/сек;
стадия пайки от 160 до 215 °С, скорость нагрева 2 °С/сек.
Более длительное время стадии пайки может улучшить качество паяного соединения, уменьшить количество и сделать более инертными остатки флюса после пайки. Более короткое время пайки может также дать хорошие результаты, однако в этом случае возможно увеличение количества остатков флюса после пайки. Рекомендуется обеспечить время выдержки выше температуры плавления (+183 °С) в пределах от 30 до 60 сек. Минимальная пиковая температура в зоне пайки должна быть не менее 210 °С в течение 5 сек. Увеличение скорости повышения температуры на стадии предварительного нагрева может привести к увеличению остатков флюса после пайки и ухудшению внешнего вида паяного соединения. Этот косметический дефект полностью устраняется при отмывке остатков флюса.
Вышеуказанные рекомендации служат для первоначальной установки режимов пайки. Конкретные режимы пайки определяются технологом исходя из конструкции печатной платы и оборудования для пайки.
Технология нанесения припойной пасты.
Процесс нанесения паяльной пасты зависит от большого числа составляющих:
от характеристик оборудования – принтеров, держателей плат и др.;
от трафаретов – формы и размеров отверстий, качества стенок отверстий, толщины трафарета;
от параметров процесса нанесения пасты – скорости, угла атаки, давления и жесткости ракеля, скорости отделения трафарета, зазора между трафаретом и платой;
от припойной пасты – размера частиц, объемного содержания металла, вязкости пасты, подвижности флюса;
от параметров рабочего помещения – температуры, влажности, пыли.
Припойная паста может наноситься с помощью механических устройств для трафаретной печати (ручной способ), с помощью автоматических принтеров, с помощью дозаторов.
Дозаторы – устройства последовательной обработки, паста наносится по программе в определенном объеме на заданные точки ПП. Автоматический дозатор представляет собой рабочий стол, на который крепится обрабатываемая плата. Над рабочим полем перемещается дозатор, который осуществляет нанесение материалов на плату, для управления используется персональный компьютер. Ключевые параметры дозаторов: скорость дозирования (до 15 тыс. точек в час) и максимальный формат обрабатываемой платы (до 450×450 мм). Как и любой последовательный процесс, такой способ нанесения пасты занимает гораздо больше времени, чем трафаретная печать. Однако для дозатора не требуется разрабатывать и изготавливать трафарет. При малых объемах производства (единичные платы) для нанесения материалов можно применять и ручное дозирование.
Если на производстве изготавливается большое число конструкций плат при малом их количестве, то целесообразно применять метод дозирования, особенно при лабораторном производств, так как стоимость изготовления трафаретов (по одному на каждую сторону каждой разновидности плат) может оказаться больше стоимости изготовления самих плат. В случае промышленного производства, напротив, нанесение материалов методом дозирования нежелательно из-за низкой скорости процесса по сравнению с трафаретной печатью. На крупносерийных производствах стоимость трафаретов не вносит заметного вклада в общие расходы.
Устройства трафаретной печати могут быть как ручными, так и автоматическими.
Ручной принтер представляет собой сравнительно простое устройство: на металлической раме закрепляется трафарет, после чего раму крепят к рабочему столу, на котором находится плата, давление на ракель осуществляется оператором вручную. В автоматических принтерах все операции – совмещение трафарета и печатной платы, осуществление приводного давления на ракель, дозирование припойной пасты на трафарет – выполняются автоматически. Эти устройства могут работать как автономно, так и в составе производственной линии. Основные параметры автоматических принтеров: максимальный формат платы, который может достигать значения 510х510 мм, и скорость перемещения ракеля (до 150 мм/с).
Технологии изготовления трафаретов.
Главная функция трафарета – облегчить размещение припойной пасты. Цель – нанести точное количество материала на точно определенное место на ПП.
Рекомендованные соотношения шага выводов компонентов, размеров контактных площадок (КП) и размеров отверстий трафаретов приведены в таблице.
Шаг компонентов, мм | Стандарт ширины КП, мм | Стандарт ширины отверстий трафарета, мм | Толщина трафарета, мкм |
1,27 1,0 0,825 0,635 0,5 0,425 0,3 | 0,635 0,5 0,45 0,4 0,3 0,25 0,2 | 0,635 0,5 0,425 0,3 0,25 0,2 0,15 | 200 150 125 125 125 120 100 |
Уменьшение размеров отверстий трафарета по отношению к размерам КП выполняется равномерно со всех сторон и центрируется по КП. Для уменьшения площади стенок окна трафарета и прилипания паяльной пасты к стенкам рекомендуется делать скругленные углы окон в трафарете. Оптимальное соотношение площади отпечатка паяльной пасты к площади стенок окна в трафарете должно быть Sкп/Sбс > 0,80, где Sкп – площадь отпечатка паяльной пасты на плате, Sбс – площадь боковых стенок окна в трафарете.
Рис. 16.1.3.
Наиболее распространены три технологии для производства трафарета – химическое травление, лазерное испарение и электроосаждение. Каждая из них имеет свои особенности. Химически вытравленные трафареты создаются путем травления металлической фольги, покрытой маской из фоторезиста с двух сторон. Профиль отверстий при этом имеет характерный вид (рис. 16.1.3 а). При размере шага в 0,5 мм и менее такой профиль увеличивает сопротивление прохождению пасты, для его устранения применяют электрополирование стенок отверстий трафарета (рис. 16.1.3 б), которое уменьшает поверхностное трение и позволяет хорошо продавливать пасту.Трафареты с трапецеидальными отверстиями (рис. 16.1.3 в) имеют со стороны основания трафарета большие размеры, чем со стороны вершины. Трапецеидальное отверстие может быть выполнено двумя способами: изменением размеров маски фоторезиста на разных сторонах фольги или изменением давления струи травителя при обработке разных сторон фольги. Такая форма отверстий подходит для шага компонентов 0,5 мм и выше.
Методом химического травления могут быть получены трафареты двойного уровня (ступенчатые), которые позволяют варьировать объем припоя для компонентов, имеющих различный шаг выводов. Ступенчатость должна быть на стороне ракеля, так как сторона основания трафарета должна ровно прилегать к плате. Как и в технологии формирования рисунка ПП методом травления фольги (субтрактивная технология), при химическом травлении трафаретов возникает боковое подтравливание под маску фоторезиста, вызывающее относительное удлинение размеров отверстий. Это относительное удлинение зависит от толщины трафарета, поэтому размер отверстий определяется к толщине фольги как 1,5 к 1. То есть, при 150 мкм толщине трафарета минимальное отверстие будет 225 мкм.
Метод электроформирования трафарета основан на гальваническом наращивании металлической фольги (как правило, Ni) на основании (носителе), на котором сформированы «островки» фоторезистивной маски на месте будущих отверстий. Толщина трафарета может варьироваться от 25 мкм до 0,3 мм и подходит для нанесения пасты для ультрамалых шагов выводов компонентов: от 0,2 мм до 0,4 мм. Отношение размера отверстий к толщине трафарета 1 к 1.
Трафареты, формируемые лазерным испарением, изготавливаются непосредственно по оригинальным данным клиента (Gerber формат) и не требуют фотолитографии. Прямое формирование позволяет повысить точность и воспроизводимость изготовления трафаретов. По сравнению с химическим травлением края отверстий в ряде случаев могут иметь неровности в силу взрывного испарения металла. Процесс долговременный, т.к. машина вырезает каждое отверстие индивидуально. Трафареты могут быть произведены комбинированным способом: химическим травлением для компонентов стандартного шага и лазерным испарением для компонентов малого шага. Готовый трафарет может быть электроотполирован, чтобы обеспечить гладкость стенок отверстий. Лазерная методика – единственный процесс, который позволяет корректировать трафарет во время его изготовления (например, добавлять или изменять существующие отверстия или добавлять реперные знаки).
Процесс трафаретной печати.
Для нанесения паяльной пасты могут использоваться ракели различной конструкции и материала, в том числе стальные или полиуретановые. Угол наклона ракеля: 60° — стандартный, 45° для компонентов с шагом <0,4 мм.
Для контактных площадок прямоугольной формы имеет значение направление движения ракеля: вдоль длинной или короткой стороны, поскольку из-за увлечения пасты ракелем вдоль одной из стенок трафарета остаются небольшие пустоты. Разный объем пасты на разных КП может приводить к разной высоте припойных столбиков после оплавления припойной пасты. Это может приводить к дефектам типа «открытое соединение» — отсутствию электрического контакта. Для предотвращения таких дефектов ракель движется под углом 45° к наиболее критичным посадочным местам компонентов. Давление ракеля подбирается опытным путем и зависит от толщины трафарета и скорости перемещения ракеля. После прохода ракеля трафарет должен полностью очищаться от остатков паяльной пасты. Например, значения первоначальной установки давления металлического ракеля составляют от 0,12 кг (на каждый см длины ракеля), при скорости перемещения 50 мм/сек до 0,32 кг, при скорости 150 мм/сек при температуре +23°С. Увеличение или уменьшение рабочей температуры на 1°С требует пропорционального изменения давления ракеля на 5%. Скорость печати может составлять от 30 до 150 мм/сек. Скорость разделения трафарета с печатной платой после нанесения паяльной пасты высокая – 20 мм/сек; для компонентов с малым шагом рекомендуется уменьшить скорость до 10 мм/сек.
После нанесения паяльной пасты на 15÷20 печатных плат рекомендуется произвести очистку трафарета с нижней стороны для предотвращения образования перемычек и шариков припоя в процессе пайки. Для очистки трафарета необходимо использовать только специальные материалы (бумагу и промывочные жидкости). Обычные материалы хуже впитывают влагу и оставляют пыль, нитки и ворсинки, которые могут забивать окна в трафарете и создавать «мостики» между соседними контактными площадками, образуя перемычки припоя в процессе пайки.
Очистка плат после пайки.
Обычная ПП содержит много внутренних полостей (в том числе и под компонентами), имеющих выход на поверхность через узкие вертикальные зазоры между компонентами или их выводами. Эти полости способны удерживать продукты разложения флюса и другие загрязнения, которые могут стать источниками коррозии или причиной проникновения внутрь корпусов компонентов веществ, вызывающие повышенные токи утечки. Усиленные попытки очистить плату, например, с помощью органических растворителей, сами по себе могут вызвать механические повреждения или коррозию.
Как правило, загрязнения бывают либо полярными (ионы), либо неполярными. Свободные ионы, особенно электроотрицательные, обладающие высокой химической активностью, быстро вступают в реакцию с металлом коммутационных дорожек и вызывают коррозию. Неполярные загрязнения ухудшают адгезию припоя, свойства защитного покрытия и электрический контакт для функционального испытания микросборки.
Органические растворители в соответствии с их очистной способностью можно разделить на три группы. Гидрофобные — не смешиваются с водой, используются для растворения органических загрязнений, например канифоли и жиров. Гидрофильные — смешиваются с водой, растворяют полярные и неполярные соединения, причем последние в меньшей степени, чем гидрофобные растворители. Азеотропные — представляют собой в основном смесь вышеуказанных типов растворителей. В их состав обязательно входят такие ингредиенты, как фреон-113 или тетрахлордифторэтан, с добавками спиртов и стабилизирующих ингредиентов.
Очистка изделий с применением растворителей может быть реализована погружением плат в ванну с растворителем, равномерным по полю платы или направленным в виде струй опрыскиванием, либо комбинацией обоих методов. Может применяться ультразвуковое перемешивание при очистке плат в ванне с растворителем. На эффективность очистки может повлиять ряд факторов, в том числе расположение компонентов. Компоненты должны размещаться на поверхности платы таким образом, чтобы их корпуса не загораживали друг друга при движении потока растворителя. Прерывания движения платы и остановки во время пайки волной припоя должны быть сведены к минимуму, чтобы флюс нигде не задерживался в полостях платы. Если используются чувствительные компоненты, рекомендуется обрабатывать микросборки в потоке растворителя. При этом необходимо обеспечить максимальную однородность потока растворителя, а интервал времени между пайкой и очисткой уменьшить до минимума.
studfiles.net