Аксиальне дисковые ветрогенераторы своими руками
В этом разделе размещены самодельные ветрогенераторы, сделанные на основе дисковых,аксиальных генераторов. Главная особенность и преимущество таких генераторов это полное отсутствие магнитного залипания. Статор не содержит железа, катушки просто залиты эпоксидной или полиэфирной смолой. Но в отличие от классических генераторов с железными статорами, магнитов в такой генератор требуется как минимум в два раза больше — чтобы получить такую-же мощность. Зато ветрогенераторы с такими генераторами стартуют на малой скорости ветра. >Генератор 24 вольта 500 ватт
В этой статье фото и описание изготовления аксиального генератора для работы на АКБ 24 вольта. Есть данные по оборотам и мощности, также к нему рассчитан винт диаметом 2.1м из ПВХ трубы 315мм >Изготовление ветрогенератора 1.

Ветрогенератор 2кВт для дома
Небольшая история о том как и почему строился ветрогенератор, что нужно учитывать новичкам и как все получилось. В статье нет расчетов и подробных фотографий изготовления, статья немног не об этом, зато есть рассказ автора ветрогенератора о том как сделать ветрогенератор и нужен ли он, насколько это сложно. Так-же есть фото его ветрогенератора >Аксиальный ветряк из подручных материалов
Еще один ветрогенератор, собранный из подручных материалов поднят на ветер. Раньше у меня уже были попытки делать такие ветрогенераторы.
Красивый ветрячек получился
Еще немного фотографий изготовления дискового ветрогенератора своими руками. Хоть сам ветрогенератор и не получился из-за банальных ошибок, но зато подход к делу и основательность радует, хорош внешний вид ветрогенератора. Деревянные лопасти, складывающийся хвост, крепкая мачта на растяжках, все это прокрашено. >Как сделать аксиальный ветрогенератор
В статье на конкретном примере описывается процесс создания аксиального ветрогенератора на автомобильной ступице. Для генератора было сделано несколько статоров, особенностью последнего статора является применение сердечников в катушках статора для увеличения мощности. >Аксиальный генератор на ферритовых магнитах
В генераторе использовались обычные ферритовые магниты, из-за невысокой мощности магнитов катушки генератора содержат по 325 витков проводом 0,5мм.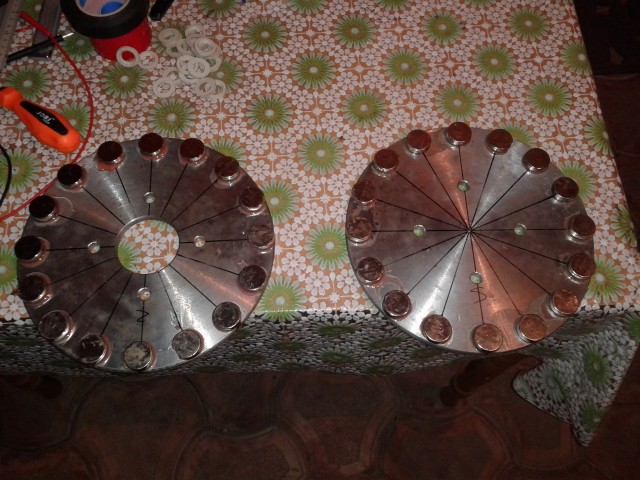
Ветрогенератор 20-ти полюсной на магнитах 20*5мм
Фото отчет с кратким описанием процесса создания самодельного ветрогенератора. В основе лежит ступица от прицепа «Зубренок» , поворотная ось так-же сделана из автомобильной ступицы. Генератор трехфазный, 20 полюсов и 15 катушек намотанных проводом 0,7мм по 70 витков. Винт двухлопастной, сделан из ПВХ трубы. >Маленький ветряк на 30ватт
Небольшой двух-лопастной ветрогенератор был построен как тестовая уменьшенная модель, чтобы выдавала на аккумулятор до 1А. В итоге генератор получился удачным, и в будущем планируется построить большой аксиальный ветрогенератор. >Мини ветрогенератор 20ватт/ч
Этот небольшой ветрогенератор делался ради опыта, чтобы возможно в дальнейшем сделать большой и мощный ветрогенератор.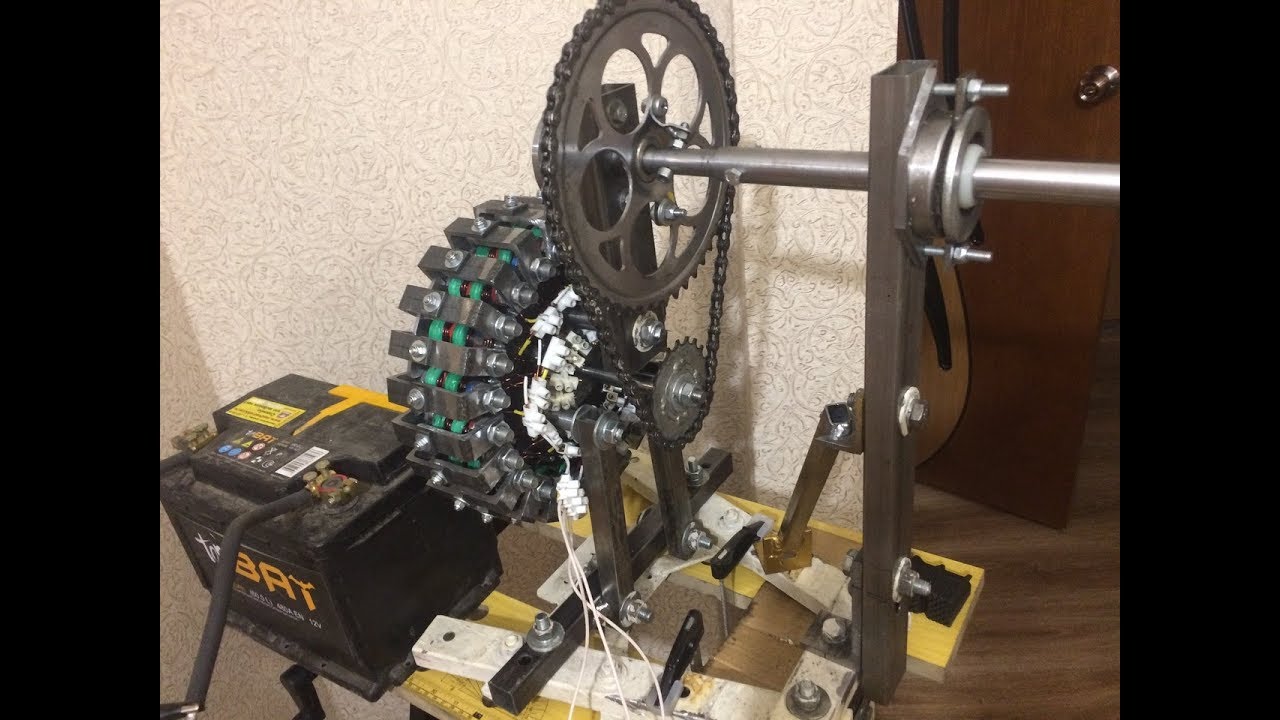
Дешевый мини ветрогенератор для зарядки АКБ
Простейшие мини ветрогенераторы аксиального типа, делать много маленьких проще чем один большой. Каждый такой ветрячек заражает свой аккумулятор напрямую, а слабый ток позволяет не следить за процессом зарядки без контроллера, так-как не вредит АКБ. >Небольшой много-полюсной генератор 50 ватт
В генераторе использовались магниты от первого ветряка, так-как магниты небольших размеров, было решено поднять мощность за счет увеличения числа полюсов генератора. Для проверки своих расчетов и проверки информации из интернета было изготовлено несколько статоров с разным числом катушек и фаз. >Аксиальный ветрогенератор на ступице от ВАЗ2108
Классическая конструкция аксиального генератора на автомобильной ступице.
Ветрогенераторы с необычным внешним видом
Аксиальные ветрогенераторы из автомобильных ступиц мы делаем уже давно. В этот раз мы решили придать индивидуальность и красоту нашим ветрякам, чтобы они не только заряжали наши аккумуляторы, но и радовали глаз внешним видом. В конструкции ветрогенераторов ничего особенного кроме внешнего вида нет, классический трехфазный аксиальный генератор. >Мощный ветрогенератор на основе самодельного аксиального генератора
Конструкция этого ветрогенератора специально проектировалась для работы в местности с преобладанием малых ветров. В основе ветрогенератора мы собрали мощный низко-оборотный генератор аксиального типа с бес-железным статором.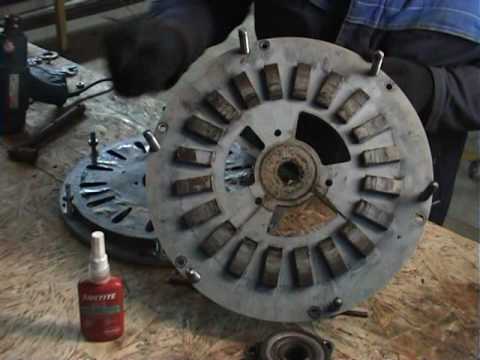
Однофазный ветрогенератор аксиальный
Самодельный ветрогенератор с дисковым генератором на неодимовых магнитах. Классическая схема аксиального генератора на постоянных магнитах.Однофазная схема, 12 катушек и по 12 магнитов на каждом диске, в итоге малыш развивает до 100ватт, а иногда и больше.
>Фото отчет о строительстве сразу 3-х ветрогенераторов
В этот раз мы вместе с соседями строим сразу три аксиальных ветрогенератора на основе автомобильных ступиц. Генераторы абсолютно идентичны, мощность каждого 500ватт/ч. Эти генераторы мы делаем уже давно, такая компоновка ветрогенератора доступна для повторения каждому, так-как не требует специальных условий и инструментов для изготовления ветряка.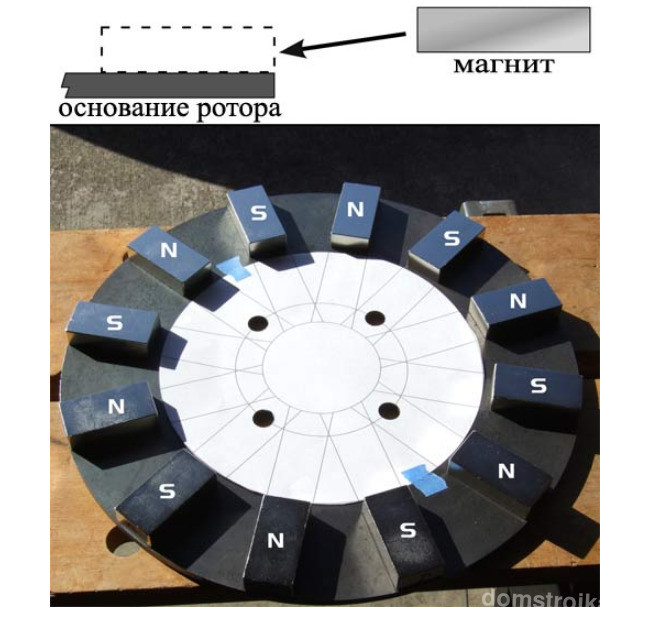
Профессионально сделанный ветряк 2кВт
Самедельная домашняя ветровая турбина мощностью 2кВт от Итальянского мастера. Точнее сказать проффесионально сделанный дисковый аксиальный ветрогенератор приличной мошности. В статье много фото процесса изготовления ветряка с небольшим описанием.Аксиальный ветрогенератор 100ватт
Конструкция таких генераторов, как этот довольно проста часто повторяема. Генераторы для ветряков такого типа первыми начали строить в США, в связи с доступностью у них редко-земельных магнитов. Со временем такая концепция самодельного бытового ветрогенератора распространилась по всему миру. > Генератор я собирал так, в основе генератора лежит ступица от ВАЗ2108, в качестве роторов используются тормозные диски тоже от ВАЗ2108.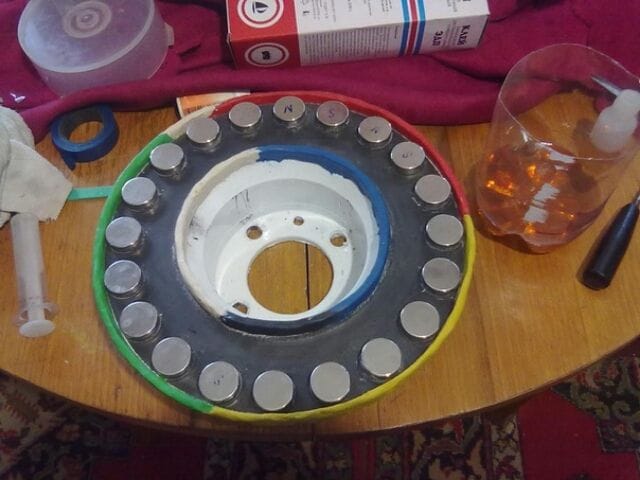
Тормозные диски я зачистил до блестящей поверхности под магниты. Магниты клеил с помощью супер клея, магниты клеятся чередуясь полюсами, а диски ротора должны притягиваться, то-есть магниты половинок должны притягиваться друг к другу. После наклейки магниты дополнительно залил эпоксидной смолой для надежности.
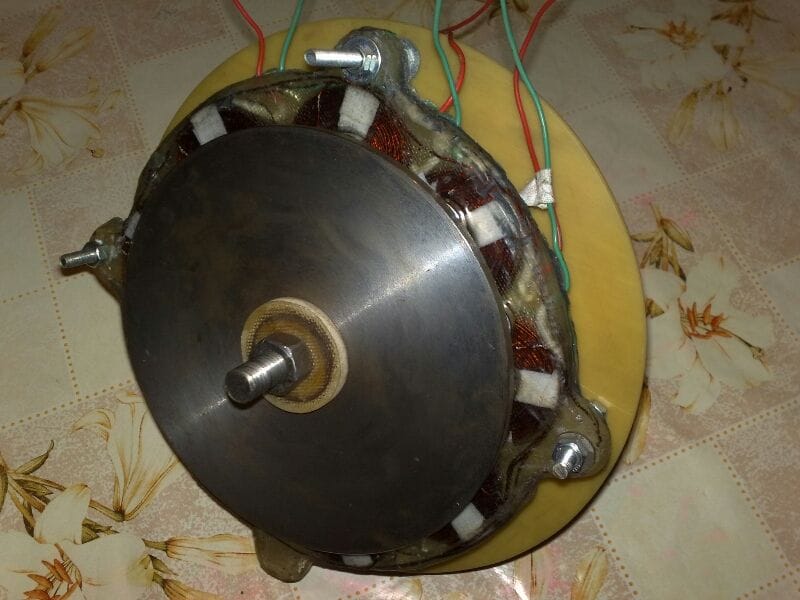
Для заливки катушек статора я вырезал форму из фанеры, зачистил края до гладкой поверхности. Форму обильно смазал обычным вазелином, можно кстати любыми жирами, или воском, парафином, это нужно чтобы после высыхания статор легко извлечь из формы. На дно формы сначала положил круг из стеклоткани, потом выложил катушки, спаял их в фазы и вывел концы каждой фазы наружу, чтобы потом можно было соединять их в звезду или треугольником. Внутреннее отверстие каждой катушки я залепил пластилином, это будет дополнительная вентиляция для катушек если они будут греться. Далее все это дело я залил эпоксидной смолой с 40% добавкой талька ( детская присыпка), тальк делает статор прочнее, но как оказалось статор намного прочнее если добавлять обыкновенную муку, но об этом я узнал уже потом. Сверху проложил ище кружок стеклоткани и накрыл крышкой из фанеры, которую прикрутил на саморезы прямо через внутренние отверстия катушек.
После высыхания и небольшой обработки получился вот такой статор для генератора. После сборки уже готовый ветрогенератор я поднял на мачту, и подключил автомобильный аккумулятор. Ниже фото этого генератора.

Как сделать аксиальный ветрогенератор
Эта статья посвящена созданию аксиального ветрогенератора на неодимовых магнитах со статорами без металла. Ветряки подобной конструкции стали особенно популярны из-за растущей доступности неодимовых магнитов.
Материалы и инструменты использованные для постройки ветряка этой модели:
1) ступица от автомобиля с тормозными дисками.
2) дрель с металлической щеткой.
3) 20 неодимовых магнитов размером 25 на 8 мм.
4) эпоксидная смола
5) мастика
6) труба ПВХ 160 мм диаметром
7) ручная лебедка
8) труба металлическая длинной 6 метров
Рассмотрим основные этапы постройки ветряка.
За основу генератора была взята ступица автомобиля с тормозным диском. Так как основная деталь заводского производства, то это послужит гарантом качества и надежности. Ступица была полностью разобрана, подшипники находящиеся в ней были проверены на целостность и смазаны. Так как ступица была снята со старого автомобиля, то ржавчину пришлось зачистить с помощью щетки, которую автор насадил на дрель.
Ниже предоставлена фотография ступицы.
Затем автор приступил к установке магнитов на диски ротора. Было использовано 20 магнитов. Причем важно заметить, что для однофазного генератора количество задействованных магнитов равно количеству полюсов, для двухфазного соотношение будет три к двум или четыре полюса к трем катушкам. Магниты следует крепить на диски с чередованием полюсов. Для соблюдения точности необходимо сделать шаблон размещения на бумаге, либо начертить линии секторов прямо на самом диске.
Так же следует разметить магниты по полюсам маркером. Определить полюса можно поднося поочередно магниты к одной стороне проверяющего магнита, если притягивается — плюс, отталкивается- минус, главное, чтобы полюса при установке на диск чередовались.
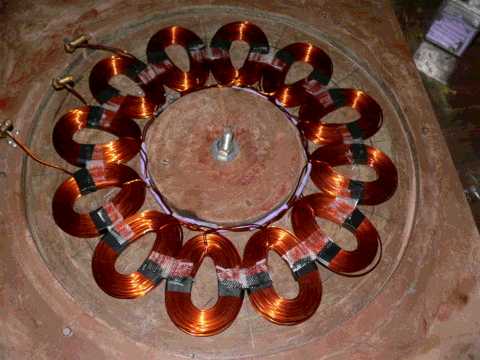
Магниты были приклеены на диски при помощи эпоксидной смолы. Чтобы смола не растекалась за границы диска автор сделал бордюры по краям при помощи мастики, то же самое можно сделать при помощи скотча, просто обмотав колесо по кругу.
Рассмотрим основные отличия конструкции однофазного и трехфазного генераторов.
Однофазный генератор будет давать вибрацию при нагрузках, что будет отражаться на мощности самого генератора. Трехфазная конструкция лишена подобного недостатка благодаря чему, мощность постоянна в любой момент времени. Это происходит потому, что фазы компенсируют потерю тока друг в друге. По скромным расчетам автора трехфазная конструкция превосходит однофазную на целых 50 процентов. К тому же из-за отсутствия вибраций мачта не будет дополнительно раскачиваться,следовательно не будет дополнительного шума при работе ротора.
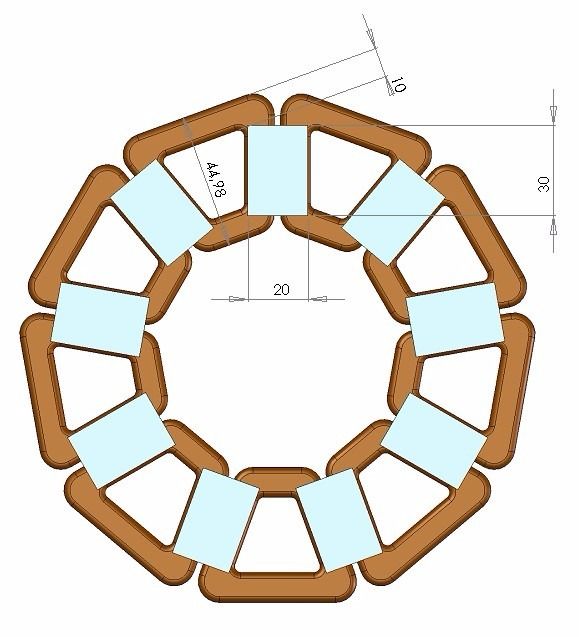
При расчете зарядки 12-ого аккумулятора, которая будет начинаться на 100-150 оборотах в минуту, автор сделал по 1000-1200 витков в катушках. При намотке катушек автор использовал максимально допустимую толщину проволоки, чтобы избежать сопротивления.
Для наматывания проволоки на катушки автор соорудил самодельный станок, фотографии которого представлены ниже.
Лучше использовать катушки эллипсоидной формы, что позволит большей плотности магнитных полей их пересекать. Внутреннее отверстие катушки стоит делать по диаметру магнита либо больше него. В случае, если делать их меньше, то лобовые части практически не участвуют в выработке электроэнергии, а служат проводниками.
Толщина самого статора должна равняться толщине магнитов, которые задействованы в установке.
Форму для статора можно сделать из фанеры, хотя автор решил этот вопрос иначе. Был нарисован шаблон на бумаге, а затем сделаны борта при помощи мастики. Так же для прочности была использована стеклоткань.
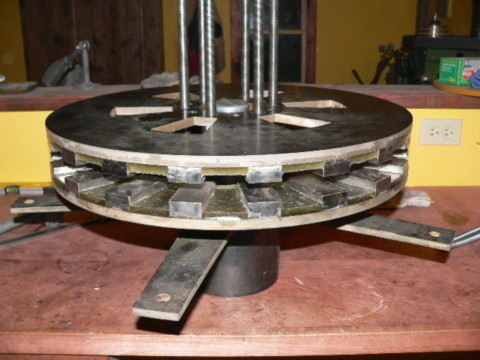
Перед заливкой катушки необходимо точно закрепить, а их концы вывести за пределы формы, чтобы затем соединить провода звездой или треугольником.
После того, как основная часть генератора была собрана, автор измерил протестировал его работу. При ручном вращении генератор вырабатывает напряжение в 40 вольт и силу тока в 10 ампер.
Затем автор изготовил мачту для генератора высотой в 6 метров. В будущем планируется увеличить высоту мачты за счет использования более толстой трубы минимум вдвое. Чтобы мачта была неподвижна основание было залито бетоном. Для опускания и поднимания мачты было сделано металлическое крепление. Это необходимо, чтобы иметь доступ к винту на земле, так как заниматься ремонтными работами на высоте не особенно удобно.
Для поднятия мачты используется ручная лебедка.
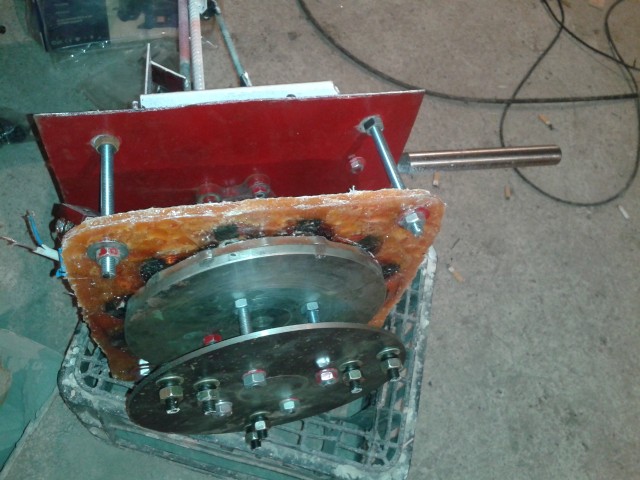
Сам винт для генератора был сделан из трубы ПВХ диаметром 160 мм.
После установки и испытаний генератора в стандартных условиях автор сделал следующие наблюдения: мощность генератора доходит до 300 ватт при ветре в 8 метров в секунду. В последующем увеличил мощность генератора за счет металлических сердечников установленных в катушки. Винт стартует уже при двух метрах в секунду.
Дальше автор приступил к совершенствованию конструкции в целях увеличения мощности генератора. Были набраны магнитопроводы из пластин, которые в последствии были установлены в конструкцию. Из-за их установки появился эффект залипания, но не очень сильный. Старт работы винта происходит при скорости ветра около двух метров в секунду.
Таким образом установка металлических сердечников увеличила мощность генератора до 500 ватт при ветре в 8 метров в секунду.
Для защиты от сильных ветров была использована классическая схема увода винта складывающимся хвостом.
В среднем генератор способен вырабатывать до 150 ватт энергии в час, которая идет на зарядку аккумуляторов.
Источник (Source) Становитесь автором сайта, публикуйте собственные статьи, описания самоделок с оплатой за текст. Подробнее здесь.
Аксиальный ветрогенератор своими руками
Вот и я изготовил свой генератор для ветряка. Начиналось всё с изучения большого количества информации и общения на форуме. Ветроэнергетикой я интересовался уже давно, но собрать свой собственный ветряк мешали некоторые обстоятельства. И вот как говорится свершилось.
За основу взял популярный торцевой генератор на постоянных магнитах, так как он состоит всего из нескольких деталей, и очень прост в изготовлении. Для генератора приобрёл дисковые ниодимые магниты размером 20 на 5 мм. Статор намотал проводом 0,7мм. Катушки соединил в кольцо, соединил выводы катушек в звезду и уложил в заранее заготовленную форму. Залил всё это дело эпоксидной смолой. В итоге получился готовый статор.
Ниже изображена схема соеденения катушек статора, за основу взял эту схему, так как пишут, что она вроде эффективнее, хотя немного сложнее чем последовательное соединение всех катушек. Для ротора заказал два диска, на которые наклеил магниты, так-же мне выточили и ступицу вместе с валом под готовые подшипники.
После собрал все дитали воедино и получился вот такой генератор. Это мой первый генератор, так что прошу сильно не кретиковать. Хотя я считаю что вышло неплохо. Теперь надо было его протестировать и узнать на что спообен этот малышь.
Далее принялся за изготовление лопастей, тоже не стал ничего усложнять и изготовил из трубы ПВХ. Размеры не выссчитывал,так как не некому было, а сам я в этих рассчётах ничего не понимаю. Поэтому делал на овось, примерно определив какие они должны быть. Но в последствии понял, что лопасти надо рассчитывать под конкретный генератор, иначе может быть большой недобор мощности и слишком малые обороты.
Но это был наверно единственный доступный вареант быстрого изготовления лопастей. Хотя в общем и с ними генератор тоже работал и давал ток зарядки на аккумулятор. Ниже на фото получившиеся лопасти. После монтажа лопастей сделал простенький хвост без всякой защиты и водрузил ветрогенератор на мачту, чтобы проверить его работоспособность. Сначало поставил на невысокую мачту (4м), но потом понял, что этого мало и сделал более высокую 8-ми метровую мачту и установил ветрогенератор. После нескольких дней работы ветряка нарисовались некоторые параметры ветряка.
Замеры делал при разной скорости ветра: ток короткого замыкания при ветре 15м/с составил 30в 9А. При ветре 10м/с 20в 2.75А, 5м.с 13в 1А.
Как оказалось такие лопасти очень слабые и они у меня разлетлись не выдержав сильного ветра. Пока генератор был снят решил снять реальные параметры генератора.Так как на ветру лопасти не выводили генератор на полную мощность. Для этого покрутил генератор подключая нагрузку 2,1Ом, сопротивление каждой фазы генератора 1,9 Ом. Обороты мерил тахометром. Вот что получилось, на 160об/м было всего 3в 1.23А, далее 280об.мин 6в 2.9А, 320об.мин 8в 3.23А, 670об.мин 12в 5.8А. Думаю померял правильно, более весокие обороты покрутить нечем, хотя для общего представления этих данных вполне достаточно.
После вырезал новые лопасти из такой-же трубы ПВХ, но переделал крепление , теперь оно более надёжное. Так-же переработал хвост, зделав его складывающимся при сильных парывах ветра. Центр оси смещён относительно головки генератора, и когда дует сильный ветер лопасти уходят из под ветра, при этом складывается хвост, это классическая схема увода от ветра.
Новые параметры пока не успел замерить, так как извесно что после установки ветряка ветер 2 недели не дует. вот и у меня не дул. Есть конечно небольшой ветерок, но это не то, на чём стоит снимать параметры.
Аксиальный генератор на постоянных магнитах своими руками
Самое доступное, детальное описание конструкцииМного ссылок,фото и видео
Народ, будет желание – ВСЁ ПОЛУЧИТСЯ!
Если руки золотые, то неважно с какого места они растут
САМОДЕЛЬНЫЙ ВЕТРЯК С АКСИАЛЬНЫМ ГЕНЕРАТОРОМ НА НЕОДИМОВЫХ МАГНИТАХ
от Яловенко Валерия Григорьевича email Данный адрес e-mail защищен от спам-ботов, Вам необходимо включить Javascript для его просмотра.
Живу я в маленьком городке Харьковской обл., часный дом, небольшой участок.
Сам я как говорит сосед ходячий генератор идей, так как практически всё в своем
хозяйстве сделано своими руками. Ветер хоть и небольшой, но практически постоянно дует, и тем самым соблазняет использовать свою энергию.
После нескольких неудачных попыток с тракторным самовозбуждающим генератором идея создания ветрогениратора засела в мозгу еще больше. Начал искать и после двух месяцев поисков в инете, множества скачанных файлов, прочтенных форумов и советов я окончательно определился с постройкой генератора.
За основу была взята конструкция Бурлака Виктора Афанасьевича http://rosinmn.ru/sam/burlaka/burlaka.html с небольшими конструктивными изменениями.
Основной задачей была постройка генератора с того материала, который есть, с минимумом затрат. Поэтому каждый, кто попытается сделать подобную конструкцию должен исходить с того материала, который у него есть, главное желание и понять принцип работы.
Для изготовления ротора использовал листовой кусок метала толщиной 20мм (что было) с которого по моим чертежам кум выточил и разметил на 12 частей два диска диаметром 150 мм и еще один диск под винт который разметил на 6 частей диаметром 170 мм.
Купил через Интернет 24 шт. дисковых неодимовых магнита 25?8 мм
http://mega-magnit.ru/ тел. (+38)066 11-77-777 , которые приклеил к дискам, (очень выручила разметка). ОСТОРОЖНО НЕ ПОДСТАВЛЯЕТЕ ПАЛЬЦИ!
Перед тем как приклеить магниты к стальному диску маркером нанесите на магниты полярность , это очень поможет вам избежать ошибок. После размещения магнитов(12 шт. на диск и чередуйте полярность), до половины залил их эпоксидной смолой.
Для изготовления статора использовал эмаль-провод ПЭТ-155 диаметром 0,95 мм (купил на частном предприятии Хармедь). Намотал 12 катушек по 55 витков каждая, толщина обмоток получилась 7 мм. Для намотки изготовил несложный разборный каркас. Намотку катушек делал на самодельном намоточном станке. (делал во времена застоя)
Затем разместил 12 катушек по шаблону и зафиксировал их положение изолентой на тканевой основе. Выводы катушек распаял последовательно начало с началом ,конец с концом. Я использовал 1 фазную схему включения.
.
Для изготовления формы под заливку катушек эпоксидной смолой склеил две прямоугольные заготовки 4 мм фанеры. После высыхания получилась прочная 8 мм заготовка. С помощью сверлильного станка и приспособления (балерина) вырезал в фанере отверстие диаметром 200 мм, а с вырезанного диска вырезал центральный диск диаметром 60 мм. Заранее заготовленные ДСП заготовки прямоугольной формы обтянул плёнкой и по краях закрепил стиплером, затем по разметке разместил вырезанный центр (обтянутый скотчем), а также вырезанную заготовку, обмотанную скотчем.
Форму до половины залил эпоксидной смолой, на дно положил стеклоткань, затем катушки, сверху стеклоткань, долил эпоксидку, немного выждал и сверху сдавил вторым куском ДСП также обтянутым пленкой. После застывания извлёк диск с катушками, обработал, покрасил, просверлил отверстия
Ступицу, а также основу поворотного узла изготовил с буровой трубы НКТ с внутренним диаметром 63 мм. Были изготовлены гнёзда под 204 подшипник и приварены к трубе. С задней стороны тремя болтами прикручена крышка с прокладкой с маслостойкой резины, с передней стороны прикручена крышка с сальником. Внутрь между подшипниками через специальное отверстие залил автомобильное полусинтетическое масло. На вал надел диск с магнитами, причем поскольку паз под шпонку сделать небыло возможности на валу сделал углубления на половину диаметра шарика с 202 подшипника т.е. 3,5 мм, а на дисках высверлил паз 7 мм сверлом предварительно выточив боночку и запрессовал её в диск. После извлечения боночки в диске получился ровный, красивый паз под шарик.
Далее закрепил статор тремя латунными шпильками, вставил промежуточное кольцо с расчетом чтобы статор не затирало и надел второй диск с магнитами(магниты на дисках должны иметь противоположную полярность, т.е. притягиваться) ЗДЕСЬ ОЧЕНЬ ОСТОРОЖНО С ПАЛЬЦАМИ!
чертежи по которым кум точил детали,извените что от руки ,но кум всё понял,мелочи уточняли в процессе.
Винт изготовил с канализационной трубы диаметром 160 мм http://ecotoc.ru/alternative_energy/wind_energy/d120/
Кстати неплохой получается винт.Поэтому принципу изготовлен последний винт с алюминевой трубы 1,3м (смотрите выше)
Разметил трубу, болгаркой вырезал заготовки, по концах стянул болтами и електрорубанком обработал пакет. Затем раскрутил пакет и каждую лопасть обработал отдельно, подгоняя вес на электронных весах.
Защита от ураганного ветра выполнена по классической зарубежной схеме, т. е. ось вращения смещена от центра. Вот ссылка на сайт http://www.otherpower.com/otherpower_wind.html
Желающие узнать больше здесь найдут все интересующие вопросы, причем совершенно бесплатно! Мне этот сайт помог очень здорово особенно с чертежами хвоста. Вот пример чертежей с этого сайта.
Свой хвост ветряка я подгонял методом подпиливания.
Вся конструкция насаженна на два 206 подшипника, которые закреплены на оси с внутренним отверстием под кабель и приваренной к двухдюймовой трубе.
Подшипники плотно входят в корпус ветроустановки, что позволяет без каких либо усилий и люфтов свободно поворачиваться конструкции. Кабель проходит внутри мачты к диодному мосту.(выше смотрите чертежи)
на фото первоначальный вариант
Для изготовления ветроголовки не учитывая двух месяцев поиска решений, ушло полтора месяца, сейчас у нас февраль месяц, снег и холод похоже за всю зиму, поэтому основных испытаний еще не проводил, но даже на этом расстоянии от земли автомобильная лампочка 21 ватт перегорела. Жду весны, готовлю трубы под мачту. Эта зима пролетела у меня быстро и интересно.
VIDEO можно просмотреть здесь
Прошло немного времени с того момента когда разместил на сайте свой ветряк, но весна так толком и не пришла, землю копать чтобы замуровать стол под мачту еще нельзя,-земля мёрзлая да и грязь везде, поэтому времени для испытаний на временной 1,5м стойке было предостаточно, а теперь подробней.
После первых испытаний винт случайно зацепил трубу, это я пытался зафиксировать хвост, чтобы ветряк не уходил из под ветра и посмотреть какая будет максимальная мощность. В итоге мощность успел зафиксировать примерно ватт 40, после чего винт благополучно разлетелся на щепки. Неприятно, но наверное полезно для мозгов. После этого я решил поэкспериментировать и намотал новый статор. Для этого изготовил новую форму под заливку катушек .Форму тщательно смазал автомобильным литолом, чтобы лишнее не пристало. Катушки теперь немного уменьшил по длине, благодаря чему в сектор теперь поместилось 60 витков 0,95мм толщина намотки 8мм (в конечном итоге статор получился 9 мм), причем длина провода осталась прежней.
В эпоксидку добовил тальк примерно 30%
Винт теперь сделал с более прочной трубы 160мм и трехлопастным, длина лопасти 800мм.
Новые испытания сразу показали результат, теперь ГЕНА выдавал до 100 ватт, галогенная автомобильная лампочка в 100 ватт горела в полный накал, и чтобы её не спалить на сильных порывах ветра лампочку отключал.
замеры на автомобильном акумуляторе 55 А.ч.
Теперь окончательные испытания на мачте, результат опишу поже.
Ну, вот уже середина августа, и как я обещал, попытаюсь закончить эту страничку.
Сначала то, что пропустил
Мачта один из ответственных елементов конструкции
Один из стыков (труба меньшего диаметра входит внутрь большей)
и поворотный узел
3-х лопастный винт (рыжая канализационая труба диаметром 160мм)
Начну с того, что сменил несколько винтов и остановился на 6-ти лопастном с алюминиевой трубы диаметром 1,3м, хотя большую мощность давал винт с ПВХ трубы 1,7м.
Основная проблема была в том чтобы заставить заряжаться АКБ от малейшего вращения винта и вот здесь на помощь пришел блокинг генератор который даже при входном напряжении в 2v дает заряд АКБ – пускай маленьким током, но лучше чем разряд, а на нормальных ветрах вся энергия на АКБ поступает через VD2(смотрите по схеме), и идет полноценный заряд.
Конструкция собрана прямо на радиаторе, полунавесным монтажом,если монтаж правильный,- работает без проблем. В некоторых случаях для запуска блокин-генератора возможно уменьшение сопротивления R1 до 500 Ом, трансформатор – феритовое кольцо диаметром 45мм, сечение 8мм на 8мм ( можно намотать на строчном трансе от старого телека), намотан проводом 1мм ,сначала мотал 60 витков ,а сверху равномерно намотал 21 виток
Контролёр заряда тоже использовал самодельный, схема простая, слепил как всегда с того, что было под рукой, нагрузкой служит два витка нихромового провода (при заряженном АКБ и сильном ветре нагревается до красна) Все транзисторы ставил на радиаторы (с запасом), хотя VT1 и VT2 практически не греются, а вот VT3 на радиатор ставить обязательно! (при продолжительном срабатывании контролёра VT3 греется прилично)
фото готового контролёра
простая схемка
Схема подключения ветряка к нагрузке выглядит так
фото готового системного блока
Вид сзади
Нагрузкой у меня как и планировалось, является свет в туалете и летнем душе + уличное освещение (4 светодиодные лампы которые включаются автоматически через фотореле и освещают двор целую ночь ,с восходом солнца опять срабатывает фотореле которое отключает освещение и идет заряд АКБ .И это на убитой АКБ (в прошлом году снял с авто)
на фото снято защитное стекло ( в верху фотодатчик)
Фотореле купил готовое для сети 220V и переделал на питание от 12V(перемкнул входной конденсатор и последовательно стабилитрону подпаял резистор в 1К)
Теперь самое ГЛАВНОЕ.
С своего опыта, советовал для начала сделать небольшой ветрячок, набратся опыта и знаний и понаблюдать что можно поиметь с ветров вашей местности,Ведь можно потратить кучу денег, сделать мощный ветряк ,а силы ветра не хватит чтобы получать теже 50 ватт и будет ваш ветряк типа подводной лодки в гараже. Здесь ЛУЧШЕ СИНИЦА В РУКАХ ЧЕМ ДЯТЕЛ В ЖО-Е.
Простейший анемометр.Квадрат сторона 12см на 12см,на нитке 25см привязан тенисный шарик.
Я сделал вот такой анемометр
Мы никогда незадумываемся насколько сильным бывает даже маленький ветерок,но стоит посмотреоть с какой скоростью иногда раскручивается турбина и сразу понимаеш какая это мощь
Ветер, ветер ты могуч. (фото со двора)
Процес модернизации ветряка закончен , так он выглядит на даном этапе.На видео его рабочий режим (снимал фотокамерой, поэтому видна дискретность винта, насамом деле он крутится как подорваный). На очень малых ветрах работает БЛОКИНГ ГЕНЕРАТОР.
Вот сайты, по которым можно отыскать много интересного
Для Харьковчан и не только
Всем удачи.
Буду рад если хоть немножко комуто помог,все вопросы на стену или email
Как сделать аксиальный ветрогенератор
Эта статья посвящена созданию аксиального ветрогенератора на неодимовых магнитах со статорами без металла. Ветряки подобной конструкции стали особенно популярны из-за растущей доступности неодимовых магнитов.
Материалы и инструменты использованные для постройки ветряка этой модели:
1) ступица от автомобиля с тормозными дисками.
2) дрель с металлической щеткой.
3) 20 неодимовых магнитов размером 25 на 8 мм.
4) эпоксидная смола
5) мастика
6) труба ПВХ 160 мм диаметром
7) ручная лебедка
8) труба металлическая длинной 6 метров
Рассмотрим основные этапы постройки ветряка.
За основу генератора была взята ступица автомобиля с тормозным диском. Так как основная деталь заводского производства, то это послужит гарантом качества и надежности. Ступица была полностью разобрана, подшипники находящиеся в ней были проверены на целостность и смазаны. Так как ступица была снята со старого автомобиля, то ржавчину пришлось зачистить с помощью щетки, которую автор насадил на дрель.
Ниже предоставлена фотография ступицы.
Затем автор приступил к установке магнитов на диски ротора. Было использовано 20 магнитов. Причем важно заметить, что для однофазного генератора количество задействованных магнитов равно количеству полюсов, для двухфазного соотношение будет три к двум или четыре полюса к трем катушкам. Магниты следует крепить на диски с чередованием полюсов. Для соблюдения точности необходимо сделать шаблон размещения на бумаге, либо начертить линии секторов прямо на самом диске.
Рассмотрим основные отличия конструкции однофазного и трехфазного генераторов.
Однофазный генератор будет давать вибрацию при нагрузках, что будет отражаться на мощности самого генератора. Трехфазная конструкция лишена подобного недостатка благодаря чему, мощность постоянна в любой момент времени. Это происходит потому, что фазы компенсируют потерю тока друг в друге. По скромным расчетам автора трехфазная конструкция превосходит однофазную на целых 50 процентов. К тому же из-за отсутствия вибраций мачта не будет дополнительно раскачиваться,следовательно не будет дополнительного шума при работе ротора.
При расчете зарядки 12-ого аккумулятора, которая будет начинаться на 100-150 оборотах в минуту, автор сделал по 1000-1200 витков в катушках. При намотке катушек автор использовал максимально допустимую толщину проволоки, чтобы избежать сопротивления.
Для наматывания проволоки на катушки автор соорудил самодельный станок, фотографии которого представлены ниже.
Лучше использовать катушки эллипсоидной формы, что позволит большей плотности магнитных полей их пересекать. Внутреннее отверстие катушки стоит делать по диаметру магнита либо больше него. В случае, если делать их меньше, то лобовые части практически не участвуют в выработке электроэнергии, а служат проводниками.
Толщина самого статора должна равняться толщине магнитов, которые задействованы в установке.
Форму для статора можно сделать из фанеры, хотя автор решил этот вопрос иначе. Был нарисован шаблон на бумаге, а затем сделаны борта при помощи мастики. Так же для прочности была использована стеклоткань. Для того, чтобы эпоксидная смола не прилипла к форме, ее необходимо смазать воском или вазелином, или можно использовать скотч, пленку, которую в последствии можно будет отодрать от готовой формы.
Перед заливкой катушки необходимо точно закрепить, а их концы вывести за пределы формы, чтобы затем соединить провода звездой или треугольником.
После того, как основная часть генератора была собрана, автор измерил протестировал его работу. При ручном вращении генератор вырабатывает напряжение в 40 вольт и силу тока в 10 ампер.
Для поднятия мачты используется ручная лебедка.
Сам винт для генератора был сделан из трубы ПВХ диаметром 160 мм.
После установки и испытаний генератора в стандартных условиях автор сделал следующие наблюдения: мощность генератора доходит до 300 ватт при ветре в 8 метров в секунду. В последующем увеличил мощность генератора за счет металлических сердечников установленных в катушки. Винт стартует уже при двух метрах в секунду.
Дальше автор приступил к совершенствованию конструкции в целях увеличения мощности генератора. Были набраны магнитопроводы из пластин, которые в последствии были установлены в конструкцию. Из-за их установки появился эффект залипания, но не очень сильный. Старт работы винта происходит при скорости ветра около двух метров в секунду.
Таким образом установка металлических сердечников увеличила мощность генератора до 500 ватт при ветре в 8 метров в секунду.
Для защиты от сильных ветров была использована классическая схема увода винта складывающимся хвостом.
В среднем генератор способен вырабатывать до 150 ватт энергии в час, которая идет на зарядку аккумуляторов.
сборка статора, крыльчатки и выбор количества фаз генератора
Самодельный ветряк
Приобретение ветрогенератора — дорогостоящая и не всегда полностью эффективная затея. Образцы ветряков, имеющиеся в продаже, имеют ограниченный срок службы, низкую ремонтопригодность и высокую цену. Покупка такого комплекта не по карману многим потенциальным пользователям. Выходом из положения становится самостоятельное изготовление ветрогенератора, обходящееся гораздо дешевле и позволяющее получить устройство с высокой эффективностью и производительностью.
Самодельный ветряк имеет высокую ремонтопригодность и, как следствие, длительный срок службы. Зачастую конструкцию по ходу эксплуатации модернизируют, улучшают и доводят до максимально возможных параметров, чего нельзя сделать с заводскими комплектами.
Тихоходные ветрогенераторы
Наиболее привлекательными конструкциями ветряков для большинства регионов России являются образцы, дающие высокие показатели на слабых и средних ветрах — тихоходные ветряки. Для них характерна возможность начинать вращение при низких скоростях потока, выдавая достаточное напряжение для питания приборов потребления.
Выработка энергии на таких устройствах производится генераторами, адаптированными к работе с ветряками. Специфика конструкции таких генераторов состоит в высокой чувствительности, поскольку устройство изначально рассчитывается на работу с низкими скоростями вращения.
Для того, чтобы обеспечить заданный режим работы, необходимо обмотку возбуждения исключить из конструкции, заменив ее постоянными магнитами. В результате отпадет необходимость подачи напряжения для образования электромагнитов, индукция станет более стабильной, независимой от источника питания на обмотке ротора. Кроме того, отпадет надобность в щеточном узле, подающем питание на обмотку возбуждения.
Изготовление ротора на постоянных магнитах
Конструкция генератора на постоянных магнитах в каком-то смысле проще, чем с электромагнитным возбуждением. Создание такого устройства может выполняться как на базе готового генератора, так и при помощи подручных материалов.
Модификация автомобильного генератора
Создание ротора на постоянных магнитах требует достаточно серьезного вмешательства в конструкцию. Необходимо уменьшить диаметр на толщину магнитов плюс толщину стальной гильзы, которая одевается на ротор для образования сплошного магнитного потока и одновременно служит посадочной площадкой под магниты. Некоторые специалисты обходятся без гильзы, устанавливая магниты прямо на ротор с уменьшенным диаметром и фиксируя на эпоксидку.
Процесс изготовления требует участия производственного оборудования. В токарный станок зажимается ротор и аккуратно снимается слой с таким расчетом, чтобы установленные магниты вращались с минимальным зазором, но вполне свободно. Установка магнитов производится на пластины ротора с чередованием полюсности.
Наибольшего эффекта удается добиться при установке относительно небольших по размерам магнитов, расположенных рядами в продольном направлении. Достигается ровный и мощный магнитный поток, воздействующий на силовые обмотки статора с равномерной плотностью во всех точках.
Изготовление ротора из ступицы и тормозного диска
Рассмотренный способ относится к готовым генераторам, нуждающимся в небольших изменениях конструкции. К таким устройствам относятся автомобильные генераторы, часто применяющиеся самодеятельными конструкторами в качестве базового устройства. Зачастую генераторы собирают полностью самостоятельно, не имея готового устройства.
В таких случаях действуют несколько иначе. За основу берется автомобильная ступица с тормозным диском. Она качественно отбалансирована, прочна и приспособлена к нагрузкам определенного рода. Кроме того, размер ступицы позволяет разместить по окружности большое число магнитов, позволяя получить трехфазное напряжение.
Магниты с чередованием полюсности размещают на равноудаленном от центра расстоянии. Очевидно, что наибольшее число можно установить, если приклеивать их как можно ближе к наружному краю. Наиболее точным показателем станет размер магнитов, который определит возможность размещения на определенном расстоянии. Число магнитов должно быть четным, чтобы не сбивался ритм чередования полюсов при вращении.
Наклейка магнитов на ступицу производится при помощи любого клея, оптимальным вариантом считается эпоксидная смола, которой заливают магниты полностью. Это защищает их от воздействия влаги или от механических воздействий. Перед заливкой по краю ступицы рекомендуется сделать бортик из пластилина, не позволяющий эпоксидке стекать со ступицы вниз.
Конструкция генератора на автомобильной ступице наиболее удобна при изготовлении вертикального ветряка. Примечательно, что подобную схему можно использовать и без ступицы, на диске, вырезанном из обычной фанеры. Такая конструкция намного легче, позволяет выбирать удобный размер, что делает возможным создание чувствительного и производительного устройства.
Ветряк с аксиальным генератором на неодимовых магнитах
Наиболее сильными магнитами, обладающими оптимальными параметрами для использования в конструкции генератора, являются неодимовые магниты. Они несколько дороже обычных, но превосходят их многократно и дают возможность создать мощное устройство при относительно компактном размере.
Принципиального отличия в конструкции не имеется. Неодимовые магниты изготавливаются в различных формфакторах, позволяющих выбрать наиболее удобный для себя вариант — тонкие продолговатые брусочки, форма таблетки, цилиндры и т.д. если используется металлический ротор, то приклеивать магниты необязательно, они сами по себе с усилием прикрепляются к основанию. Остается лишь залить их эпоксидкой для защиты от коррозии.
Приобрести такие магниты проще всего через Интернет, заодно можно сразу же выбрать самую удобную форму.
Изготовление статора
Статор — это неподвижная часть генератора, несущая силовую обмотку, индуцирующую электрический ток. В зависимости от типа конструкции, статор может быть использован от готового устройства (например, от автомобильного генератора), или изготовлен с нуля самостоятельно. Техника изготовления в каждом случае своя, но принцип остается общий — по окружности, охватывающей вращающийся ротор, располагаются катушки, вырабатывающие переменный ток.
При модификации автомобильного генератора иногда силовые обмотки не трогают, предпочитая изменить конструкцию ротора и на этом остановиться. Чаще всего причиной тому является слабая техническая или теоретическая подготовка, когда мастер имеет весьма смутное представление, как именно подобные вещи делаются. Рассмотрим вопрос внимательнее:
Выбор количества фаз
Многие мастера пытаются облегчить себе задачу, делая генератор на одну фазу. В данном случае простота весьма сомнительная, так как экономия усилий получается только на стадии намотки катушек. Зато при эксплуатации получается неприятный эффект — амплитуда напряжения имеет классический вид, отчего выпрямленный ток имеет пульсирующую структуру.
Скачки противопоказаны аккумуляторам, создают отрицательное воздействие на все узлы комплекса и способствуют быстрому выходу из строя. Появляется вибрация, которая может стать причиной жалоб соседей, источником неприятных ощущений для людей или животных.
Трехфазная конструкция, напротив, имеет более мягкую огибающую, в выпрямленном состоянии ток практически не имеет каких-либо отклонений. Мощность устройства имеет стабильное значение, сохраняется в рабочем состоянии механическая и электрическая часть агрегата.
Выбор между трех- и однофазным устройством однозначно следует делать в сторону трехфазной конструкции. Количество намотанных катушек возрастает, но число витков не настолько велико, чтобы отказываться от более качественного результата из-за призрачной экономии времени.
Модификация статора автогенератора
Автомобильный генератор имеет готовые силовые катушки, плотно уложенные в каналах статора. Для получения качественного результата требуется изменить чувствительность статора, поскольку номинальная частота вращения автомобильного двигателя находится в пределах 2000-3000 об/мин, а на пике может подниматься до 5000-6000 об/мин. Таких параметров ветряк выдать не в состоянии, а использование повышающей передачи значительно снизит мощность крыльчатки.
Решением вопроса становится увеличение количества витков, для чего старые обмотки демонтируются, а на их место наматываются новые, с большим числом витков из более тонкого провода. При этом, нельзя использовать слишком тонкий провод, так как с возрастанием числа витков растет и сопротивление, делающее генератор менее производительным. Необходимо соблюдать «золотую середину», увеличивая количество аккуратно, без излишнего рвения.
Важно! Подобная операция требует расчета, но на практике чаще всего поступают проще — наматывают столько витков, сколько способна вместить конструкция статора. Результат обычно достигается положительный, поскольку слишком большое число витков вместить не получится.
Изготовление статора аксиального типа
Такая конструкция подойдет для генератора аксиального типа, ротор которого создан из ступицы и тормозного диска от автомобильного колеса. Статор имеет форму плоского диска, по окружности которого расположены силовые обмотки. Они должны быть намотаны из достаточно толстого провода, чтобы число витков было достаточным, но и сопротивление не снижало эффективность конструкции. Количество катушек кратно трем, чтобы на каждую фазу приходилось одинаковое количество.
Соединяются они между собой звездой, для каждой фазы соединяются 1, 4, 7, 10 и т.д. При намотке однофазного статора каждая катушка мотается в противоположном направлении — первая по часовой стрелке, вторая — против, затем опять по часовой и т.д. соединяются они последовательно.
Готовый статор устанавливается соосно с ротором. Зазор между катушками и неодимовыми магнитами должен быть минимальным, но ход ротора свободный, без соприкосновения с катушками.
Для защиты от влаги, пыли или прочих воздействий катушки обычно заливают эпоксидной смолой. Для этого предварительно делается по внешнему краю диска статора бортик из пластилина высотой, немного превышающей слой заливки.
Сборка крыльчатки
Крыльчатка должна обеспечивать максимальную чувствительность. Перед тем, как начать создание ветряка, следует подробно изучить метеорологическую обстановку в регионе, направление и скорость преобладающих ветров, частоту и силу шквалистых порывов, возможность ураганов. Эта информация поможет выбрать наиболее подходящую конструкцию ветряка (вертикальный или горизонтальный, размер, количество лопастей и т.п.).
Создание крыльчатки производится из подручного материала на основании параметров генератора. Размер лопастей должен обеспечивать начало вращения при невысоких скоростях потока, но не создавать чрезмерно большой преграды. Это снизит риск падения мачты при сильном порыве или шквале.
Регионы с нестабильными и часто меняющимися ветрами (каких большинство в России) больше подходят для эксплуатации вертикальных конструкций. Горизонтальные ветряки считаются более эффективными, но нуждаются в установке на высокие мачты, что создает проблемы при обслуживании.
Рабочее колесо ветрогенератора должно быть качественно отбалансировано и прочно соединено. Установка комплекта на крышу дома запрещается, особенно, если в нем проживает несколько семей. Рекомендуется выбирать открытое место на возвышении неподалеку от дома, чтобы длина кабеля не создавала большого сопротивления. Поблизости не должно быть преград, высоких деревьев или зданий, заслоняющих прямой поток ветра.
Рекомендуемые товары
Торцевой аксиальный генератор для ветротурбины
Многие мечтают создать для ветротурбины генератор своими руками. Достать стальную электротехническую холоднокатанную анизотропную ленту не всегда возможно. По этой причине рассмотрим способ изготовить сердечник статора с подручных материалов. Такие генераторы просты в изготовлении и достаточно эффективны.
Вот один из примеров, как создать торцевой аксиальный генератор для ветротурбины. Для изготовления статора могут подойти пластины от старых 110 вольтовых звуковых трансформаторов. На рынке их достаточное количество и пластины у них легко отделяются друг от друга.
В качестве магнитов используем диски размером 19х4 мм, соответственно этим размерам рассчитываем и размеры статора. Размечаем на бумаге контуры статора. По всей окружности должно равномерно разместиться 24 зуба (8 катушек на 3 фазы), и соответственно 16 выводов с каждой группы. В результате внешний диаметр статора составляет 145 мм, а внутренний – 105 мм. Заполняем пространство между внешним и внутренним диаметром пластинами, которые соединяем между собой при помощи суперклея.
Результатом нашей работы получилась вот такая заготовка статора.
Наклеиваем ее на фанеру и пропитываем эпоксидной смолой. Когда конструкция высохнет, необходимо ножовкой удалить все ненужные части фанеры, оставив немного с внутренней стороны, а также внешний ободок. Он будет использоваться в качестве площадки для крепления. Сами зубцы аккуратно обрабатываем напильником. Чтобы во время обработки пластины не отделялись от общей конструкции, каждый обрабатываемый зуб обжимаем небольшой струбциной. Все работы должны выполняться очень внимательно. Ведь даже несколько небольших острых выступов могут повредить изоляцию провода. Если есть возможность, лучше на зубцы надеть усадочную трубку. Каждому известно, что процесс переделывания всегда намного труднее, чем изготовление.
Катушки лучше наматывать непосредственно на месте, чем отдельно с последующим надеванием на зуб. В этом случае она будет плотнее прилегать к пластинам статора, и устройство в целом будет иметь лучшие электротехнические показатели. Провод для катушек лучше выбирать 0,7 мм. Есть возможность делать обмотки проводом 0,5 мм, но тогда генератор будет выдавать ток меньшей величины, когда напряжение будет достаточным в обоих случаях. Чем плотнее витки провода будут прилегать друг к другу, тем будет лучше, поэтому спешить и делать все быстро, но не совсем качественно, не рекомендуется.
Готовый статор устанавливаем на ступицу. В качестве ее может служить часть помпы от Уазика. Конструкция в этом случае будет прочная и более легкая, чем использование деталей от других автомобилей, например Ваз 2108. Обмотки генератора соединяются по схеме «звезда». Зачастую проверить дома готовое изделие на стенде нет возможности, но существует более примитивный метод, которым возможно сделать приблизительные измерения. На спицы наматывается веревочка. Когда за нее тянуть не очень сильно, на выходе будет ток около 6 А. Если приложить больше усилий, есть возможность увеличить ток до 11,5 А и напряжение 12,4 В.
Когда основные работы сделаны, к изделию крепятся три лопасти по 1,7 м и все вместе закрепляется на открытой местности. Вес изготовленной конструкции не превышает 4 кг. Изделие, конечно, имеет некоторые недостатки, так как собрано из подручных средств. В частности площадь магнита больше площади зуба. Но даже в данном варианте, когда скорость вращения за минуту достигает 900 оборотов, мощность на выходе становит не менее 200 ватт.
.
Генератор с осевым потоком
Генератор осевого потока (иногда называемый генератором) является сердцем многих проектов ветряных турбин своими руками. Хотя небольшой двигатель постоянного тока с постоянным магнитом, такой как Ametek 30, обеспечивает очень быструю и простую проектную сборку, эти двигатели становится очень трудно найти и они становятся довольно дорогими. Ebay переполнен людьми, продающими двигатели постоянного тока для проектов домашних ветряных турбин, которые просто НЕ будут работать из-за чрезвычайно высоких оборотов, необходимых для получения какой-либо полезной мощности.Таким образом, самодельный генератор с осевым потоком может быть вашей лучшей альтернативой.
Что такое генератор с осевым потоком?
Генератор с постоянными магнитами генерирует мощность, пропуская магниты через группу катушек с проволокой. Магнитное поле, окружающее магнит, называется потоком. Осевой поток просто означает, что линии магнитного потока, проходящие через катушки с проволокой, проходят вдоль «оси» вращательного движения. Другой тип магнитного потока в генераторе переменного тока называется РАДИАЛЬНЫЙ ПОТОК и возникает, когда магнитный поток возникает «вокруг» магнита.Картинки дороже тысячи слов:
На левом рисунке желтый диск — статор. Две голубоватые пластины вращаются вдоль горизонтальной оси мимо неподвижного статора. На изображении справа статор находится на корпусе. Ротор на оси вращается «внутри» статора. Есть руководство Хью Пигготта, в котором подробно описан процесс.
Обзор всего процесса — создание генератора с осевым потоком
В феврале 2001 года Хью Пигготт создал руководство по созданию генератора с постоянными магнитами (PMG) (генератора переменного тока) после того, как оно было заказано британским правительством.Это руководство остается в открытом доступе и дает отличный обзор всего процесса. Вы можете построить PMG из этих планов, хотя эти инструкции продолжают улучшаться. Документ в формате PDF можно скачать здесь: PMG Manual
В этом руководстве описывается, как построить «генератор на постоянных магнитах» (PMG). Мы можем также назвать его
«генератором переменного тока», потому что он вырабатывает переменный ток (AC).Статор содержит шесть витков медной проволоки, залитой стекловолокном.Эта отливка статора
устанавливается на корешок; он не двигается. Провода от катушек подают электричество
на выпрямитель, который меняет переменный ток на постоянный для зарядки аккумулятора. Выпрямитель
установлен на алюминиевом «радиаторе» для охлаждения.
Магнитные роторы установлены на подшипниках, которые вращают вал. Задний ротор находится на
позади статора и заключен в него. Передний находится снаружи, прикреплен к заднему
с помощью длинных шпилек, которые проходят через отверстие в статоре.Лопасти ротора
ветряной турбины будут установлены на тех же шпильках. Они будут вращать магнитные роторы и перемещать магниты мимо катушек. Магнитный поток проходит от одного ротора к другому через статор. Этот движущийся магнитный поток производит электроэнергию.
Улучшения дизайна Хью Пигготта
Дэн Бартманн и Дэн Финк, а также другие продолжали создавать генераторы с осевым потоком и улучшать первоначальную конструкцию.Дэн и Дэн поддерживают веб-сайт Otherpower, который включает дополнительную информацию о том, как построить один из этих генераторов переменного тока, а также ссылки на их книги по этой теме. После нескольких раз прочтения PDF-документа Хью, это ваш следующий шаг.
Взгляните на проект полностью. Да, в первый или два раза, когда вы прочитаете этот процесс, он может показаться довольно сложным и БОЛЬШИМ. Однако Dan & Dan предоставляют инструкции для человека, который хочет построить несколько генераторов переменного тока.Лично я бы изменил некоторые инструкции для собственного использования.
Например, я бы не стал делать намотчик катушек с индивидуальной металлической подставкой и металлической ручкой — мне подходит дерево.
Вот ссылка на веб-сайт OtherPower, где вы можете найти дополнительную информацию о том, как построить генератор с осевым потоком, а также о лопастях ветряных турбин и металлоконструкциях:
OtherPower — PMG
Дополнительные ресурсы для генераторов с осевым потоком
Техническая группа AxialFlux на Yahoo
Типовой генератор своими руками.(а) Ротор, использующий ПМ с вырезанного жесткого диска. (b) Без сердечника …
Контекст 1
… из этих генераторов используют PM из HDD для производства потока и используют статор без сердечника, оборудованный неперекрывающимися обмотками, как показано на Рис. 1. В этих машинах, PM снимаются с их опорных пластин, разрезаются и закрепляются на стальных дисках ротора. PM от HDD изготовлены из высокоэнергетических редкоземельных неодим-железо-борных магнитов (NdFeB) и используются из-за их хорошего производства магнитного потока по сравнению с ферритовыми магнитами, которые используются, например, в динамиках.Своеобразная форма и …
Контекст 2
… большое значение. Только один магнит жесткого диска, то есть шестнадцатый из дисков ротора PM, необходимо было смоделировать из-за нынешних симметричных и периодических условий работы машины. Чётное / циклическое периодическое граничное условие применяется к сторонам как двухмерной, так и трехмерной модели. Для двухмерной модели симметрия была задана вдоль пунктирной линии на рис.10, но не могла быть использована для трехмерной модели, поскольку полную обмотку можно было смоделировать только в трехмерной среде, как показано на рис.11. Глубина двумерного моделирования была установлена на 15 мм, что равно длине магнитов в радиальном направлении (l a). Остаточная магнитная индукция магнитов должна быть определена для …
Контекст 3
… и периодических состояний машины. Чётное / циклическое периодическое граничное условие применяется к сторонам как двухмерной, так и трехмерной модели. Для двухмерной модели симметрия была задана вдоль пунктирной линии на рис.10, но не могла быть использована для трехмерной модели, поскольку полную обмотку можно было смоделировать только в трехмерной среде, как показано на рис.11. Глубина двумерного моделирования была установлена на 15 мм, что равно длине магнитов в радиальном направлении (l a). Остаточная магнитная индукция магнитов должна быть определена для FEA. Поскольку марка магнитов PM жестких дисков неизвестна, плотность потока была измерена в центре воздушного зазора двух противоположных жестких дисков …
Контекст 4
… анализ чувствительности будет проводиться только в 2 -D, поскольку двухмерная модель была проверена трехмерной моделью.Двухмерная модель предполагает кубоид для формы PM, как показано на рис. 15. Трехмерные размеры кубоида следующие: ширина магнита (bp), которая равна одному шагу полюсов (τ p) для идеальная машина, высота магнита (h M) и глубина магнита, которая равна длине PM в радиальном направлении (la) для идеальной машины. Высота магнита и глубина магнита будут иметь аналогичные эффекты на …
Контекст 5
… на глубину магнита, которая равна длине PM в радиальном направлении (l a) для идеальной машины.Высота магнита и глубина магнита будут иметь аналогичные эффекты на форму сигнала обратной ЭДС, поскольку оба размера только уменьшают эффективный поток на полюс. Следовательно, при анализе будут изменяться только высота и ширина магнита, как показано на рис. …
Контекст 6
… имеет симметрию в центре воздушного зазора. Этот сценарий, вероятно, будет реализован, поскольку каждый жесткий диск состоит из двух одинаковых наборов магнитов. Для несимметричной конфигурации PM магниты расположены случайным образом, и симметрия отсутствует.Были смоделированы четыре из 16 неразрезанных магнитов, т. Е. Машина воспроизводится после четырех магнитов, как показано на рис. 15. Электрический цикл (= 22,5 мех. Градуса) представляет собой идеальную конфигурацию магнита с bp = τ p, за которой следуют три конфигурации PM. , которые имеют большую или меньшую ширину и высоту полюса (см. рис. 15). Сплошная линия представляет модель с симметрией, а пунктирная — модель без симметрии. На рис.16 это может быть …
Контекст 7
… размещен, и симметрии нет. Были смоделированы четыре из 16 неразрезанных магнитов, т. Е. Машина воспроизводится после четырех магнитов, как показано на рис. 15. Электрический цикл (= 22,5 мех. Градуса) представляет собой идеальную конфигурацию магнита с bp = τ p, за которой следуют три конфигурации PM. , которые имеют большую или меньшую ширину и высоту полюса (см. рис. 15). Сплошная линия представляет модель с симметрией, а пунктирная — модель без симметрии. Из рис. 16 можно видеть, что нормальная составляющая плотности потока в воздушном зазоре существенно не зависит от того, используется ли симметрия или нет.Однако тангенциальная составляющая значительно увеличивается, если противоположные магниты …
Контекст 8
… сплошная линия представляет модель с симметрией, а пунктирная — модель без симметрии. Из рис. 16 можно видеть, что нормальная составляющая плотности потока в воздушном зазоре существенно не зависит от того, используется ли симметрия или нет. Однако тангенциальная составляющая значительно увеличивается, если противоположные магниты не идентичны. …
Контекст 9
… симметрия. Из рис. 16 можно видеть, что нормальная составляющая плотности потока в воздушном зазоре существенно не зависит от того, используется ли симметрия или нет. Однако тангенциальная составляющая значительно увеличивается, если противоположные магниты не идентичны. Это может привести к серьезным дополнительным потерям на вихревые токи в обмотках статора [9]. На рис. 17 показаны формы сигнала обратной ЭДС без нагрузки для различных конфигураций магнитов, а соответствующие гармоники показаны на рис. 18. Из рис. 17 можно увидеть, что величина сигнала обратной ЭДС составляет всего лишь затронутый.На плотность потока напрямую влияет высота магнита в соответствии с (6) и, следовательно, среднеквадратичное значение …
Контекст 10
… используется симметрия или нет. Однако тангенциальная составляющая значительно увеличивается, если противоположные магниты не идентичны. Это может привести к серьезным дополнительным потерям на вихревые токи в обмотках статора [9]. На рис. 17 показаны формы сигналов обратной ЭДС без нагрузки для различных конфигураций магнитов, а соответствующие гармоники показаны на рис.18. Из рисунка 17 видно, что это влияет только на величину сигнала обратной ЭДС. Плотность потока напрямую зависит от высоты магнита согласно (6), и, следовательно, влияет на среднеквадратичное значение ЭДС. Уменьшение или увеличение шага полюсов изменяет форму волны плотности потока в воздушном зазоре, и магнитный поток, связывающий …
Контекст 11
… плотность напрямую зависит от высоты магнита в соответствии с (6 ), и, следовательно, влияет на действующее значение ЭДС.Уменьшение или увеличение шага полюсов изменяет форму волны плотности потока в воздушном зазоре, а также изменяется магнитный поток, связывающий катушки. Однако на рис. 17 не наблюдается видимой деформации формы сигнала обратной ЭДС. Даже при анализе содержания гармоник сигналов обратной ЭДС не заметно ухудшения выходного напряжения машины. Значения общего гармонического искажения (THD) были вычислены как 6,9%, 6,5% и 5,3% для переменной высоты PM, переменной ширины PM и комбинации высоты и ширины PM, соответственно.Эти …
Context 12
… статоры на сегодняшний день являются самыми дешевыми и простыми в изготовлении из-за отсутствия железного сердечника. Обмотки статора обычно покрыты эпоксидной смолой. Обмотка была намотана вокруг формы, как показано на рис. 19 (а), чтобы обеспечить симметричную структуру намотки. Таким образом были сформированы три волновые обмотки, а концевые обмотки скручены, чтобы обеспечить перекрытие фаз, как показано на фиг. 11 и 19 (б). Основным недостатком статора без сердечника является большой эффективный воздушный зазор, создаваемый в машине из-за отсутствия…
Контекст 13
… отсутствия железного сердечника. Обмотки статора обычно покрыты эпоксидной смолой. Обмотка была намотана вокруг формы, как показано на рис. 19 (а), чтобы обеспечить симметричную структуру намотки. Таким образом были сформированы три волновые обмотки, а концевые обмотки скручены, чтобы обеспечить перекрытие фаз, как показано на фиг. 11 и 19 (б). Основным недостатком статора без сердечника является большой эффективный воздушный зазор, создаваемый в машине из-за отсутствия ферромагнитного сердечника статора.Следовательно, воздушный зазор устойчивого ветрогенератора должен быть как можно меньше из-за фиксированной формы и произведения энергии магнитов HDD по сравнению с …
Контекст 14
… магниты, адаптированные под конкретную конструкцию машины. По этой причине статор был спроектирован с канавкой, в которой магниты жесткого диска могут вращаться, чтобы минимизировать эффективный воздушный зазор. На рис. 20 показана полная структура статора до и после заливки эпоксидной смолы.Полная сборка генератора показана на рис. 21. …
Генератор осевого потока готов принять вес и проблемы из гондол
Генераторы с прямым приводом Magnax позволят избежать проблем с редукторами
Небольшой стартап в Бельгии завершает разработку прототипа генератора, который легче, меньше и эффективнее обычных конструкций аналогичной мощности. Изобретатель и основатель Magnax Питер Лейнен говорит, что его прототип с осевым потоком 100 кВт весит около 850 кг, что значительно меньше, чем у традиционного генератора с прямым приводом, который обычно весит 4000 кг или больше.Преимущества новой технологии включают более высокую эффективность (от 96% до 97%, в зависимости от размера машины), надежность и масштабируемость при относительно низких производственных затратах. Хотя прототип будет установлен в ветряной турбине среднего размера с прямым приводом, Лейнен добавляет, что компания Magnax сосредоточена на разработке машин мегаваттного размера для крупных ветряных турбин.
«Идея нового генератора возникла, когда клиент попросил меня разработать новый тип ветряной турбины, для которой требуется генератор с прямым приводом и значительно меньший вес», — говорит Лейнен.После некоторого исследования рынка он пришел к выводу, что ни один существующий генератор не будет соответствовать требованиям. «Итак, я решил построить один. Предыдущие исследования показали, что цель может быть достигнута только с помощью так называемой топологии «осевого потока», которая работает для генераторов и двигателей ».
При одинаковом диаметре конструкция Magnax составляет примерно половину длины и треть веса обычного генератора аналогичной мощности. Трехэлементный дизайн — это концептуальная иллюстрация.
К счастью, Гентский университет, который находится недалеко от того места, где живет Лейнен, исследовал технологию осевого потока в течение последних шести лет.Тем не менее, впереди стояла серьезная задача превратить эту технологию в конструкцию, которую можно было бы производить с высокой степенью автоматизации в промышленных масштабах и с номинальной мощностью до нескольких МВт.
На основе расчетов и электромагнитного моделирования, проведенных в университете, команда Лейнена спроектировала и построила прототип мощностью 100 кВт «за два года серьезных исследований и разработок и создания прототипов», — говорит он.
Несмотря на их электромагнитное превосходство над машинами с радиальным потоком, конструкции с осевым потоком создают серьезные производственные проблемы.Лейнен говорит, что это основная причина, по которой сегодня в большинстве генераторов используется радиальный поток.
По его словам, первая проблема заключалась в том, чтобы найти способ точно зафиксировать и расположить зубья статора и обмотки в статоре, что сложно, поскольку между ротором и статором действуют большие магнитные силы. Воздушный зазор должен быть равномерным и небольшим.
Большой полый вал на станках Magnax предоставляет достаточно места для интеграции несущей системы, которая не зависит от внутреннего подшипника генератора.Это позволяет спроектировать несущую систему, подходящую для данной области применения. Кроме того, по словам Лейнена, осевой воздушный зазор означает, что даже отклонения системы подшипников не влияют на воздушный зазор. Также возможно использовать только внутренний подшипник Magnax Machine в случаях, когда прилагаются только крутящие нагрузки.
«Вторая проблема заключалась в охлаждении обмоток, что сложно, поскольку они находятся глубоко внутри статора и между двумя дисками ротора. Третья проблема заключается в том, что традиционные станки с осевым флюсом, как известно, сложны в производстве, и практически невозможно полностью автоматизировать их производство.Машины с радиальным потоком легче производить, потому что они используют более или менее те же принципы, что и хорошо известные индукционные генераторы ». Лейнен говорит, что новая запатентованная механическая концепция решает проблемы и обеспечивает высокую степень автоматизации производства.
Электромагнитные расчеты на машинах с осевым потоком, добавляет он, особенно сложны и требуют огромного количества моделирования методом конечных элементов и аналитических расчетов. «Параметры, такие как напряжение на клеммах, потери в стали, потери на вихревые токи в постоянных магнитах, потери в меди, пульсации крутящего момента и крутящий момент, должны быть рассчитаны еще до того, как вы сможете приступить к проектированию механической части.За последние шесть лет Гентский университет накопил опыт в этой области, особенно в отношении машин с осевым потоком. Поэтому они создали электромагнитную модель, которую я затем перевел в механическую конструкцию, используя нашу новую концепцию », — говорит Лейнен.
По его словам, он убежден, что энергия ветра останется самой крупной долей в производстве возобновляемой энергии, даже при экспоненциальном росте солнечной энергии. «С такими инновациями энергия ветра в конечном итоге станет дешевле, чем энергия ископаемого топлива, даже с турбинами мощностью менее мегаватта в автономных приложениях.Еще больший потенциал имеет морской ветер. Технические достижения позволят строить турбины все большего размера, что приведет к дальнейшему снижению затрат на электроэнергию. Развертывание в таком большом масштабе и на таких обширных пространствах, как океан, потребует компонентов с низким уровнем обслуживания или даже без них, и наши генераторы с прямым приводом и герметизированными обмотками также будут трудно превзойти в этом отношении ».
Радиальные потоки и, следовательно, силы в большинстве обычных генераторов проецируются радиально. Компания Magnax предложила конструкцию с осевым потоком, которая имеет ряд преимуществ и проблем при проектировании.
Итак, что будет дальше с Magnax? «С точки зрения разработки продукта у меня есть четкое представление о том, как мы можем внедрять инновации с помощью этих машин. Не только в ветроэнергетике, но и для других целей, таких как лифты и самолеты », — говорит он.
Лейнен добавляет, что, поскольку концепция доказана, его соучредитель Даан Морелс готовит план выхода на рынок. «Потребуется некоторое время, чтобы найти идеальные варианты использования и возможности совместного создания, но мы продолжим и дальше использовать промышленные инновации с помощью двигателей и генераторов с прямым приводом, которые превосходят традиционные технологии по весу, эффективности, надежности и стоимости. эффективность.Таким образом, мы поддерживаем глобальный переход к полностью возобновляемым источникам энергии и сверхэффективным машинам ». Морелс добавляет, что генератор Magnax прошел испытания прототипа, работу которых можно увидеть в этом видео: https://goo.gl/VYQGQq
Из рубрики: Генераторы
С тегами: Magnax
Подключение статора — Homebrew Wind Power
На рисунке показано, как мы будем соединять катушки вместе. Каждая фаза пронумерована и состоит из 3 последовательно соединенных катушек.Мы определяем, что каждая катушка (и каждая фаза) имеет «начало» и «конец». «Начало» — это вывод, который идет изнутри катушки, а «конец» — это снаружи катушки. Единственное, что не показано на рисунке, — это соединение «звездой». (На чертеже начала обозначены A, B и C, концы обозначены X, Y и Z) Чтобы соединить звездой, вы соедините 3 начала (A, B и C). Единственная разница между чертежом и тем, что вы собираетесь сделать, заключается в том, что вы будете выполнять все соединения на внутреннем диаметре статора.
Возьмите 3 катушки и поместите их в форму в правильном положении. Выберите 3 клетки на расстоянии 120 градусов друг от друга. Если вы можете наложить и отобразить наши магнитные роторы на этих трех катушках, вы увидите, что они видят «идентичную» магнитную ситуацию, поэтому они находятся «в фазе» друг с другом. (когда один из них находится на максимальном напряжении, то же самое будет и с двумя другими). Убедитесь, что все 3 катушки расположены одной стороной вверх (начало катушки — это провод, который пересекает внутреннюю часть, и он должен быть направлен вверх — вы должны быть уверены, что никакие катушки не перевернуты.Мы собираемся подключить 1 фазу генератора.
Возьмите «конец» одной катушки и оберните его так, чтобы он указывал на внешнюю сторону формы, и прикрепите липкой лентой к ножке катушки. (Обычно при этом вы добавляете к катушке 1/2 оборота). Раньше он указывал внутрь формы, теперь он должен указывать наружу. Затем возьмите внутреннюю часть той же катушки и согните ее вокруг островка в середине формы до следующей радиальной линии в форме и отрежьте ее примерно на 1/2 дюйма за этой линией.Этот провод будет подключаться к концу следующей катушки, и начало этой катушки необходимо будет соединить с концом последней катушки в этой фазе. Итак, что вы делаете, это убедитесь, что у вас есть ровно необходимое количество провода для соединения катушек и отрезания лишнего. Лучше быть немного длинной стороной, чем немного короткой, поэтому на всякий случай дайте себе немного дополнительной длины — но не намного, потому что внутри формы не так много места для проволоки. Как только это будет сделано с тремя катушками, у вас будет готовая 1 фаза.Повторите это для следующих двух фаз.
Изоляция на качественном магнитном проводе довольно толстая, и ее очень трудно соскоблить. Я обнаружил, что он обычно имеет двойную изоляцию, а внутренний слой изоляции почти не виден, так что даже если вы думаете, что хорошо поработали, сняв изоляцию с провода, это может быть плохо! Лучше всего сжечь изоляцию пропановой горелкой на расстоянии около 1 дюйма от конца провода. Я обычно нагреваю ее достаточно, чтобы сам провод стал докрасна.Это также отжигает медь и облегчает скручивание. Сделайте это со всеми отведениями, которые вы отрезали. Вы еще не обрезали конец 1-го витка (он выступает к внешней стороне формы), и вы еще не обрезали внутреннюю часть последнего витка, так что оставьте его — вы разберетесь с этим позже.
Дайте проводам остыть, а затем осторожно очистите пригоревшую изоляцию наждачной бумагой.
Поместите 3 катушки обратно в форму и плотно скрутите провода. Вы можете видеть на картинке, как соединения между катушками в значительной степени расположены по центру.Затем припаяйте соединения и согните их плоскогубцами, чтобы можно было изолировать их изолентой и сделать все как можно тоньше. Вы также можете использовать термоусадку для более аккуратного внешнего вида — если вы это сделаете, обязательно наденьте ее, прежде чем скручивать провода вместе!
Если вы собираете машину на 12 В с несколькими жилами проводов, может быть сложно хорошо скрутить все вместе. Для машин, которые имеют несколько жил, лучше всего выполнить соединения, вставив выводы катушки в небольшую медную или латунную трубку, а затем обжать и припаять.
После того, как вы соединили одну фазу, осторожно извлеките ее из формы и проделайте то же самое с двумя другими фазами.
Когда все три этапа будут завершены, поместите все три обратно в форму, как показано на рисунке. Сделайте это так, чтобы ваши три «конца» (те провода, которые направлены наружу от формы) были рядом друг с другом. Эти три «конца» будут выводами статора (выходом ветряной турбины).
Теперь необходимо соединить фазы звездой.3 внутренних провода должны быть соединены вместе, чтобы мы могли соединить их вместе. Оставьте достаточно провисания проводов, чтобы мы могли выполнить это соединение, а затем протолкните его между катушками и островком в форме. Определите длину, отрежьте их, обожгите изоляцию горелкой, отшлифуйте, скрутите и припаяйте. Затем заизолируйте соединение изолентой или термоусадочной лентой.
На изображении выше изображено законченное соединение звездой, все, что нужно сделать, это прижать его вниз, чтобы оно не выступало над катушками.
Несмотря на то, что катушки подходят и подходят по размеру, после того, как мы сделаем все эти соединения, все станет отчасти пружинистым, и, конечно, катушки не на своем идеальном месте. Сделанные нами соединения и вся эта проволока внутри наверняка вытолкнет некоторые из катушек дальше, чем они должны быть. Используйте клейкую ленту и оборачивайте статор по одной катушке за раз, и закрепите ее точно там, где она должна быть. Держите ленту на «ножках» катушек, как показано на рисунке.
Используйте цианокрилатный клей, чтобы приклеить прямоугольники ткани к ножкам катушек.Положите побольше — вы поймете, что это хороший клеевой шов, когда ткань станет прозрачной. Это также послужит для того, чтобы немного «забить» ножки катушек и предотвратить вибрацию отдельных проводов друг относительно друга — возможно, это не проблема, но мне нравится, когда в катушках есть много суперклея. Также нанесите клей на ткань между витками, чтобы ткань стала «жесткой» и менее гибкой. Это сделает статор достаточно жестким и легким в обращении перед его отливкой. Старайтесь не приклеивать катушки к форме!
На картинке вы видите, что все катушки соединены между собой стеклотканью.
Теперь вы можете осторожно поднять неотлитый статор и вынуть его из формы. Положите его в безопасное место, пока вы не будете готовы отлить статор в смоле.
Отливка статора
Отливка статора
Статор будет отлит из той же полиэфирной смолы, которую вы использовали для магнитных роторов. Вам понадобится стеклоткань с обеих сторон катушек. Возможно, будет полезно просмотреть раздел, посвященный отливке магнитных роторов, прежде чем делать это, поскольку процедура очень похожа, и меры безопасности такие же.
Если вы правильно сложите ткань, вы можете выложить только 1/4 кольца и вырезать два за один выстрел. Вам понадобятся два кольца из стекловолокна с внешним диаметром 15 дюймов и внутренним диаметром 6 дюймов.
На фото вы видите два кольца из стеклопластика. Отложите их и пока катушки в сторону. Смажьте форму статора внутри, сверху и по краю. То же с крышкой —
все должно быть тщательно покрыто жиром или воском. Автомобильный воск или воск для дерева действительно хорошо работают.
Для отливки статора требуется ровно 1/2 галлона смолы.Найдите ровное место, чтобы поставить форму. Важно либо держать края формы за пределами рабочего стола, либо найти верстак (как тот, что на картинке), который обеспечивает доступ для зажимов C по краям формы. Когда вы закончите, вам нужно будет зажать крышку струбцинами, так что думайте наперед! Налейте примерно пол-литра смолы в форму и раскатайте ее так, чтобы все дно и стороны были «мокрыми» от смолы.
Поместите одно из стекловолоконных колец в смолу и обработайте ее палкой, пока она не пропитается.При насыщении — ткань станет практически незаметной. (вы не увидите белого)
Затем налейте еще пинту смолы в форму, еще больше втирайте ее в ткань — попробуйте избавиться от пузырьков воздуха.
Осторожно вставьте катушки, проткните их так, чтобы смола текла вокруг катушек и поднимались воздушные пузыри.
Затем заполните форму смолой и убедитесь, что все поверхности змеевиков покрыты смолой.
Поместите оставшееся кольцо из стекловолокна поверх катушек и нанесите на него смолу — оно должно почти исчезнуть.
Вылейте оставшуюся смолу поверх ткани. Вмешайте его и попытайтесь избавиться от пузырьков воздуха. Возможно, в это время не повредит немного постучать по форме или встряхнуть ее шлифовальной машиной (или чем-то еще) в течение пары минут, чтобы пузырьки воздуха поднялись вверх.
- Осторожно опустите крышку формы на отливку.
Наденьте шайбу 1/2 дюйма на стержень с резьбой и наденьте гайку 1/2 дюйма на нее. Затяните гайку — это хорошо прижимает крышку к форме и гарантирует, что готовая отливка будет толщиной 1/2 дюйма.
Поместите C-образные зажимы с каждой стороны формы (используйте 4 C-образных зажима) и равномерно затяните их. Вы поймете, когда смола затвердеет из-за всего, что вылилось сбоку! Оставьте статор в форме, пока смола не затвердеет.
Долото хорошо подходит для соскабливания / снятия смолы с внешней стороны формы. Хорошее время для этого — пока он еще немного гибкий (до того, как станет по-настоящему сложным).
Когда смола станет твердой, снимите С-образные зажимы и гайку в центре.Используйте долото или отвертку, чтобы осторожно поддеть крышку, пока она не откроется.
После снятия крышки обычно можно перевернуть форму вверх дном, и статор просто выпадет. В противном случае переверните форму вверх дном и постучите по ней молотком или осторожно подденьте кромку статора. Он должен выйти легко.
Используйте напильник или шлифовальную машинку (или и то, и другое), чтобы очистить края статора. Внутренний диаметр должен быть довольно чистым, потому что между этим отверстием и ступицей колеса, которая будет внутри него, не так много свободного места.
Хорошо, если вы просверлите 3 отверстия для шпилек, которые крепят статор к ветряной турбине, прежде чем выполнять сварку на раме, затем вы можете прижать кронштейн статора к статору по центру и просверлить отверстия диаметром 1/2 дюйма Если вы сделаете это таким образом, очень важно, чтобы центральное отверстие статора было примерно точно по центру с кронштейном статора.Также убедитесь, что 3 отверстия выходят между катушками — желательно с тремя идущими проводами. между теми же двумя отверстиями.Вы же не хотите ударить сверлом по меди!
Если вы уже приварили раму, вы можете отцентрировать статор на раме ветряной турбины относительно кронштейна статора и зажать его там — и просверлить отверстия.
Просверлите 3 отверстия диаметром 1/4 дюйма на расстоянии примерно 1/2 дюйма от края статора — по одному возле каждого выходящего вывода.
Вставьте латунный винт 1/4 — 20tpi через каждый с шайбой с каждой стороны и гайкой с обратной стороны. Отрежьте провода ровно настолько, чтобы их можно было зажать между головкой винта и шайбой.Теперь на каждый винт можно надеть еще пару шайб и по одной гайке. Они будут служить наконечниками, к которым мы сможем подсоединить линию к ветряной турбине.
Статор готов! Мы можем отложить это в сторону, пока не будем готовы собрать генератор.
Продолжить чтение здесь: Создание магнитных роторов Пресс-форма
Была ли эта статья полезной?
там, где орлы боятся сесть на насест: самодельный генератор осевого потока — часть 1
В конце прошлого года я подумал, что смогу создать экспериментальный генератор, который можно было бы использовать с ветряной турбиной, либо с вертикальной осью Савониуса новой сборки, либо с использованием моего запасного набора самодельных лопастей для наш существующий станок с горизонтальной осью.
Я начинаю с малого, с общим диаметром ротора всего около 150 мм (6 дюймов), но у меня в мастерской валяется пара изношенных передних тормозных дисков от моего старого MGF (давно исчезнувшего …), которые могли возможно, будет использоваться для более крупной версии в будущем.
Сначала я посмотрел на то, что другие сделали на YouTube и т. д., я придумал дизайн, немного отличающийся от большинства других, а затем принялся за работу. На этом этапе он предназначен для Это трехфазный генератор переменного тока, поэтому с 12 полюсами магнита нам понадобится 9 катушек, сокращающих магнитный поток во время вращения.Это даст требуемые 120 градусов разделения фаз во время работы — в Интернете доступно несколько анимаций, которые показывают движущиеся графики напряжений, наведенных в трехфазном генераторе переменного тока.
Катушки генератора будут статичными, то есть будут формировать «статор», а магниты будут прикреплены к стальным пластинам и вращаться, то есть «ротор». Собранный ротор состоит из двух частей: внешней и внутренней. Вал ротора вращается в шарикоподшипниках в корпусе, к которому будет прикреплен статор.
Купил на eBay пару стальных профилированных пластин для дисков ротора. У меня уже было несколько алюминиевых прутков круглого и квадратного сечения, из которых можно было обрабатывать корпуса подшипников, валы и т. Д.
корпус подшипника, временный центральный болт, задний подшипник , задний поворотный вал и распорная втулка подшипника |
В передней части корпуса установлены два подшипника, поэтому вал генератора может вращаться независимо, а третий сзади, который будет поддерживать прямое соединение комплекта турбинных лопаток через короткий вал.Затем весь узел ступицы лопасти / генератора можно было бы удерживать с помощью одного центрального болта M10 — на данный момент я только что использовал длину шпильки, повернутую до диаметра 8 мм на заднем конце, чтобы я мог поместиться в аккумуляторный сверлильный патрон. для тестирования.
Цилиндрическая распорная втулка подшипника надевается на валы и обеспечивает контакт между внутренними кольцами переднего и заднего комплектов подшипников. Прокладка немного длиннее, чем расстояние между поверхностями отверстий подшипников в корпусе. Это позволяет полностью затянуть центральный болт без перегрузки подшипников и их блокировки, как это было бы, если бы путь нагрузки проходил через шариковые элементы, затягивая как внутренние, так и внешние дорожки качения.Альтернативой может быть использование шпилек в качестве центрального вала и регулировка осевой нагрузки на подшипники во время сборки, чтобы они могли свободно вращаться без чрезмерного концевого смещения, а затем установка контргаек, чтобы удерживать вал в установленном положении.
Четыре резьбовых отверстия, показанные на лицевой стороне корпуса, предназначены для фиксации узла статора. Я просверлил комплекты резьбовых отверстий на всех других поверхностях корпуса, чтобы предоставить различные варианты монтажа собранного генератора без необходимости разбирать его и повторно обрабатывать в будущем.
Показанный в настоящее время нижний профилированный блок, прикрепленный под корпусом подшипника, может быть просверлен в его основании для установки непосредственно на опору мачты турбины, если он будет использоваться для станка с горизонтальной осью — на данный момент он просто позволяет мне держать генератор. в тисках для сборки и тестирования.
Опять же на eBay я купил 50 неодимовых дисковых магнитов диаметром 20 мм и толщиной 5 мм. По цене 39 фунтов стерлингов они были из материала N35, самого низкого доступного сорта, но 50 x N35 были примерно той же цене, что и 25 x N40, и мне нужно было 48 из них в конструкции.
На станке с ЧПУ я сначала обработал карманы в стальных пластинах для первой колонки магнитов, а также просверлил монтажные и фиксирующие отверстия. После того, как эта обработка была завершена, я пометил и собрал пластины ротора вместе с валом и выровнял внешние диаметры на токарном станке так, чтобы они были концентричными с валом — это должно помочь гарантировать, что сборка ротора уже близка к уравновешивается, хотя мне все равно может потребоваться добавить несколько балансировочных грузов во время тестирования, чтобы устранить любую вибрацию.
Двенадцать магнитов были помещены в карманы каждой пластины ротора с эпоксидной смолой, а затем следующий столбик из двенадцати магнитов был помещен сверху.
внешняя пластина ротора с фиксированными первыми наборами магнитов и с отверстиями и отверстиями для крепления вала |
ступени и той же внутренней пластине ротора …. |
Одно слово предостережения: неодимовые магниты очень сильны, и с ними всегда нужно обращаться с уважением.Если вы позволите стальным инструментам и т. Д. Находиться слишком близко к поверхностям магнитов, они очень резко сойдутся вместе, и есть риск повредить магниты.
Полюса магнитов расположены поочередно с севера на юг вокруг дисков, а крепежные отверстия в каждой пластине ротора просверлены и отмечены совпадениями, чтобы гарантировать, что северный полюс магнитов на внешней пластине ротора находится напротив на внутренней. плита южным полюсом, и наоборот. Такое расположение сохраняет магнитный поток внутри пластин ротора и через зазор между ними — это очень эффективно, прикосновение отвертки к задним поверхностям пластин показывает, что магнитная сила там совсем небольшая, но передние грани очень сильны.
Затем, чтобы сохранить внешний набор магнитов, я сделал форму вокруг центра каждого диска, смешал немного полиуретановой смолы для литья и затем залил ее, чтобы герметизировать магниты.
вторая колонка магнитов и установленный вал (внешние винты являются временными только для формования) |
после заливки, затвердевания и извлечения из формы…. магниты находятся чуть ниже поверхности смолы |
Двухкомпонентная полиуретановая смола для литья была куплена на eBay, довольно дорого, по цене 21 фунт стерлингов, доставленной всего за один литр, но это система быстрого нанесения жизнеспособность всего несколько минут и готовность к извлечению из формы менее чем за полчаса. Этого более чем достаточно для двух роторов, а также для полной герметизации катушек статора.
пробная сборка механических компонентов |
На фотографии выше показана пробная сборка генератора — на этом этапе все механические компоненты в основном готовы, за исключением покрытия распылением. Hammerite или аналогичный материал на роторах для защиты от коррозии стальных деталей.Все шпильки и гайки, которые я использовал, изготовлены из нержавеющей стали. Поверхности магнитов уже покрыты полиуретаном — важно, чтобы они не подвергались воздействию элементов, поскольку, хотя они и должны быть никелированы во время производства, мой предыдущий опыт работы с подобными магнитами показывает, что они могут очень скоро показать признаки коррозия.
Как видите, я использовал шпильки большой длины, чтобы разделить две половины ротора. Это позволяет довести зазор между магнитами и катушками статора до минимума при окончательной сборке.Чем ближе магниты к катушкам, тем лучше производительность генератора.
зазор между внутренней пластиной ротора и корпусом подшипника … |
На приведенной выше фотографии вы можете увидеть зазор между внутренним ротором и квадратным корпусом подшипника. Это позволяет ротору свободно вращаться, не загрязняя корпус, а также обеспечивает кабельную трассу для пропуска проводов от статора через внутреннее отверстие ротора.
Итак, теперь, когда он механически завершен, я перейду к сложной части наматывания катушек и т. Д.Я уже купил обмоточный провод и трехфазный мостовой выпрямитель и начал делать формирователи катушек и т. Д. — Я покажу конструкцию статора и начальные испытания готового генератора в следующем посте …
Анализ конструкции электродвигателя и генератора с помощью COMSOL®
В этом сообщении блога мы исследуем 12-контактный 10-полюсный двигатель с постоянными магнитами (PM), смоделированный в программном обеспечении COMSOL Multiphysics® и модуле AC / DC. Машина в этом примере служит типичным примером вращающегося устройства и имеет внешний диаметр 35 мм и осевую длину 80 мм.С небольшими изменениями входных условий та же модель может стать двигателем или генератором. В следующих статьях блога мы подробно остановимся на каждом из обсуждаемых здесь аспектов дизайна.
Конструкции электродвигателей и генераторовЭто первая запись в блоге из серии, в которой обсуждается, как получить представление о некоторых аспектах проектирования вращающихся машин, используя возможности моделирования и постобработки программного обеспечения COMSOL Multiphysics®.
: установка модели
В двигателе с постоянными магнитами магнитные поля ротора вращаются синхронно с магнитными полями, создаваемыми токами статора.Взаимодействие магнитных полей ротора и статора создает чистый крутящий момент, который позволяет двигателю преобразовывать токи обмоток в механическую энергию. Вследствие синхронного характера возбуждения в двигателе с постоянными магнитами на мгновенный крутящий момент сильно влияет угловое положение ротора, поскольку положение синхронизируется с токами статора. Это отличается от асинхронных машин, где обмотки статора индуцируют магнитные поля ротора в зависимости от отставания в скорости между ротором и статором (отсюда его популярное название, индукционная машина ).{\ circ} / N_p}, где N_p — количество полюсов ротора. Знаменатель дает угловой размах одного полюса ротора.
Исследование и оптимизация распределения магнитного поля
Распределение магнитного поля является очень важным фактором при проектировании электрических машин. В синхронно вращающихся машинах ключевым параметром для исследования индуцированных напряжений является пространственное распределение потока в воздушном зазоре (поток, передаваемый между ротором и статором). Напряжение фазы статора будет синусоидальным только в том случае, если радиальный магнитный поток имеет синусоидальное распределение по периферии ротора.Эта пространственная форма волны также называется волной магнитодвижущей силы (МДС) воздушного зазора. Если волна MMF несинусоидальна, в индуцированное напряжение вводятся гармоники более высокого порядка.
В этой модели, чтобы получить волну MMF воздушного зазора, мы оцениваем радиальную составляющую плотности магнитного потока вдоль границы непрерывности. По мере вращения ротора мы можем наблюдать, как волна MMF развивается с течением времени. Просто осмотрев, мы можем понять, что индуцированное напряжение не будет идеально синусоидальным.В следующей серии блогов мы объясним, как получить пространственные и временные преобразования Фурье магнитного потока в воздушном зазоре и как связать их с конкатенированным потоком и гармоническим искажением напряжения.
Слева: изменение плотности магнитного потока при вращении ротора. Справа: Развитие волны MMF воздушного зазора при вращении ротора.
Исследование и оптимизация механического крутящего момента
Существует несколько способов возбуждения обмоток статора для конкретной комбинации паз / полюс двигателя с постоянными магнитами.Схема, показанная на схеме модели машины с постоянными магнитами (первый рисунок в сообщении в блоге), является одним из способов управления 12-контактным 10-полюсным двигателем с постоянными магнитами. Возбуждение обмотки статора (или начальное положение ротора) необходимо отрегулировать так, чтобы к ротору прилагался максимальный крутящий момент. Для этого ротору придается начальное угловое смещение. Угол ротора \ alpha изменяется в пределах углового диапазона одного магнита ротора, и вычисляется средний крутящий момент. В качестве начального положения ротора выбрано значение начального углового смещения, соответствующее максимальному среднему крутящему моменту.Таким образом, становится легче визуализировать, какое относительное положение статора и ротора создает максимальный крутящий момент.
В представленном здесь случае наблюдаются два максимума:
- Положительный максимум, который будет соответствовать вращению против часовой стрелки — после применения правильной последовательности фаз.
- Отрицательный максимум, который приведет к вращению по часовой стрелке (также здесь, после точной настройки последовательности фаз)
Форма кривой крутящего момента ротора, приведенная в следующем разделе, соответствует положительному максимуму кривой среднего крутящего момента.{\ circ}).
Исследование и оптимизация использования железа и потерь
Используя график плотности магнитного потока, мы можем исследовать распределение плотности магнитного потока в железном сердечнике. В некоторых частях геометрии ярмо может образовывать узкое место, которое может подтолкнуть значение плотности магнитного потока к области насыщения кривой B-H. В других случаях он достаточно широкий, чтобы создавать области с низкой напряженностью поля. Когда определенная часть ярма постоянно показывает слабое поле, эта часть недостаточно используется для создания крутящего момента.{\ circ}, как получено из кривой среднего крутящего момента в предыдущем разделе. Как видно из графиков и кривой крутящего момента ниже, использование чугуна оптимально, когда толщина чугуна составляет около 2 мм: переход менее 2 мм отрицательно повлияет на крутящий момент, а увеличение количества добавит ненужный материал. — и поэтому; вес, а стоимость — до мотора.
Распределение плотности магнитного потока для различных значений толщины железа. Слева: 1 мм. Центр: 2 мм.Справа: 3 мм.
Изменение формы кривой крутящего момента ротора в зависимости от толщины железа.
Но это еще не все: при определении толщины железа необходимо учитывать дополнительные факторы, такие как механическая прочность, резистивные и магнитные потери. При исследовании плотности магнитного потока и крутящего момента можно также оценить влияние различной толщины железа на потери в стали. Начиная с версии COMSOL Multiphysics 5.6, имеется встроенная функция расчета потерь , позволяющая легко оценить потери в меди и в стали с помощью уравнения Steinmetz , формулировки Bertotti или пользовательской модели потерь.В следующих статьях блога мы продолжим обсуждать мультифизические аспекты моделирования вращающихся машин, такие как расчет эффективности, оценка повышения температуры, анализ вибрации и исследование шума.
Распределение потерь в стали для различных значений толщины железа. Слева: 1 мм. Центр: 2 мм. Справа: 3 мм.
Резюме
Мы обсудили использование некоторых функций COMSOL Multiphysics и модуля AC / DC, чтобы легко понять некоторые аспекты конструкции вращающихся машин.Мы видели, как линейный график радиальной плотности магнитного потока в воздушном зазоре показывает нам, будет ли индуцированное напряжение синусоидальным. Используя COMSOL Multiphysics, можно использовать параметр Parametric Sweep для определения начального угла ротора, при котором создается максимальный крутящий момент ротора. Поверхностный график плотности магнитного потока в машине позволяет визуально определить, оптимально ли использование чугуна для эффективного производства крутящего момента. Влияние толщины железа на потери в стали также можно наблюдать с помощью встроенных моделей потерь, предлагаемых COMSOL Multiphysics.
Этот первый пост в блоге из серии показывает, как мощные возможности моделирования и постобработки COMSOL Multiphysics могут быть использованы для получения ценной информации о конструкции вращающихся машин. В следующих статьях блога будут подробно обсуждаться методы расчета крутящего момента, расчет эффективности, анализ потерь в стали и тепловых характеристик, а также проверка вибрации и шума двигателя. Оставайтесь в курсе!
Попробуйте сами
Попробуйте смоделировать обсуждаемый здесь электродвигатель, нажав кнопку ниже:
Magnax готовится к производству радикально мощного и компактного электродвигателя с осевым потоком
Чтобы представить себе такую мощность в перспективе, смехотворно быстрый 193-сильный супербайк BMW S1000RR 2011 г. ни о чем в автомобильном мире — есть легкий мотор, который делает жалкие 2.4 киловатта на килограмм. Так что 9 кВт / кг — это не шутка.
Что делает этот двигатель с осевым потоком и прямым приводом от бельгийской компании Magnax по-настоящему удивительным. Magnax заявляет, что его пиковая мощность составляет не менее 15 кВт / кг, а постоянная мощность составляет около 7,5 кВт / кг. Вернемся к примеру с мотоциклом: если вы построите двигатель Magnax, который весит столько же, сколько двигатель супербайка BMW, у вас будет 603-сильная трансмиссия, которая на короткие промежутки времени может производить всплески до 1206 лошадиных сил до перегрева и нужно немного расслабиться.
Очевидно, что это глупый пример, но такие сверхлегкие двигатели могут значительно поработать, чтобы компенсировать большие весовые показатели сегодняшних тяжелых литиевых аккумуляторных батарей в электромобилях. И до тех пор, пока плотность аккумуляторов автомобильного класса не совершит значительный скачок вперед, как это было многообещающе уже несколько лет, вес по-прежнему будет серьезной проблемой для электронной мобильности.
Преимущества и недостатки конструкций осевого флюса
В то время как подавляющее большинство электродвигателей, находящихся в настоящее время в обращении, представляют собой конструкции с радиальным магнитным потоком, Magnax утверждает, что ключом к высокой удельной мощности, которую она достигает, является конструкция осевого потока с прямым приводом, используемая во всех ее двигателях, в которой используется диск статора, зажатый между двумя дисками ротора. с небольшими воздушными зазорами между ними.Компания утверждает, что двигатели с осевым магнитным потоком без ярма имеют ряд преимуществ при правильной реализации. Путь потока короче, а магниты дальше от оси, что приводит к большей эффективности и рычагу вокруг центральной оси.
Более того, конструкция осевого потока позволяет Magnax тратить очень мало меди на выступающие петли обмоток. У двигателей Magnax нулевой вылет; Активны 100 процентов обмоток, а в двигателях с радиальным магнитным потоком иногда может быть до 50 процентов неактивной меди, что добавляет дополнительное сопротивление и вызывает накопление тепла.В обмотках Magnax используется медный провод прямоугольного сечения для обеспечения максимально возможной плотности. А двигатели намного тоньше, чем машины с радиальным флюсом, а это означает, что вы можете легко сложить их для параллельной работы.
Конечно, существуют трудности, когда дело доходит до создания двигателей с осевым потоком — иначе их бы делали все. Сильные магнитные силы, действующие между дисками ротора и статора, очень затрудняют поддержание равномерного воздушного зазора между ними.Если они начнут раскачиваться или гнуться, диски могут начать тереться друг о друга, что в лучшем случае приведет к повреждению подшипников, а в худшем — к быстрой и впечатляющей внеплановой разборке.
Magnax утверждает, что решает эту проблему в своей конструкции с осевым потоком без ярма за счет наличия двух дисков ротора, которые постоянно прикладывают равные и противоположные силы к диску статора. Роторы соединены напрямую друг с другом через кольцо вала, поэтому магнитные силы нейтрализуют друг друга, и внутренний подшипник не должен иметь с ними дело.
Охлаждение является ключевым моментом для любого электродвигателя большой мощности, который должен выполнять стабильную работу, и конструкции с осевым потоком, как правило, страдают в этом отношении, поскольку их обмотки статора зажаты между дисками ротора, что затрудняет отвод тепла. Magnax утверждает, что конструкция его двигателя хорошо охлаждается, поскольку обмотки находятся в прямом контакте с внешним алюминиевым корпусом, обеспечивая приличную теплопередачу.
Вроде работает. Показатели непрерывной мощности для двигателя Magnax составляют 50 процентов от того, что он может производить на пике, что довольно прилично, но не в области лучших охлаждаемых двигателей с радиальным магнитным потоком.Например, двигатель Equipmake может непрерывно обеспечивать почти 70 процентов своей пиковой мощности, что свидетельствует о превосходном охлаждении.
Еще одна проблема связана с производством, так как диски статора может быть особенно трудно исправить, а еще сложнее встроить в автоматизированный процесс большого объема. Поэтому, когда они действительно построены, они сделаны вручную и в результате очень дороги. Компания Magnax утверждает, что решила и эту проблему, с помощью ряда «проприетарных решений», которые позволяют масштабировать и создавать эти устройства с минимальными затратами.
Двигатель Magnax отличается высокой масштабируемостью: его размер варьируется от 15 сантиметров (~ 6 дюймов) до дисков диаметром 5,4 метра (~ 13 футов) и более. Их можно вставить рядом друг с другом для параллельной работы, и они могут работать как с прямым приводом, так и через коробку передач, если вы готовы принять связанные с этим потери эффективности.
Magnax предлагает их для электромобилей и мотоциклов, роторов самолетов, а также в качестве решений большого диаметра, с высоким крутящим моментом и низкой частотой вращения для ветроэнергетики, гидроэлектроэнергии и производства энергии волн.
В конце концов, полевые испытания в автомобильном и промышленном мире будут доказательством этого пудинга, но если это действительно мощный, долговечный, хорошо охлаждаемый, высокоэффективный, не требующий обслуживания осевой магнитный двигатель, Magnax может вызвать серьезные волнения.
Компания потратила около девяти лет на сборку своей технологии после того, как в 2009 году в Гентском университете была первоначально создана экспериментальная концепция. Теперь она утверждает, что у нее есть рабочие прототипы и разработанная методология производства.Если повезет, резина скоро отправится в путь, и мы сможем увидеть, действительно ли это электродвигатель будущего.
Посмотрите несколько видео ниже:
Источник: https://newatlas.com/magnax-axial-flux-electric-motor/54821/
.